About the Team
Industry: Technology, Wireless Networking
Product: WaveTunnelTM
Location: Santa Clara, CA
Why Fictiv
Customer Challenges:
Building and launching the industry’s first indoor 60GHz wireless system.
Capabilities Leveraged:
Urethane Casting
Die Casting
Injection Molding
Design for Manufacturability Assembly Verification
Program Management
Result:
- Brought wireless Ethernet backbones to market in half the time with Fictiv.
- Realized revenue 2X faster
with Fictiv.
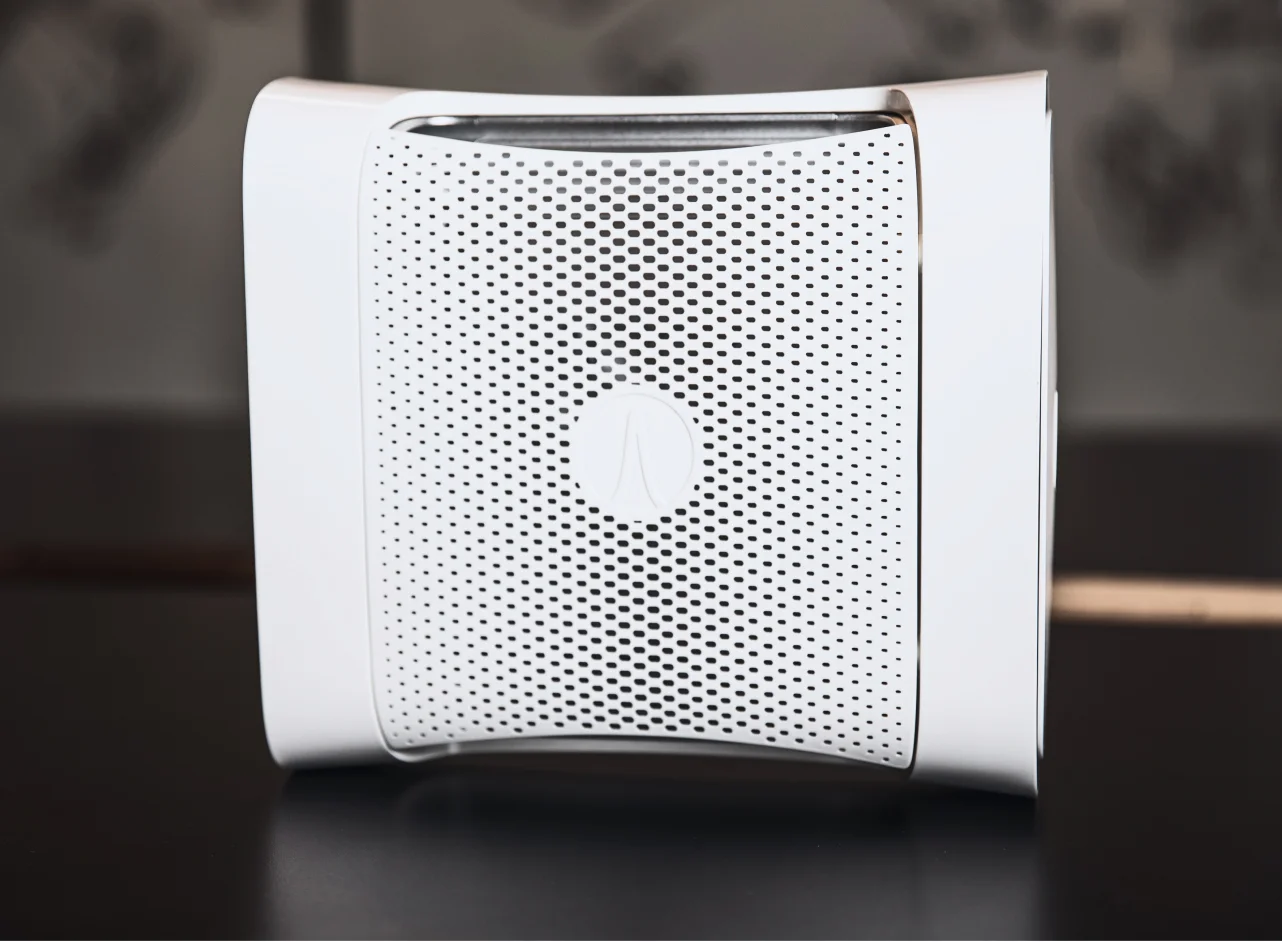
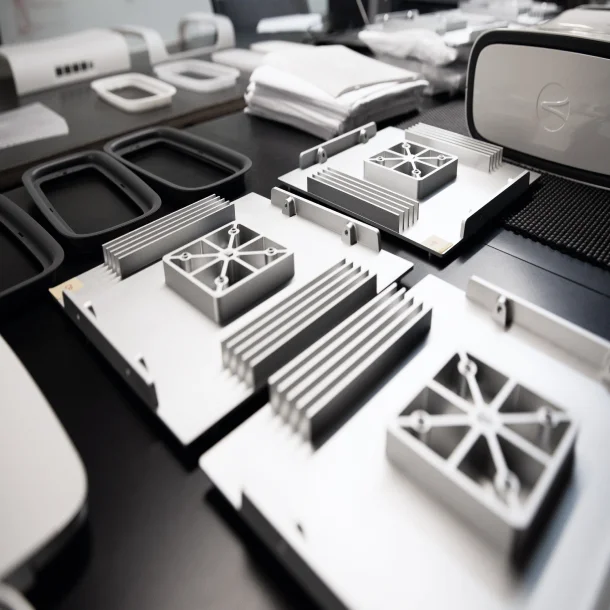
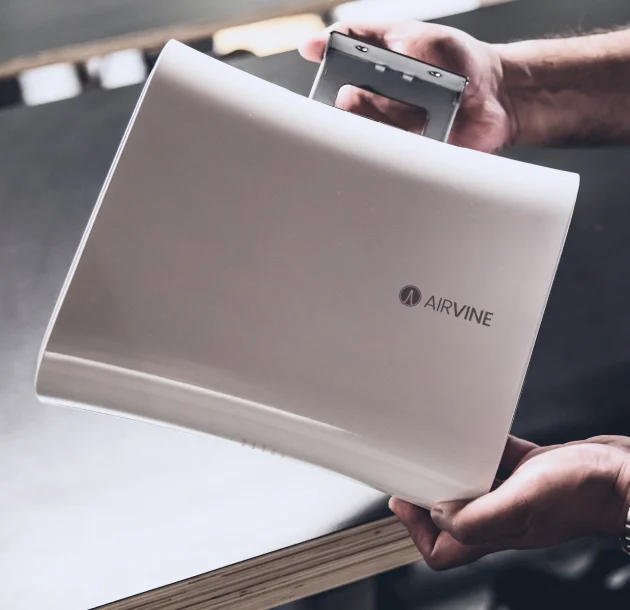
The Internet’s Next Frontier
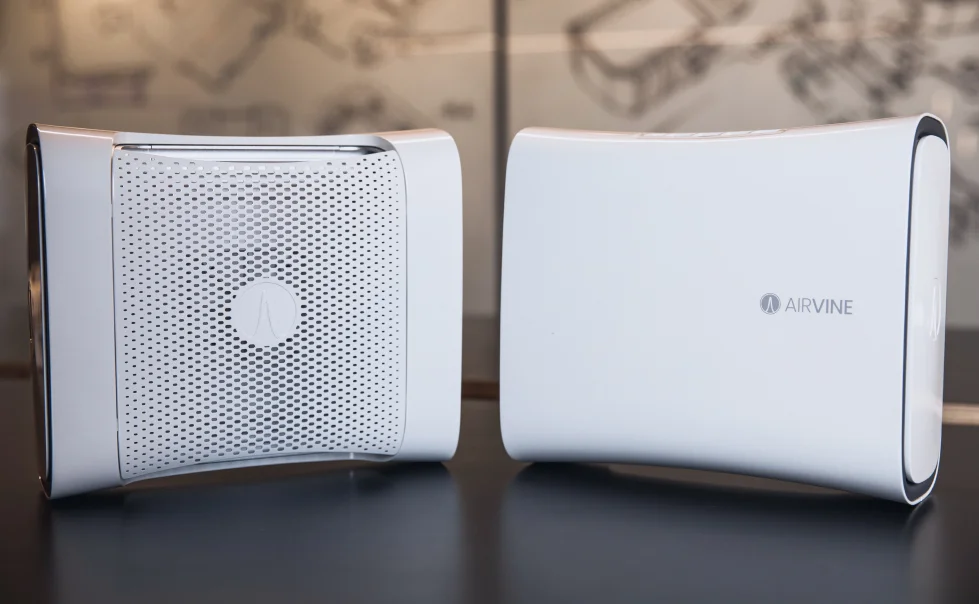
For most entrepreneurs, great products start with a vision for a better future. Hatch Graham, founder of Airvine, is no exception. Graham’s vision is to radically improve how indoor Internet network infrastructures are deployed, operated, reconfigured, and repurposed worldwide. Airvine has created