Time to read: 6 min
Aluminum, or aluminium if you’re from the UK, is my favorite metal because of its high strength to weight ratio and suitability for a wide range of manufacturing applications. Aluminum is a commonly utilized material in many industries, and there are many aluminum alloys for CNC machining, CNC milling, CNC turning, welding, brazing, casting, stamping, forging, and laser cutting. Because aluminum is so versatile, it’s utilized in many industries including automotive, aerospace, and medical.
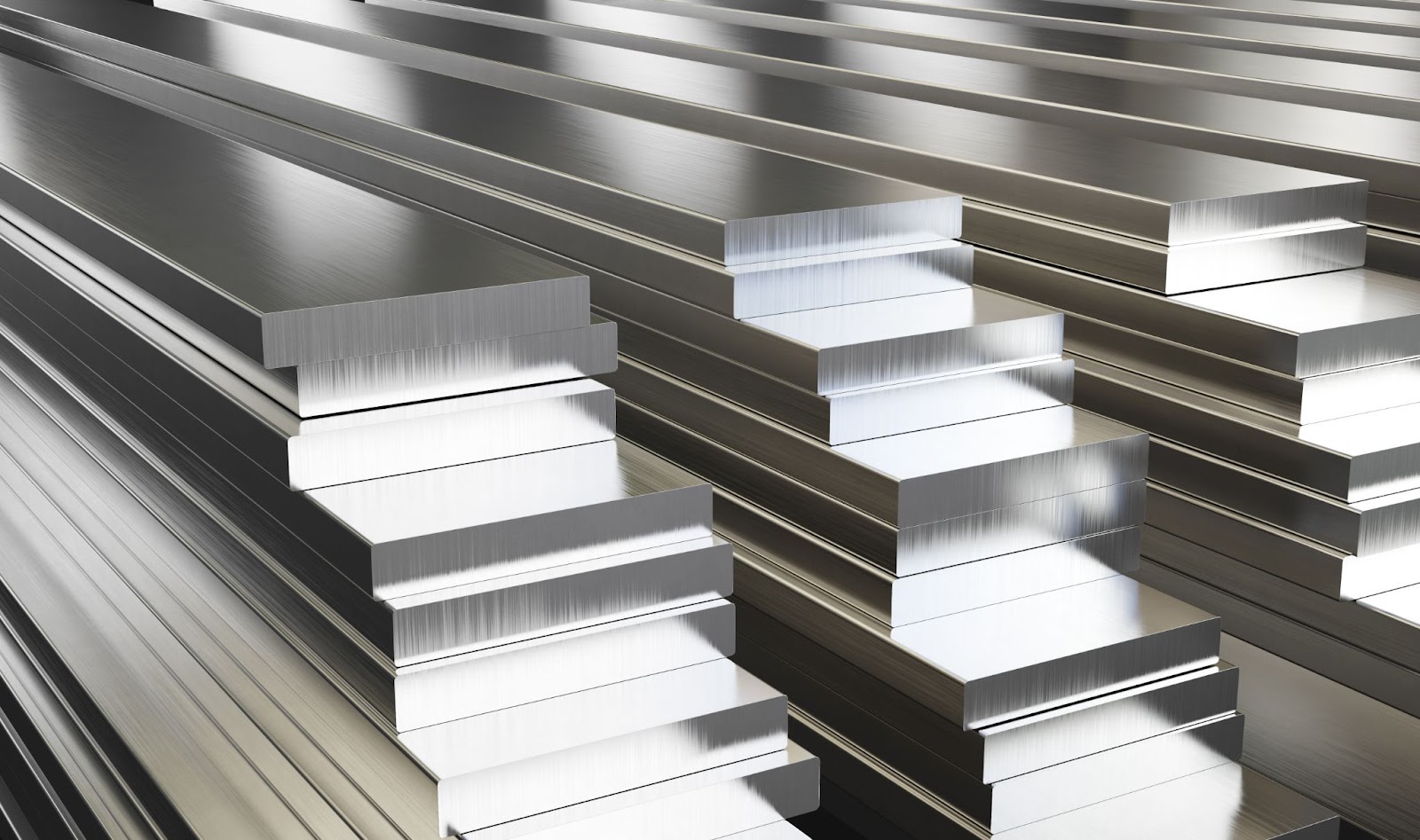
Read on to learn about some of the most popular aluminum-alloys and their common use cases, so you can choose the best material for your next project.
