Time to read: 8 min
Filler materials or compounds can be added to thermoplastics to improve their mechanical properties, lower material costs, or achieve a combination of both. The properties of filled thermoplastics can vary depending on the type of base plastic, the type of filler used, and the filler concentration. These improved characteristics make filled thermoplastics valuable across various applications and industries.
In this article, we’ll take an in-depth look at the fillers used in thermoplastics, how they modify those plastics, the different types of fillers and their effects on plastics, when to use filled vs. unfilled plastics, and design constraints for filled plastic components.
How Plastic Fillers Modify Thermoplastic Properties
Plastic fillers can be used to significantly modify the properties of thermoplastics. Some properties are very advantageous to the end function of the part, including:
Tensile Strength
Adding glass or carbon fibers can significantly increase the tensile strength of thermoplastics. Glass-fiber-reinforced nylon, for example, can have tensile strengths that are more than double those of standard unfilled nylon.
Stiffness and Rigidity
Fillers like glass fibers are commonly used to increase the stiffness and hardness of polymers. Other inert fillers, such as chalk, talc, and barium sulfate, can also be used and are usually less expensive than the base polymer.
The size of the particles added to the plastic is important; finer particles typically distribute more uniformly and can enhance strength and surface finish, while larger, coarser particles may reduce mechanical strength and lead to stress concentrations if poorly bonded or dispersed.
Heat Resistance
Fillers can be used to reduce the polymer’s coefficient of thermal expansion (CTE), allowing it to better maintain shape and strength at elevated temperatures. Mineral fillers like talc and glass fibers also increase the heat deflection temperature (HDT) of polymers.
Dimensional Stability
Some filled thermoplastics have lower shrinkage and better warpage control during molding. Talc is particularly effective at reducing warpage in parts with uneven thickness or complex geometries. Talc also helps with moldability and reducing molding cycle times. However, limiting warpage could come at the expense of mechanical properties like tensile strength.
Disadvantages of Plastic Fillers
There are also trade-offs to consider when adding fillers to your polymer matrix, including:
- Reduced Impact Resistance: It is common for fillers to reduce the ductility and impact strength of the base polymer. The stiffer the filler, the more brittle the material can become under sudden stress.
- Surface-Finish Degradation: Fillers can lead to rougher surface textures and visible flow lines, especially with high filler loadings. This can require additional finishing or coating steps, or confine applications to internal parts that cannot be seen post-assembly.
- Increased Tooling Wear: Abrasive fillers like glass and carbon fibers can accelerate wear on molding equipment. Hardened tool steels are usually used for this reason.
- Higher Injection Pressures Required: Fillers can increase the viscosity of the polymer melt, which may require higher injection pressures during molding. This puts added stress on molding machines and increases energy consumption.
- More Robust Tooling Needed: To accommodate the abrasive nature of certain fillers and the elevated pressures involved, tooling must be built with stronger, more wear-resistant materials, which could increase initial capital costs.
- Potential for Poor Filler Dispersion: Inadequate mixing or filler dispersion can lead to weak points, non-uniform mechanical properties, or cosmetic defects in the final part.
Types of Plastic Fillers and Their Effects
Glass-Filled Plastics
Glass fibers are among the most commonly used reinforcement fillers in engineering thermoplastics, especially in resins like nylon (PA), PBT, PEI, and PPS. These fibers, typically added as short or long strands, significantly improve mechanical properties. In fact, long-strand glass-filled polypropylene has been shown to triple tensile strength and quadruple stiffness at room temperature compared to its unfilled counterpart.
The fibers act as load-bearing elements within the matrix, making the plastic more rigid and dimensionally stable. These qualities are essential for parts that experience mechanical stress, such as automotive brackets, pump housings, gears, and industrial structural components. However, the orientation of the fibers during molding plays a crucial role in determining final part strength. That’s why part design and (mold) gate placement must be optimized to maximize fiber alignment in the direction of stress.
