Time to read: 6 min
Cleaning is defined as the removal of dirt, impurities, or extraneous matter. You may not think of cleaning as an important part of your manufacturing processes, but it’s a critical post-CNC machining process. Why? Improper cleaning can result in quality issues that are entirely preventable with the proper methods. Here are some of those issues:
- Poor metal joining
- braze joint
- weld porosity
- weld voids
- Contamination of inspection areas
- Improper finish coverage
- Paint or coating adhesion issues
Proper cleaning is vital to provide a good surface for post-CNC processing, and is simple to achieve once you have an understanding of basic cleaning methodology. Read on to learn our best tips for cleaning CNC machined parts.
Water Quality
Water quality is an often overlooked and uncontrolled area in many cleaning line operations even though it significantly impacts substrate cleanliness. Take a look at your city’s tap water contaminant levels and, depending on your geographic location, you’ll find many contaminants — such as silicon, sodium, and chlorine — that are known to cause issues with finishing or subsequent processing operations.
While the concentration of these contaminants may seem to be small (up to a few parts per million), trace amounts can still cause adhesion, weld porosity, rust or corrosion, and coverage issues. The Water Quality Association is an international organization with a large library of information surrounding water contamination levels and treatment options.
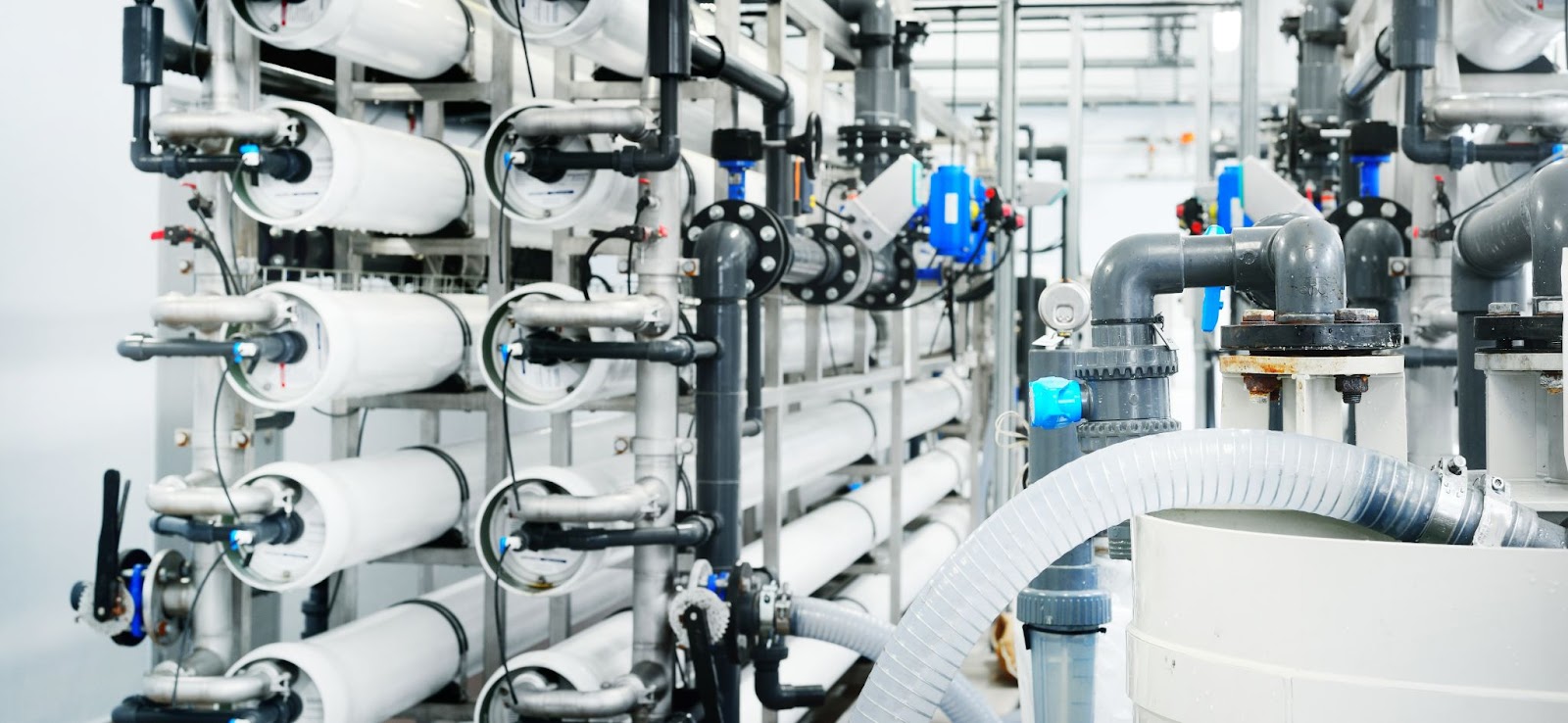
Cleaning Water for Process or Rinse Tanks
Now that you know how unsuited your tap water is to your process and rinse tanks, it’s time to clean it up! Don’t panic — you have options. Let’s review them, starting from the most effective to the least effective:
- Lab-grade purified water uses a combination of purification techniques (carbon filters, ion-exchange resin beds, microfiltration, UV lights, and various filtration membranes) to produce ultrapure, type I lab-grade water. This is the purest form of water, free of all contaminants (or at least down to the parts per trillion level). While highly useful, lab-grade water is expensive and often not needed for your cleaning, rinse, or processing baths. This is type I water per ASTM D1193-91.