Pro-tip: all of the aluminum alloys discussed in this article are excellent choices for CNC machining, and there are many use cases beyond those listed for each alloy.
6061-T6 Aluminum
6061-T6 aluminum is precipitation-hardened 6061 aluminum. 6061 aluminum is one of the most versatile, common aluminum alloys that may be heat treated. The main alloying elements for 6061 aluminum are silicon and magnesium. The addition of silicon reduces the material’s melting temperature and improves its fluidity, while the magnesium provides greater strength and hardness.
T6 is the temperament of 6061 aluminum material that has undergone precipitation hardening to increase its hardness. The ‘T’ in the T6 designation refers to thermal tempering, which is a solution heat treating (above 900°F), followed by a quenching in water and then aging at a lower temperature (around 300°F) for several hours.
Advantages of 6061-T6 aluminum:
- High strength with relatively low density
- Excellent corrosion resistance
- Machinable
- Is paintable and accepts finishes easily
- Capable of being joined
Disadvantages of 6061-T6 aluminum:
- Experiences a reduction in strength when exposed to high temperatures
- Requires experience to weld
- Is susceptible to cracking (brittle fracturing) when bent
- Lower fatigue strength
Common uses for 6061-T6 aluminum:
- Consumer products like cabinet hardware
- High-strength automotive components
- Electronics industry parts like connectors and fittings
- Valve parts
- Bicycle frames
- Aerospace fittings
- Pressure vessels
- Hydraulics
- Marine industry fittings and bodies
- Automotive or locomotive frames
- Commercial property construction
- Infrastructure such as bridges or other structures
7075-T6 Aluminum
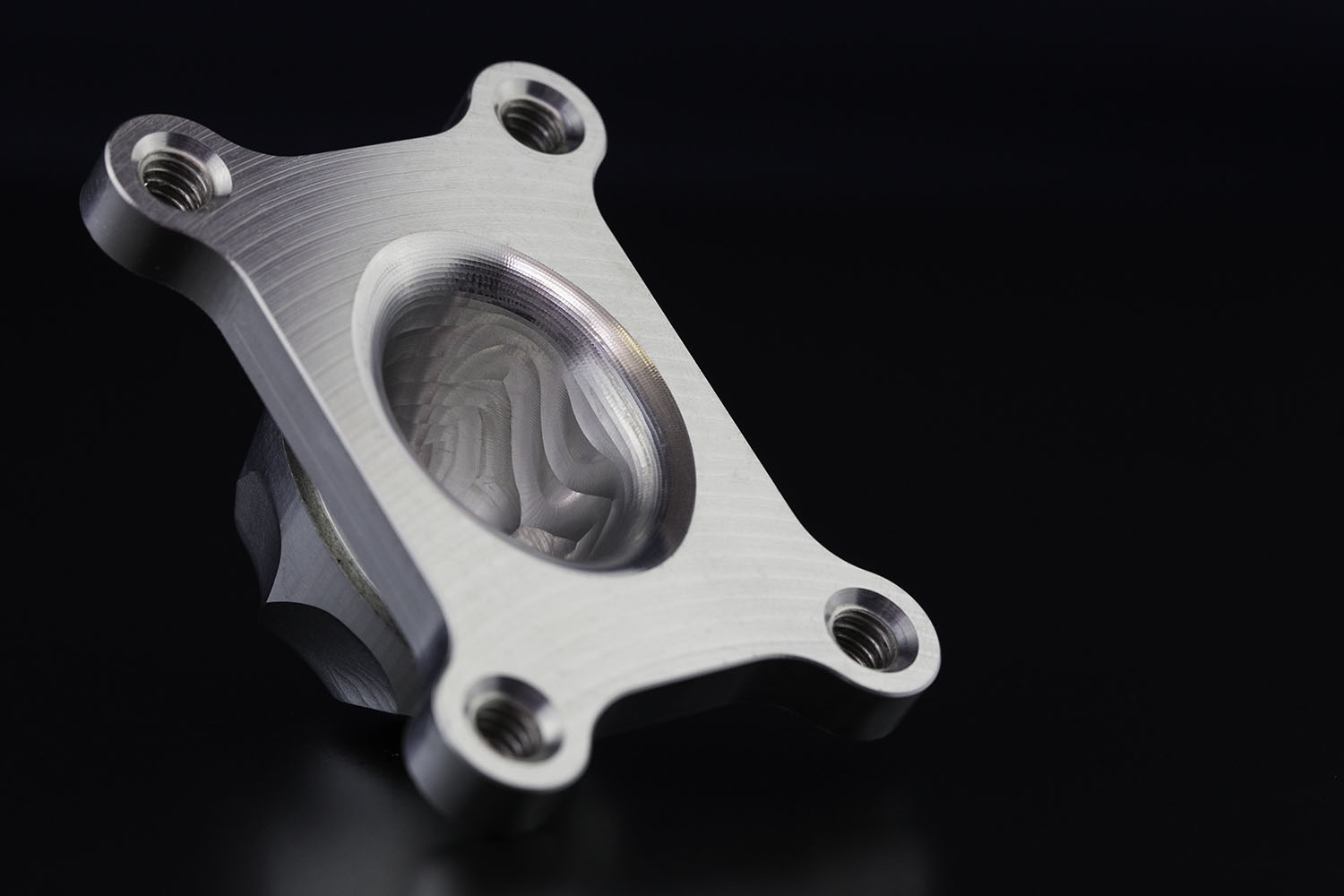
7075-T6 aluminum is precipitation-hardened 7075 aluminum. Like 6061-T6 aluminum, it has been tempered to the T6 condition. The primary alloying element for 7075 aluminum is zinc, which makes the strength of the aluminum alloy comparable to steel alloys — it’s one of the strongest aluminum alloys commercially available.
7075-T6 is not only the strongest aluminum alloy, it also has the greatest shear strength of all the alloys listed here. For this reason, 7075 aluminum is often referred to as aircraft grade or aerospace aluminum. But, this super high strength comes at a cost — 7075 aluminum has reduced corrosion resistance compared to weaker aluminum alloys.
