Time to read: 5 min
It really grinds my gears when people use the word rust incorrectly. I spent years working as a metallurgist and design engineer analyzing material samples for failure. I love chemistry and have an obsession with relaying factual information. That’s why I dream of the day when all humans understand the difference between corrosion, oxidation, and rust. And this article is my latest contribution to making that dream a reality.
While it may seem like a small distinction, rust is a type of corrosion, which is a type of oxidation. Understanding this hierarchy and how to use each term correctly is essential to any mechanical engineer and anyone who designs, manufactures, or interacts with engineered parts. See what I did there? Everyone needs to know the difference between corrosion, oxidation, and rust.
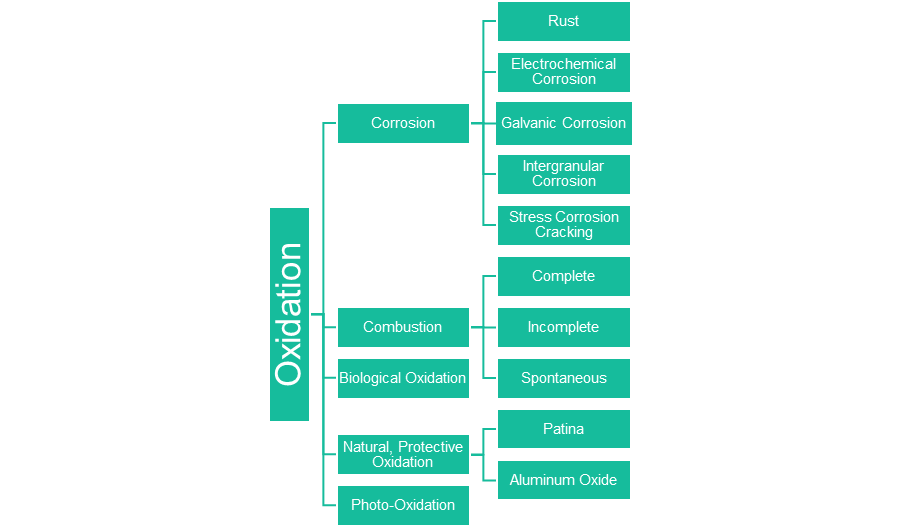
The diagram above is not comprehensive, but it showcases many forms of oxidation. If you follow the top path on the diagram, you see this: Oxidation → Corrosion → Rust. There are other types of oxidation and other types of corrosion but for the purposes of this article, we are focusing on the relationship between oxidation, rust, and corrosion.

What is Oxidation?
The oxygen that our bodies require to function is highly reactive and combines with many metals and nonmetals to form substances called oxides — and the reaction that occurs is oxidation. In more technical chemistry terminology, an oxidation reaction is simply the loss of electrons from one substance to oxygen atoms. This process is technically called an oxidation-reduction reaction or a redox reaction.
There are many examples of redox (oxidation) reactions in nature, like combustion. Here’s an example equation that represents the combustion of methane, which forms carbon dioxide and water:

In this reaction, the methane (CH4) loses electrons and the O2 bonds with the C atom to form carbon dioxide gas. The electrons lost by the methane are transferred to the oxygen atoms and form water vapor.
Metals have a tendency to form a natural oxide layer on their surface when exposed to air. This oxidation doesn’t occur as a chemical attack and doesn’t require any electrolytic solution to progress. It’s a weak, naturally occurring, protecting layer of metal oxide. For example, magnesium reacts with air surrounding it and forms a black oxide layer with the following reaction:

Temperature or water can accelerate the reaction of oxides on the surface of a metal, because they act as a catalyst. Once this reaction becomes aggressive enough, it changes to corrosion and degradation to the material occurs.
For example, magnesium turnings are used in fluxless vacuum brazing as a gettering agent — which means the magnesium gathers oxygen atoms left behind when the vacuum is pulled, or oxygen atoms that leave the metal as it heats up. This oxidation of the magnesium turnings results in corrosion of the magnesium, so the turnings can only be used once.
