Time to read: 9 min
Plastic materials for injection molding range from commonly used polymers to specialty plastics and polymer blends. There are hundreds of different plastic resins available, and they each have different end-use properties and processing requirements. Plus, there are different grades of the same plastic material, including resin types with fillers such as glass fibers or carbon fibers, and specific brand names.
With so many choices, it’s daunting to choose the right material for your project. Whether your project involves medical plastic injection molding, molded plastic components for the automotive industry, or something else, Fictiv experts are ready to help you go from design to production quickly.
And if you’re looking for help with your injection molding projects, check out our Guide to Injection Molding Production. This downloadable PDF explains what you need to know to make your next injection molding project a success.
By signing up, you agree to our Terms of Use and Privacy Policy. We may use the info you submit to contact you and use data from third parties to personalize your experience.
Otherwise, keep reading to learn about the top 10 plastic injection molding materials.
The Top 10 Plastic Injection Molding Materials
These are the most common plastic materials for injection molding:
- acrylic (PMMA)
- acrylonitrile butadiene styrene (ABS)
- nylon (polyamide, PA)
- polycarbonate (PC)
- polyethylene (PE)
- polyoxymethylene (POM)
- polypropylene (PP)
- polystyrene (PS)
- thermoplastic elastomer (TPE)
- thermoplastic polyurethane (TPU)
This article discusses their properties, including comparisons to other materials, along with injection molding applications, grades, and brand names for each.
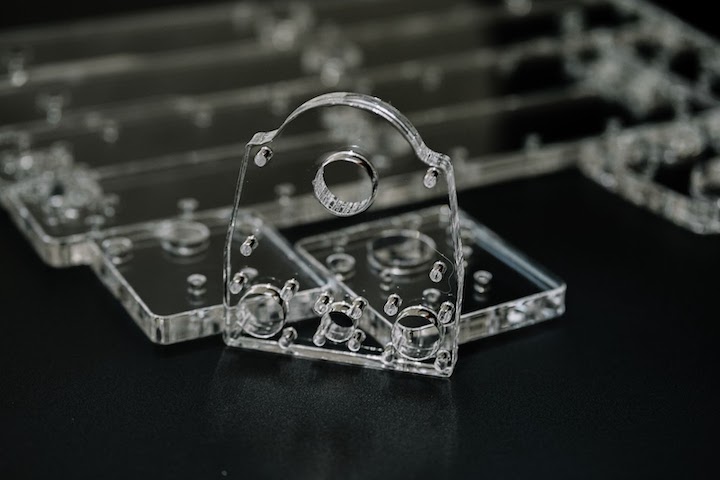
Acrylic (PMMA)
Acrylic is a strong, clear thermoplastic that provides a lightweight, shatter-resistant alternative to glass. This injection-molded material also offers excellent optical clarity so that a high percentage of light passes through. Acrylic resists ultraviolet (UV) light and weather, and is also known as PMMA, or by its full chemical name: poly(methyl methacrylate).
Properties
Unlike some plastics, acrylic can withstand exposure to water and hold tight tolerances. PMMA won’t absorb odors, but it cannot resist solvents and is easily stained by greases and oils. Although injection-molded acrylic has high tensile strength, it’s prone to stress cracking under heavy loads.
Applications
Applications for acrylic injection molding include windows, greenhouses, solar panels, bathroom enclosures, and other transparent components for architectural, lighting, and outdoor applications.
Grades and Brands
General-purpose and specialty grades of PMMA plastics are available, including:
- General-purpose acrylic is used in commodity products.
- Sign-grade acrylic is stronger and provides excellent light transmission for outdoor signage.
- Marine-grade acrylic resists continuous exposure to water.
Common brand names for acrylic plastics include Trinseo PLEXIGLAS®, which is available with high heat resistance, and DuPont LUCITE®, which has excellent optical clarity and transparency.