Advantages of 7075-T6 aluminum:
- Ultra-high strength (tensile and shear strength)
- Is paintable and accepts finishes easily
- Formable
- Good fatigue strength
Disadvantages of 7075-T6 aluminum:
- High cost
- Lower corrosion resistance
- Fair machinability (requires more precision and experience)
Common uses for 7075-T6 aluminum:
- Aerospace frames and other structural parts
- Bicycle frames
- Tooling
- Gears
- Structural marine and automotive parts
- Plastic injection molds
7050 Aluminum
7050 aluminum is high strength and possesses excellent exfoliation corrosion resistance — exfoliation is a type of intergranular corrosion that specifically attacks the metal at or near the grain boundaries. 7050 is also tough and fatigue resistant.
It’s composed primarily of aluminum, zinc, copper, and magnesium. As with the other alloys, the zinc improves strength and magnesium increases the material’s hardness. The addition of copper increases the alloy’s strength and aids precipitation hardening.
Advantages of 7050 aluminum:
- Heat-treatable
- High fracture toughness
- High strength
- Excellent stress-corrosion cracking resistance (and exfoliation corrosion resistance)
- Machinable and formable (even in higher thicknesses)
Disadvantages of 7050 aluminum:
- Not ideal for welding, as the weld joints are weaker than 7075 aluminum
- Lower electrical conductivity
Common uses for 7050 aluminum:
- Aerospace structural parts
- Rock climbing equipment
- Bicycle parts
2024 Aluminum
2024 aluminum is a versatile, inexpensive aluminum alloy that’s weaker than some of the others on this list. It offers a good level of machinability and workability and is easy to finish. Its main alloying components are copper and magnesium, which increase its strength and hardness.
2024 aluminum boasts a high strength to weight ratio and is easily heat treated. But, its higher percentage of copper also reduces 2024 aluminum’s corrosion resistance. 2024 aluminum is often found as a clad sheet due to its lower corrosion resistance — so a different aluminum alloy or another type of metal altogether is exposed to the environment instead.
