Time to read: 8 min
When metal is exposed to the elements or certain chemicals, deterioration in the form of oxidation may occur. The Second Law of Thermodynamics declares that everything tends to move into a state of disorder. After designing and manufacturing your products, the last thing you want to discover is a breakdown of a metal component in the form of oxidation, corrosion, or rust.
While oxidation and deterioration are age-old problems, there are ways to circumvent them. One of the best solutions is to apply a protective coating to your part so it’s unaffected by natural elements or harsh chemicals that cause degradation. Conversion coatings are an example of a protective coating that removes surface impurities and enhances the oxide layer on a metal part’s surface.
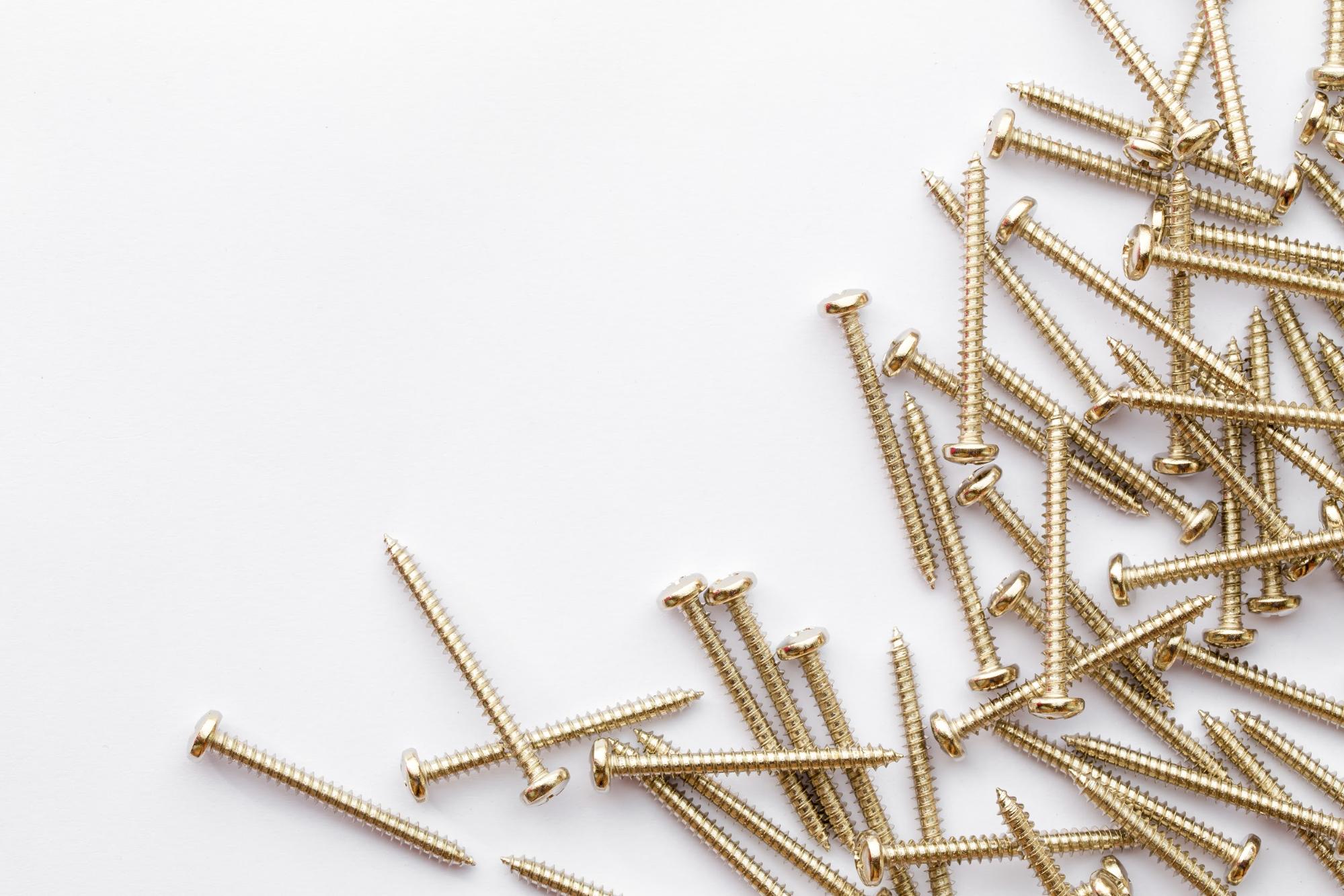
This article covers some of the most common types of conversion coatings. Unlike passive coatings such as paint or powder coat, conversion coatings involve a chemical reaction at the outer surface of a metal part.
