Time to read: 5 min
CNC machining is a complex and revolutionary subtractive manufacturing method whereby a metal or engineering plastic raw material is turned into a complex part. Whether components for aerospace, medical, automotive, consumer products, or robotics, CNC-machined parts are in high demand.
Once a new product is designed a critical part of the new product development process is to price out production costs. To get a rough estimate, a few factors determine how much it will cost to CNC machine a custom part. Read on to learn more.
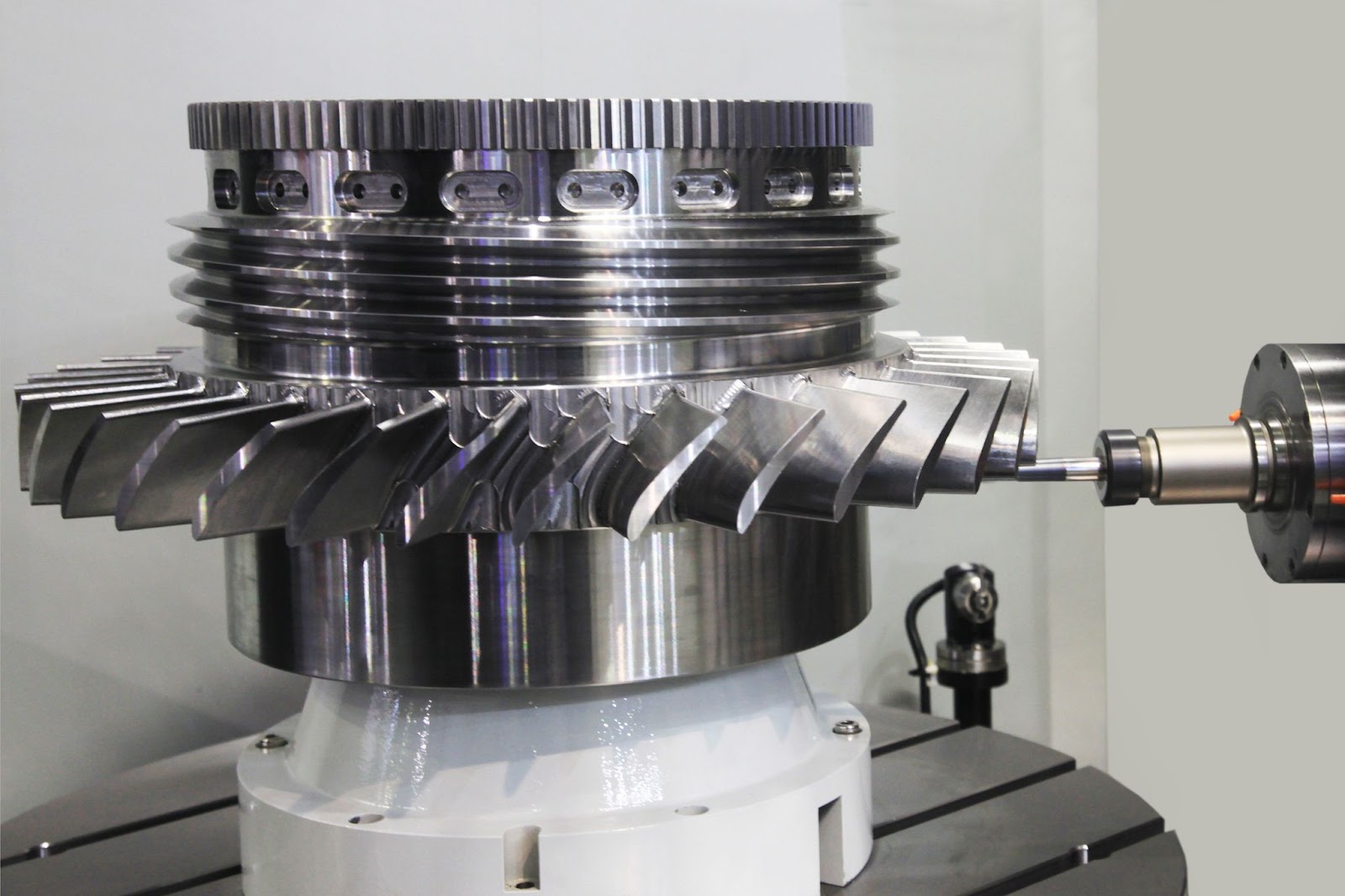
Part Complexity
One of the most impactful factors to consider for the CNC machining price is part complexity. CNC machining complex parts is expensive because the cost of machining is directly proportional to the complexity of the design — the more complex a part, the longer it takes to machine. And remember, you have to pay for setup time, the number of setups, programming time, and machining time. It adds up quickly.