- Deionized (DI) water is produced by an ion-exchange purification process where contaminants are captured within resin in resin beds. DI water has a low resistivity and a slightly higher percentage of contaminants versus lab-grade water. DI is classified as type II water per ASTM D1193-91.
- Reverse osmosis (RO) water isproduced with reverse osmosis systems and is often a water source for DI systems and lab grade water. RO water may be type III or type IV water per ASTM D1193-91, depending on the concentration of contaminants.
So, you don’t need to use lab-grade water for every single bath makeup, replenish or rinse tank, but you should consider using RO or DI water for those purposes. Even if you use the best cleaning solution, poor water quality can undo all the hard work done to clean your parts.
Pro-Tip: Try using hot DI water in your final process rinse tank. Heated water allows parts to dry faster.
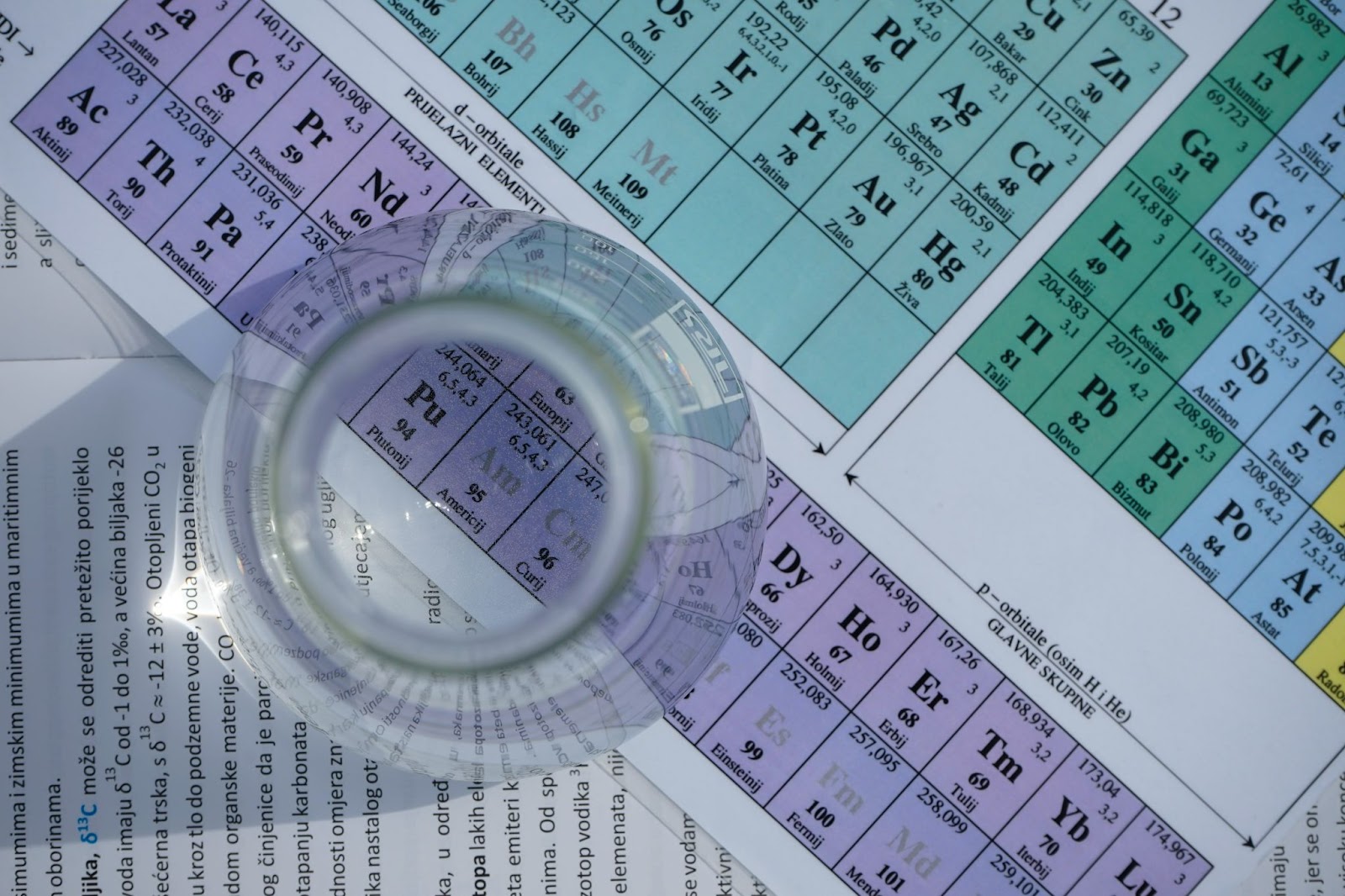
Tips for Setting Up Your Cleaning Line
First, determine the type of cleaning solution, so you get an idea of the footprint required for a typical cleaning line. Cleaning solutions are typically aqueous or water-based, solvent-based, electro-cleaning or acid etch. Usually, aqueous solutions go in a tank with agitation and heat, while solvent-based solutions are utilized in a vapor degreaser.
The type of cleaning solution you use should depends on three factors:
- The type of surface residue or contamination you want to remove — this ranges from cutting oils, to dust, to heavy oxidation, or fingerprint residue.