This article covers the benefits of the following conversion coatings and the differences between them:
- Chromate conversion coatings, aka chem film or Alodine™, and anodizing are commonly used on aluminum parts.
- Black oxide is commonly used for coating steel and stainless steel.
Each coating is a protective surface modification treatment that enhances resistance to corrosion, such as rust caused by oxidation.
What is a Chemical Conversion Coating?
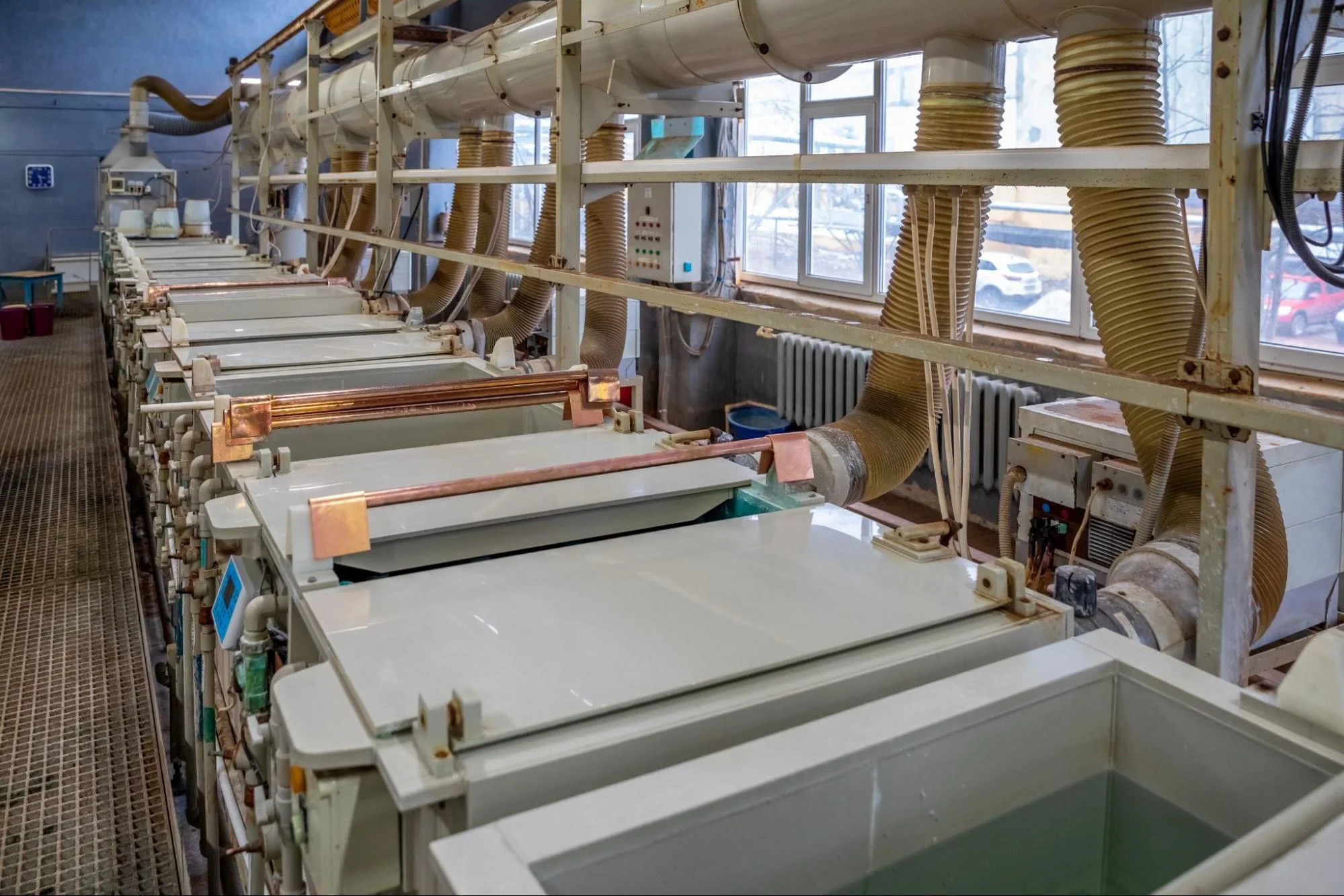
Chemical conversion coatings are thin layers formed on metal surfaces consisting of oxides, phosphates, or chromates. A chemical conversion coating is applied via submersion of metallic parts in a chemical bath, resulting in a chemical reaction between certain reagents and the part’s surface. This specific reaction is an oxidation-reduction reaction where a small amount of surface metal (specifically metal oxide and impurities) is removed and replaced with a more homogenous and more resilient oxide layer than the naturally occurring oxide layer. The amount of metal/metal oxide removed is typically between 0.00001 to 0.0001 inches. Keep in mind that the naturally occurring oxide layer on aluminum, for example, is much thinner than this.
