Time to read: 5 min
Humans have always produced tools and parts in various ways, and some of the oldest methods leverage the flexibility of metal at or near its melting temperature, such as casting and forging. Aluminum casting is a centuries-old manufacturing process that produces aluminum parts by pouring molten aluminum into a mold, then allowing it to cool and solidify into a final product. Many industries commonly use this production method due to its versatility and comparatively low cost.
Aluminum casting is used in aerospace, automotive, construction, and consumer goods industries, where lightweight and durable materials are required. It’s also commonly used to create intricate designs and shapes that cannot be realized with other manufacturing processes.
Read on to learn more about aluminum casting.
Pro-Tip: Check out our aluminum materials page to learn more about the different types of aluminum alloys.
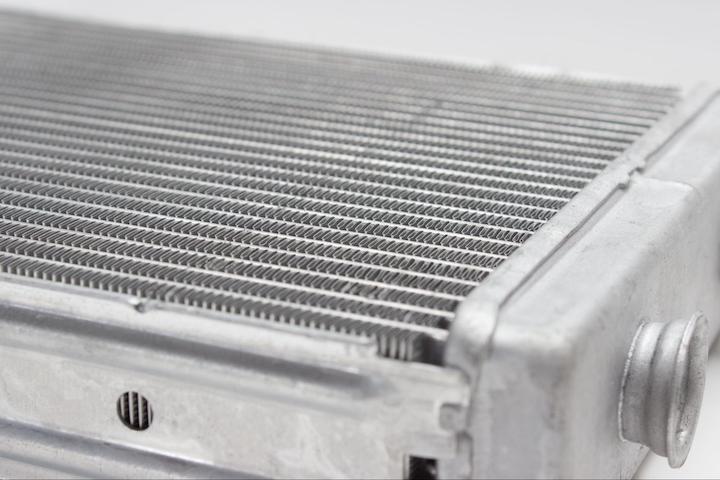
Definition of Aluminum Casting
Aluminum casting is a method of making things from molten aluminum, and here’s how it works. First, a pattern is made to create a mold, then melted aluminum is poured into the mold and left to cool down and harden. Finally, the finished product is removed, trimmed, and finished.
Cast aluminum is a useful material because it’s lightweight, strong, and food consumption-safe, making it an excellent fit for numerous applications. In addition, casting aluminum can create both large, complex parts in massive amounts and small and simple parts in low quantities.
The different aluminum casting processes include sand casting, die casting, investment casting, and permanent mold casting, and each has advantages and disadvantages.
Types of Aluminum Casting
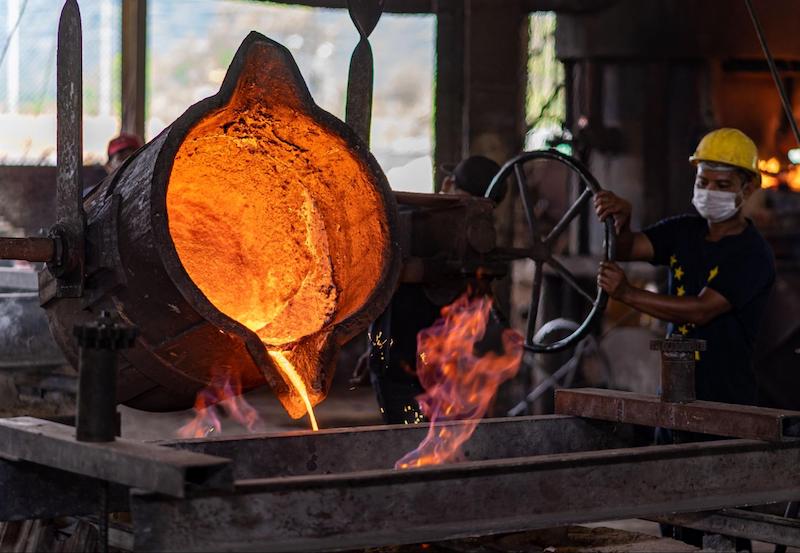
Each type of casting method works in a unique way, and has an optimal fit in the product development process, and is optimized for different parts in a given assembly. The aluminum casting process includes a few stages: design making, shape making, softening and pouring, and wrapping up and finishing. The type of casting process used depends on the specific application and requirements, and each process has unique advantages and disadvantages.
Sand Casting
Sand casting is the oldest and most prevalent casting method. In sand casting, a mold form is made by pressing sand mixed with a binder around an example of the ideal shape, called a pattern. Liquid aluminum is poured into the pattern and allowed to harden, producing both small and large parts alike. Since sand casting can’t be used for repeated production (some patterns are single use), it’s commonly utilized for small runs, test samples, and prototypes
Investment Casting
Investment casting uses a wax prototype of the ideal shape that is covered with a clay or ceramic shell. The wax is softened or melted, then removed, to create an empty ceramic shell, which is then filled with liquid aluminum. Investment casting produces intricate details, complex shapes, and various surface finishes.
3D printing technology allows investment cast molds to be produced from 3D printed stereolithography (SL) prototypes made of thin resin layers. This allows for the creation of highly complex geometric shapes, improved dimensional accuracy, reduced lead time, and more design flexibility due to the capabilities of 3D printing. Investment casting is also commonly called lost-wax casting for the lost wax used to create the mold.
Die Casting
This casting method relies on a metal mold called a die; hence the name die casting. In die casting, a metal mold is manufactured with CNC machining or another process, and liquid aluminum is injected into that mold, or ‘die’, and parts are formed quickly at high-pressure. There are two halves of a die-cast, the cover, and the ejector die, with the former being the fixed half and the latter being the moving half of the die.
