Time to read: 7 min
Robotic humanoids are becoming increasingly common as critical hardware and software breakthroughs overcome long-standing barriers to creating viable and high-functioning systems. These robots are being increasingly adopted across manufacturing and related sectors to perform tasks traditionally handled by humans.
These humanoid robots are designed to replicate, substitute for, and enhance human capabilities. They are bringing operational flexibility, endurance, cost efficiency, and enhanced safety to manufacturing, medical, warehousing, and other operations.
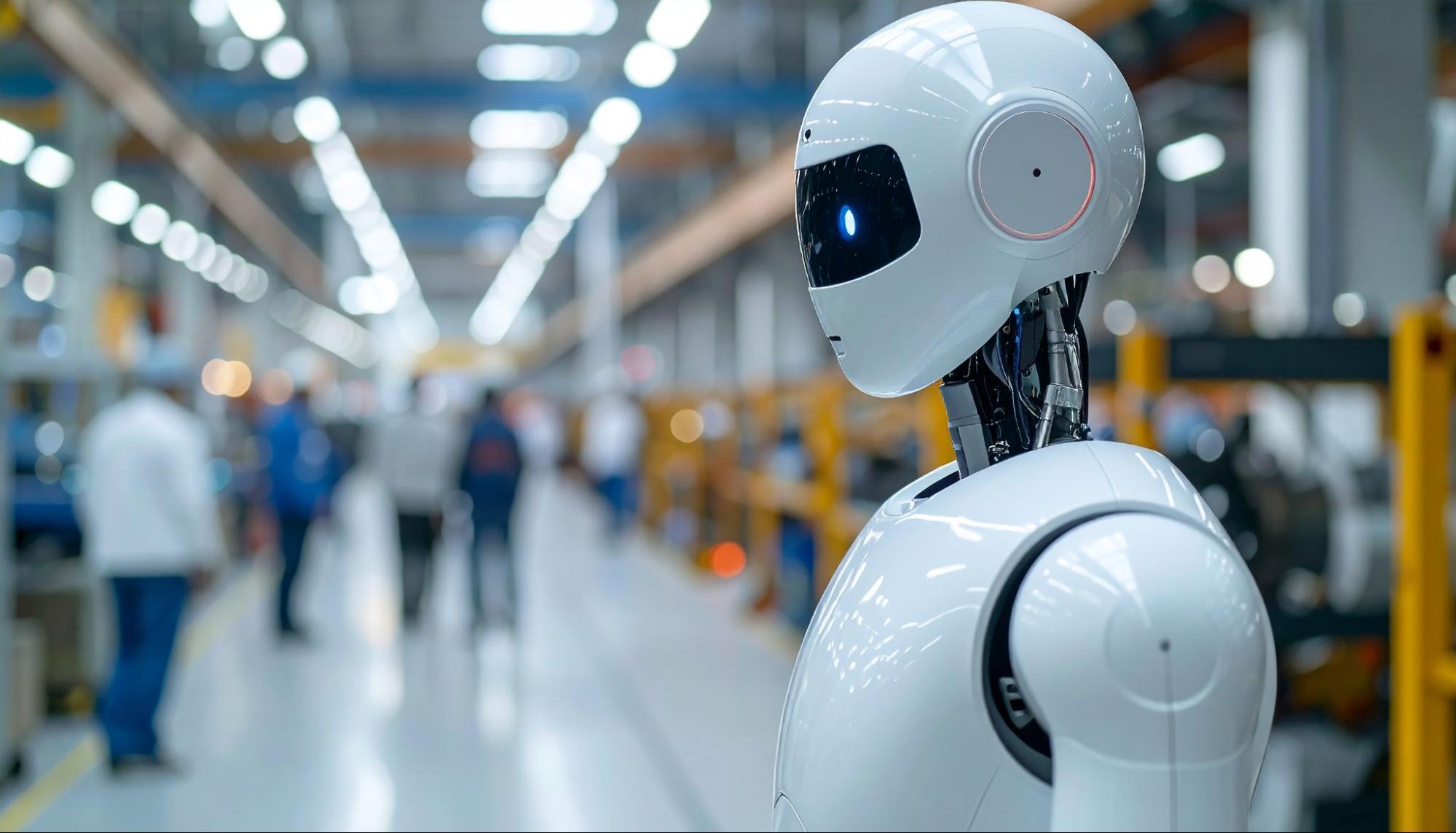
This article will discuss what humanoid robots are, their role, key applications, and the technologies that enable them, as well as the opportunities for robotic component manufacturers.