wireless Ethernet backbones that deliver a multi-gigabit per second data transfer rate to realize that vision. The current iteration of the product, WaveTunnel, is used in everything from multi-dwelling units like senior living to the hospitality sector to large venues such as convention centers and stadiums and manufacturing or warehouse environments.
According to Airvine’s VP of Product Management, Dave Sumi, “What we’ve been able to do is develop a technology that can take 60GHz frequency band and go through walls. We can go through sheetrock, wood, glass, and other indoor wall materials, which is something no one has ever done at this frequency.”
Many legacy indoor environments use Ethernet cables, so everything is hardwired. WaveTunnel gets around those limitations with a point-to-point-to-point indoor wireless backbone network that outperforms CAT5 by providing wireless connectivity throughout the facility. Airvine ensures critical uninterrupted service for warehouses and large-scale factory settings, elder care facilities,
and more.
“What we’ve been able to do is develop a technology that take 60GHz frequency band and go
– Dave Sumi, VP of Product Management
through walls.”
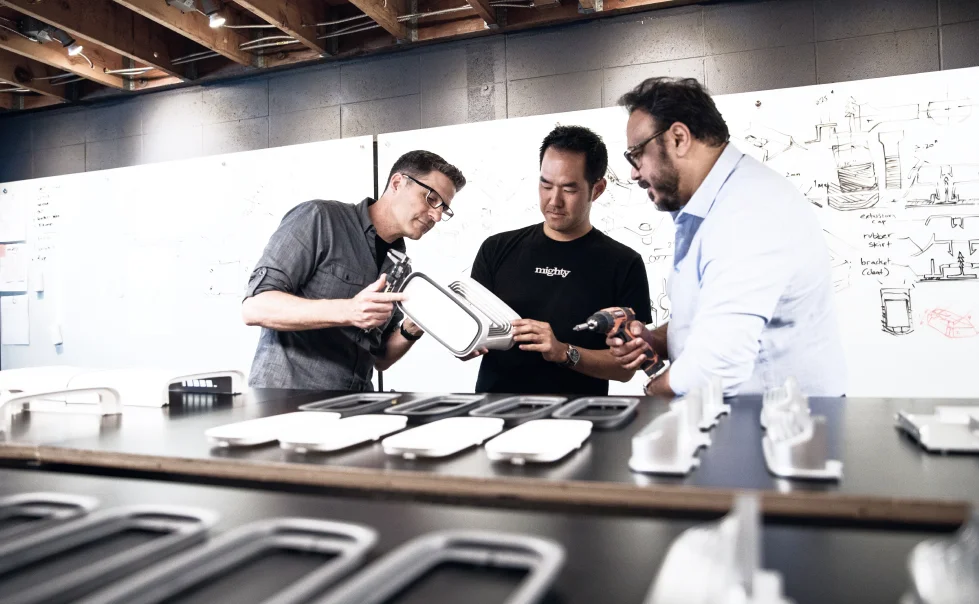
Following a successful pilot program with their industrial design partner, Mighty Studios, the challenge became finding a manufacturing partner who could deliver complex production-ready parts with stringent global fire safety, cosmetic, RF, and design requirements—and who could meet their accelerated production timelines. Mighty Studios recommended Fictiv, and Airvine selected them for their comprehensive design for manufacturability guidance, the capacity and capabilities to manufacture over 10,000 strictly regulated parts. The result? Airvine tested and launched a new product and brought it to market 2X faster than they could have without Fictiv. This translated into realizing revenue faster.