Aluminum Oxide Layer
However, not all oxidation becomes corrosion. For example, aluminum, my favorite metal. It’s strong and lightweight, shiny, durable, and easy to work with. It also has a naturally occurring oxide layer that protects it from corrosion. Freshly machined or etched aluminum, when exposed to oxygen in the atmosphere, naturally forms an oxide layer. This layer grows exponentially before naturally stopping when the oxide layer is about 4 Angstroms (0.0000004mm) thick.
The naturally occurring, protective aluminum oxide layer also self-heals. You read that right — if you take an abrasive and rub the surface of aluminum, you will likely remove some or all of the oxide layer, but you can reform it by simply exposing the bare aluminum to oxygen in the air. Pretty cool, right?
Here’s what else you should know about the aluminum oxide layer:
- The oxide layer must be removed when joining aluminum together with processes like brazing or welding. In aluminum brazing, the oxide layer cracks because it’s more brittle than the aluminum and the braze alloy can penetrate through the cracks. Aluminum oxide cracks at a lower temperature than the melting point of the braze alloy, which is part of the reason why ramp rate is critical in brazing.
- The naturally occurring oxide layer is all that’s needed to protect aluminum from corrosion in environments not subject to moisture or major temperature fluctuations.
- The aluminum oxide layer can also be manufactured with a process called anodizing, which you can learn more about in our resource center.
- Aluminum oxide is known as a barrier oxide layer because it provides a barrier to corrosive elements. The anodized oxide layer is either a barrier or a porous oxide layer, depending on the acidity of the electrochemical anodizing bath.
- Anodized oxide layers are about 0.001mm thick, which is significantly thicker than naturally occurring layers of aluminum oxide.
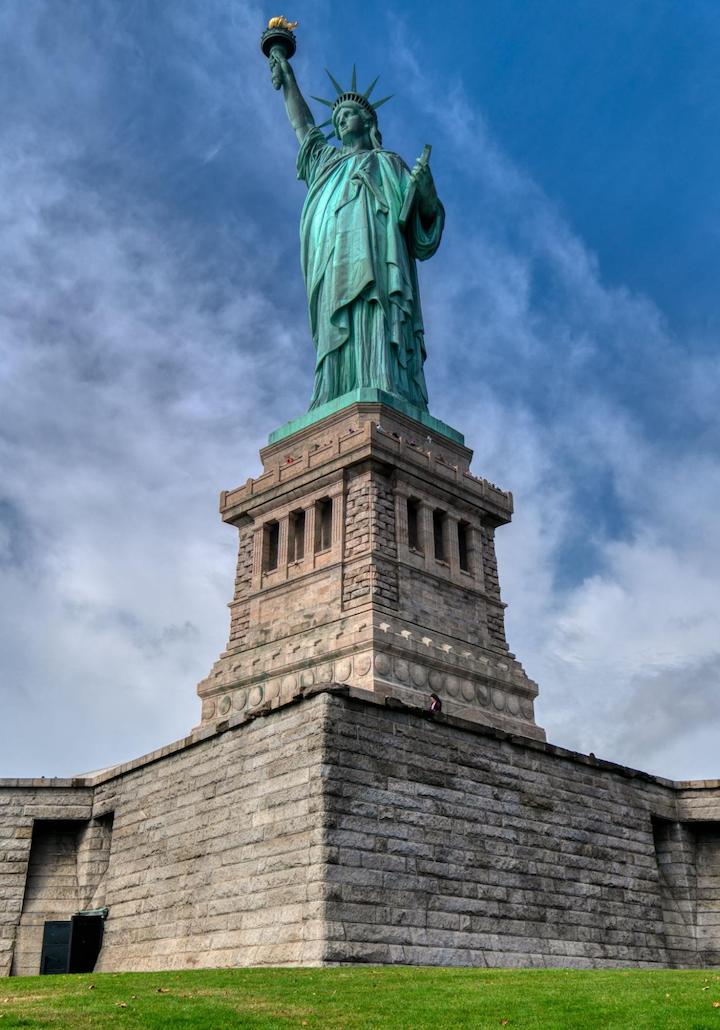
What is Corrosion?
