About the team
Industry: Consumer Products
Product: Wearable device designed to reinforce good habits
Location: San Francisco, France
Why Fictiv
Customer challenges: Quality and lead time challenges with existing injection molding supply
Favorite features: Facilitation with overseas supplier communications to translate design intent
Result: Over 40,000 injection molded parts produced through Fictiv’s Agile Manufacturing Solution
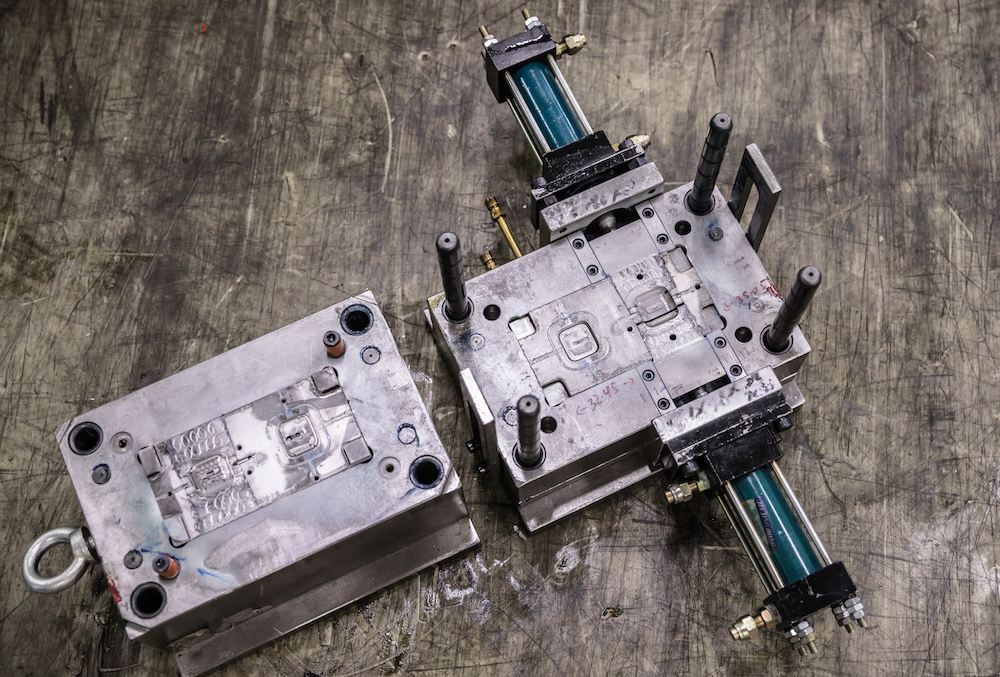
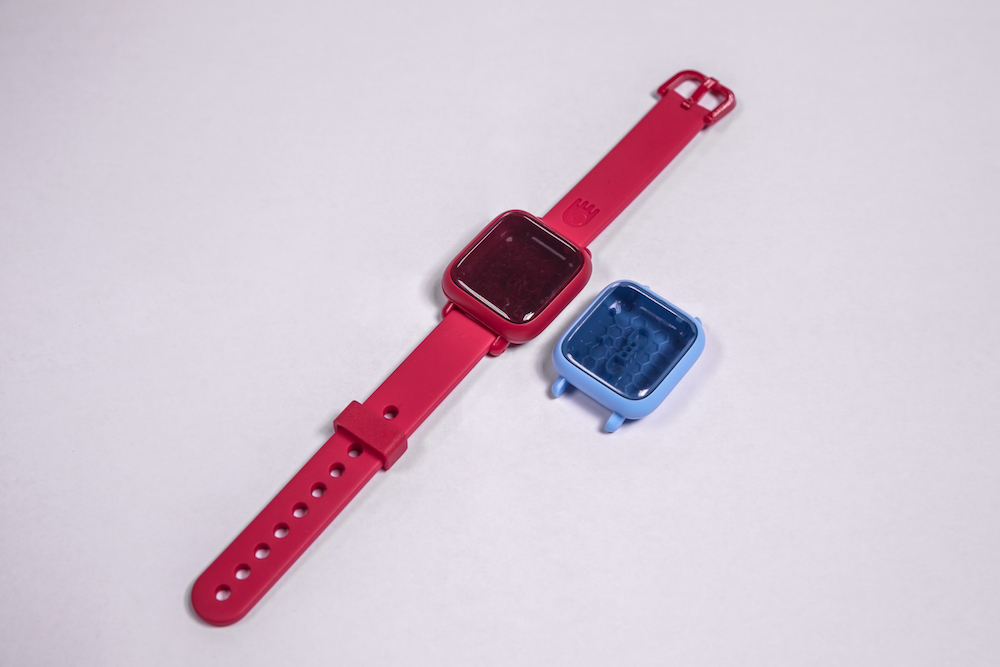
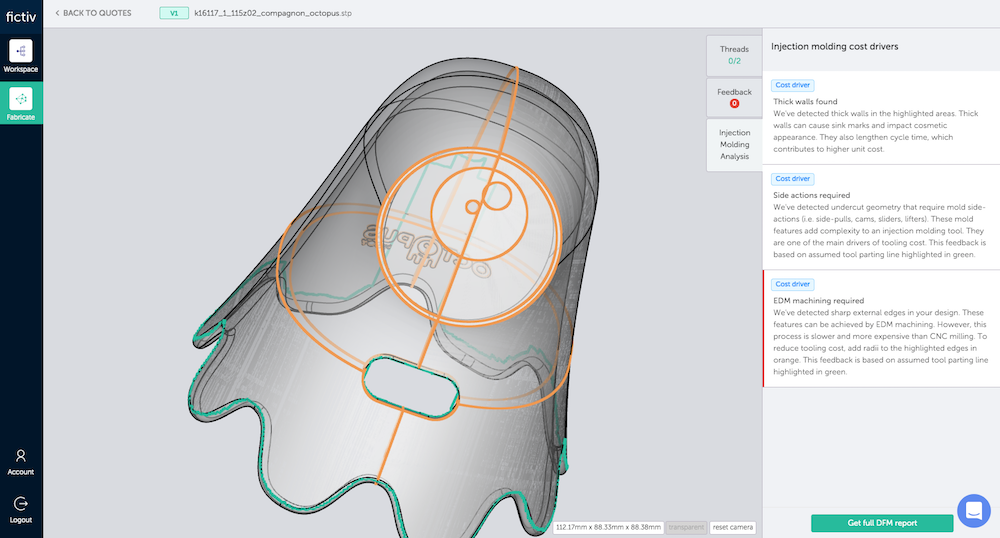
Joy is a wearable technology company based in San Francisco and France, whose mission is to help families spend more quality time together through technology to manage schedules and tasks. Joy’s first product, the Octopus watch, is an icon-based device for kids designed to reinforce good behaviour.
To manufacture critical mechanical components of the Octopus watch at scale, Joy leveraged Fictiv’s Agile Manufacturing Solution (AMS) for streamlined access to high quality overseas injection molding services.
A developing partnership, from prototype to production
Joy first discovered Fictiv through their hardware accelerator HAX in the early development stage and leveraged Fictiv’s Rapid Prototyping Solution for quick-turn multi-material rigid and elastomeric 3D printed parts.