Comparison of Conversion Coatings
Type of Coating | Coating Structure | Properties | Applications |
---|---|---|---|
Anodization | A dense barrier layer, porous outer layer. | Corrosion and scratch resistance, non-conductive. | Aesthetics, lubrication, corrosion resistance. |
Chromate Conversion (Chem Film) | Nonporous film, moisture barrier, primarily chromate oxide. | Corrosion resistance, enhanced paint adhesion, inhibits further corrosion if surface is damaged. | Marine applications, may be decorative, paint adhesion to nonporous layer. |
Black Oxide | Ferric oxide (stable), formed. | Inhibits formation of rust (iron oxide), absorbant, increased wear-resistance. | Improved aesthetics, rust resistance. |
Phosphate | Crystalline structures of phosphate compounds formed on the surface from iron, zinc, or manganese phosphates. | Highly absorbent and chemically inert surface. | Excellent bonding for paint to iron, prevents heavy wear or seizing. |
Examples of chemical conversion coatings include chromate conversion coating (CCC), phosphate conversion coating (PCC), and black oxide coating. During the conversion process, part of the metal surface is converted into a protective surface layer, as seen in chromate conversion coating, phosphate conversion coating, and black oxide coating. A chromate conversion coating on an aluminum substrate is a chemical film.
Also, nanopores within the oxide’s crystal layer can often be filled with dye or other sealants to achieve enhanced properties like color, lubricity, and increased hardness. Most importantly, the metal oxide layer is chemically bonded to the metal it protects. This makes conversion coatings extremely durable and difficult to penetrate.
Benefits of Chemical Conversion Coating

Chemical conversion coatings can positively impact part appearance, affinity for galvanic corrosion, electrical conductivity, hardness, and oxidation resistance. Some of the main benefits of chemical conversion coatings are:
- Reduced rate of corrosion.
- Increased wear resistance and durability.
- Improved adhesion for organic coatings, such as paints or powders.
- Enhanced ability to draw or form the metal without damage.
- They can be colored or dyed for decorative purposes.
- They can be applied using various simple methods, such as spraying, dipping or brushing.
Ultimately, applying a conversion coating to your parts can help them last longer and add desired properties like color, hardness, lubricity, or increased corrosion resistance. So, keep these common conversion coatings in mind when designing and optimizing your next product!
Conversion Coating of Aluminum
Anodizing
Anodizing is a common form of electrolytic passivation for aluminum (and steel, but we will focus on aluminum here). First, parts are typically cleaned and/or desmutted to remove any scale or heavy contaminants. Next, a sulfuric or other acid solution bath is used to strip (etch) away any naturally occurring oxidation layer. Then, parts are connected to a power supply to give them a positive charge and immersed in the anodizing bath, which involves immersion of a component in an acid solution and passing electricity, specifically electrical current, through the component, with the component being the anode in the electrical circuit. While in the bath, parts attract negatively charged and reactive oxygen atoms directly to their surface.
The metal oxide crystal nanopores formed in this process can be filled with dye, revealing a wide range of colors before being sealed in another chemical bath. Because of the brilliant spectrum of color available through the anodizing process, it is often used for consumer products.
