Time to read: 2 min
We live in an era of centralized manufacturing. The prototyping and manufacturing ecosystem is dominated by massive companies that invest a ton of capital in warehouses full of machines that can fulfill demand.
When I was at Ford’s Silicon Valley Innovation Lab working to speed up development cycles, I realized there are real problems with this system. The main problem is that when you place an order, your part needs to navigate through a very complex network of layers.
Here’s what it looks like when you place an order with a traditional large manufacturer or prototyping facility:
- Submit quote
- Quote goes to sales rep
- Sales rep sends it back
- Once approved, order goes to project rep
- Project rep sends it to the operator
- Operator sends to QC
- QC sends to third party logistics
- Then it gets to you
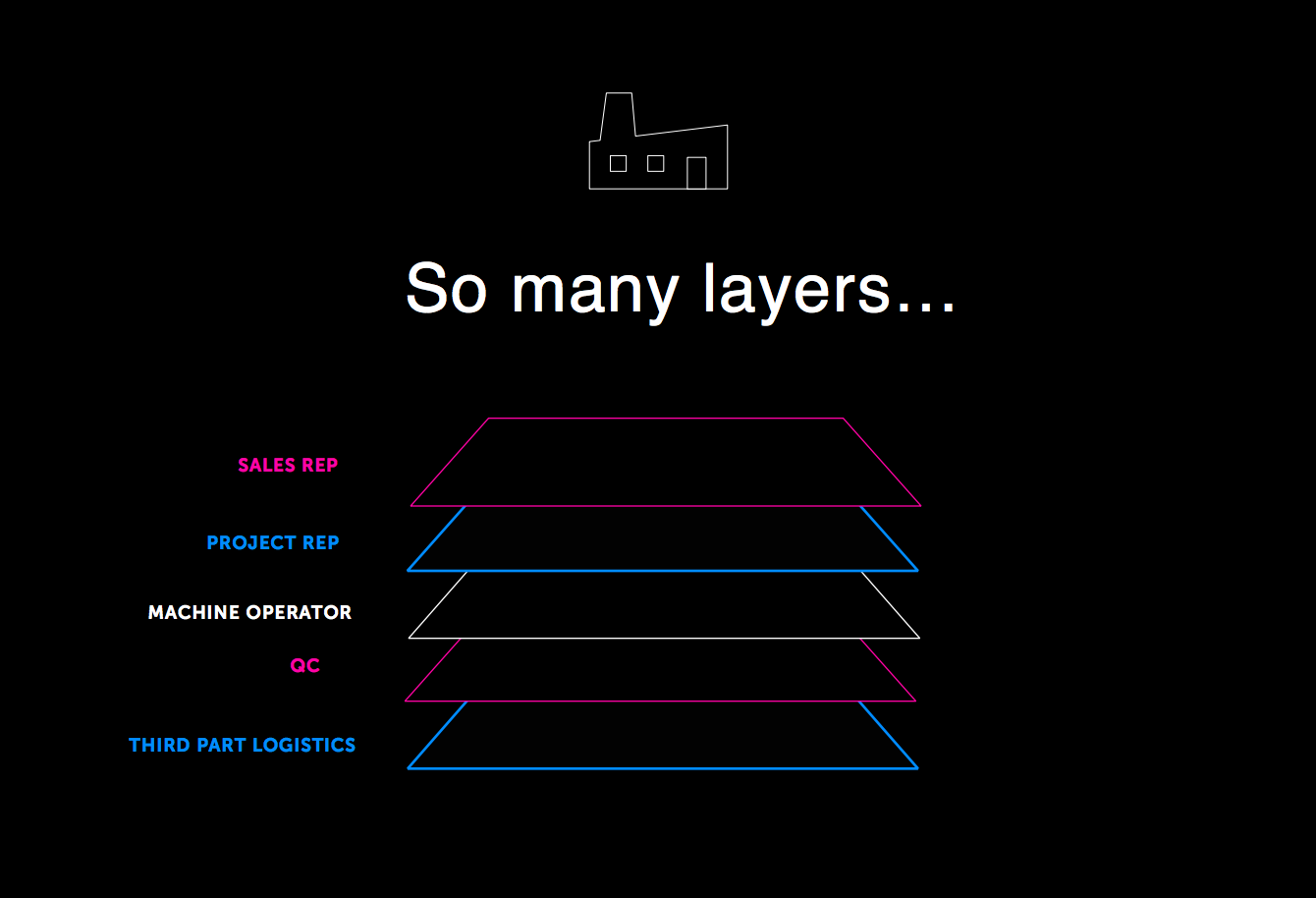
Now consider that any type of communication has to make its way through these layers every time something needs to be changed.