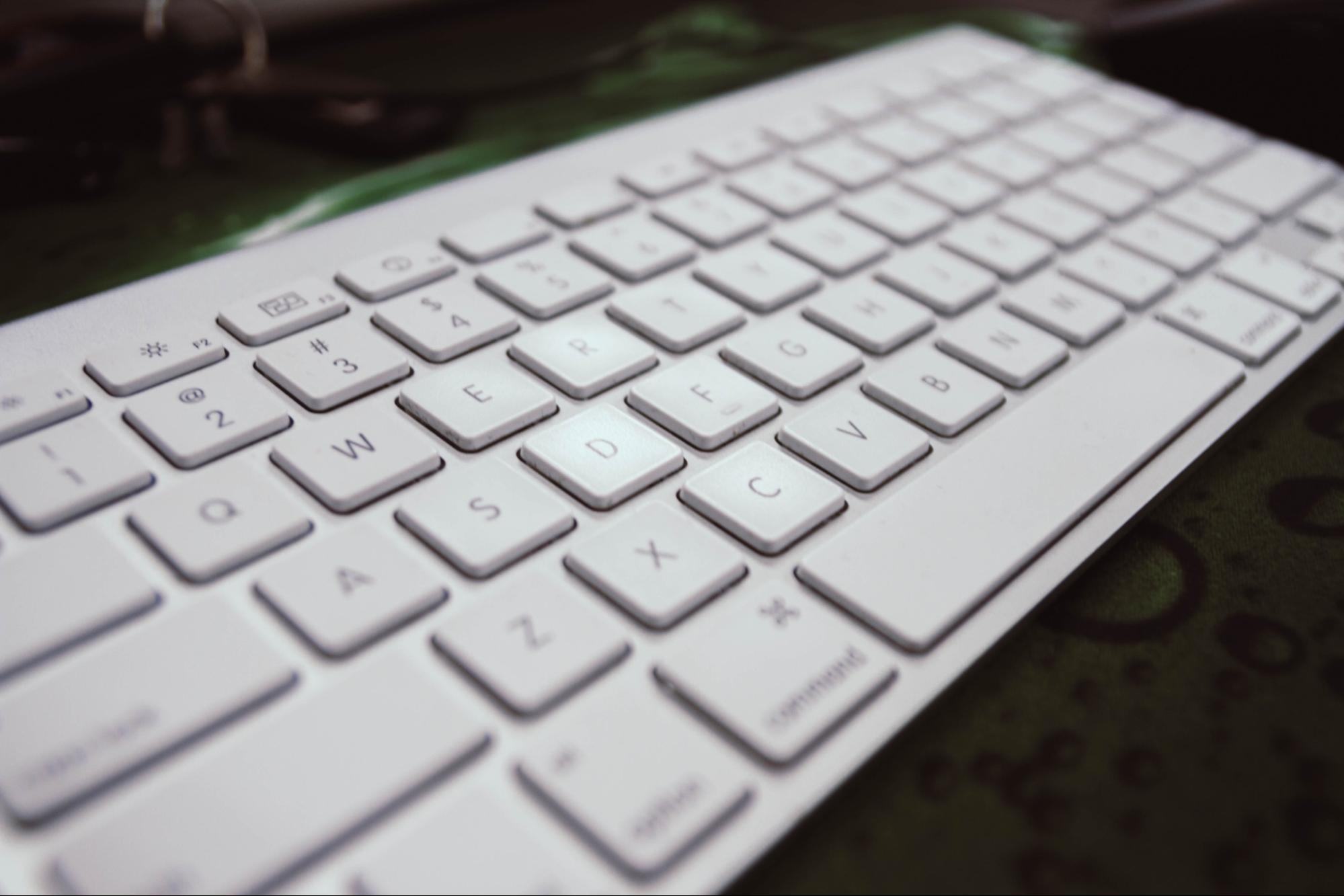
Acrylonitrile Butadiene Styrene (ABS)
ABS has a relatively low melting point that makes it easy to mold. This opaque polymer supports the use of colorants as well as various textures and surface finishes. Its butadiene content delivers exceptional toughness, even at low temperatures, and its styrene content imparts a shiny, attractive finish to plastic injection molded parts.
Properties
ABS is known for its strength and impact resistance, but it lacks strong resistance to sunlight (UV), water, and weather. Compared to acrylic, injection-molded ABS is not a good choice for outdoor applications. ABS also generates significant smoke when burned and, unlike nylon, provides poor resistance to high friction.
Applications
ABS injection molding is used to produce many types of plastic parts, including:
- keyboard keys
- protective headgear
- electrical outlet wall plates
- automotive parts like wheel covers
- consumer goods
- sports equipment
- industrial fittings
Grades and Brands
Well-known brands of ABS include Samsung Starex®, Toray Toyolac®, BASF Terluran®, and Ineos Lustran®.