One way to cut costs related to part complexity is to ensure you follow all Design for Manufacturability (DFM) feedback. When designing parts for CNC machining, it’s best to do so with your chosen manufacturing techniques and capabilities in mind.
For example, moving a feature to another side of the part so that you only need one setup (instead of 2) for a machining operation. Or maybe you can machine the part on a 6-axis machine — instead of a 3-axis machine — to increase throughput and reduce costs without sacrificing complexity. Whenever possible, limit the CNC machining to a few faces of the part to reduce CNC machining complexity as well.
Where you can, always look to reduce complexity by limiting the number of parts that you have to machine for an assembly. If possible design features within a single part to reduce CNC machining costs, instead of requiring CNC machining of several smaller components.
Raw Material Selection
The second area to consider when determining the cost of CNC machining is raw material selection. When designing for CNC machining, you’re likely to choose one of three common metals: titanium, steel, or aluminum. When choosing between them, titanium costs the most but offers a good strength-to-density ratio. Aluminum costs less and is more lightweight for its strength. Steel is also less costly, but has a higher density for its strength.
Aside from the cost of the raw material itself, it’s also important to consider the cost of machining it. For example, when comparing 304 vs 316 stainless steel, 316 is harder to machine and costs more, but is stronger and easier to weld. Choosing harder materials often drives up the cost because the tooling to machine them wears faster and requires more maintenance to stay sharp, which adds cost per piece. Modern superalloys have highly valued strength and other material properties, but they are expensive. So, choose your materials wisely.
Pro-tip: Run through your designs with multiple iterations, performing calculations for thickness requirements with multiple materials and accounting for material and machining costs. You may be surprised how much a small thickness increase can save you.
Tolerances – They Add Up
Most engineers know that tighter tolerances mean increased costs. What you may not have considered is exactly why the cost increases drastically as the tolerances get lower and lower. It’s no secret that decreasing design tolerances can cut CNC machining costs, but how? The following are all ways that tight tolerances add up when calculating the cost of CNC machining custom parts:
- Achieving tighter tolerances requires precision tooling and machine equipment with the capability to produce high precision and accuracy. This equipment and tooling cost more, and those costs are passed on to the customer.
- Achieving tighter tolerances often means additional manufacturing steps like grinding, honing, and polishing. These are manual and labor-intensive tasks, so they drive up costs.
- Tight tolerances also require more or more sophisticated inspections which also adds costs. And for critical features with tight tolerances, the inspection rate is even higher, which increases costs further.
So, the key takeaway is to think carefully about your tolerances and design tight tolerances only where necessary.
Surface Finishes Matter
As engineers, we’re often so focused on the mechanical and physical design of products that we forget to calculate the cost of post-CNC-machining processing. Whether it’s plating, conversion coating, polishing, or painting, each of these specialty services adds cost to the part.
CNC machined surfaces often have discernable swirl marks, and while these don’t have an impact on dimensional accuracy, they impact part aesthetics. To get surface roughness to an acceptable level for smooth finishes you may need secondary machining and additional setups.
Also, you may be designing a part for a harsh environment containing seawater, extreme temperatures, or abrasives. To withstand those harsh conditions, your parts may need to be plated, coated, or painted. These operations must be performed under specific, controlled conditions and therefore they increase the cost of your parts.
Pro-tip: Choose a CNC machining supplier for custom parts, like Fictiv, who can provide all the CNC machining and post-processing finishing services you need. You’ll save time and money!