Anand Shirur, VP of Operations at Airvine says, “At one point, we met with Fictiv every three days. They spent a great deal of time with us to help ensure we met our aggressive timelines.”
“At one point, we met with Fictiv every three days. They spent a great deal of time with us to help ensure we met our aggressive timelines.”
– Anand Shirur, VP of Operations, Airvine
Manufacturing the Future of Wireless
Fictiv manufactured all the enclosure components for the WaveTunnel system. Critical manufacturing support areas included assembly verification, materials and design guidance, quality control with on-the-ground expertise, and logistics.
Consistency & Tolerances
Effective heat dissipation is critical, given the incredible performance capabilities of the WaveTunnel’s core components. The die-cast aluminum heat sink required post-casting machining operations to maintain consistent datum heights, flatness, and tolerances for assembly.
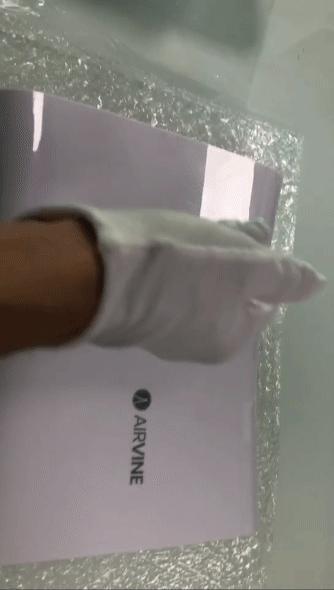
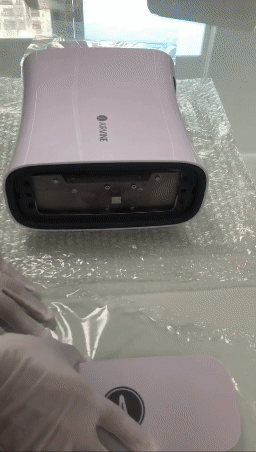
A Fictiv supplier quality engineer inspects and verifies the WaveTunnel enclosure assembly.
Throughout multiple engineering change orders that would otherwise slow a traditional manufacturer, the Fictiv team maintained close oversight of individual part production and ongoing verification of the successful assembly of the enclosure to protect Airvine’s speed to market. This working model is the furthest thing from a typical “marketplace” Fictiv’s competitors tout. Instead, it’s a manufacturing partnership where Fictiv became an extension of Airvine’s team to ensure quality and timeliness at every turn.
Materials Expertise
Later in the program, Airvine determined to pursue a major opportunity in Europe that required a significant change in parts materials in order for WaveTunnel to achieve the necessary fire rating. But they didn’t have a year to complete such a change. Fictiv’s in-house experts highlighted cost-effective, commercially available material grades that met the UL94 V0 level certification and completed the new production run, all in just 2 months. That’s the type of manufacturing and supply chain agility that comes from a true partnership.