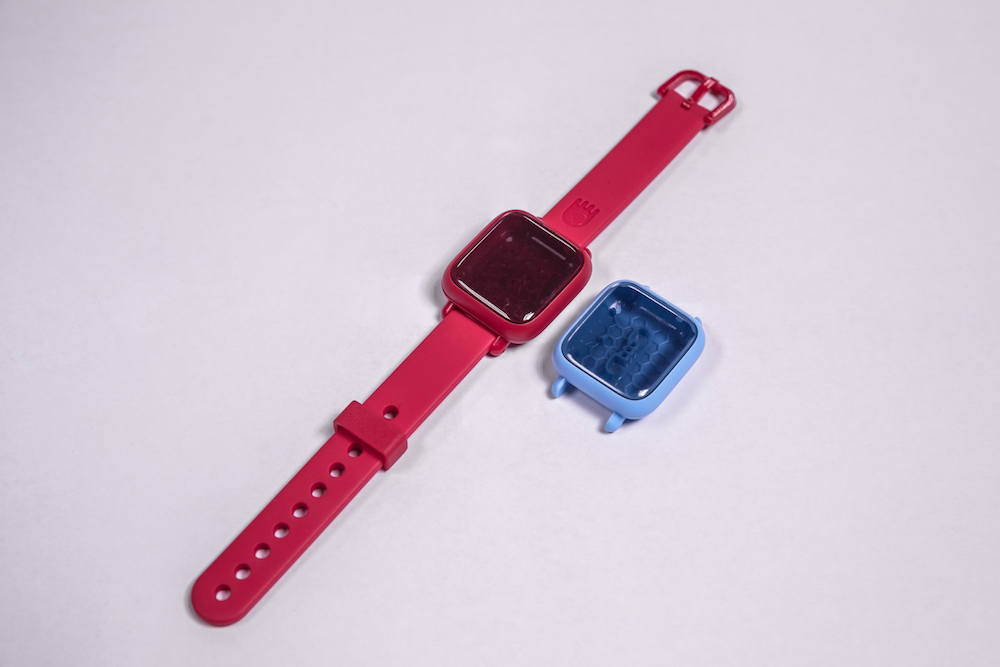
Joy’s mechanical engineers were able to iterate on designs quickly using Fictiv’s auto-quote system for instant 3D printing quotes. After receiving an instant quote, they could checkout securely with a credit card and conveniently pick up parts from Fictiv’s San Francisco office next-day.
Unexpected manufacturing challenges
As Joy’s team began to scale up production of the Octopus watch, they faced a number of manufacturing challenges. For example, critical components of the product, such as the wristband, are very small and delicate, making it prone to ripping and tearing. There were also challenges in achieving color consistency and hitting tolerances for the parts to mate properly.
“Initially, before starting collaboration with Fictiv, everything that could go wrong with plastic parts did go wrong,” said Joy COO Jean-Yves Bitterlich. “Different parts had different blue color and some parts had mechanical issues. In addition, some components did not pass certification and there were other issues with the manufacturing process.”
Like many fast-paced, growing companies, Joy has yet to build a dedicated supply chain team, which meant that Jean-Yves faced many painstaking hours, emails, and flights to try and manage these issues himself.