Most glass fillers are short-chopped strands, but the use of long-strand fiber technology is growing. These provide better load transfer and more uniform reinforcement but require careful processing, as longer fibers are more likely to shear during molding. The addition of coupling agents, such as silanes, improves adhesion between the fibers and resin, enhancing mechanical strength and especially impact resistance, which is a known drawback in highly rigid, glass-filled composites.
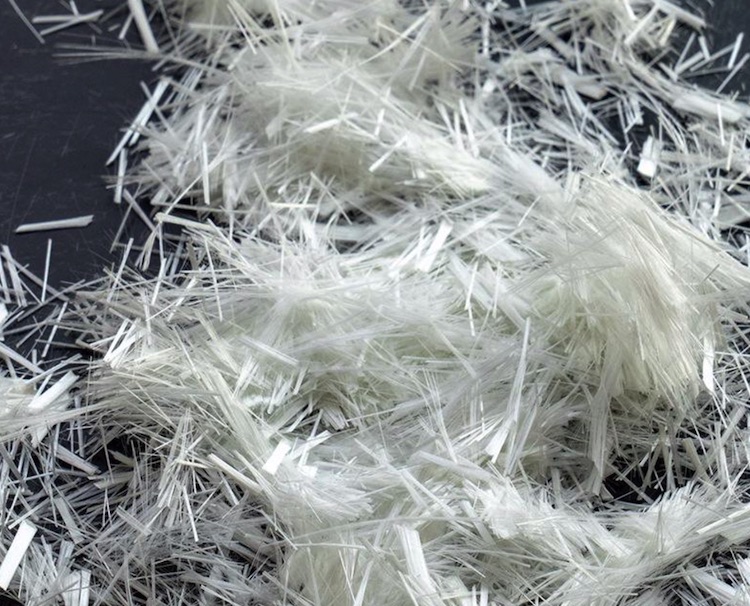
Carbon Fiber-Filled Plastics
Carbon fiber fillers are reserved for high-performance applications where lightweight strength, stiffness, and electrical conductivity are crucial. Unlike glass, which adds bulk and weight, carbon fibers drastically increase elastic modulus without adversely affecting density. This makes them ideal for aerospace, electronics, drones, and high-end automotive parts.
When incorporated into thermoplastics such as PEI, PEEK, or PPS, they form a composite with a superior modulus-to-weight ratio, enhanced fatigue resistance, and excellent dimensional stability under thermal and mechanical stress. Their electrical conductivity also makes them ideal for EMI shielding enclosures, static-dissipative components, and electronic housings.
Carbon-filled plastics, however, tend to be brittle, with lower impact strength unless carefully modified. The cost is also significantly higher than traditional fillers, and processing challenges include abrasion of tooling and a tendency for fibers to align during flow, creating anisotropic (direction-dependent) properties. Despite this, their performance in weight-sensitive structural applications, like UAV fuselages or automotive body panels, often outweighs the drawbacks.