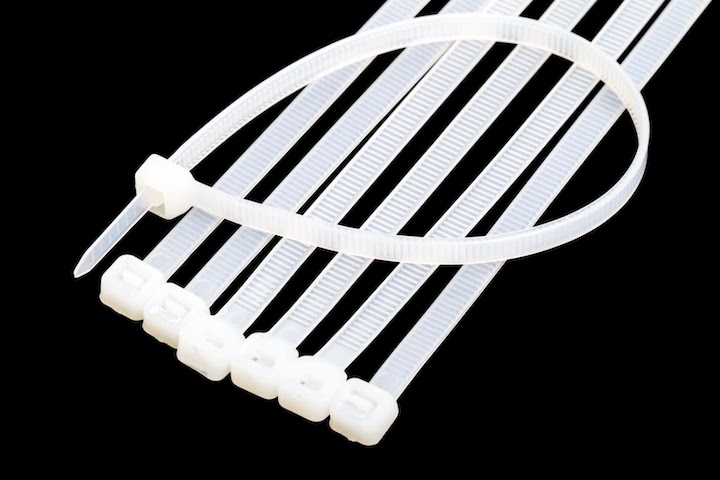
Nylon Polyamide (PA)
Nylon is a synthetic polyamide (PA) that combines toughness and high heat resistance with high abrasion resistance, good fatigue resistance, and noise-dampening properties. Nylon isn’t inherently flame-resistant, but flame-retardant versions are available. Similarly, although nylon can be degraded by sunlight, a UV stabilizer can be added to improve outdoor performance.
Properties
Compared to other plastics, nylon provides poor resistance to strong acids and bases. Nylon is not as strong as polypropylene and can’t match polycarbonate for impact resistance. Injection molding nylon is challenging because it’s prone to shrinkage and is subject to inadequate mold filling.
Applications
Applications for nylon injection molding include:
- strong mechanical parts such as bearings, bushings, gears, and slides
- casings and snap-fit closures
- threaded inserts and kinetic parts
- jigs and fixtures
With its low coefficient of friction, nylon is also well-suited for applications with high-friction and wear.
Grades and Brands
Nylon comes in four main grades, and each has slightly different mechanical properties:
- Nylon 11 is used in outdoor applications and has greater resistance to dimensional changes.
- Nylon 12 has the lowest melting point of all four grades and resists water absorption.
- Nylon 46 has the highest operating temperature.
- Nylon 66 has a high melting point and resists acids used in chemical processing.
Nylon can also be filled with glass fibers for greater mechanical strength.
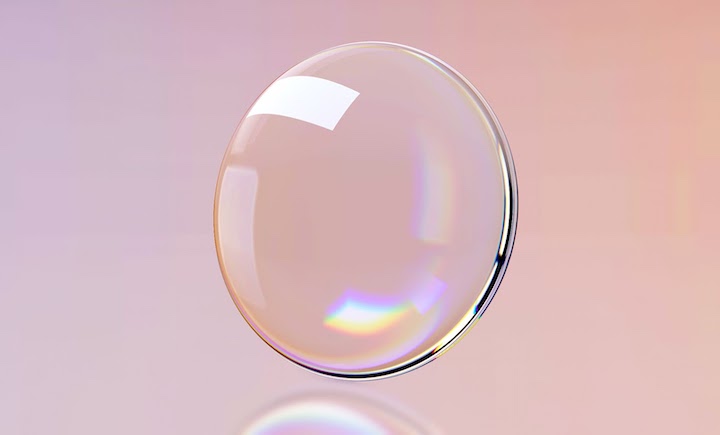
Polycarbonate (PC)
Polycarbonate is strong, lightweight, and naturally transparent. This plastic injection molding material has excellent optical properties to support light transmission, but maintains its color and retains its strength when pigmented. Although it isn’t scratch-resistant, polycarbonate is significantly stronger than glass and is extremely durable.
Properties
Injection-molded polycarbonate is sometimes used instead of acrylic because PC maintains its physical properties over a wider temperature range. PC requires high processing temperatures, however, which can make it more expensive to mold. With its predictable and uniform shrinkage, however, polycarbonate offers precise dimensional control for tighter tolerances.
