Time to read: 5 min
Anodizing is a popular surface treatment process used in various industries to provide superior protection and enhance the appearance of aluminum parts. Since anodizing is an electrochemical process, meaning there needs to be chemical immersion/exposure along with a flow of electricity, there has to be a way for the circuit to be completed to the parts and back to the power supply. This is typically done by placing the parts on a rack made of conductive material. When the rack contacts the part during the anodizing process, it may result in rack marks on its surface where the anodizing finish is typically missing. This is a concern for many because it may affect the cosmetic quality of the finished product, especially if the part requires a Type III (hard-coat) anodize that requires a firm hold during the entire anodizing cycle, especially for parts dyed a dark color.
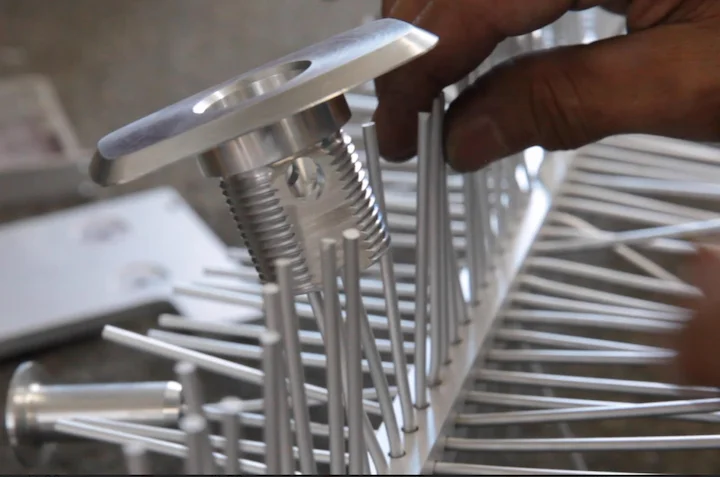
But the good news is there is a simple method to reduce the impact of rack marks on your anodized parts. Read on as we explore potential solutions, such as marking drawings for anodizing rack marks in non-functional or hidden features of a part. We’ll examine the details of rack marking for anodizing per MIL-PRF-8625 and provide guidance on which features are best for racking.
What are Rack Marks?
Rack marks are the visible marks left on the surface of a metal part after it has been anodized. They are caused by the small contact points between the part and the anodizing rack used to hold it and provide a pathway for the flow of electricity during the anodizing process.
Electrical contact must be made to each part to be anodized, and the more electrical current required, the greater the electrical contact and potential for rack marks. The size of the rack mark is a function of the part’s surface area, with larger surface area parts having larger rack marks due to the application of more total current. Additionally, larger surface area parts may require multiple rack locations to create a uniform coating, resulting in a consistent coating thickness across the part. Rack marks can vary in size and depth depending on the type and size of the rack used.
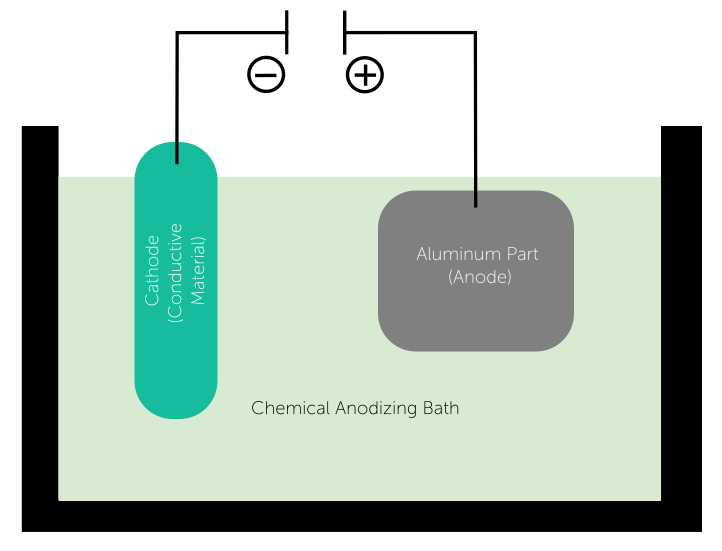
As previously mentioned, rack marks may be necessary, depending on the parts’ size (surface area). The parts must be positioned, and they must make contact with the rack to allow for the flow of electricity during the anodizing process.
The Mil-PRF-8625 military standard identifies the need for rack marks. Rev F, section 3.13.1 states: “The size and number of contact marks shall be at a minimum consistent with good practice (see 6.14). If a specific location for contact marks is desired, the location shall be as specified on the applicable drawing, contract or purchase order (see 6.2).”
Why are Rack Marks a Problem?
Rack marks can significantly affect the cosmetic quality of the anodized part, especially if they are visible on the functional or visible areas of the part. In addition, areas with rack marks are typically either not anodized or not anodized to the same thickness.
So, considering the cosmetic appearance and corrosion protection required for most parts, it is essential to minimize the visibility of rack marks.
Marking Drawings for Anodizing Rack Marks
One way to minimize the visibility of anodized rack marks is to mark the drawing for non-functional or hidden features of the part that can be used for racking. The anodizing rack can then be designed to hold the part in these areas, leaving the functional or visible areas free from rack marks on the exposed surface. This can help improve the cosmetic quality of the part and reduce the visibility of the rack mark, especially when considering the part size and weight in relation to the type of anodizing process used.
You should be aware of the most common types of racking for anodizing in order to know where to specify allowable rack marks:
- Wiring or threading: involves using flexible, conductive wire fed through the part somewhere or suspending the part in the bath and connected to the power source through a frame
- Hanging: parts are hung on a coat rack design to allow for fixturing while solution can flow around them; good for cylindrical parts
- Clamping: good for larger parts or heavy parts; involves using clamps, typically holding the edge of parts
- Spring Grippers: used to make spring or compressive contact on the internal diameter of a hole; good for complex geometries and fast-racking
Best Features for Racking – Design Tips for Racking
The following features are the best for specifying allowable rack marks:
– Holes: Holes that are not critical to the part’s functionality can be used for racking.
– Counterbores and countersinks: These features can be used for racking as long as they do not affect the part’s function.
– Keyways and slots: These features can be used for racking as long as they are not critical to the part’s function.
– Flats and shoulders: Flat surfaces not critical to the part’s function can be used for racking.
It is important to note that the racking features must be designed to provide good electrical contact, and adequate support to the part during the anodizing process and promote good solution flow since entrapment of solution can reduce the anodizing quality. The contact size must also be considered in the design of the racking features, as it depends on the anodizing process and the size of the part being anodized. The anodizing rack must not cause any distortion or deformation of the part and must not interfere with the part’s function, as this can lead to finishing problems. Additionally, it is important to consult with a professional for general reference and to ensure the safety and quality of the anodizing process.
Anodizing rack marks can significantly affect a part’s cosmetic quality and functionality. Marking the drawing for non-functional or hidden features that can be used for racking is an effective way to minimize the visibility of rack marks and maintain the tight tolerances required for some applications. However, ensuring that the racking features are designed to provide adequate support to the part and do not affect its function is essential for sufficient current requirements. By following the mark guidelines in the Mil-PRF-8625 standard and this article, you can ensure that your anodized parts meet the highest quality standards, including MIL spec requirements.