So when something goes wrong (and something always goes wrong in manufacturing), you have a lot of complexity to deal with and potentially a lot of time lost.
From an engineer’s perspective, when you’re in the prototyping and ideation stages, time is everything. It’s the way you stay ahead of the curve and beat out the competition. It’s the deciding factor for whether or not your product makes it to production. So even a 1-2 day loss matters significantly.
That’s why I left Ford 3 years ago to start Fictiv, where we’re building the future of distributed manufacturing for faster, leaner hardware development.
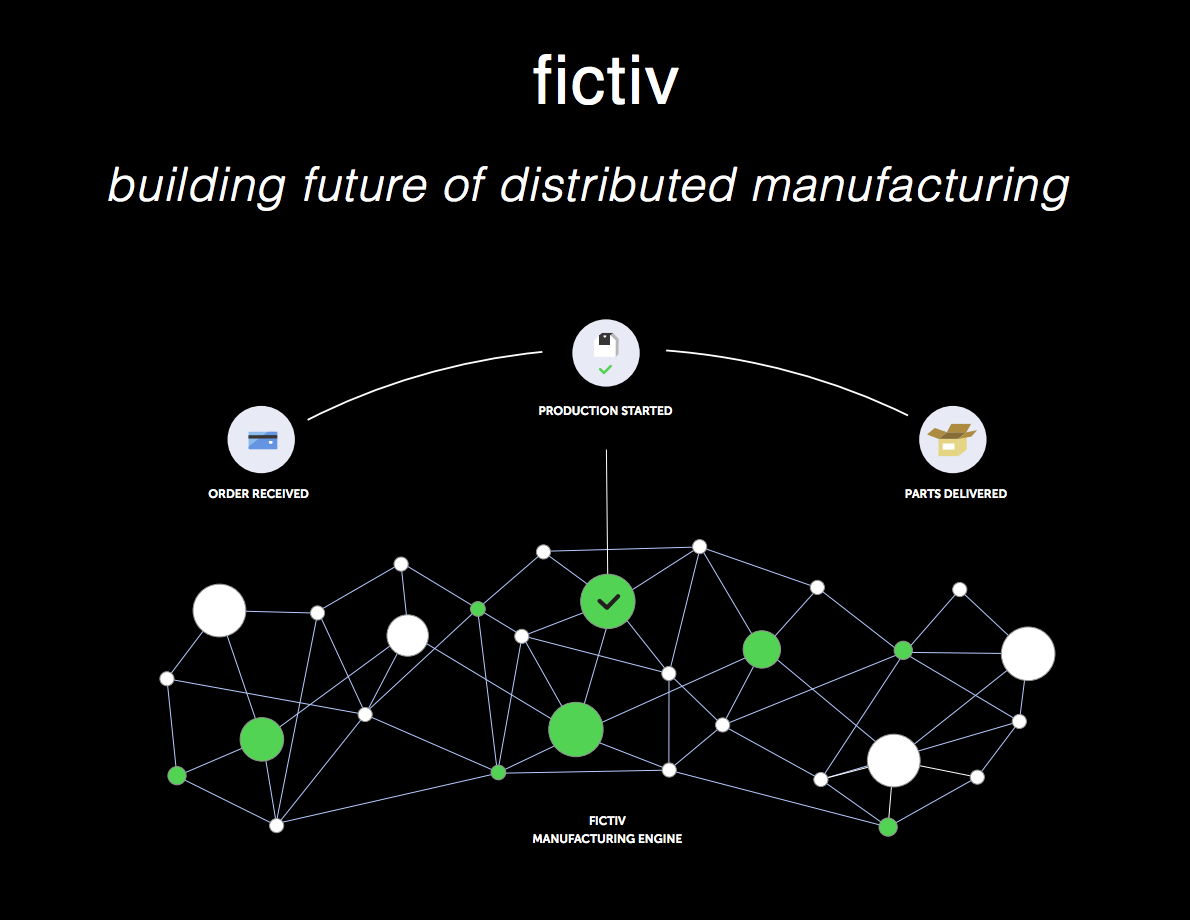
For more detail on the centralized manufacturing landscape, my prototyping experiences from Ford, and the potential of a distributed system for faster development, check out my talk from Hardware Con below.
And to take advantage of 24 hour turnaround on 3D printed parts, hop on over to Fictiv to get started.