Applications
Applications for polycarbonate injection molding include:
- machinery guards
- clear and tinted windows
- diffusers and light pipes for light-emitting diodes (LEDs)
- clear molds for urethane and silicone casting
Because it contains the chemical bisphenol A (BPA), polycarbonate is not recommended for food preparation or storage.
Grades and Brands
Polycarbonate plastic can be filled with glass and is available in grades that contain a relatively small percentage of stainless steel fiber. Popular brands include SABIC Lexan®, which is available in flame-resistant versions, and Covestro Makrolon®, which has glass-like transparency.
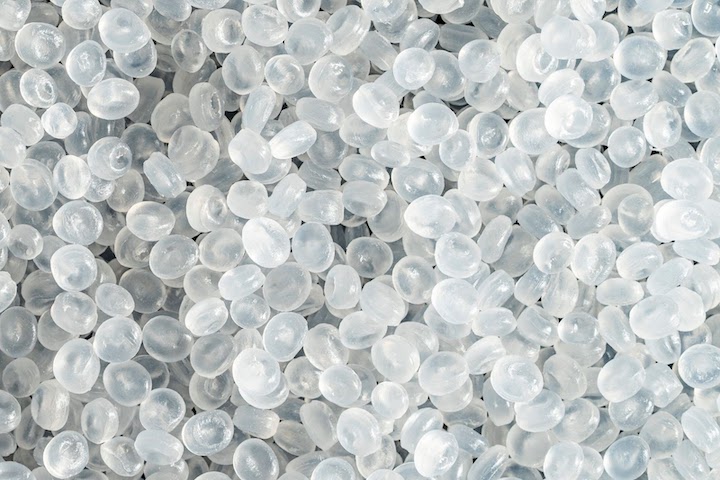
Polyethylene (PE)
Polyethylene is the most commonly used plastic in the world and is a commercial polymer that can be selected according to its density. High-density polyethylene (HDPE) and low-density polyethylene (LDPE) both provide chemical resistance, but they differ in terms of their hardness, flexibility, melting point, and optical transparency.
Properties
PE plastics include polyethylene terephthalate (PET, PETE), a material that is not defined by its density. Like LDPE, PET can be as clear as glass; however, designers can also select grades of PET or PETE with different levels of optical clarity. HDPE, LDPE, and PET all resist moisture and chemicals, but LDPE is softer and more flexible than HDPE, which is an opaque material.
Applications
Applications for polyethylene injection molding may be limited to indoor applications because of their poor UV resistance. Because they are unable to withstand high service temperatures, these plastic materials may not be suitable for some processing applications. Often, injection molded polyethylene is used in products such as housewares, toys, food containers, and automotive parts.
Grades and Brands
PE plastics come in numbered grades where higher numbers generally indicate higher densities. For example, HDPE 500 has a higher density than HDPE 300. Both grades have a higher density than LDPE, which also uses a numbering system for grades. BASF and DuPont are two of the leading suppliers of PE for engineering (as opposed to general-purpose) applications.
Polyoxymethylene (POM)
Polyoxymethylene (POM) is an engineering plastic that is also known as acetal. It combines excellent rigidity with thermal stability and has a low coefficient of friction. This plastic material has low water absorption and good chemical resistance. In terms of appearance, POM plastics are naturally opaque and white in color.
Properties
In its pure form, acetals have low impact strength and a very high rate of thermal expansion. Yet, POM can be reinforced with fiberglass or minerals for improved strength and stiffness. Compounds that are reinforced with both provide an excellent balance of mechanical properties. Because injected molded POM lacks resistance to sunlight, its outdoor applications are limited.
Applications
With its low coefficient of friction, injection-molded POM is used in bearings, gears, conveyor belts, and pulley wheels. Additional applications include fasteners, eyeglass frames, parts for knives and firearms, lock systems, and high-performance engineering components.
Grades and Brands
There are two main types of acetal plastics: homopolymers, which provide higher hardness and tensile strength, and POM copolymers. Neither type of material can be fire-rated to a standard such as UL 94, and both experience relatively high shrinkage during injection molding. Popular brand names for POM plastics include DuPont Delrin® and Ensinger TECAFORM®.