Advantages of 2024 aluminum:
- Heat-treatable
- Formable and machinable
- High strength
- Durable with a high fatigue strength
Disadvantages of 2024 aluminum:
- Lower corrosion resistance
- Only weldable through friction welding (otherwise not weldable)
Common uses for 2024 aluminum:
- Automotive wheels
- Aircraft structural components (skins too)
- Gears
- Engine components like pistons and cylinders
- Fasteners
5052 Aluminum
5052 aluminum offers good workability and electrical conductivity, making it a great choice for material selection in a wide range of applications. While it offers high fatigue strength, it does have a lower tensile and shear strength than other aluminum alloys.
Advantages of 5052 aluminum:
- Machinable and workable
- Excellent corrosion resistance
- Weldable
- High fatigue strength
Disadvantages of 5052 aluminum:
- Lower tensile and shear strength
- Can only be hardened by cold working
Common uses for 5052 aluminum:
- Fuel and oil lines for aerospace and automotive applications
- Sheet metal
- Lighting
- Wiring
- Marine industry components
- Consumer electronics like computers and televisions
6063 Aluminum
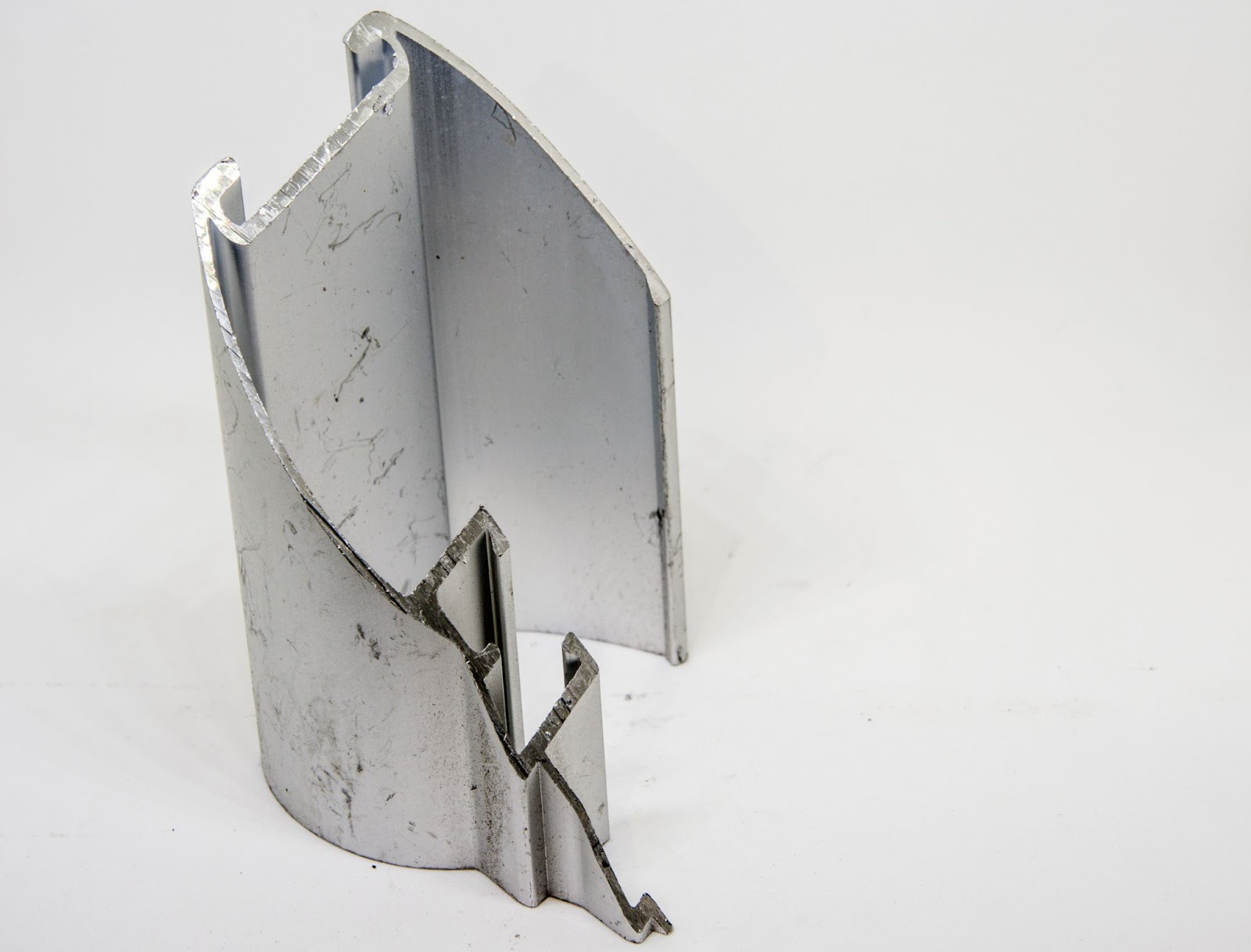
6063 aluminum is an alloy composed mainly of aluminum, silicon and magnesium. Due to 6063 aluminum’s silicon content, it’s well suited for extrusions and vacuum brazing — it has a lower melting temperature, and allows for grain boundary penetration of the braze alloy at the correct temperature.
