Time to read: 7 min
Sometimes when you’re choosing what manufacturing method to use, the requirements for dimensions, materials, and specifications make conventional production processes too expensive. Milling, turning and drilling to machine a block with openings and chamfers that will hold bearings or other components is complex and difficult. Of course, you can cast parts, but the up-front cast molding investment only makes sense when fabricating parts in high volumes.
What if you’re working on a prototype in its early design stages and you only need to fabricate only one or two parts? Milling and turning take a lot of time and waste a lot of material, but electrical discharge machining services (EDM) can be a more efficient solution. EDM is a manufacturing process where material is removed from a workpiece by applying a series of current discharges between two electrodes separated by a dielectric bath liquid.
Why would you use EDM manufacturing as opposed to traditional methods? Read on to learn about the different types of electrical discharge machining and find out.
Types of EDM Manufacturing
- Wire Cutting Electrical Discharge Machining: For this type of EDM, a wire is used as an electrode, and is continuously and automatically fed with a spool during the process. Typically, the fluid is ionized water and the wire is brass or copper. Checking the workpiece material and wire electrode materials to determine best electrical discharge machining process parameters is highly recommended to guarantee compatibility and to prevent corrosion. Because a wire electrode is used to cut the workpiece, only cuts through the whole thickness of the workpiece are possible.
- Sinker Discharge Machining: This process is known as die, traditional, or Ram EDM. It can produce complex geometries not possible with Wire EDM. The electrode material is typically graphite or copper machined into a specific shape that’s the inverse of the intended final geometry of the part. Once the electrode is shaped, a process called “electrode wear” damages the workpiece by the sparks to form the correct geometry. Unlike Wire EDM, Sinker EDM can do both partial cuts and cuts completely through the workpiece.
- Hole Drilling Electric Discharge Machining: The third type of EDM is used for drilling. Hole drilling EDM is able to machine very small, deep holes, which is difficult or even impossible with conventional drilling methods. Additionally, hole drilling EDM is super clean, and doesn’t require any deburring. In this process, the electrodes are tubular and the dielectric fluid is fed through them. Similar to the other EDM types, the electrode cuts/erodes the workpiece, but due to the discharged gap, the electrode doesn’t actually contact the workpiece. This minimizes deflection of the tube electrode as compared to drill bit deflection in conventional drilling processes.
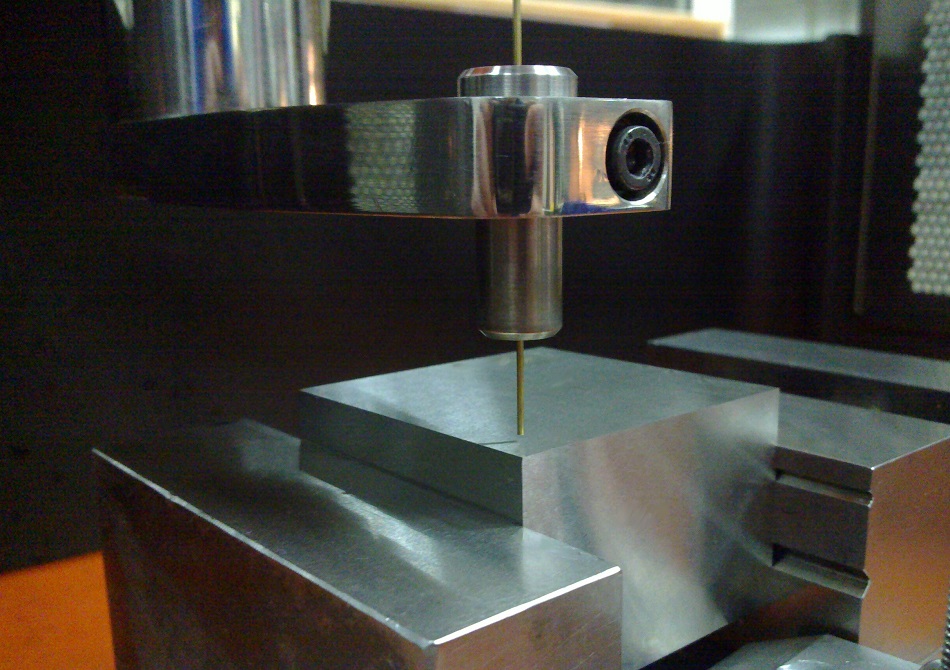
Components of an EDM System
While the three types of EDM differ in their use, the structure of each system is similar. You can see the typical components of an EDM system in Figure 2 below:
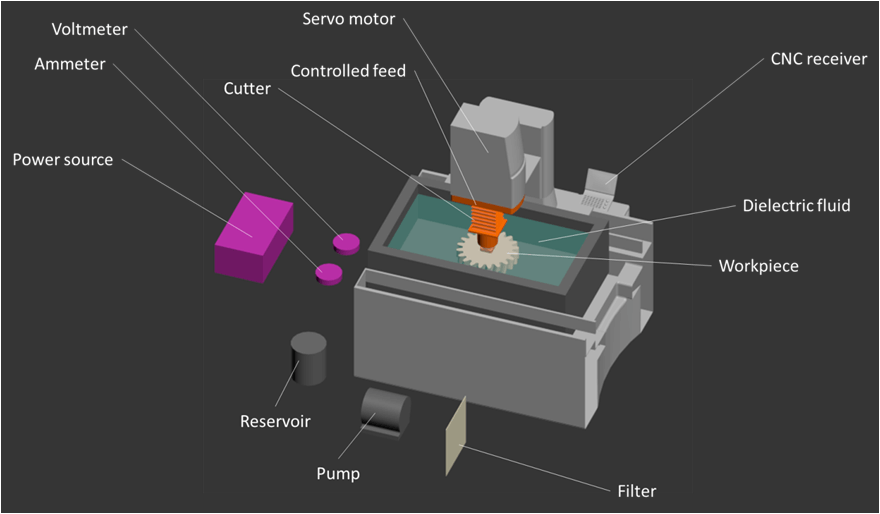
- Computer Numerical Control (CNC) corresponds to the unit that processes the path of the tool. There are several software programs — like FeatureCAM from Autodesk — that can simulate and design these CNC codes for your geometry.