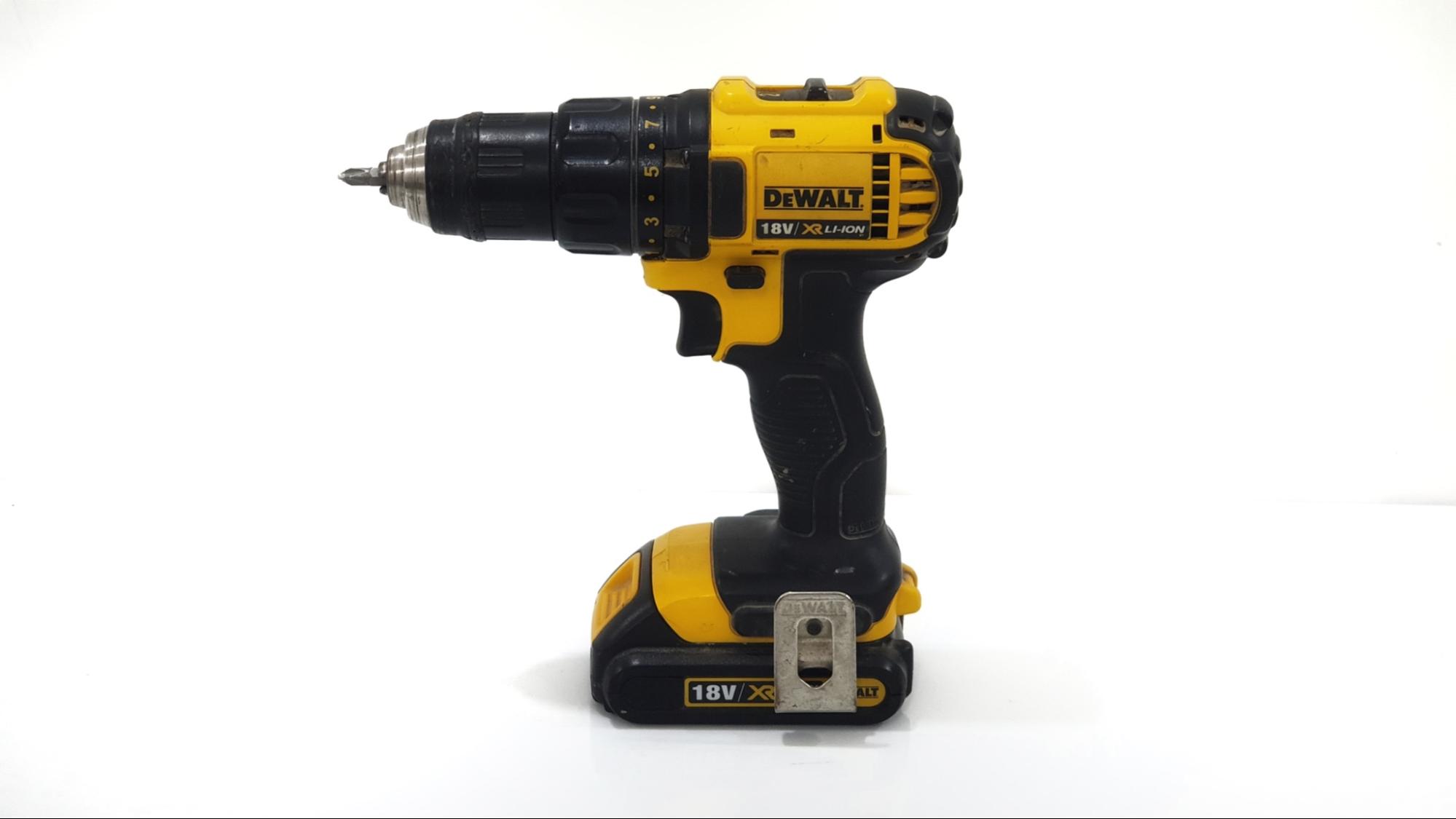
Polypropylene (PP)
Polypropylene is the second most commonly used plastic in the world. It provides good chemical resistance, retains its shape after torsion or bending, has a high melting point, and won’t degrade when exposed to moisture or water. Injected molded polypro, as PP is sometimes called, is also recyclable.