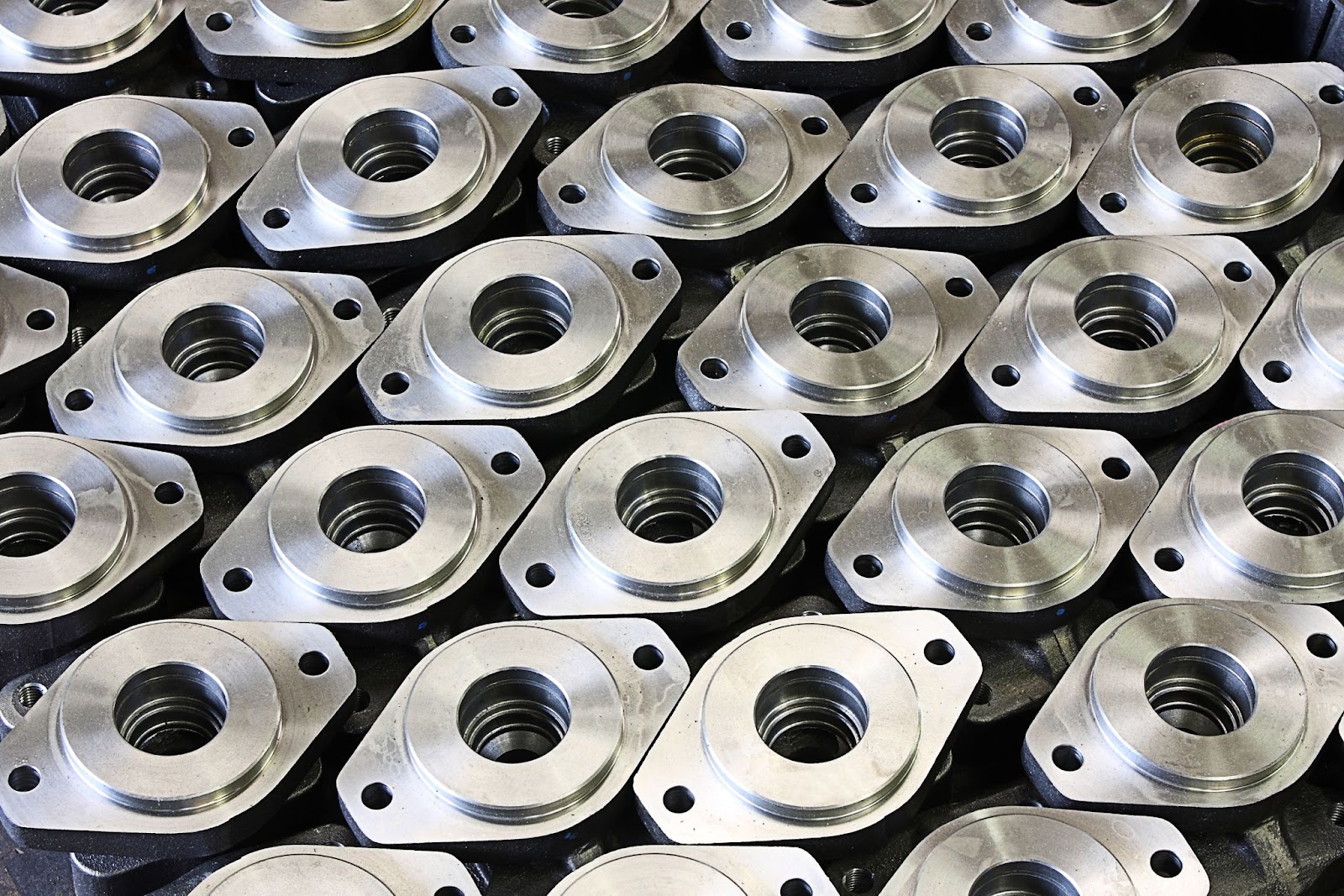
Order Quantity – Prototype or Large Volume
Because setup and programming costs are significant for every new CNC machining job, smaller volume orders cost more per part than larger ones — typically, the higher the order quantity, the lower the price you pay per part. This maxim holds for repeat orders.
With traditional machining, you pay exorbitant amounts for prototypes or custom, one-off parts. But, with custom machining platforms like Fictiv, you can get prototypes made at reasonable prices and excellent leadtimes without sacrificing quality.
Calculating the True Cost of a CNC Machined Part
Calculating the true cost of CNC machined parts involves all the factors above. And how much each contributes to the overall cost depends on the part and the manufacturer you choose. So, there are no simple calculations to determine the cost to CNC machine a given part.
Regardless of the manufacturer you work with, I recommend following their DFM feedback and asking for ways to optimize your machining choices and reduce your costs.
Sourcing Simplified – Start Your Next Project With Fictiv
If you’re tasked with sourcing and supplying custom CNC machined parts, Fictiv is your operating system for custom manufacturing that makes part procurement faster, easier, and more efficient. In other words, Fictiv lets engineers, like you, engineer. Create an account and upload your part to see what our instant quote process, design for manufacturability feedback, and intelligent platform can do for you. Our CNC machining service can create quality precision parts in as little as 2 days!