- Power source: power supply that provides energy to the spark
- Voltmeter, ammeter: instrumentation to measure electrical potential and current
- Cutter: tool to cut the workpiece
- Workpiece: material to be cut
- Dielectric fluid: serves as a medium between the cutter and workpiece. It also controls the electrical discharge and absorbs heat during the process, which cools the workpiece. Another function of the dielectric fluid is remove debris.
- Pump: controls the flow of the dielectric fluid so that the EDM equipment can run continuously.
- Filter: maintains the condition of the dielectric fluid (resistivity/conductivity), temperature of the water, and other conditions. Debris that could affect those conditions are filtered out, maintaining a clean system.
- Fixtures: boards, jig tools and other workholding setups that will keep the workpiece and cutter stable and in a specific position.
Characteristics of an EDM process
In EDM, the electrode and workpiece are immersed in a dielectric fluid. The produced electric spark erodes or cuts the workpiece to remove material and achieve the designed geometry. The movement of the electrode is controlled by CNC programs, and there are a few key concepts you need to understand to ensure the process functions well.
Figure 2: Representation of EDM circuit
Discharge gap
In order to generate sparks between the electrode and the workpiece, there must be a gap, sometimes called “discharge gap”, which is typically in the 0.005 – 1 mm range. If the electrode and the workpiece are in contact, then sparks are not produced. This gap and the movement of the electrode are controlled by a servo mechanism on the EDM system.
Electrode wear ratio
This ratio corresponds to the volume of material lost from the tool electrode divided by the volume of metal removed from the workpiece. Sometimes it is represented by the percentage of mass loss of the tool divided by amount of work.
Removal rate
The speed at which the spark removes material from the workpiece. Typical mass or volume units are used to quantify it ([g/min] [mm3/min]).
Polarity
In order to apply voltage between the workpiece and the electrode, one must be positive, and the other negative. It’s common to use the term “positive polarity” or just “polarity” when the electrode is negative and the workpiece is positive. A “reverse polarity” setup is when the electrode is positive, and the workpiece is negative. We highly recommend familiarizing yourself with your combination of electrode/workpiece materials to determine the best settings and process parameters for your application. The polarity can impact the material removal rate, “electrode wear ratio” and surface roughness, which in turn produces wear, speed and stability effects.
What are the Advantages and Disadvantages of EDM?
Now that you know the basics of the different EDM processes and how EDM generally works, it’s time to consider the benefits and limitations of electrical discharge machining.
The good
- Produces complex geometries without inducing stresses
- Deflection of drilling electrodes is minimal compared to conventional drill bits
- Minimal or no debris produced
The bad
- Process speed is typically slow
- Additional processes necessary to create electrode tooling
- Must carefully consider workpiece and cutter materials before selecting process parameters to prevent issues
Applications for EDM
Once you understand the limitations of electrical discharge machining, the applications for this process become clear. EDM is principally used to generate parts that are difficult to machine using traditional techniques. Below are some examples of EDM applications from the automotive, aerospace, medical, consumer products, and jewelry industries.
Dies, Molds and Tools
EDM can accurately cut hardened steel, so it’s often used to generate complex geometries of dies, molds and tools. There’s no need for heat treatment during EDM cutting, so you can control microstructure and design your molds, dies and tools in a more efficient way.
Prototypes
EDM is not typically used in mass production due to process time, but is a great option for prototypes. It’s especially suited to make preliminary concepts when manufacturing limitations are not yet considered — so the design can focus on functionality and explore different geometries.
Components with precise holes
Due to the accuracy and size capabilities of EDM Drilling, this process is used in a variety of precision applications. One example of application is turbomachines like jet engines, gas and steam turbines: cooling holes on turbine blades are designed with tight tolerances and dispersed throughout the blades in order to maximize the cooling effectiveness and turbine performance. Because the turbines are typically made of hard materials and holes are small but with specific patterns, EDM drilling is a great choice for this application. Microscopic orifices in lab equipment and polymer extrusion are another application example; components like spinnerets are manufactured with the help of EDM and they are used to extrude polymers solution or polymer melt to form fibers for similar reasons than the turbine holes.