For corrosion to occur, there must be a chemical reaction that causes deterioration of a metal by an external agent. This deterioration may be caused by oxidation, galvanic contact of dissimilar metals, or microorganisms. The most heavily studied form of corrosion is the electrochemical corrosion of metals, in which the oxidation process M → M+ + e– is facilitated by the presence of a suitable electron acceptor — called a depolarizer in corrosion science.
The electrochemical corrosion of metal is an area of focus due to the financial issues it causes. In the USA alone, over $137 billion is spent annually dealing with the repercussions of corrosion in the infrastructure, utilities, transportation, manufacturing, and government industries. It’s estimated that five tons of steel in the world corrode every few seconds!
What is Rust?
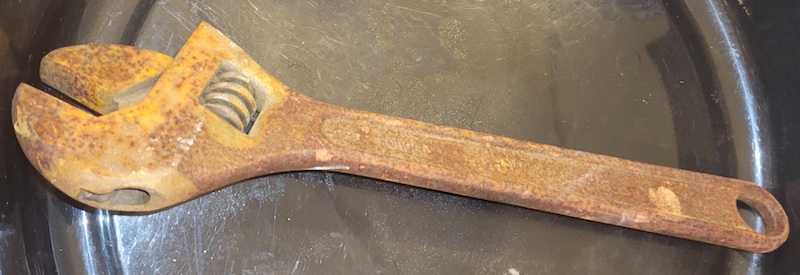
Rust is used to describe the process of iron corrosion, so if a metal alloy doesn’t contain iron, it can’t rust. The byproduct of the corrosion of iron (rusting) is iron oxide, as shown by the following chemical formula:
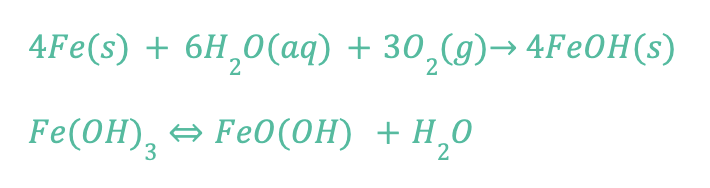
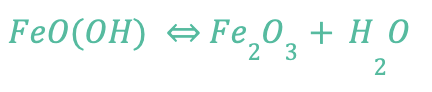
The formation of rust (FeOH – iron oxide) requires the presence of water and oxygen, and rust is permanent. You cannot reverse the reaction of rust, but you can remove rust from a surface and there are methods to prevent further rusting.
How to Prevent Rust
The key to prevent rusting of ferrous metals is to protect the iron atoms from exposure to oxygen and water or water vapor. For it to work, the protection must be adhered to the surface of the ferrous metal, so surface preparation is key to ensuring sufficient protection. Here are some methods to prevent rusting:
- Painting
- Oil or Grease
- Protective Coatings
- Passivation
- Galvanizing
- Electroplating
Fictiv – Sourcing Simplified
Now that you know the basics of oxidation, corrosion and rust, you can design even better metal CNC machined parts — and Fictiv can deliver the parts you need.
Fictiv is your operating system for custom manufacturing that makes part procurement faster, easier, and more efficient. Our manufacturing partners have incredibly skilled machinists and finishing experts who can deliver quality parts at incredible speeds — whether you need precision anodized aluminum components or passivated, galvanized or electroplated steel parts to be protected from corrosion.
Create an account and upload your design to see what our instant quote process, design for manufacturability feedback, and intelligent platform can do for you.