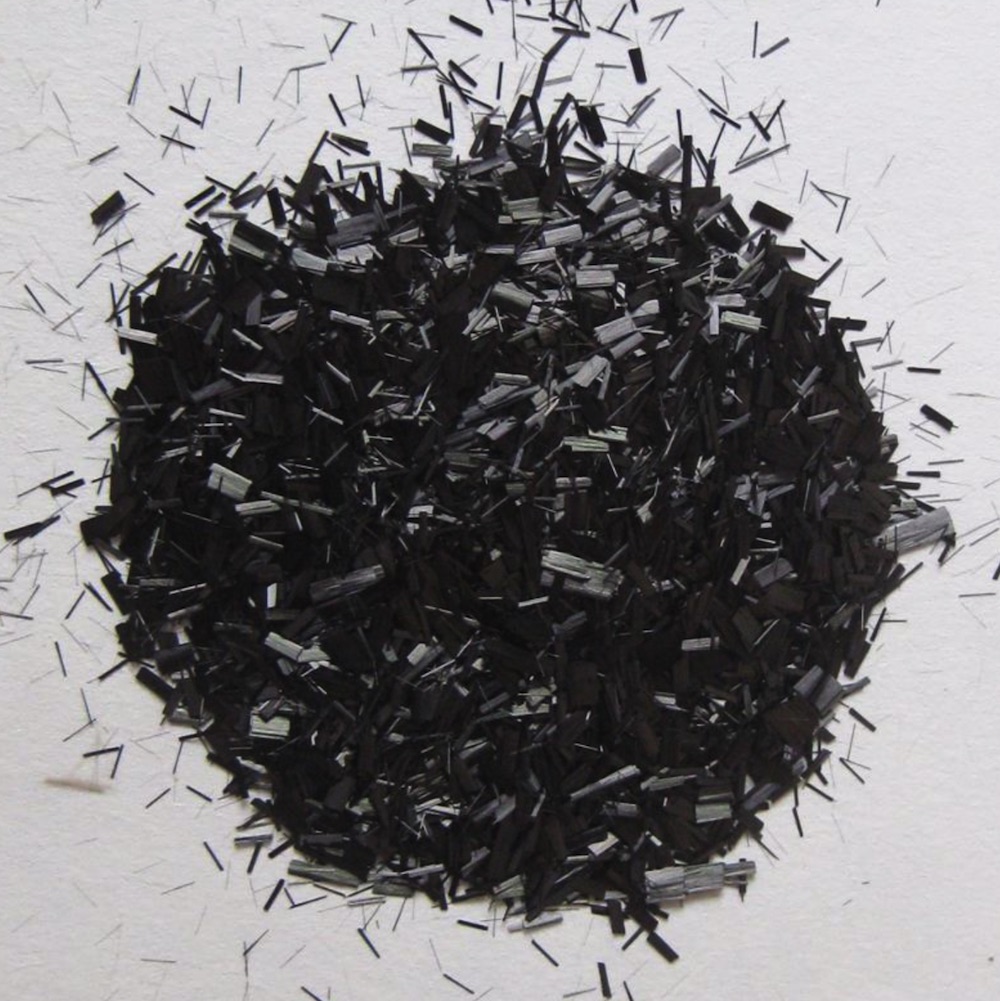
Mineral-Filled Plastics
Mineral fillers such as talc, calcium carbonate, mica, silica, and wollastonite are widely used in thermoplastics—particularly polypropylene (PP), nylon (PA), and PVC—to enhance dimensional stability, heat resistance, and processability, while reducing raw material cost.
Here’s a short overview of different mineral-filled plastics:
- Talc: The most common mineral filler in polypropylene. It offers good rigidity, thermal insulation, and creep resistance, along with excellent molding performance. It is commonly used in automotive interiors, appliance parts, and food packaging.
- Calcium Carbonate and Chalk: Reduce shrinkage during molding, contribute to flame retardancy, increase stiffness, and are cost-effective.
- Silica: Improves dielectric strength, moisture and heat resistance, and mechanical strength while increasing the glass transition temperature.
- Diatomaceous Earth: A soft, fossilized silica that enhances chemical, thermal, and electrical insulation while being less abrasive than quartz.
- Wollastonite: A needle-like calcium silicate that improves dimensional stability, UV resistance, and hydrolysis resistance.
- Kaolin (Clay): Offers good electrical properties and melt flow; calcined kaolin improves acid resistance and is often used in wire insulation.
- Mica: Enhances dimensional stability, chemical resistance, barrier properties, electrical insulation, and thermal resistance. It significantly reduces mold shrinkage by up to 85% in nylon and is commonly used with silane-based coupling agents to improve bonding with the polymer matrix.