What Are Humanoid Robots?
Humanoid robots are typically characterized by bipedal legs, multi-jointed arms, adaptive hand-like end-effectors, and compound-sensory inputs, and are designed to operate in human environments. In contrast, traditional automation relies primarily on dedicated, single-purpose machines with limited adaptability.
Humanoid, self-propelled, and highly adaptive platforms offer a new level of versatility. The robotics industry is keen to suggest that these robots are being positioned not as replacements, but as critical reinforcements in areas of high staff turnover, labor scarcity, and higher human risk.
Core Technologies and Capabilities of Humanoid Robots in Manufacturing
The currently near-commercialized embodiments of humanoid robots in manufacturing integrate advanced mechatronics and real-time, layered-sensor fusion. These systems are guided by AI-supervised micro- and macro-motion planning with continuous correction. Key capabilities include:
- Dexterous Manipulation: Multi-articulated arms and end-effectors enable fine motor control for detailed tasks, such as highly accurate pickup, orientation, placement, attachment, and wiring.
- Mobility and Balance: Balanced and agile bipedal locomotion enables movement across human-optimized workspaces, including those with stairs, ladders, and uneven flooring.
- Machine Vision and Multi-Sensory Situational Awareness: Integrated cameras, lidar, and tactile sensors provide data for object recognition, collision avoidance, and effective interaction in complex and often unpredictable environments.
- AI and Machine Learning: Reinforcement learning—informed by balance sensors, vision models, and error correction/recognition—enables adaptive behavior, grasp planning, and navigation in dynamic environments.
These capabilities are enabling the latest generation of humanoid robots in manufacturing to transition between tasks and adapt to disordered human environments, new tools, or fixtures. They can now work safely alongside humans with minimal workspace changes and no personnel risk.
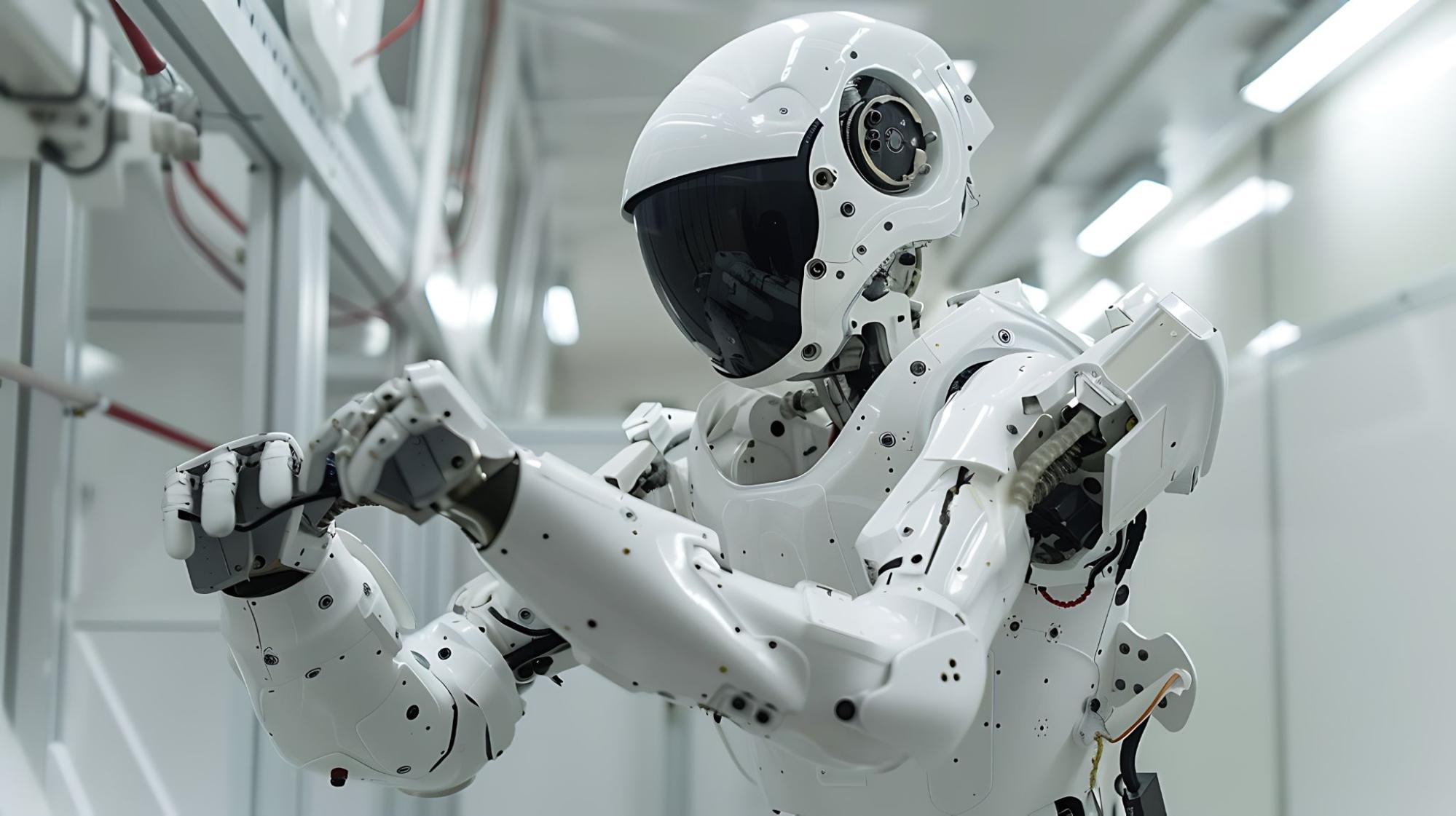
Why Are Manufacturers Exploring Humanoid Robots Now?
Humanoid robots provide functional and commercial advantages that address multiple long-standing challenges faced by manufacturers, including:
Labor Shortages
Labor shortages continuously affect sectors such as logistics, product assembly, and warehousing. These roles are often repetitive, physically demanding, and unappealing to human workers, especially in higher-value economies or among aging populations. By integrating humanoid robots, companies can fill labor gaps and maintain production continuity, solving a range of personnel challenges.