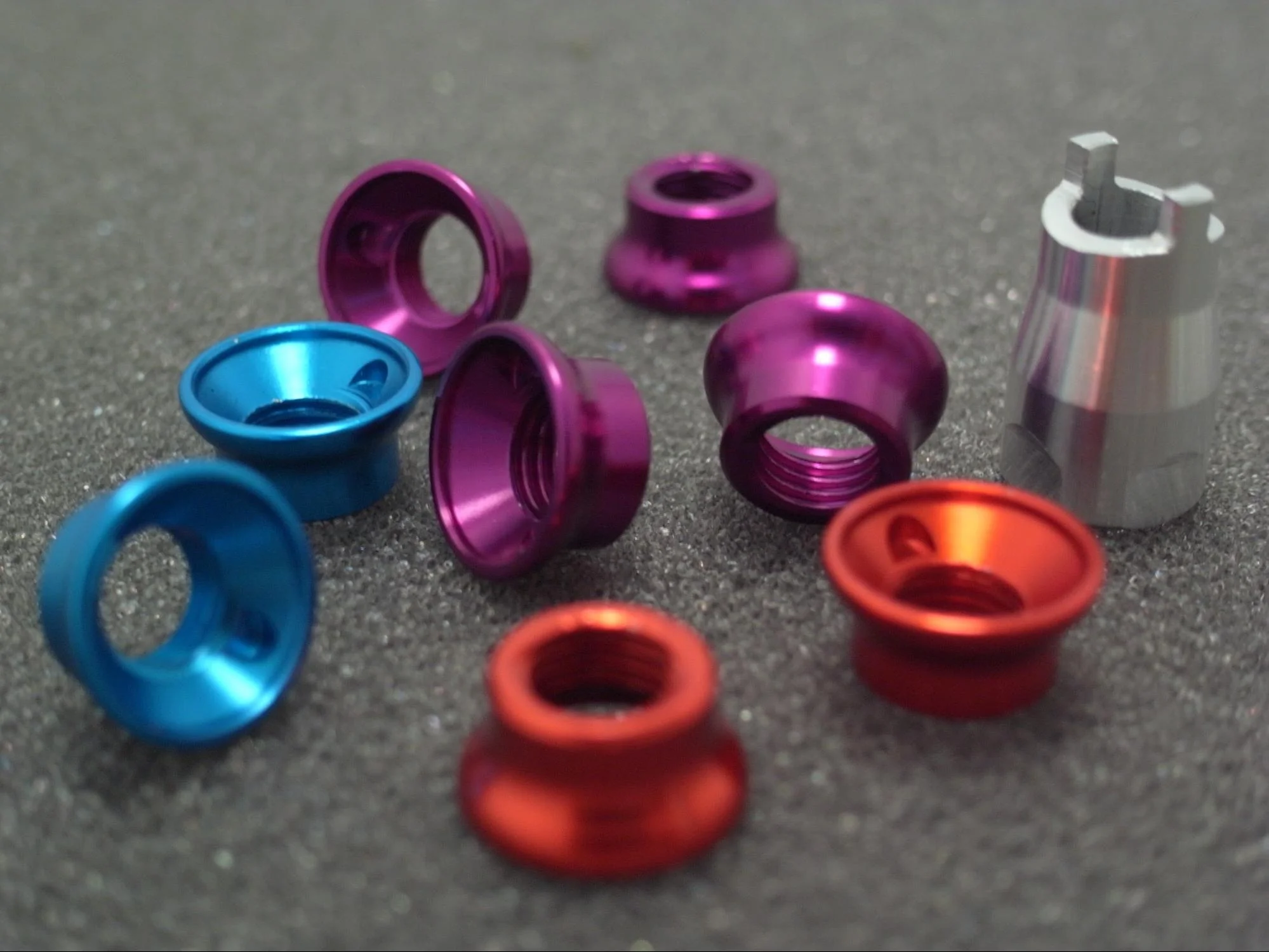
Anodizing adds an insignificant amount of material to the surface of the part to cause a reaction, so the parts grow outward — the standard thickness of an anodized coating is up to a few thousandths of an inch. So, if your part requires tight tolerances, you should consider this change for your designs and use masking or hole plugs on those areas prior to anodizing.
It’s also important to remember that different anodizing processes (Type 1/1B, Type II, Type III/III w/PTFE) result in different layer thicknesses. These different types of anodizing allow this coating to be useful in various industries and applications, from trusses on the International Space Station to artistic sculptures and sporting goods.
Chem Film or Alodine™
Chromate conversion coating, known as chem film, or chromating, is similar to anodizing because it produces a modified, corrosion-resistant oxide layer on metal parts, but does not use electricity to create its oxide layer. Alodine™ is the trademarked name for a chemical conversion coating produced by Henkel (other brand names include Iridite®, Bonderite®, and Chromicoat® ). I like to think of chromating as the electroless version of anodizing. Chem film or Alodine™ is a proper corrosion-resistant aluminum surface treatment for painting, powder coating, adhesive bonding, heat sinks, and automotive wheels.
Instead of an electrochemical reaction, chem film or Alodine™ is produced using a reactive chromium atom to drive a purely chemical reaction. To get a chem film or Alodine™ finish, parts are first cleaned, degreased, and rinsed. Then parts are placed in the chromium bath, removed, rinsed, and dried. Chem film or Alodine™ is often applied to screws, bolts, brackets, and other fasteners because it doesn’t produce a noticeable dimensional change. Chem film or Alodine™ is cheaper than anodizing, but more susceptible to wear and scratches.

