Time to read: 5 min
Copper is a truly versatile metal. Copper has a naturally beautiful, shiny finish that makes it desirable for artwork, cookware, kitchen backsplashes, countertops, and even jewelry. It also has excellent material and electrical properties for engineered, complex parts, like EDM electrodes.
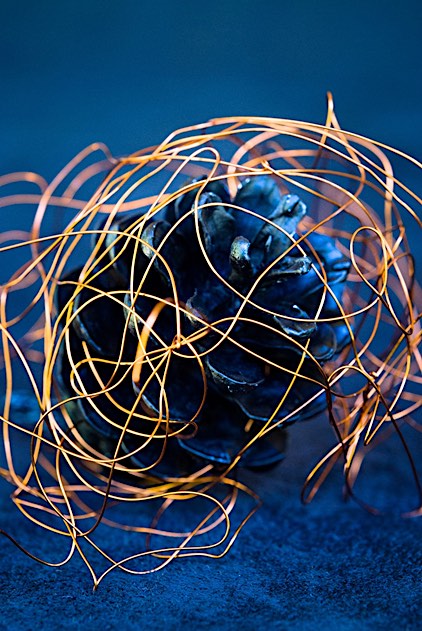
There are many benefits to using copper for machined parts. Copper is one of the most versatile metals in the world, with high resistance to corrosion and great electrical and thermal conductivity. In this article, we’ll discuss copper and copper alloy machining methods, design considerations, and finishing requirements that deliver more than just aesthetic benefits.
Techniques for Machining Copper
Pure copper is a difficult metal to machine due to its high ductility, plasticity, and toughness. Alloying copper improves its machinability and even makes copper alloys easier to machine than most other metallic materials. Most machined copper parts are made from copper alloyed with zinc, tin, aluminum, silicon, and/or nickel. These alloys require far less cutting force as compared to machining steels or aluminum alloys of comparable strength.
CNC Milling
Copper alloys can be machined utilizing various techniques. CNC milling is an automated machining process that utilizes computerized controls to manage the movement and operation of multi-point rotary cutting tools. As the tools rotate and move across the surface of the workpiece, they slowly remove excess material to complete the desired shape and size. Milling can be used to create different design characteristics such as grooves, notches, pockets, holes, slots, contours, and flat surfaces.
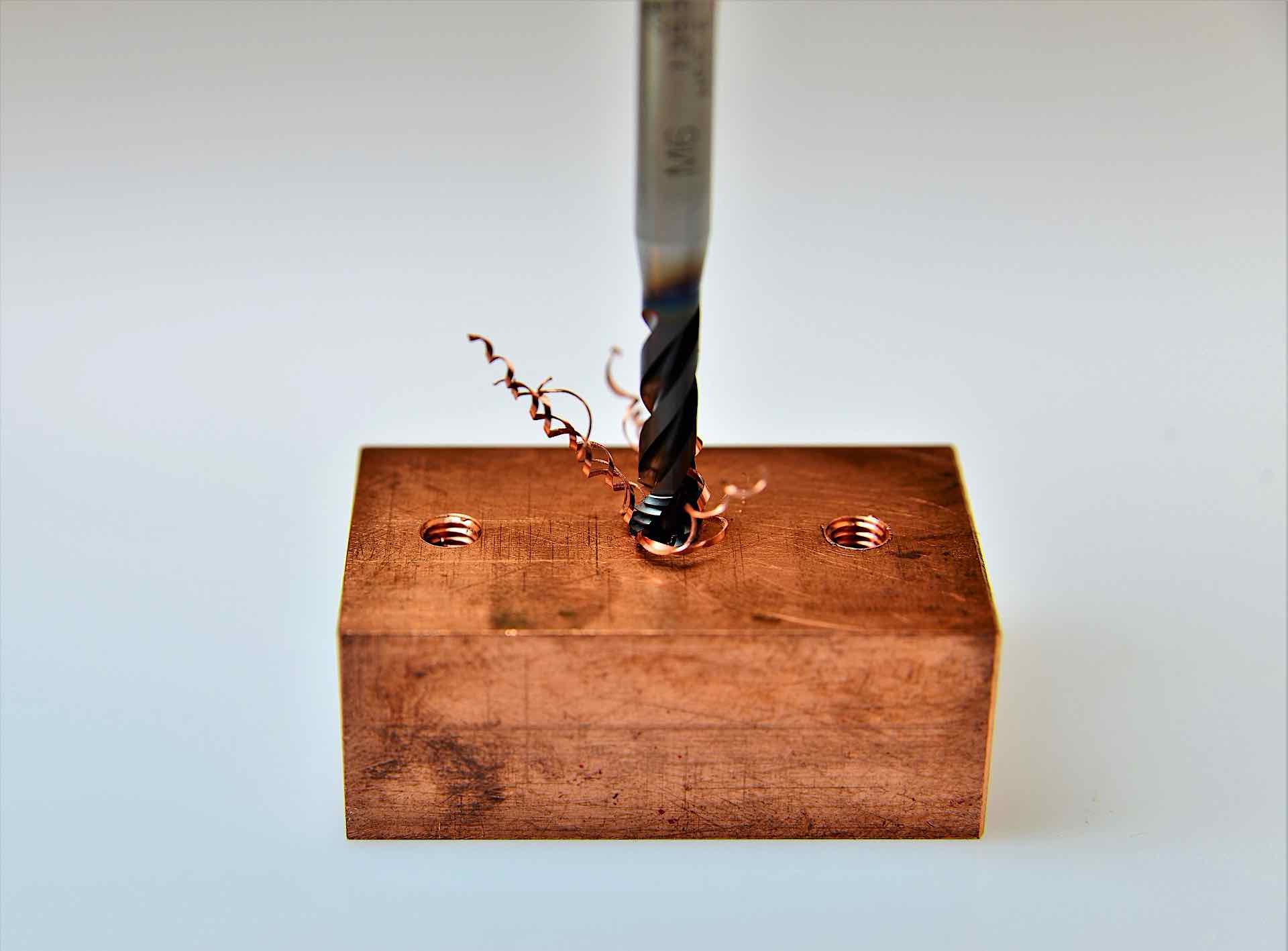
Here are some guidelines for CNC milling copper or copper alloys:
- Common cutting materials are carbide application groups such as N10 and N20, and the HSS grades
- You can double tool life by reducing the cutting speed by 10%
- When milling a copper cast alloy with a cast skin, reduce the cutting speed by 15 percent for a carbide group tool or 20 percent for an HSS grade tool
CNC Turning
Another technique for machining copper is CNC turning, where the tool remains stationary, while the workpiece moves to produce the desired shape. CNC turning is an adaptable machining system used to make many electronic and mechanical components.
There are many benefits in using CNC turning, including cost-effectiveness, precision, and increased manufacturing speed. When turning a copper workpiece, it’s particularly important to carefully consider your speed — because copper is an excellent thermal conductor, it creates more heat than other materials, which increases tool wear over time.
Here are some tips for CNC turning copper or copper alloys:
- Set the cutting tool edge angle in the range of 70° to 95°
- Softer coppers prone to smearing require a cutting tool edge angle of approximately 90˚
- A constant cutting depth and reducing the cutting tool edge angle results in lower stress on the tool and increases both tool life and cutting speed
- Increasing the angle between the major and minor cutting edges (the tool included angle) allows the tool to sustain higher mechanical loads and results in lower thermal stresses
Considerations for Design
When creating designs with copper machined parts, there are multiple factors to consider. Generally, you should only use copper where necessary because copper is expensive and producing an entire part out of copper is often unnecessary. A good design can leverage a small portion of copper to maximize the benefit of its uncommon properties.