- The material you’re cleaning — certain materials will be corroded by certain cleaning solutions, reducing the integrity of your CNC machined parts. (Stay tuned for future articles in this series where we’ll review our favorite cleaning solutions for common CNC machined metals such as aluminum and stainless steel.)
- Regulatory guidelines and laws for chemical contamination and disposal, as well as safe handling practices and minimizing exposure to employees on the cleaning lines — there are often alternatives to harsh or unsafe chemicals.
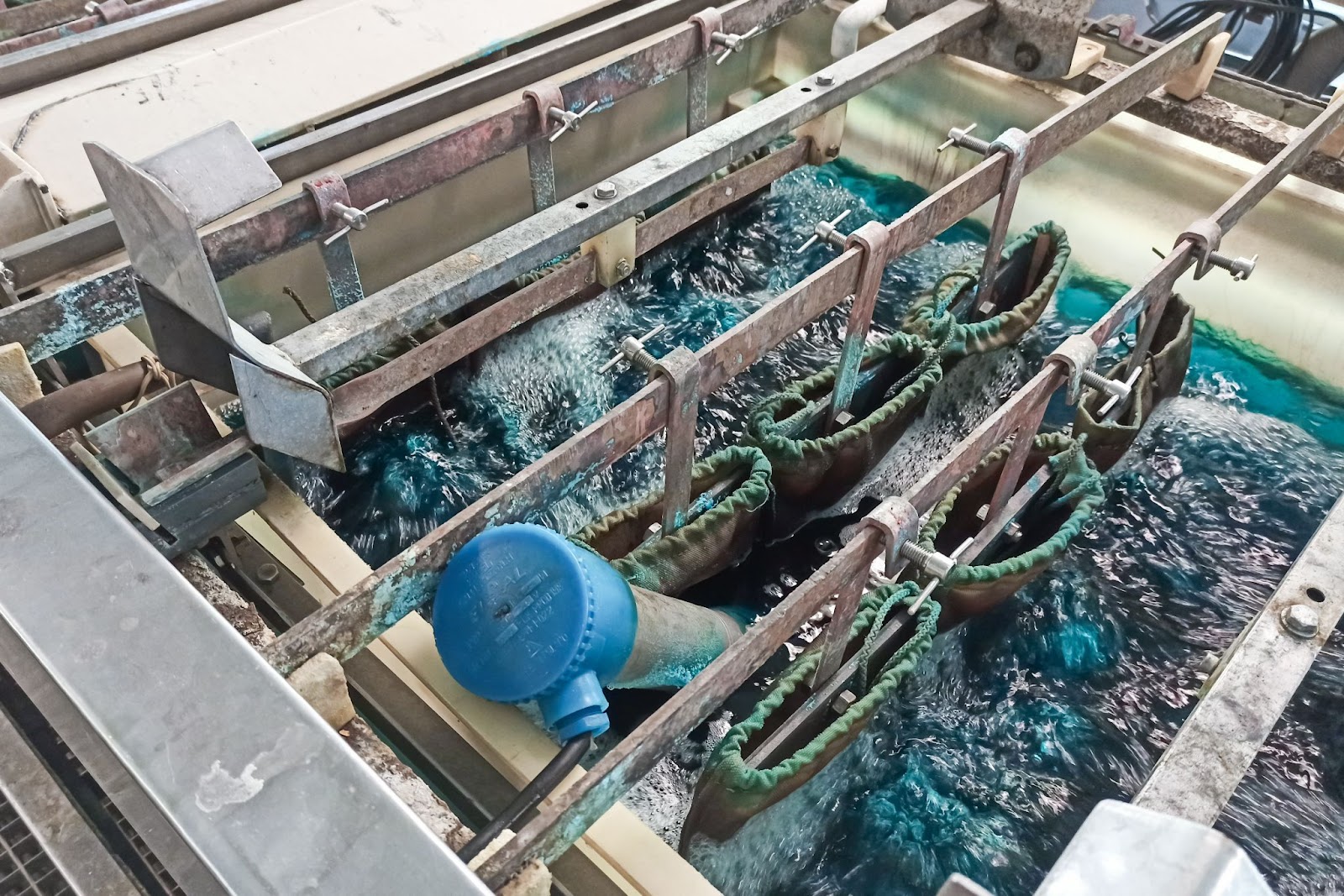
Aqueous Cleaners
An aqueous cleaner is a mixture of water and chemical additives that provides cleaning properties. This type of part cleaning solution encompasses a wide variety of cleaning mixtures, some of which are eco-friendly alternatives to chemicals of the past. The chemical additives that provide the functional cleaning results can be one or more of the following:
- Detergent/Surfactant
- Emulsifier
- Saponifier
- Sequestering Agent
- Builder
- Chelating Agent
Aqueous cleaning typically involves following a three-step process:
- immersion in the cleaning solution
- immersion in a rinse tank
- immersion in a final hot rinse or isopropyl alcohol.
The parts are then dried with heated, forced air, or are air dried. Rinsing is critical to ensure all contaminants are removed from the surface of parts, as well as removing any cleaner residue. The temperature, time, and agitation are the other important factors to ensure sufficient cleaning of your parts.
Aqueous cleaners can be acidic or alkaline, and each provides different benefits and different targeted contaminant removal. Acidic aqueous cleaners (those with a low pH) are suitable for removing heavy oxidation, scale, or rust from a metal’s surface. Alkaline aqueous cleaners (those with a higher pH) are not only utilized for oxide removal, but also salts, organic solutions (like oils or grease), metal chips, and cutting fluids.