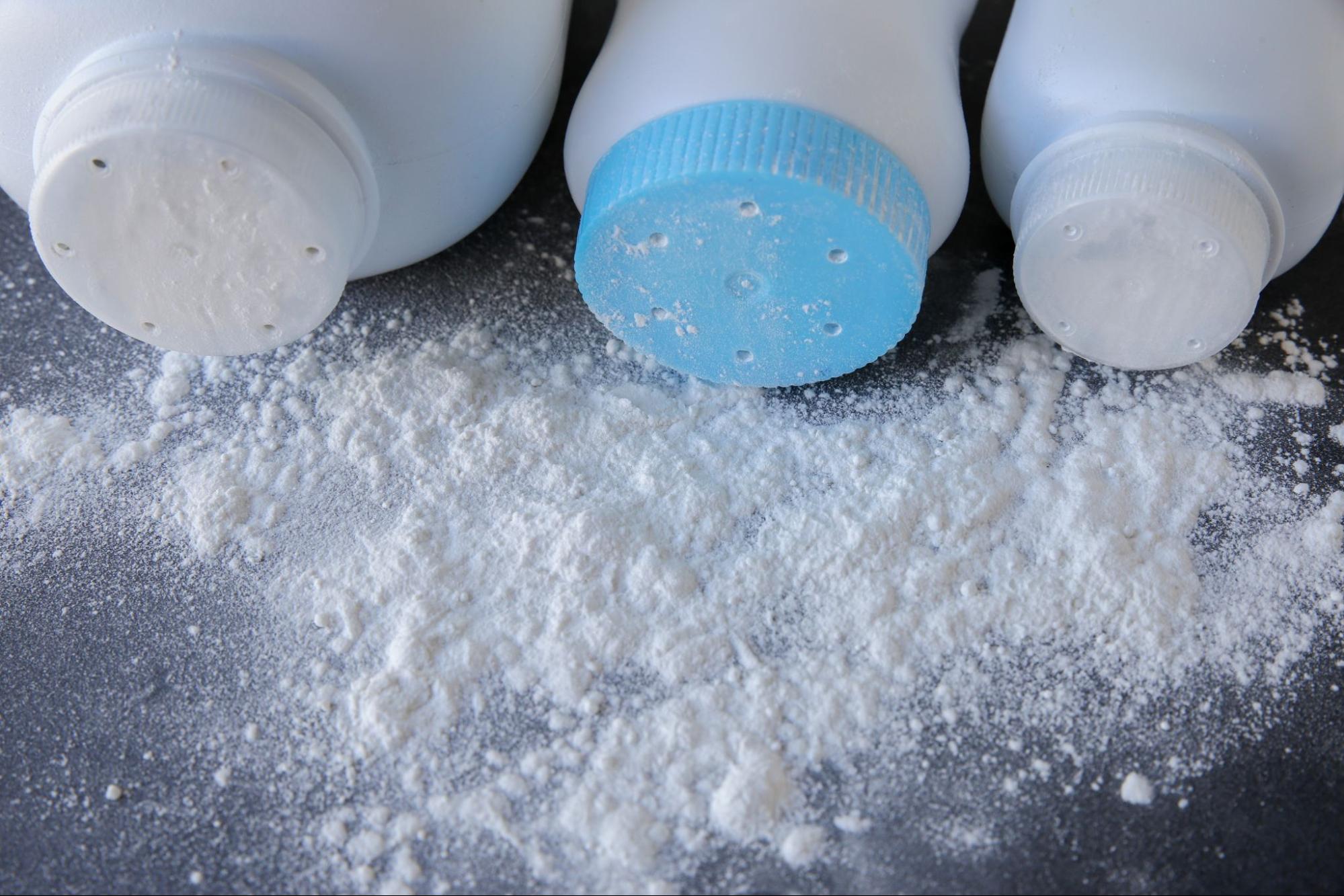
Design and DFM Considerations for Filled Thermoplastics
When designing with filled plastics, several key factors impact part performance and manufacturability:
Fiber Orientation and Mechanical Anisotropy
In fiber-filled thermoplastics, the fibers tend to align in the direction of flow during molding, resulting in anisotropic mechanical properties. This means strength and stiffness vary depending on the load direction, so designers must account for directional load paths to avoid unexpected failures.