Discovering Fictiv’s Agile Manufacturing Solution for proactive consultation
While picking up 3D printed parts at Fictiv’s office in San Francisco, Joy’s engineers discovered that Fictiv had expanded its manufacturing network to include verified injection molding partners overseas and an opportunity arose to improve their current production supply chain with Fictiv’s Agile Manufacturing Solution.
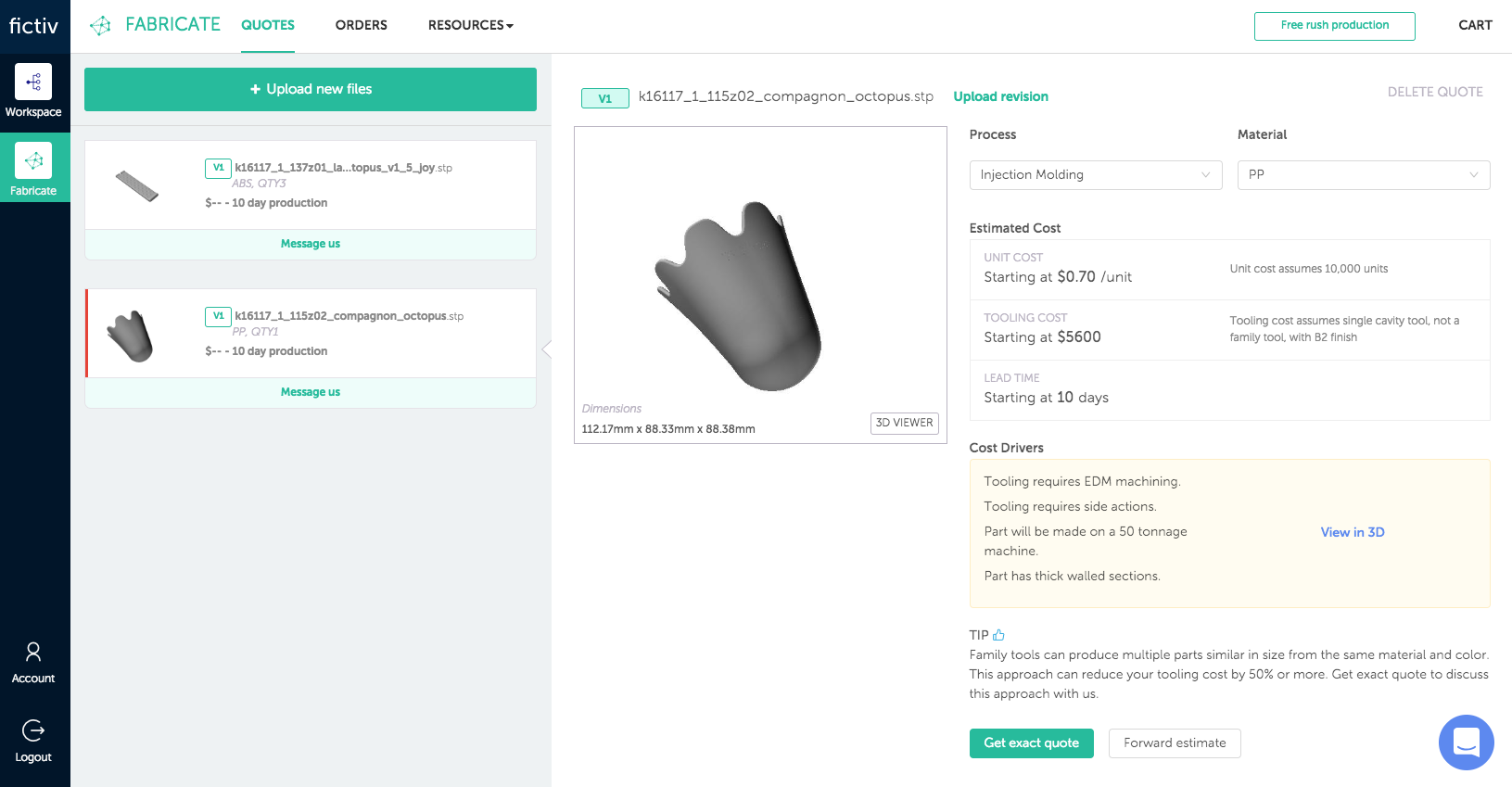
Bitterlich realized the team could now benefit from the same service experience and online order management system used with Fictiv Rapid Prototyping, now for high-volume injection molding.
To kickoff the quoting process, Fictiv was able to deliver a full design for manufacturing report and quote within 1 business day, in addition to instant pricing feedback and injection molding analysis upon file upload to Fictiv’s online platform.
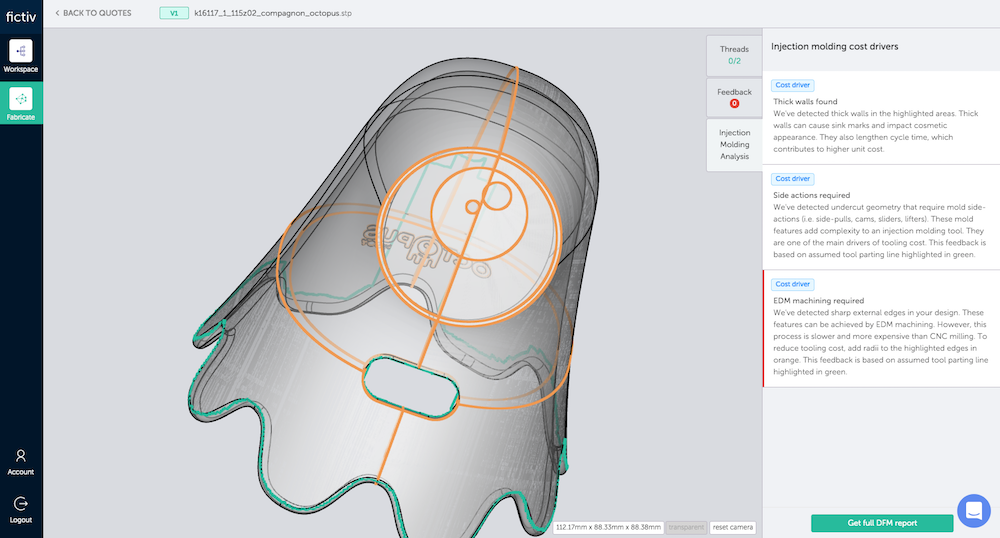
Bitterlich appreciated Fictiv’s proactiveness in delivering the DFM feedback and helpful information; in some cases, Fictiv anticipated Joy’s needs prior to Joy’s specific request.
