Time to read: 4 min
Electrical Discharge Machining (EDM) is an amazing technology that can manufacture complex shapes in a variety of conductive materials — and it produces tightly toleranced parts with excellent finishes. EDM is a subtractive electro-thermal manufacturing method that utilizes electricity to erode the surface of a part.
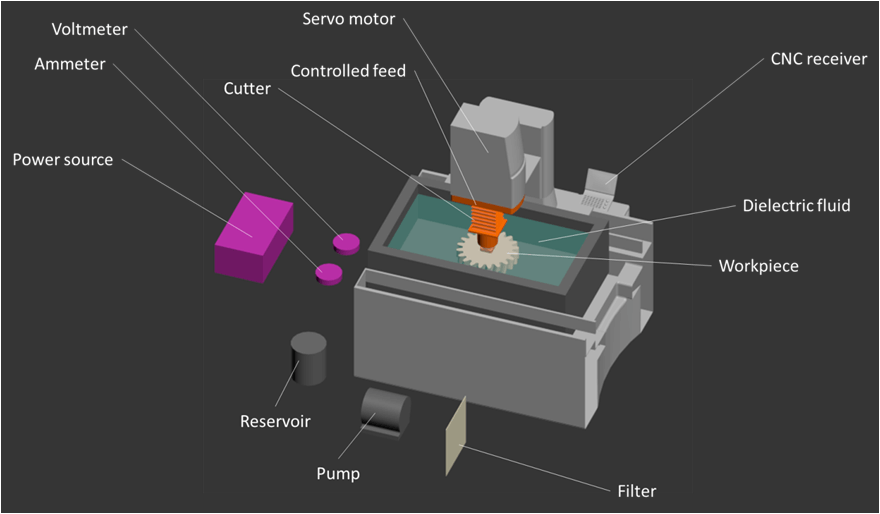
Basics of Electrical Discharge Machining
In general, EDM can be utilized to produce any electrically conductive part, even those produced from hardened workpieces and other typically hard-to-machine materials. The process generates no heat-affected zone, so it can produce thin walls and complex geometries without warping or deformation.
For EDM to work, both the workpiece and the electrode material must be electrically conductive as the process is literally ‘electric’. The process utilizes spark erosion created by a charge between the workpiece and the electrode to erode material from the workpiece. There are two common EDM mechanisms: conventional (also known as die sinking, or sinker) and wire EDM.
Wire vs. Sinker EDM
In wire EDM, the wire acts as the electrode whereby a charge is produced between the conductive part and the wire. This charge cuts the workpiece like a band saw, but the wire doesn’t contact the part.
In sinker EDM, a pre-machined, electrically conductive electrode is shaped to be the inverse of the form of the part it will make. The EDM machine feeds the electrode down into the workpiece that’s submerged in a dielectric fluid. From there, what workpiece is eroded by an electrical charge. The process removes the material and produces a cavity in the workpiece that is the same shape, but slightly larger than the electrode.
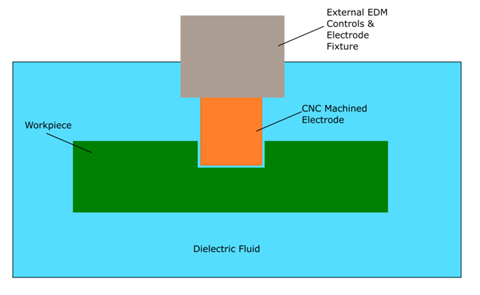
Sinker EDM utilizes consumable parts (or wear parts), including pneumatic valves, contact sleeves, nozzles, bearings, and the electrodes, which must be replaced periodically as they wear. Replacing the electrodes requires CNC machining electrically conductive workpieces to create the necessary dimensions. Copper alloys are commonly used for EDM electrodes, in part because copper alloys are easily machinable.
Sinker Electrode Material Selection
The manufacturing of a sinker EDM electrode plays a large role in the quality of the finished product, and choosing the right material is critical if you want a quality electrode. Graphite, tungsten carbide, and copper alloys are all typically used for electrodes.
Copper alloys are commonly used for electrodes because of their greater durability and conductivity as compared to graphite. They also have greater machinability as compared to tungsten carbide and offer comparatively low tool wear given their material removal rate.

Different copper alloys may be considered for EDM electrode material, including copper tungsten and brass. Generally, such electrodes produce a mirror-like surface finish and work well for small cavities. Copper tungsten sintered electrodes are heat resistant with high electrothermal conductivity and provide a relatively low wear rate versus speed of material removal. Brass, a mixture of copper and zinc, is a good electrode material for less precise work because it’s a softer material.
CNC Machining Sinker EDM Electrodes
CNC machining is the optimal method for manufacturing copper EDM electrodes because it creates accurate and intricate details at a relatively fast pace, for a low cost. CNC machining is also versatile and can produce both complex geometries and simple features like flat surfaces. Additionally, when a CNC machined electrode wears beyond its useful dimensions, it’s easy to make an identical electrode to replace it.
Obtaining a CNC machined electrode is a relatively straightforward 5-step process:
- Design: First, you have to design the electrode. The electrode is designed as the negative of the shape you are trying to machine with EDM. Ensuring the part drawing and solid model are complete and correctly toleranced are key. Accurate GD&T will ensure uniformity and a smooth handoff of the 3D part model to your CNC machining vendor.
- Ordering: Upon submission of your request for quote, your CNC Machining vendor will then review their capacity to ensure they have the equipment available to machine the electrode to the specified requirements. Then you’ll get pricing and lead time information — note that unit costs for electrode machining may be higher than usual because of the low part volume.
- Machining: Once you agree on the price and place your order, your vendor will perform preliminary set-up including designing fixtures as needed and programming the CNC machine to meet your part requirements. The electrode is then machined per the requirements in the drawing.
- Post-processing: EDM electrodes which have been CNC machined typically require minimal post-processing. Grit blasting or cleanup of sharp corners may be required to ensure easy handling of the electrodes.
- Inspection and delivery: The CNC machined electrode will be inspected to ensure it meets the specification of your drawing, purchase order, and any requirements that are called out. Inspection may be completed with micrometers and gauges or Coordinate Measuring Machines (CMM) to ensure quality.
As you can see, sourcing copper EDM electrodes for any design is relatively simple thanks to CNC technology. With its high machinability and conductivity, copper alloy electrodes are a great choice for your next sinker EDM project.
Regardless of the complexity of your design, Fictiv has a network of manufacturing partners who can meet your needs and unlock your innovations. Our platform provides instant quotes, free DFM feedback, and our CNC machining services can deliver parts and electrodes in as little as 2 days with tolerances as tight as +/- 0.0002 in. Sign up for a free account and get an instant quote today!