Time to read: 7 min
Glass filled nylon is a composite material that contains nylon and a specific percentage of glass fibers, typically 30% to 50%. Nylon injection molding produces strong and heat-resistant parts, but unfilled nylon lacks the performance properties required for more demanding applications. With the addition of glass fibers, however, nylon’s thermal and mechanical properties improve.
The addition of glass fibers increases nylon’s impact resistance, tensile strength, hardness, stiffness, and wear resistance; however, there are trade offs to consider. Specifically, glass filled nylon is more brittle and prone to breaking than pure nylon. Because it’s also abrasive, glass filled nylon causes tooling and equipment to wear more quickly.
If you’re considering glass-filled nylon for your injection molding project, keep reading to lear more about this commonly used injection molding material, including:
● Advantages
● Disadvantages
● Applications
● Properties
● Design guidelines
● Processing requirements
● Potential alternatives
Fictiv works with a carefully-vetted network of injection molders who can produce complex parts at amazing speeds. Whether it’s for prototyping or production, you’ll also receive design for manufacturing (DFM) assistance along with your quote. Create a free Fictiv account to get started.
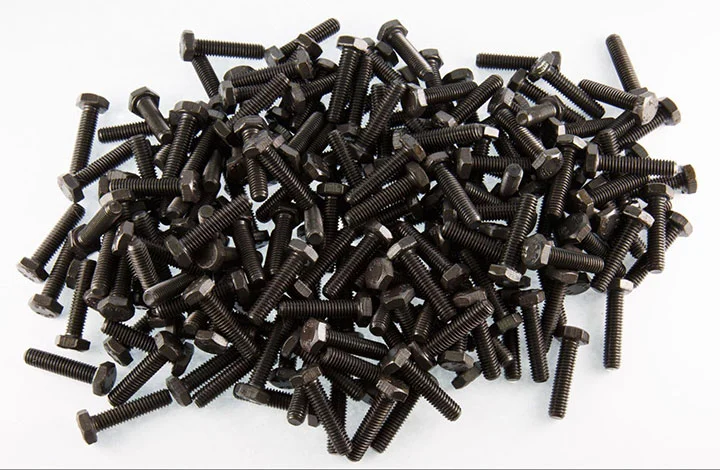
Advantages of Glass Filled Nylon
The advantages of using glass filled nylon for injection molding include its mechanical properties, heat resistance, and chemical resistance.
Mechanical Properties
Compared to pure nylon, glass filled nylon is harder, stiffer, and more wear resistant. Glass filled nylon also has greater creep resistance, the ability to resist distortion when subjected to prolonged compressive load over an extended period. Typically, creep develops in materials that are subjected to mechanical stresses at high pressures and operating temperatures.
Heat Resistance
Glass filled nylon has a higher coefficient of thermal expansion (CTE) than unfilled nylon. Because different materials expand and contract at different rates, a higher CTE may be important in assemblies with dissimilar materials. Note that CTE decreases as the percentage of glass fibers increases.
Compared to pure nylon, glass filled nylon provides greater dimensional stability at elevated temperatures. Depending on the percentage of fibers, the continuous service temperature for glass filled nylon ranges from 100°C to 150°C.
Chemical Resistance
Like pure nylon, glass filled nylon resists a wide range of chemicals, including hydrocarbons, motor oil, petroleum-based grease, organic bases, and some inorganic compounds. This make glass filled nylon a good choice for automotive components, such as gears and bushings, that require strength plus heat and chemical resistance
Disadvantages of Injection Molding Glass Filled Nylon
The disadvantages of glass filled nylon for injection molding include its abrasiveness, uneven material shrinkage, and brittleness.
Abrasiveness
Because they are abrasive, the fibers in glass filled nylon can cause significant wear in tooling and equipment. Consequently, the injection molds for glass filled nylon parts are usually made of harder materials. This can result in increased tooling costs and longer machining times. With Fictiv, however, you can get cost-effective steel molds in just a few weeks.
Uneven Material Shrinkage
The fibers in glass filled nylon orient themselves in the direction of mold flow. This can result in uneven material shrinkage, parts warping, and properties with different values when parts are measured in different directions (anisotropy).