Human Safety Risks
Various tasks and operating environments in manufacturing are inherently hazardous to humans. Repetitive strain injuries, awkward body mechanics, heavy lifting, high temperatures, and chemical or radiation exposures contribute to long-term health issues. Humanoid robots are better suited to such roles, reducing injury rates and improving workplace ergonomics. Their ability to consistently perform precise, repetitive motions without tiredness or distraction also enhances product quality.
Operational Flexibility
Humanoid robots align with existing factory infrastructure. Manufacturing environments are typically human-adapted. Tools, controls, transport paths, and safety systems are all appropriate for the human form.
Unlike traditional industrial robots that require dedicated and isolating operational environments, humanoid robots can operate (and cooperate) using the same tools and within the same spaces as human staff. This compatibility minimizes integration burden and allows for a progressive handover of tasks, as circumstances dictate.
Ease of Reconfigurability
Traditional automation is fixed purpose and expensive (often impossible) to reassign. Due to recent advancements in AI, including large language models (LLMs) like ChatGPT, it will be possible to assign a single humanoid robot a variety of tasks throughout a shift. This allows manufacturers to dynamically reallocate robotic labor as production needs evolve.
Market leaders like Tesla, Agility Robotics, Apptronik, Hyundai, Persona AI, and Figure AI are actively deploying or piloting robotic humanoids in logistics, assembly, and warehousing tasks. These early deployments mark a shift from proof-of-concept demonstrations to partial operational integration in fast, high-value settings. The scope of activities being trialed, from material movement to light assembly, demonstrates confidence in both the functional capability and the economic viability of humanoid robots.
Trials report flexibility in robotic workforce deployment and reduced downtime, where human labor is difficult to source or retain, or simply uneconomical. As performance data accumulates and positive ROI cases become both known and quantified, pilot projects will scale into full deployments across varied industries and operation types. However, this is a rapidly changing industry, the timeline of which is exceedingly difficult to predict. For example, in 2024, Goldman Sachs upgraded its forecast value (from only one year previous) of the humanoid robotics market in 2035 by sixfold to $38 billion.
For more information and statistics regarding trends in the manufacturing industry, read our 2025 State of Manufacturing report.