“What I really liked when starting the interface with Fictiv was the sense of proactivity on Fictiv’s side,” said Bitterlich. “A very concrete example is the DFM. Fictiv studied the designs to pre-identify issues, even before we signed the contract. Fictiv was able to identify some issues on the drawing we submitted and we had very good technical discussions to resolve issues ahead of time. That was one of the signs that made me decide to go with Fictiv.”
A trusted partner to facilitate supplier communications
One of the key services Fictiv’s AMS provides is the facilitation of communications with manufacturers to effectively translate design intent.
“Communication is key… With Fictiv, the process was very smooth.”
“Fictiv’s Director of Overseas Manufacturing speaks both Mandarin and English and is great to work with,” said Bitterlich. “He is very pragmatic, is a good problem-solver and has been a helpful facilitator in terms of communicating design intent to the manufacturer.”
From past experience, Bitterlich understands how difficult it can be to effectively communicate design intent when there are cultural and language barriers in place, so he appreciated the ease of communication experienced with Fictiv.
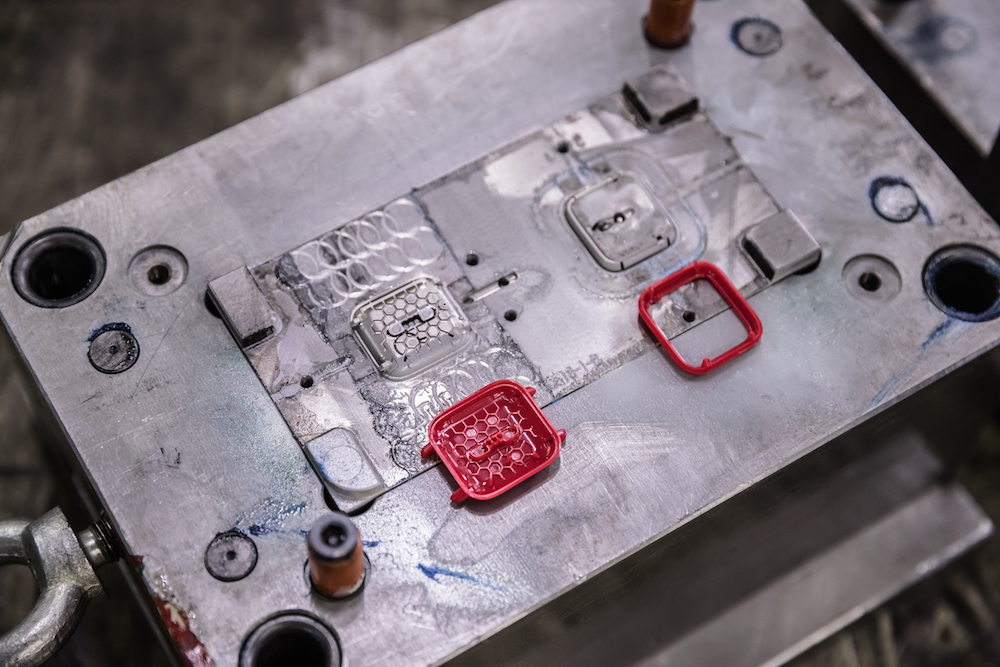
“Communication is key,” said Bitterlich. “Talking to a previous plastic supplier was challenging. We were unable to translate our issues, and in the end, a lot was done in writing, which has its own challenges. With Fictiv, the process was very smooth.”