High temperature alloys and exotic metals
EDM works on a wide variety of materials, so a broad range of components and products for aerospace are produced with EDM. For example, titanium runs the risk of catching fire when milling. However, because the EDM process is submerged in fluid, the risk is mitigated.
Medical devices
Surgical tools, implants and prosthetic joints are also created with EDM because the process can machine hard metals. EDM also has the advantages of cleanliness (from the constantly refreshed fluid), the ability to machine sharp inside corners, and the lack of burrs.
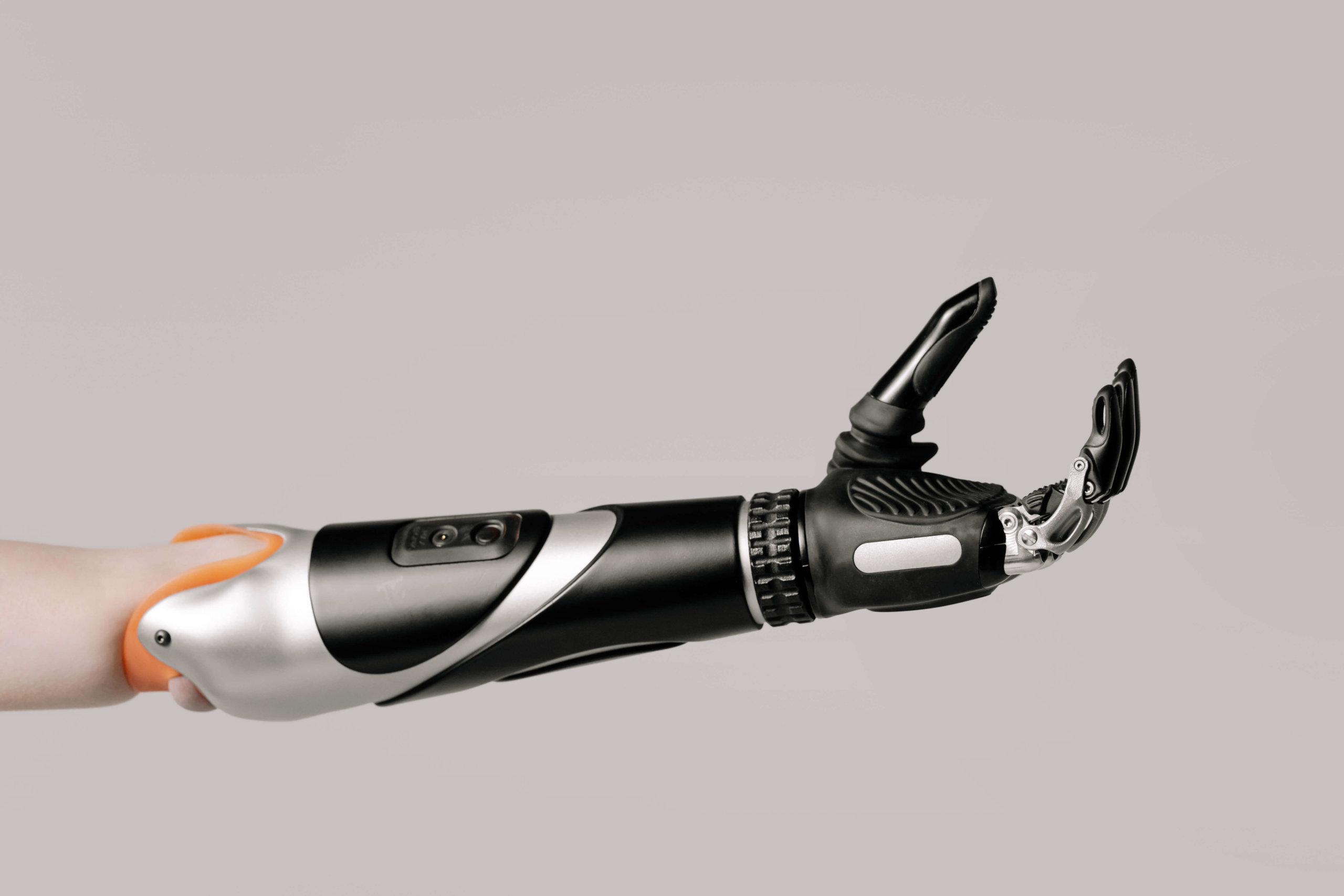
Badges and jewelry
Creating, repairing and personalizing designs with EDM is easy, from security badges with complex insignias to cutting jewels. Even when working with exotic materials and small parts, precision EDM manufacturing can produce intricate, detailed designs and engrave messages on pendants, rings, and bracelets.
Conclusion
So there you have it, the basics of electrical discharge machining. We hope this article has given you a better understanding of EDM, how it works in contrast with other manufacturing processes, and its advantages and limitations — and now you can add EDM to your manufacturing process toolbox.
Learn more about Fictiv’s Electrical Discharge Machining capabilities here. Sign up for a free Fictiv account to upload your part or get an online cnc quote today!