Surface Finish
Increasing filler content, especially fibers, generally results in a rougher surface finish due to fiber ends protruding or affecting flow patterns. Secondary finishing or coatings may be necessary to enhance the surface finish.
Higher Viscosity
The addition of fillers can raise the viscosity of the feed material during molding. This makes it harder to inject the thermoplastic into complex molds. As a result, design features such as thin walls may not be viable. It may be possible to mitigate this issue by increasing the temperature, but higher cycle costs could significantly diminish economies sought by the use of the filler.
Shrinkage Reduction and Part Warpage
Fillers can reduce overall shrinkage and improve dimensional stability, helping to minimize warpage. However, uneven fiber distribution or orientation can still cause distortion, so careful gate placement and molding parameters are critical. For tolerance-sensitive parts, it may be necessary to test production with a low-cost mold before applying any necessary modifications to a finalised hardened steel mold.
Mold and Equipment Wear
Abrasive fillers like glass and carbon fibers cause increased wear on the mold and on any tools being used for post-molding machining. Proper tooling materials, like high-quality tool steels, chip control strategies, and optimized cutting parameters, are necessary to maintain tool life.
Increased Ejection Force and Draft Angles
Filled parts usually have higher ejection forces due to increased friction. To ensure that the part is released smoothly without damage and excessive mold wear, adequate draft angles are needed.
Get more DFM tips with our injection molding design guide.
3D Printing Limitations With Filled Plastics
Integrating fiber- and mineral-filled thermoplastics into additive manufacturing comes with technical limitations that affect print quality, durability, and process compatibility.
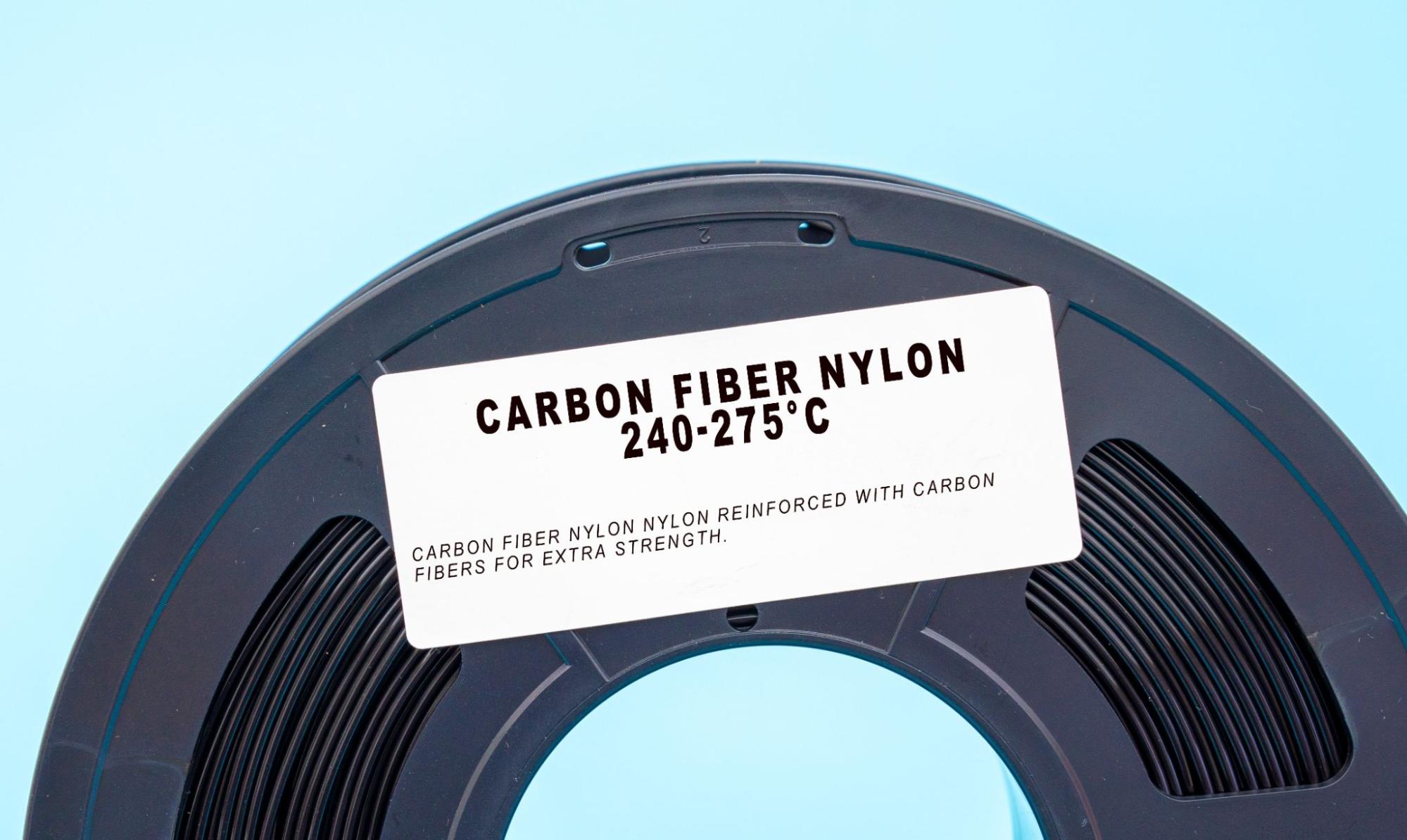
FDM (Fused Deposition Modeling)
FDM is currently the most accessible 3D printing method for working with filled plastics. Glass- and carbon-filled filaments are commercially available and provide improved stiffness, strength, and heat resistance compared to unfilled filaments.