Evaluating part quality
Bitterlich flew to China to see the T1 samples and meet Fictiv’s China team in person.
“The injection molding manufacturer we were matched with in China is also very good. I was very impressed,” Bitterlich said. “We solved a lot of points in just a few days while we were there, and that went very smoothly. That also made me consider Fictiv as a second supplier for product assembly.”
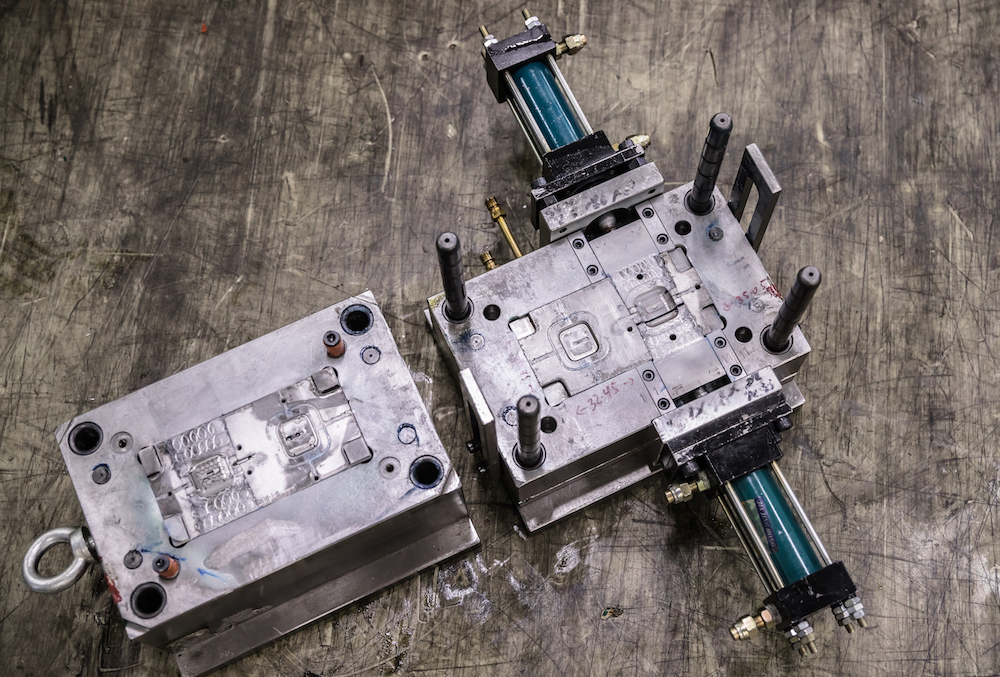
Trust is a critical component for choosing a manufacturing partner, and Bitterlich watched closely to see how Fictiv handled problems, noting that Fictiv divided problems into specific tasks that could be handled one at a time.
“We interacted quite a lot,” said Bitterlich. “We built a first version; we saw the parts; and we saw how Fictiv considered the parts. If I saw parts and said, ‘This or that could be improved,’ Fictiv would always consider every aspect and take everything seriously.”
“I have a lot of trust in Fictiv… That’s why I’m eager to bring Fictiv into more of our processes.”
Collaborating with Fictiv to scale up
To date, Joy has manufactured over 40,000 parts with Fictiv. Bitterlich is enthusiastic about Joy’s future collaboration with Fictiv and envisions working with Fictiv to manage more of Joy’s supply chain in the future.
“I have a lot of trust in Fictiv,” said Bitterlich. “I appreciate Fictiv’s proactivity, and I’m grateful for the interaction and dialogue we have with the team. That’s why I’m eager to bring Fictiv into more of our processes, from plastics to additional contract manufacturing work.”