Alkaline aqueous cleaning solutions are more popular because they’re more versatile, but acidic aqueous solutions are more effective at cutting through thick oxide layers or rust. A disadvantage of aqueous cleaning is that if you don’t have proper rinsing, you’ll end up with fluid residue left on the surface of your CNC machined parts.
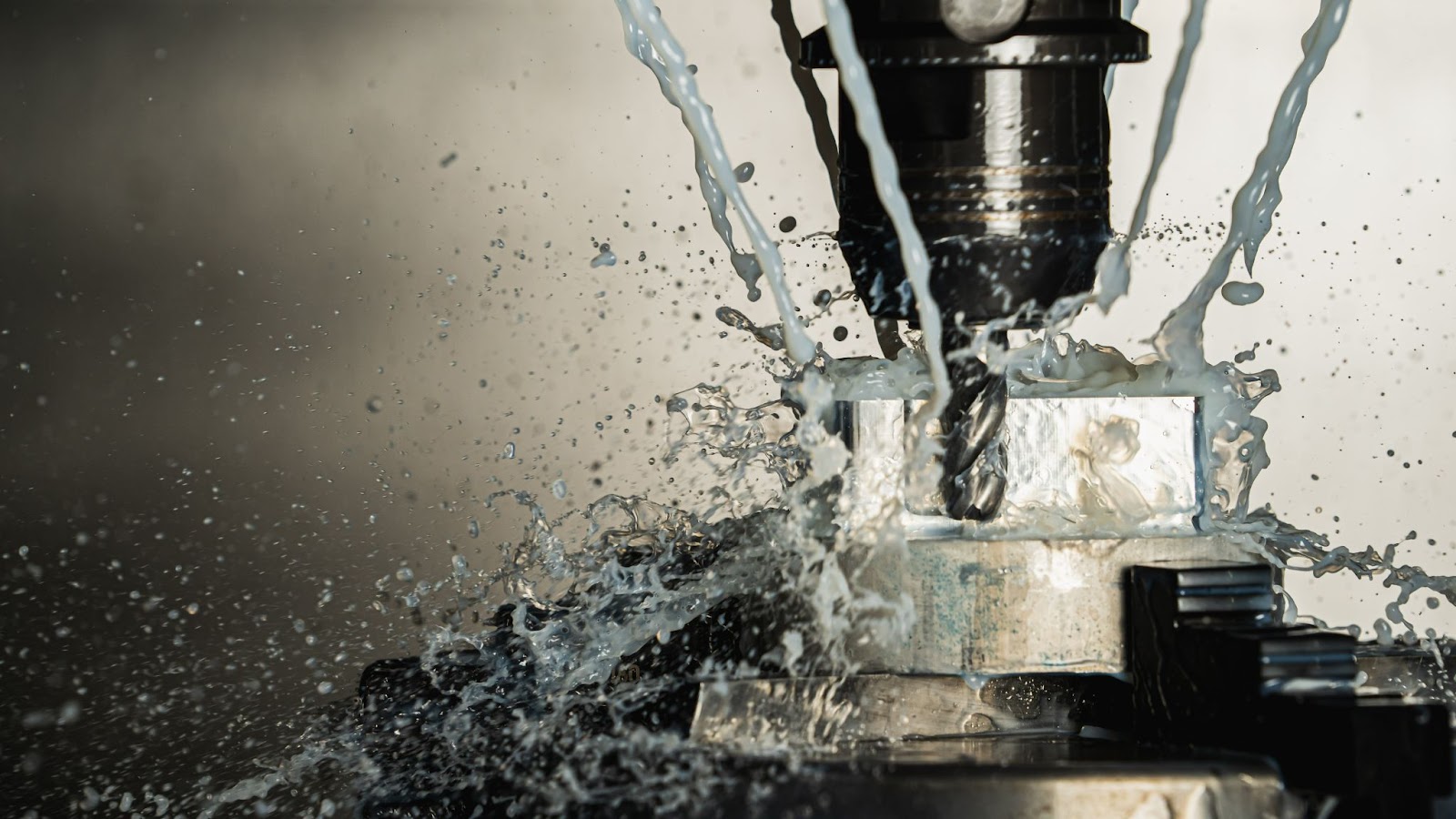
Solvent-Based Cleaners
Solvent-based cleaners are not diluted with water and ar typically utilized in special cleaning equipment, like vapor degreasers. Usually, machined metal parts are immersed in a single solution — which is often ultrasonically agitated — and the solution drips off the parts (along with the contaminants). Next, the parts are vapor rinsed and dried, because the solvent doesn’t leave any residue behind. Solvent-based cleaning is also well-suited to rapidly clean a large volume of parts with complex geometries.
Historically, solvent-based cleaners are environmentally damaging and unsafe for workers. However, modern cleaning solutions are environmentally friendly and provide safer working conditions. The benefits of solvent cleaning over aqueous cleaning are:
- Less equipment to operate (single machine for the entire cleaning process)
- Less operator interaction required
- More aggressive cleaning without residue
For especially dirty parts, some applications call for a two-stage process. First, you perform a solvent-based cleaning followed by an aqueous cleaning process to ensure all types of contaminants are removed. Other methods call for mechanical cleaning processes — such as blasting — to remove heavy oxides or scale from heat treating.