Cosmetic Standards
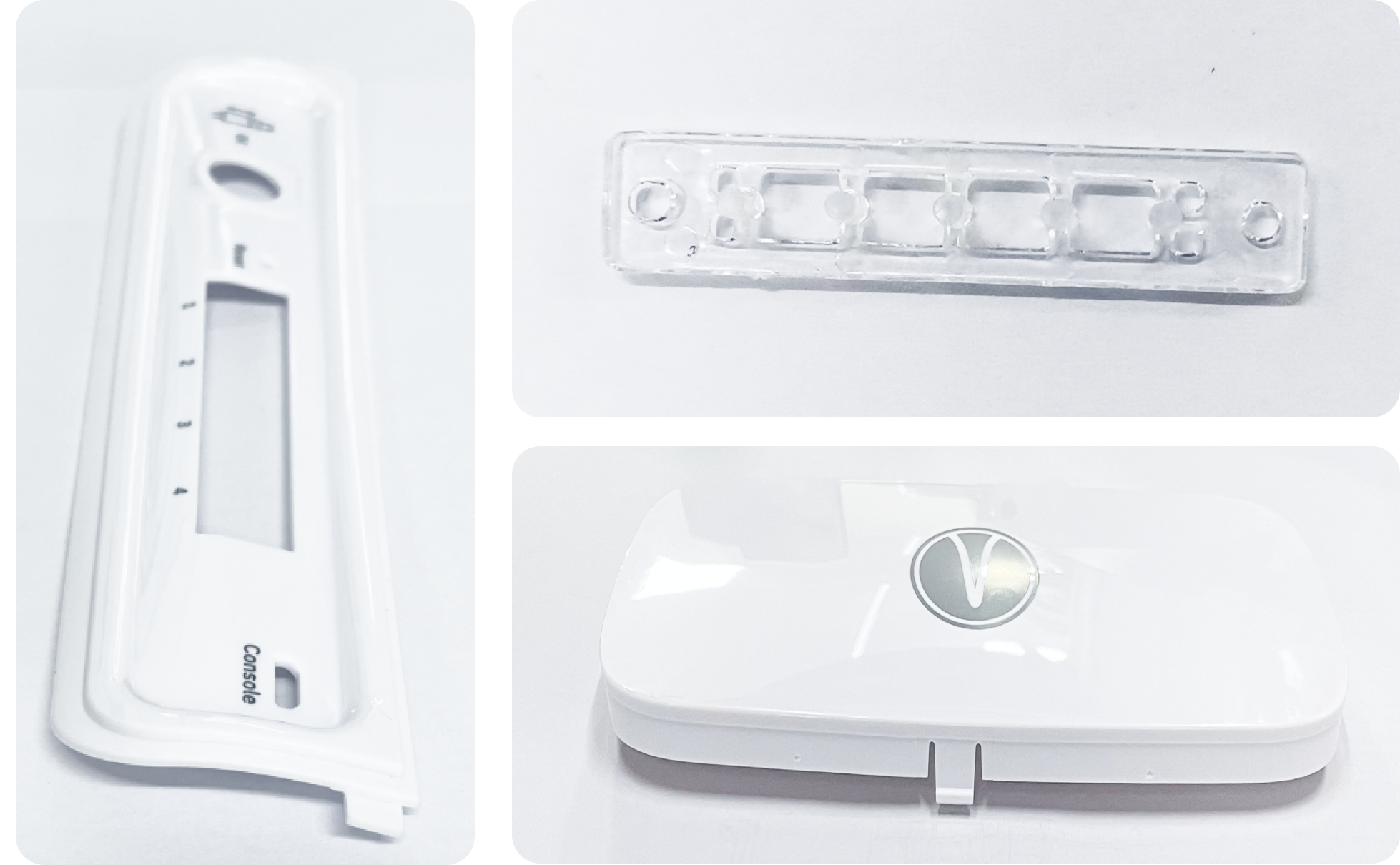
Strict cosmetic standards were required in order to achieve color consistency throughout injection molded parts and for details such as the printed and embossed branding across key touchpoints.
According to Shirur, “Fictiv takes the project from design through to production, communicating every detail along the way.”
With Fictiv, Airvine had confidence in the end product, its quality, safety, and beautiful design.