Opportunities for Robotics Companies and Component Manufacturers
The emergence of humanoid robots both relies on and drives new product development, creating opportunities for robotic humanoid companies and custom part manufacturers. Key areas of opportunity include:
- Actuation Systems: Humanoid robots require compact, high-torque actuators with lightweight housings and complex mounting geometries. Precision-machined enclosures, custom brackets, and linkages are often needed to meet spatial constraints and motion requirements.
- Thermal-Integrated Battery Housings: Modular lithium-ion battery packs demand custom casings that integrate thermal management features such as cooling channels or heat-dissipating structures, often tailored to fit into irregular form factors.
- Sensor Mounting and Enclosure Solutions: Multi-modal sensor arrays (vision, lidar, tactile, inertial) must be integrated into dense, confined spaces. This requires custom mechanical mounts, protective housings, and alignment fixtures—all designed to maintain calibration while withstanding vibration and handling.
- External Structures and Skins: Protective housings, faceplates, and articulated covers must strike a balance between durability, aesthetics, and tactile function. These are often complex, organic geometries that demand custom fabrication methods and iterative prototyping.
Manufacturers with capabilities in custom mechanical design, rapid prototyping, small-batch production, and tight-tolerance machining are in high demand. The ability to iterate quickly and provide a wide range of material options—from lightweight alloys to elastomers—will be critical.
As humanoid systems move from research labs to real-world deployment, the companies that can deliver highly customized, production-ready parts will become essential partners in scaling the next generation of robotics.
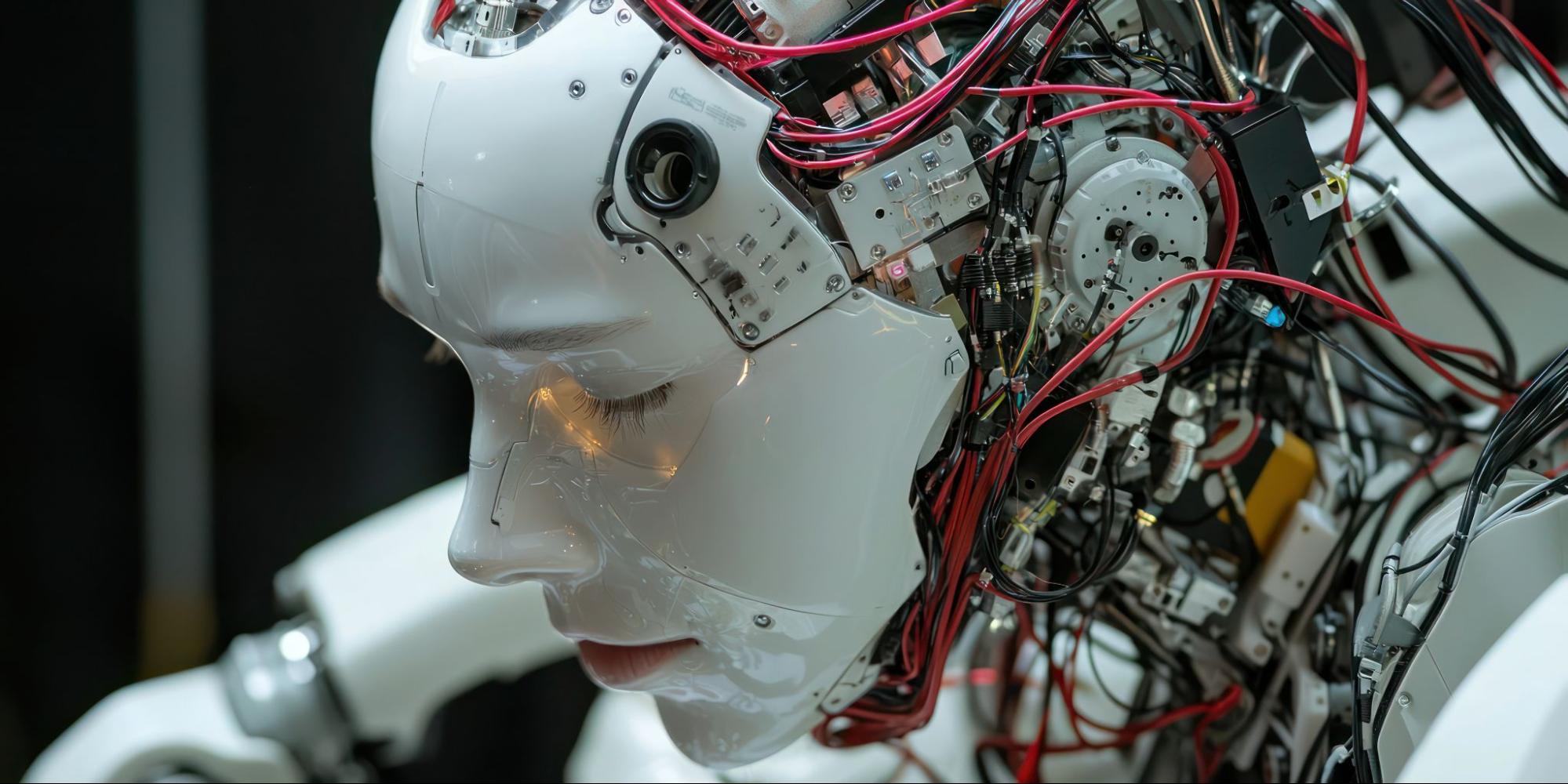
Current Challenges and Limitations in Manufacturing for Humanoid Robotics
Despite the promise, integrating humanoid robots into manufacturing comes with significant challenges:
- Cost: Current humanoid robotic devices range from $80,000 to over $300,000 per unit, without considering integration costs.
- Speed and Strength Limitations: Most humanoids move more slowly and lift less than dedicated and fixed industrial automation.
- Safety: Although collaborative by design intent, ensuring safe interactions with human workers in fast-paced settings requires extensive testing before it can be implicitly assumed.
- Battery Life and Thermal Management: Powering multiple actuators and sensor/control systems is energy-intensive. Runtime per charge is typically under eight hours and can be considerably shorter in high-demand operations.
Preparing for the Future of Human-Robot Collaboration in Manufacturing