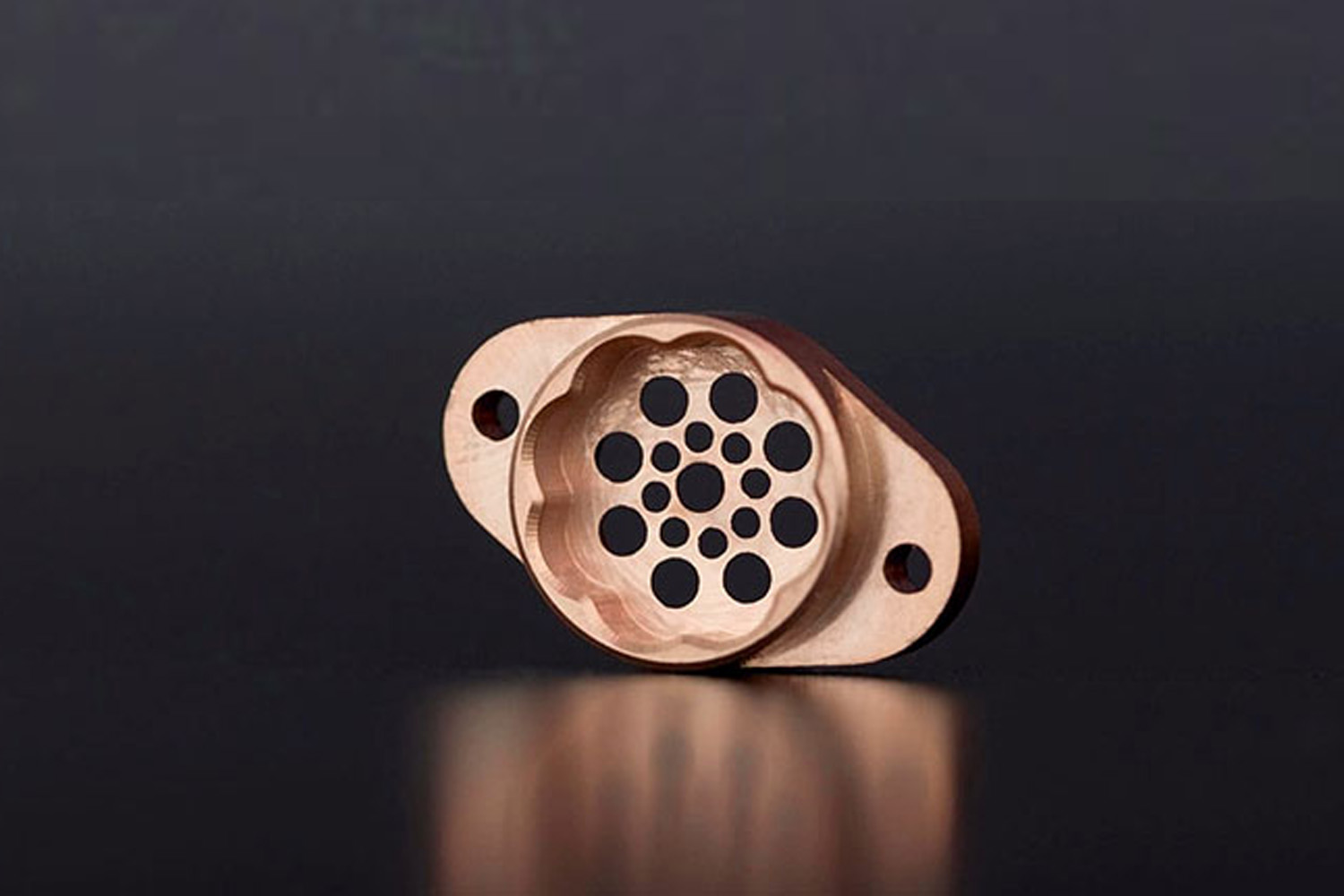
Here are some common reasons to opt for copper or copper alloy parts:
- High corrosion resistance
- High electrical and thermal conductivity, and easily soldered
- High ductility
- Highly machinable as an alloy
Picking the Right Material Grade
During the design phase, it’s important to choose the correct grade of copper for your application. For example, using pure copper for an entirely mechanical part is not only difficult but also uneconomical. C101 (pure copper) offers higher conductivity due to its purity (99.99% copper) but less machinability, while C110 is generally easier to machine and thus more cost-effective. So, choosing the right material grade depends upon the properties critical to your design function.
Designing for Manufacturability
DFM should always be top of mind no matter what material you use. At Fictiv we recommend you make your tolerances as loose as you can while retaining the functionality needed for your application. Additionally, it’s a good idea to limit dimension inspections, avoid deep pockets with small radii, and limit the number of part setups.
In particular, here are some specific best practices when designing copper parts:
- Maintain a minimum wall thickness of 0.5 mm
- Maximum part size of 1200 x 500 x 152 mm for CNC milling and 152 x 394 mm for CNC turning
- For undercuts, maintain square profiles, full radius or dovetail profiles
Finishing Copper
After machining comes finishing, and there are multiple factors to consider when deciding which process best fits your needs. The first place to look for surface finish control is within the CNC machining processes themselves. Some CNC machining parameters can be controlled to change the surface quality of the machined parts — for example, the nose radius, or tool corner radius.