Complex Manufacturing Challenges Overcome
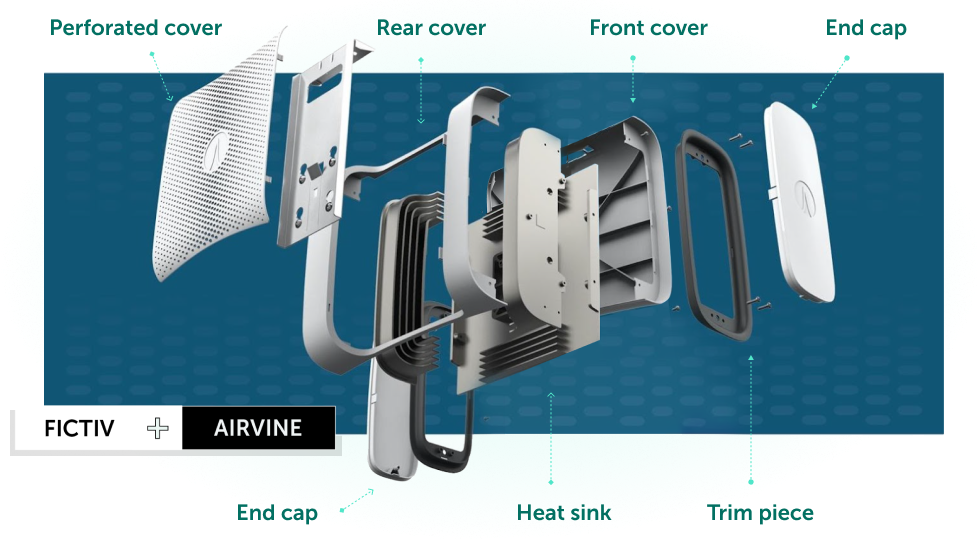
Parts manufactured by Fictiv: Front and rear covers, end caps, trim pieces, heat sink, and perforated cover for each WaveTunnel.
Yet Fictiv’s solutions for Airvine went beyond manufacturing a complex wireless Ethernet device. Fictiv also helped Airvine handle the supply chain and logistics.
DFM
Fictiv offered Airvine design for manufacturability guidance both pre- and post-order to alert Airvine to potential risks before they invested in production from the beginning.
Tooling and first samples
The first trial samples were shared with Airvine to test the parts and ensure they met expectations. Fictiv’s speed and quality of samples ultimately helped Airvine save time and money.
Logistics
Fictiv delivered additional value by offering logistics support, including shipping.
Program Management
Fictiv offered program management to make sure Airvine was kept informed along the way and could respond immediately if any issues arose. This was particularly helpful because of safety and cosmetic requirements.
Each stage of the project required precise coordination and quality control to ensure that the final product met the necessary specifications and standards for performance, durability, and safety. The specific technologies and materials used in Airvine’s WaveTunnel required additional specialized processes because of the cutting-edge components and materials.

The manufacturing partnership resulted in comprehensive project management across multiple regions to expedite the first production runs, ensuring Airvine had the completed assemblies it needed in time for commercial testing. Ultimately, Fictiv and Airvine’s top-notch communication and engineering expertise successfully brought WaveTunnel to the market. For Robbie Long, Product Marketing Manager, Injection Molding, “Whether addressing issues like warping or logistical roadblocks, it’s understood that every production program will present challenges. Working closely with Airvine and our manufacturing partners enabled us to overcome these challenges and help get WaveTunnel to market in half the time.”
“Working closely with Airvine and our manufacturing partners enabled us to overcome these challenges and help get WaveTunnel to market in half the time.”
– Robbie Long, Product Marketing Manager, Injection Molding
What’s Next for Airvine
Arvine’s roadmap includes developing a product that is smaller, faster, and cheaper. And that gives enterprise customers more gigabits. For Shirur, this means an even stronger partnership with Fictiv in the future. “No matter the challenges, Fictiv consistently demonstrates engineering excellence in proposing new designs.”
The proof is in the results says Shirur. “For this project, 10,000 parts were delivered on time and in full while meeting stringent global safety, quality, and cosmetics requirements.”
“No matter the challenges, Fictiv consistently demonstrates engineering excellence in proposing new designs.”
– Anand Shirur, VP of Operations, Airvine