Die casting, or high-pressure die casting, produces parts with excellent dimensional accuracy, high production efficiency, complex geometries, accurate and thin walls, and a good surface finish. Die casting is an optimal process for manufacturing high-volume production parts.
Permanent Form Casting
Permanent form casting, also known as permanent mold casting or gravity die casting, also uses a metal mold, and liquid aluminum is poured into the mold. Permanent form casting differs from die casting because it uses gravity or low pressure to feed the molten metal into the mold, while die casting uses high pressure to force molten metal into the mold.
Permanent form casting is good for low to medium volume production runs of parts and typically has a lower up-front cost when compared to die casting molds.
Pro-Tip: To design an aluminum casting mold, check out our best tips for CNC machining complex parts.
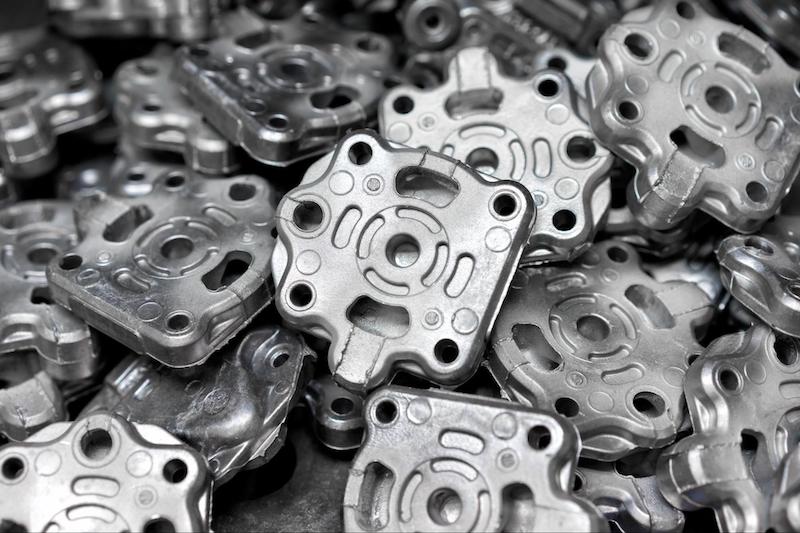
Importance of Aluminum Casting
Here are some reasons aluminum casting is an critical manufacturing process:
- Cast aluminum parts are strong and lightweight, which makes them ideal for applications where weight is a critical design feature. For instance, aviation and automotive companies depend upon aluminum casting because it decreases the weight of vehicles, without sacrificing strength.
- Aluminum casting can produce complex shapes and features, which makes it popular for various products, including engine parts, aerospace components, and consumer goods.
- Aluminum casting produces durable parts that can endure harsh environments and high temperatures. This makes it an ideal choice for industrial applications that require reliability and long-lasting performance.
- Aluminum casting can deliver large quantities of parts for a minimal price, which makes it attractive to organizations hoping to create quality parts at a minimal cost.
- Aluminum is a sustainable material that can be reused numerous times without losing its properties, and recycling aluminum is a relatively low energy process. This makes it an environmentally friendly choice for companies looking to reduce carbon emissions and operate more sustainability.
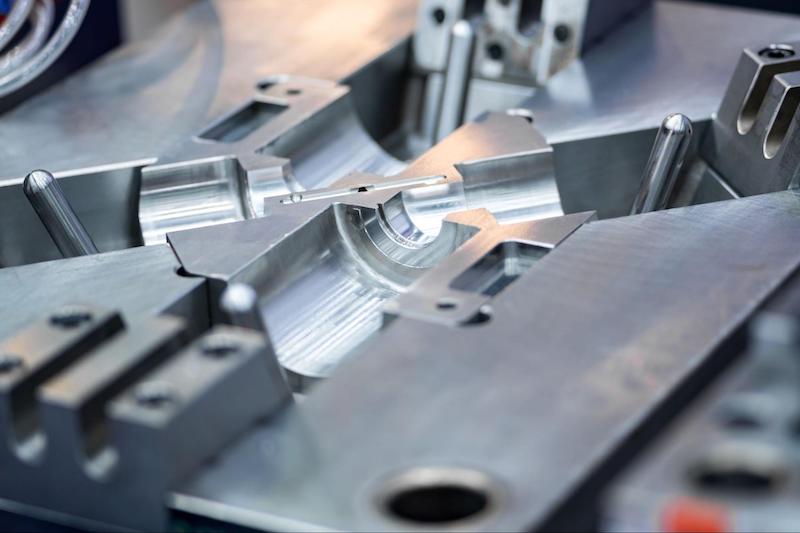
Aluminum Casting Applications
Aluminum casting has various applications in different fields, and is used to make engine parts, wing components, heat exchangers, valves, and landing gear in the aerospace industry. In the automotive industry, it produces motor blocks, chamber heads, and other components. Aluminum castings make window and entryway outlines and enhance components in the construction industry, and they create consumer cookware, lighting apparatuses, and furniture.
Aluminum casting is a versatile and cost-effective manufacturing process that offers a few benefits over different techniques. It’s fundamental in present-day fabricating, because it permits organizations to create items that satisfy strict execution guidelines. It’s also environmentally friendly, as aluminum is a sustainable material that can be reused multiple times without mechanical property degradation.
Fictiv – Your CNC Machining Partner
If you’re looking for a way to create your next aluminum casting mold, then CNC machining is the ultimate choice. And Fictiv can work with you to deliver exactly what you need — in as little as 2 days!
Fictiv is your operating system for custom manufacturing that makes part procurement faster, easier, and more efficient. Our manufacturing partners have some of the most talented machinists in the world, and they can make sure your CNC parts meet your specifications and are of the highest quality.
Create an account and upload your design today!