Brittleness
Glass filled nylon is harder and more brittle than pure nylon. This increased brittleness makes injection molded parts more susceptible to breaking under shock loads, a sudden and drastic increase in load (e.g., when a heavy weight is added).
Applications for Glass Filled Nylon Injection Molding
Glass filled nylon can be injection molded for automotive, industrial, and consumer applications.
Automotive Applications
● Gears for wiper motors
● Wire connectors
● Thermostat housings
● Bushes and bushings
● Brake fluid reservoirs
Industrial Applications
● Fasteners
● Low-friction bearings and wheel liners
● Cableway carriage sheaves
● Spacers
Consumer Goods
● Appliance handles and fittings
● Power tool housings
● Sporting goods
● Frames and handles for luggage
Properties of Injection Molded Glass Filled Nylon
Glass filled nylon is categorized by the percentage of glass fibers. Generally, a higher percentage of fibers means greater tensile strength, hardness, and flexural strength. However, brittleness also increases. Table 1 below lists the properties of injection molded nylon that is filled with 30% glass fibers and 50% glass fibers.
30% Glass-Filled Nylon | 50% Glass-Filled Nylon | ||
Physical | Density (g/cm3) | 1.37 | 1.56 |
Shrinkage Rate (cm/cm) – Linear | 0.0042 | 0.0031 | |
Rockwell Hardness (R) | 119 | 119 | |
Mechanical | Tensile Strength at Yield (MPa) | 148 | 202 |
Elongation @ break (%) | 4.46 | 3.10 | |
Flexural Modulus (GPa) | 7.45 | 12.9 | |
Flexural Strain @ break (%) | 4.86 | 3.79 | |
Injection Molding | Drying Temperature (°C) | 84.2 | 84.1 |
Melt Temperature (°C) | 266 | 271 | |
Mold Temperature (°C) | 83.7 | 88 |
Design Guidelines for Glass Filled Nylon Injection Molding
Glass filled nylon parts that are poorly designed can exhibit injection molding defects. Fictiv’s injection molding experts can help you refine your design so that you get results. Before starting your next project, download our free “Injection Molding Design Guide” to use as a reference.
Download the Injection Molding Design Guide
The following sections examine some injection molding design considerations for glass filled nylon parts.
Wall Thickness
Whenever possible, apply a uniform wall thickness throughout your part. If you need to use a greater thickness in some areas, make the transition from thinner to thicker sections gradual. Do not use transitions that are greater than 10% to 15% of the nominal wall thickness. Generally, the recommended minimum wall thickness for glass filled nylon is 3.175 mm.
Shrinkage
Like other thermoplastics, nylon shrinks when it cools. Unfilled nylon has a shrinkage ratio of 1.5% in any direction. With the addition of glass fibers, however, nylon shrinks .03% in the flow direction and 1.9% in the cross flow direction. Shrinkage is more visible on parts with high gloss surface finishes, so consider using a less glossy finish if you’re concerned about shrink marks.
Radii
Sharp corners are difficult to injection mold. Therefore, apply an internal or fillet radii to inside corners and an external or round radii to outside corners. In general, make the radius at least 50% of the adjacent wall thickness. Larger radii (around 75% of wall thickness) can reduce stress concentrations, improve mold flow characteristics, and reduce the potential for internal stresses during molding.
Draft Angle
Draft is the angle you apply to the vertical walls of parts so that they eject cleanly from the injection mold. Because nylon has self-lubricating properties, it’s possible to use smaller draft angles with glass filled nylon than with other materials. In general, apply a draft angle between 0.5% and 1%. For textured surfaces, apply a 1% draft angle per 0.025 mm of texture depth.
Part Tolerance
Injection molding tolerances are acceptable variations in size for overall dimensions and part features. As a rule, parts with tighter tolerances are more expensive because they have stricter molding and processing requirements. Parts with fine tolerances are more expensive to produce than parts with commercial tolerances. Table 2 below shows part tolerances for 30% glass filled nylon. Note how dimensional tolerances also vary by part size and type of finish.
Part Tolerance
Injection molding tolerances are acceptable variations in size for overall dimensions and part features. As a rule, parts with tighter tolerances are more expensive because they have stricter molding and processing requirements. Parts with fine tolerances are more expensive to produce than parts with commercial tolerances. Table 2 below shows part tolerances for 30% glass filled nylon. Note how dimensional tolerances also vary by part size and type of finish.