These are the most common types of chromate conversion coating (chem film):
MIL-DTL-5541 Type 1 contains hexavalent chromium, or “hex-chrome”.
MIL-DTL-5541 Type 2 replaces hexavalent chromium with trivalent chromium, titanium or zirconium.
Historically, a hexavalent chromium compound served as the main catalyst in chem film or Alodine™ conversion coatings. However, given this atom’s carcinogenic nature, hexavalent chromium has become tightly regulated and now trivalent chromium, including type 2, can be used. This type of chromating, known as hex-free chromating, is typically accepted as the standard across many industries.
There are also different classes of chromate conversion coating (chem film) described below:
MIL-DTL-5541 Class 1A tends to be thicker and darker, with higher corrosion protection.
MIL-DTL-5541 Class 3 is thinner, which allows it to reduce inference with electrical conductivity in addition to providing corrosion resistance.
Together, these common types and classes of chem film provide a variety of options, and the best solution will depend on your project needs.
Compare the general qualities of chem film and anodization in the table below:
Anodization vs. Chem Film
Quality | Anodize | Chem Film |
---|---|---|
Thickness | 1.8-25 μm | 0.25-1.0 μm |
Conductivity | No | Yes |
Appearance | Multiple Colors | Clear/Gold |
Types | Type 1/1B, 2, 3, 3 w/PTFE | Type 1, 2 Class 1A, 3 |
Materials | Aluminum and others | Aluminum and others |
Price | $$$ | $$ |
Durability | **** | ** |
Can I Use Both Anodizing and Chem Film ( Alodine™)?
While it likely wouldn’t hurt your parts to apply both an anodized and chem film (Alodine™) coating, it probably won’t help much either. Both coatings result in a modified surface composition that improves corrosion resistance. Once you apply one coating, the other won’t have any impact; you won’t get increased paint adhesion or corrosion resistance. The one exception could be to replace damaged areas from the previous coating.
Some CNC machined aluminum parts require only specific sections of their surface to be painted, while other areas are plated or coated with a different process. For such parts, you can opt to anodize certain areas and chem film or Alodine™ others.
Conversion Coating for Steel or Stainless Steel
Black Oxide
Black oxide, historically called browning or bluing, is a conversion coating most often used for steel and stainless steel. It is similar to the chem film or Alodine™ process. A variety of procedures have been developed for applying black oxide finishes. Ultimately, it is a purely chemical process that creates a conductive iron oxide layer called magnetite that provides corrosion resistance for the base metal.