Resources for Further Cleaning Research
While this article provides a good introduction to cleaning your CNC machined parts, there is a world of cleaning information out there. Here are some of the best resources for additional research on cleaning your parts:
- ASTM B322 Standard Guide for Cleaning Metals Prior to Electroplating
- ASTM A380 Standard Practice for Cleaning, Descaling, and Passivation of Stainless Steel Parts, Equipment, and Systems
- ASTM D6386 Standard Practice for Preparation of Zinc (Hot-Dip Galvanized) Coated Iron and Steel Product and Hardware Surfaces for Painting
- Consult with the specific volume of the Metals Handbook that applies to your substrate material
- Always check Technical Data Sheets (TDS) for the lubricant or cutting fluids utilized in your CNC machining process; they might provide useful information on what types of cleaners to remove them
- Consult with industry specifications, such as AS, ISO, or MIL that provide required cleaning steps prior to post-CNC machining processing
Start Your Next Project With Fictiv
If you’re tasked with sourcing and supplying well-cleaned, CNC machined parts, Fictiv has you covered! Fictiv’s your operating system for custom manufacturing that makes part procurement faster, easier, and more efficient. In other words, Fictiv lets engineers, like you, engineer.
With our design and manufacturing expertise, and innovative platform that provides instant DFM feedback, complete production visibility, and quick turnaround times, manufacturing your parts is easier than ever!