Commercial | Fine | ||||
1-20 mm | 21-100 mm | 101-160 mm | For every 20 mm over 160 | 1-20 mm | 21-100mm |
0.060 | 0.120 | 0.240 | 0.080 | 0.030 | 0.100 |
Threads
Glass filled nylon parts support the use of threads. In general, avoid using sharp root radii that can cause high stress concentrations. Use larger pitch threads instead. Because internal threads can significantly increase the cost of tooling, avoid them unless necessary.
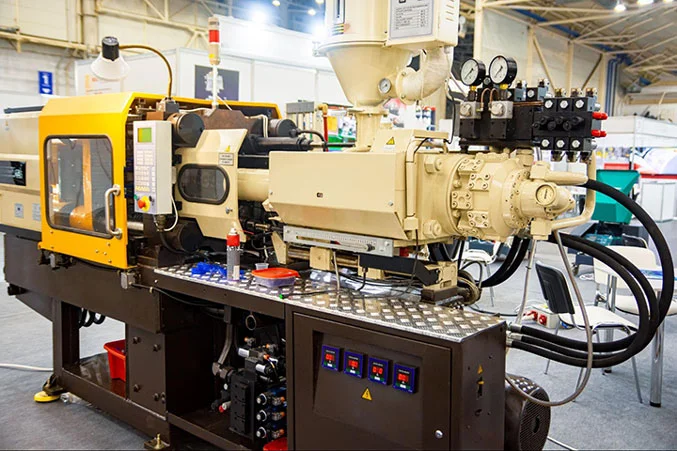
Glass Filled Nylon Processing Guidelines
During injection molding, glass filled nylon behaves similarly to unfilled nylon, which comes in grades such as Nylon 6, Nylon 66, and PA 12. Still, there are some specific processing guidelines for injection molders to consider. Because adherence to these guidelines is beyond a part designer’s immediate control, it’s important to work with an experienced injection molder like the ones in Fictiv’s carefully vetted network.
Moisture
Because it absorbs moisture from the atmosphere, glass filled nylon requires drying before injection molding. For best results, dry the material to reduce its moisture content to less than 0.2% by weight. After injection molding is complete, glass filled nylon parts may absorb up to 2.5% moisture by weight.
Temperature Control
Glass filled nylon injection molding temperature is also important to consider. Heating the mold to between 100°C and 120°C helps impart an optimal surface finish to glass filled nylon parts. If the cylinder temperature is too low, especially in the rear zone, the average length of the glass fibers becomes shorter. In turn, this reduces mechanical properties. To mitigate this, use a reverse heat profile with a hotter rear zone and cooler subsequent zones.
Injection Pressure
The addition of glass fibers to nylon increases the material’s melt viscosity, or resistance to flow. Consequently, higher injection pressures are needed. For best results, use injection pressures between 75 and 100 MPa.
Injection Speed
Because glass filled nylon has a rapid crystallization speed, it must be injected at moderate to fast speeds. Often, two-part filling cycles are used. Initially, the mold is filled at a faster speed, ideally less than four seconds. This speed is then slowed at the end of the injection cycle.
Potential Alternatives to Glass Filled Nylon
Glass filled nylon might not be the best material for your injection molding application. If that’s the case, glass filled PBT and PEEK are potential alternatives.
Glass Filled PBT
Glass filled polybutylene terephthalate (PBT) provides good UV resistance and dielectric strength. It’s also available in FDA grades. The downside to using glass filled PBT is that its rapid crystallization rate makes it challenging to injection mold.
PEEK
Polyether ether ketone (PEEK) is a high-performance polymer with excellent thermal resistance, chemical resistance, and mechanical strength. Although PEEK is more costly than glass filled nylon, it is often used in high-performance applications
Succeeding With Glass Filled Nylon Injection Molding
Glass filled nylon is an injection molding material with many desirable properties, but a manufacturing-ready design and a skilled production partner are critical. Fictiv has the engineering experts and manufacturing network you need to get quality parts fast. From prototyping through production, we’re here to help you succeed.
Create your free Fictiv account and request an injection molding quote today — we mold complex parts at ridiculous speeds!