Properties
Despite its comparative advantages, polypropylene degrades with UV light and is extremely flammable. At temperatures above 100° C (212° F), this injection-molded plastic dissolves into aromatic hydrocarbons, such as benzene and toluene, which are harmful to humans. Polypropylene plastic is also difficult to bond and paint.
Applications
Applications for polypropylene injection molding include
- toys
- storage containers
- sporting goods
- packaging
- appliances
- power tool bodies
Grades and Brands
Pure polypropylene is a commodity plastic with the lowest density, but high crystalline polypropylene (HcPP) is filled with glass fibers for rigidity. Semitron® from Mitsubishi Chemical Advanced Materials is a leading brand.
Polystyrene (PS)
Polystyrene plastics are lightweight, relatively inexpensive, and resistant to moisture and bacterial growth. These commodity plastics also provide good chemical resistance to diluted acids and bases and have excellent resistance to gamma radiation, which is used to sterilize medical devices.
Properties
There are two main types of polystyrene: general-purpose polystyrene (GPPS) and high-impact polystyrene (HIPS). GPPS is brittle and has less dimensional stability than HIPS, which is compounded with butadiene rubber to enhance its material properties. GPPS also has a glass-like clarity whereas HIPS is opaque.
Applications
Applications for polystyrene injection molding include medical, optical, electrical, and electronic applications. With its higher impact strength, HIPS is often used with appliances and equipment, while injection-molded GPPS is used in plastic toys, cases, containers, and trays.
Both materials are flammable and susceptible to UV degradation.
Grades and Brands
Polystyrene can be filled with glass for added strength or co-polymerized with acrylic for greater clarity and improved chemical and UV stability. Brand names include American Styrenics PolyRenew® and BASF Polystyrol®.
Thermoplastic Elastomer (TPE)
TPE is a blend of plastic and rubber materials. It is processed like plastic but has the properties and performance of rubber. Known also as thermoplastic rubber (TPR), TPE can be stretched to moderate elongations and, upon the removal of this stress, returns to the material’s original shape. TPE can also be recycled repeatedly.
Properties
Compared to liquid silicone rubber (LSR), TPE is easier and less expensive to mold. Under sustained pressures, however, TPE is susceptible to creep, the tendency of a solid material to permanently deform. TPE also tends to lose its rubbery properties at higher temperatures and is significantly more expensive than other plastic injection molding materials.
Applications
Applications for TPE injection molding include:
- footwear
- medical devices
- auto parts
- pet products
Automotive applications include weather seals and shock dust boots. Medical applications include breathing tubes, valves, catheters, and ventilation masks.
Grades and Brands
ISO 18064 defines generic classes of commercial TPEs. There are many different manufacturers and brand names, including Teknor Apex Telcar®, Kraiburg HIPEX®, and Dynaflex™ from Avient (formerly PolyOne). Healthcare-grade TPEs are available.
Thermoplastic Polyurethane (TPU)
TPU is a type of TPE that is often called out separately because of its popularity. It has a rubber-like elasticity, and can be used as a replacement for hard rubber because of its higher durometer. Injection-molded TPU also has good load-bearing capabilities and can withstand exposure to ozone.
Properties
Compared to TPE, TPU has superior resistance to extreme temperatures and chemicals. TPUs may be too hard for some injection molded plastic parts, and tend to cost more, in part because drying is required before processing.
Applications
Applications for TPU injection molding include footwear, gaskets, caster wheels, and sporting goods along with cases or enclosures for electronics and medical devices. In medical applications, TPUs are sometimes used instead of polyvinyl chloride (PVC), a plastic that may cause skin irritation.
Grades and Brands
Thermoplastic polyurethanes come in commercial, medical, and industrial grades. There are three main classes of TPU materials: polyester, polyether, and polycaprolactone. Trademarked products are available from manufacturers such as Lanxess, Lubrizol, Texin, and Ultralast.
More Plastic Injection Molding Materials
The plastics discussed in this article are the most common injection molding materials — including specialty plastics and polymer blends — that Fictiv can injection mold for you.
With so many options, it helps to have an expert’s advice before choosing a plastic resin for your project. As part of our injection molding service, Fictiv has design and production experts ready to help you make the right choice, and you get design for manufacturing (DFM) feedback along with your quote.
So, create an account and upload your injection molding designs today!