The path to optimized automation integration begins with a methodical evaluation of the current state of operations. Manufacturers should start by conducting a thorough audit of their existing infrastructure, examining manufacturing lines, micro and macro logistics routes, and service processes. The aim is to identify repetitive, physically demanding, or ergonomically hazardous jobs that are not only difficult to staff but also present long-term health risks for human workers. These are ideal tasks for adaptive humanoid automation in manufacturing.
The audit ideally seeks operations already built around human scale and capability. Workstations that utilize multiple hand tools in various orientations, operate in tight storage environments with narrow aisles and disorganized small-item bin contents, or feature layouts designed around standard human reach can often be made more robot-compatible without extensive redesign. Hybrid workflows, in which robots (cobots) assist rather than replace human labor, should also be considered in the mapping. These insights will feed into a phased deployment road map, allowing companies to introduce automation in this class gradually and strategically.
Equally important is exploratory engagement with robotics OEMs (original equipment manufacturers) and integrators. Partnering at the conceptual stage allows the (knowledgeable) supply chain to help in defining the development of installations that draw on a wider range of real-world use cases. Sharing process data, developing deployment plans, and revising system features and software capabilities will reduce the time to bring robots into commercial operations. Close cooperation with the supply chain will ease the initial friction of robot placement in work settings. That same cooperation will also enable faster and smoother downstream revisions and reimplementations, maintaining a dynamic workflow in system operation and maintenance.
To improve automation readiness in the workplace, organizations should proactively apply adaptable and robot-friendly design principles, adopt modular tooling and standardized fixtures, and design accessible environments. Using digital twins and simulations enables the virtual testing of robotic workflows at the specification stage, as well as in later revisions and reapplications. A “design for robotic manufacturing” approach to new products and services, along with their operational and manufacturing environments, will ensure the implementation of flexible automation is resilient, scalable, and future-ready.
It is critically important that the human workforce be empowered to adapt to this new paradigm and drive adaptations in the usage model of the tools as the applications evolve and bed in. Staff of all levels (and the AIs they interact with) must be equipped for safe and productive interaction and to mutually assist in optimization. Investing in human capital ensures smoother adoption and long-term operational resilience.