The black oxide finish greatly decreases reflection from the metal’s surface and barely changes the dimensions of the coated part. When a black oxide finish is sealed with oil or wax, lubricity increases, so it’s used on parts to prevent galling in gears and locks. Black oxide coatings can be applied to both copper and steel.
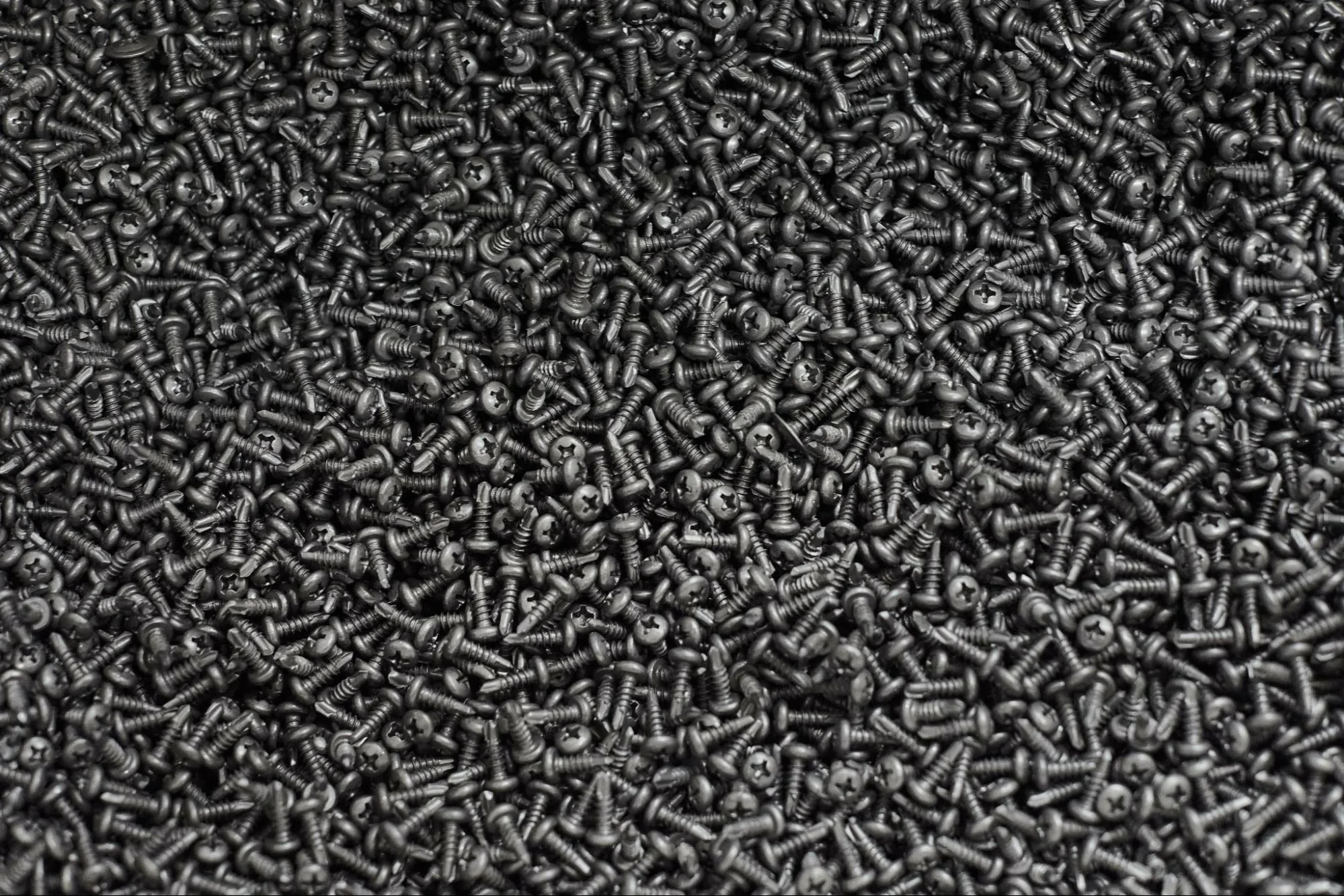
Black Oxide vs. Passivation
Black oxide and passivation are both processes utilized to enhance the corrosion resistance and aesthetics of stainless steel parts. While black oxide is a chemical conversion process, passivation is a chemical treatment process whereby free iron is removed from the surface of a stainless steel part, promoting the growth of a protective oxide layer. Stainless steel has a naturally occurring oxide layer, but free iron on the surface of a part reacts with oxygen in the air, forming rust (iron oxide). Passivation provides greater rust protection, while black oxide provides some rust protection with an enhanced surface appearance.
Passivation vs. Black Oxide
Quality | Passivation | Black Oxide |
---|---|---|
Thickness | 5-15 μm | < 0.75 μm |
Conductivity | No | Yes |
Appearance | Smooth, glossy | Smooth, matte black |
Types | Zinc or manganese sealed | Variety of procedures |
Materials | Steel, stainless steel, etc. | Steel, stainless steel, etc. |
Price | $$$ | $ |
Durability | *** | ** |
How is Conversion Coating Different from Plating?
Plating and conversion coatings may seem similar at first glance. Electroplating is an electrochemical process whereby a metal is deposited on the part’s surface. This thin, protective coating may also alter the part’s appearance, physical properties, wear resistance, biocompatibility, or electrical conductivity. Electroless plating is a similar process in which the metal is deposited without using electricity (electroless nickel, for example).
Electroplating involves forming a layer of differing metal deposited on the surface of the part via an electrochemical process, whereas chemical conversion coatings create a thin film on the surface via a chemical process, and the film is non-metallic. Electroplated layers are much thicker than chemical conversion coatings.
Sourcing Simplified – Start Your Next Project With Fictiv
At Fictiv, we are here to help source all your custom manufactured parts, and have a variety of finishes to choose from, including conversion coatings. And our CNC machining service can create your parts in as little as 2 days!
Fictiv is your operating system for custom manufacturing that makes part procurement faster, easier, and more efficient. In other words, Fictiv lets engineers, like you, engineer. Create an account and upload your part to see what our instant quote process, design for manufacturability feedback, and intelligent platform can do for you.
To get started, create a Fictiv account and upload your design today!