Although 6063 has added magnesium, it’s good for applications where moderate strength is required and when high temperatures are not anticipated. It can also be easily formed into complex shapes and boasts a high corrosion resistance, so it maintains a nice luster throughout its operating life.
6063 aluminum is an alloy composed mainly of aluminum, silicon and magnesium. Due to 6063 aluminum’s silicon content, it’s well suited for extrusions and vacuum brazing — it has a lower melting temperature, and allows for grain boundary penetration of the braze alloy at the correct temperature.
Although 6063 has added magnesium, it’s good for applications where moderate strength is required and when high temperatures are not anticipated. It can also be easily formed into complex shapes and boasts a high corrosion resistance, so it maintains a nice luster throughout its operating life.
Advantages of 6063 aluminum:
- Smooth, lustrous appearance
- Is paintable and accepts finishes easily
- Good metal joining properties (welding and brazing)
- Heat treatable
- Good for complex geometries
- High corrosion resistance
Disadvantages of 6063 aluminum:
- Lower strength
- Is not easily machined
Common uses for 6063 aluminum:
- Piping
- Railing
- Heat Exchangers
- Decorative products like furniture
- Electrical conduit
- Commercial and residential architectural components like window frames
MIC-6 Aluminum
MIC-6 aluminum is a cast aluminum with excellent rigidity and consistency (tolerance) thanks to patented continuous cast process developed for manufacturing MIC-6 to ensure a stable, deformation-free, distortion-free cast plate. This cast plate solves the issue of distortion and temperature change deformation during machining and use of the cast plate. MIC-6 is precision cast aluminum ideal for tight tolerance machining with precise dimensions. With such high precision, MIC-6 is often utilized for precision measurement equipment.
Advantages of MIC-6 aluminum:
- Excellent dimensional stability
- Can be machined to tight tolerances
- Withstands distortion and deformation
- Excellent machinability with uniform chip production
- Cast material free of voids and impurities
Disadvantages of MIC-6 aluminum:
- Care must be taken when welding (but if you must, choose MIG welding)
- Only moderate corrosion resistance
- Not formable
Common uses for MIC-6 aluminum:
- Fixturing equipment like jigs
- Precision measuring equipment like gauges
- Robotics components
- Electronics components
- Medical industry parts
- Tooling for the automotive and aerospace industries
- Hydraulic equipment
Main Takeaways
Now you know why aluminum alloys are a great choice for CNC machined parts: low density, high strength, and high corrosion resistance. But, with all the excellent options available, how do you find the optimal material for your next CNC aluminum machining project?
Well that depends on your specific need. For example, if your application requires high strength, 7075 is a great choice. If you’re making super precise parts, MIC-6 is the way to go. For electronics components, 5052 works well.
Sourcing Simplified – Start Your Next Project With Fictiv
Once you’ve decided on the best type of aluminum alloy for your next project, the next step is to choose a supplier — and Fictiv is your operating system for custom manufacturing that makes part procurement faster, easier, and more efficient. In other words, Fictiv lets engineers, like you, engineer.