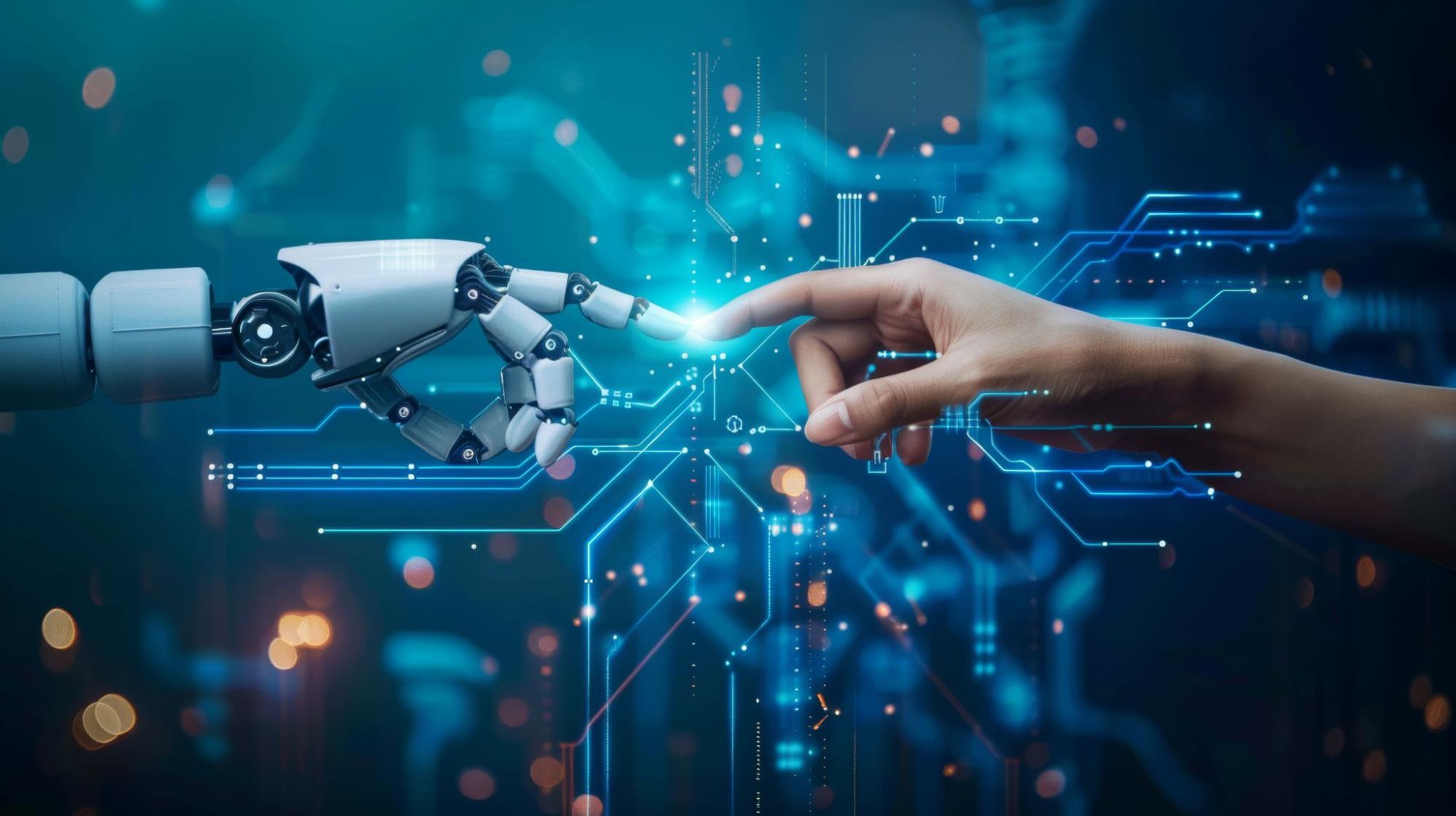
Enabling the Next Generation of Manufacturing with Digital Platforms
Humanoid robots represent an inevitable next step in industrial automation and Industry 4.0. By combining near-human dexterity with machine precision and endurance, they are consciously being designed to operate in environments built for people. Their tentative integration into manufacturing and related environments is already accelerating innovation, reducing downtime, and unlocking new levels of productivity.
To support this next wave of automation, manufacturers need agile, responsive partners. Fictiv offers end-to-end custom manufacturing services including CNC machining, 3D printing, injection molding, and sheet metal fabrication. Our rapid prototyping and production capabilities empower robotics innovators to move from concept to deployment faster than ever.
Ready to bring your design to life? Get an instant quote today.