However, these benefits come with drawbacks. The abrasive nature of reinforcing fibers leads to rapid nozzle wear, requiring the use of hardened steel or ruby-tipped nozzles. Additionally, filled filaments often result in poor interlayer adhesion and increased stringing during printing, which can compromise both the mechanical performance and the surface finish of printed parts.
SLA/DLP
Stereolithography (SLA) and Digital Light Processing (DLP) technologies use liquid resins cured by light, which inherently limits their compatibility with fiber reinforcement. Fibers cannot remain suspended in resin and are not aligned during curing, making traditional fiber-filled composites incompatible with these processes.
Instead, these printers may use ceramic or glass powder-reinforced resins, which offer some mechanical improvements but do not match the structural benefits of true fiber-filled thermoplastics. Furthermore, SLA/DLP resins designed for flexibility or durability cannot replicate the high modulus or thermal stability of fiber-reinforced materials.
SLS (Selective Laser Sintering):
SLS presents a more capable platform for producing filled plastic parts, using powdered thermoplastics that can include additives such as glass or mineral fillers. Glass-filled nylon, for example, offers increased rigidity and better thermal resistance compared to standard nylon.
SLS also produces parts with less anisotropy than FDM, thanks to its layer-by-layer sintering mechanism, which eliminates the need for extrusion. However, filled SLS powders are often expensive, and while the resulting parts perform well, they still do not reach the mechanical strength of injection-molded counterparts.
Produce Stronger Thermoplastic Parts With Glass, Carbon, or Mineral Fillers
Plastic fillers, such as glass fibers, carbon fibers, and mineral powders, significantly enhance the mechanical, thermal, and dimensional properties of thermoplastics, enabling their use in demanding engineering applications. However, these benefits come with trade-offs such as reduced impact resistance, rougher surfaces, increased tooling wear, and manufacturing complexities. Successful application relies on understanding these factors, designing for the anisotropy and behavior of filled materials, and selecting compatible manufacturing processes.
Do you need high-performance plastic parts with enhanced strength or stability? Fictiv offers 3D printing, CNC machining, and injection molding of filled plastics for both prototyping and production purposes.
Get an instant quote on our digital manufacturing platform.