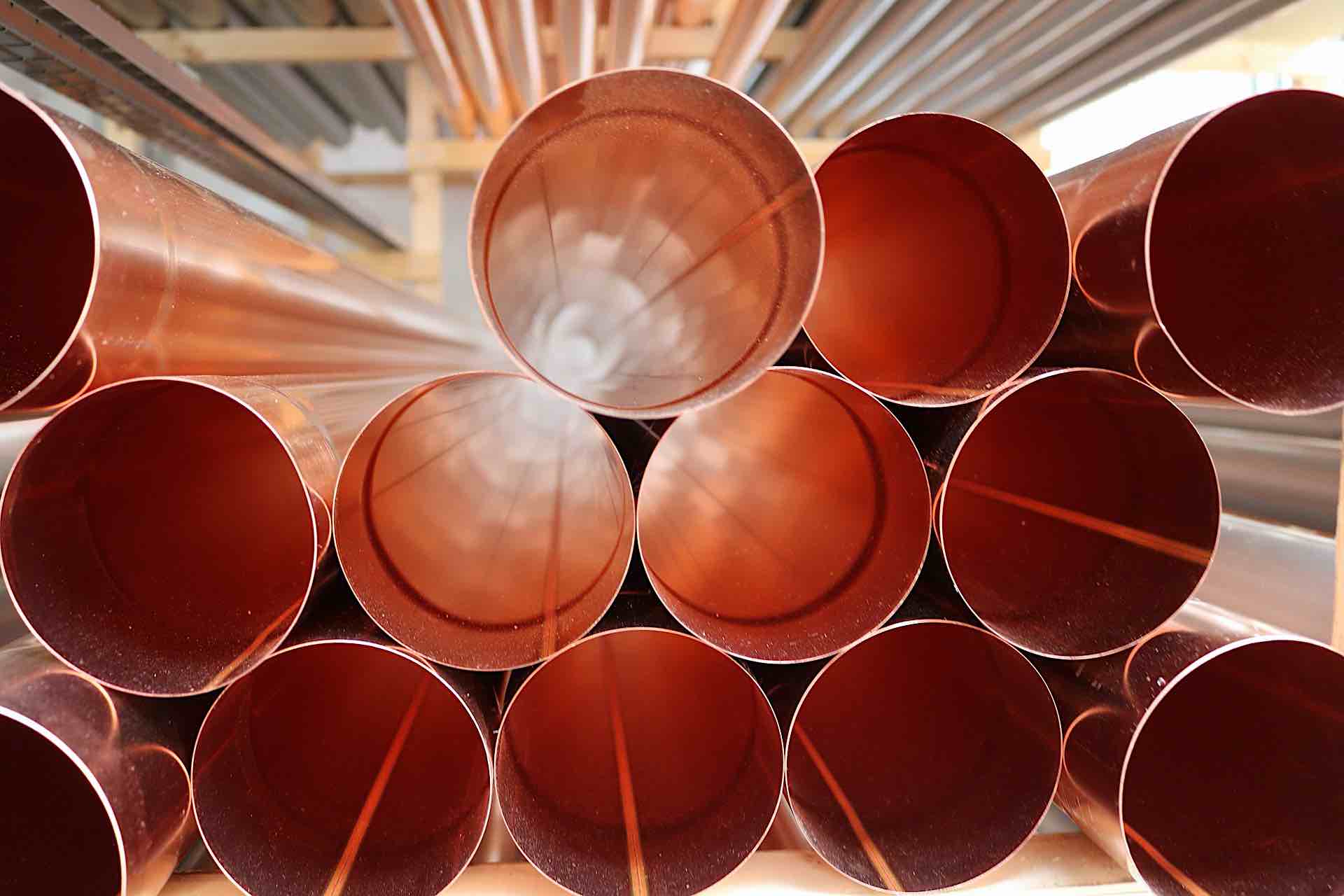
For soft copper alloys and pure copper, the quality of finish is directly and heavily dependent on the nose radius. The nose radius should be minimized, both to prevent smearing softer metals, and to reduce the surface roughness. Doing so creates a higher-quality cut surface because a smaller nose radius reduces feed marks. Wiper inserts are preferred to traditional nose radius tools because they produce an improved surface finish without modifying the feed rate.
You can also achieve part finish requirements through post-processing:
- Hand polishing – Although labor-intensive, polishing produces an attractive surface shine
- Media Blasting – This creates a uniform, matte finish and hides small flaws.
- Electropolishing – An excellent choice for finishing copper due to its incredible electrical conductivity that brightens and shines the copper.
There are also a wealth of other mechanical and chemical finishing processes, so it’s a good idea to evaluate all of your options when designing a copper machined part. Choosing an expert CNC machining service partner, like Fictiv, is critical in ensuring your parts are well machined and delivered on time to your specifications. You can learn more about our copper and copper alloy CNC machining capabilities on our site. And if you’ve already got your design, create an account and order your parts today!