Time to read: 7 min
Bringing a hardware product to life is no small feat, and choosing the right manufacturing model to get you there is one of the most critical decisions. Whether you’re a startup launching your first prototype or an enterprise scaling production globally, how you approach product design and manufacturing directly impacts your speed to market, production costs, and ability to protect your intellectual property.
Three of the most popular manufacturing models are: OEM (Original Equipment Manufacturer), ODM (Original Design Manufacturer), and JDM (Joint Design Manufacturer). Each model offers distinct advantages depending on your business goals, technical resources, and how much control you want over product design and IP.
This article explains:
- OEM, ODM, and JDM key differences
- Pros and cons of each model
- Comparison of design ownership, IP control, customization, and time to market
- How to choose a manufacturing model
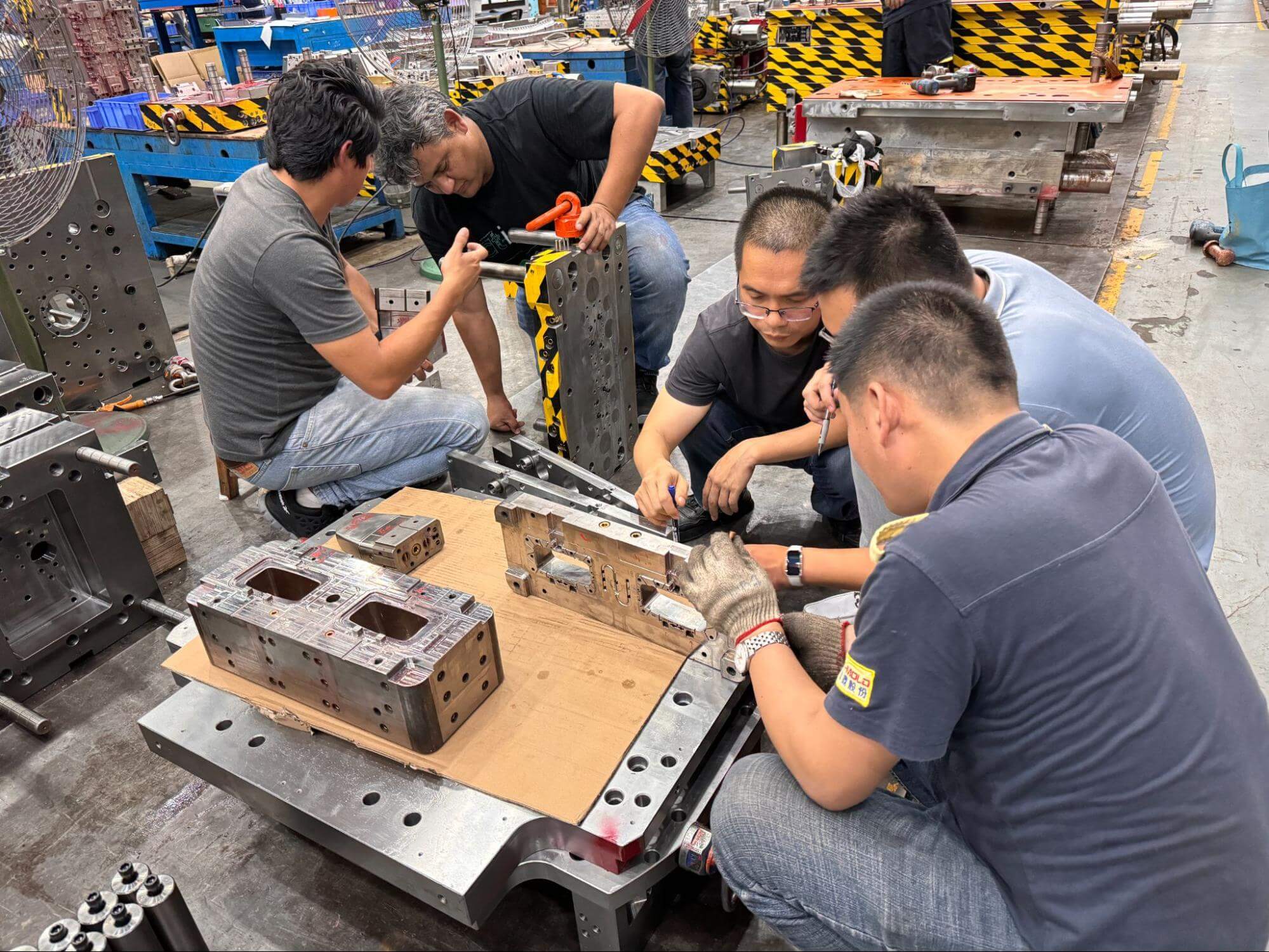
What Is OEM (Original Equipment Manufacturer)?
In an OEM arrangement, the brand owner maintains complete control over the product’s design and intellectual property, while the manufacturing partner is responsible for executing production. The OEM builds the product strictly according to the brand’s technical specifications, with minimal input into design or functionality.
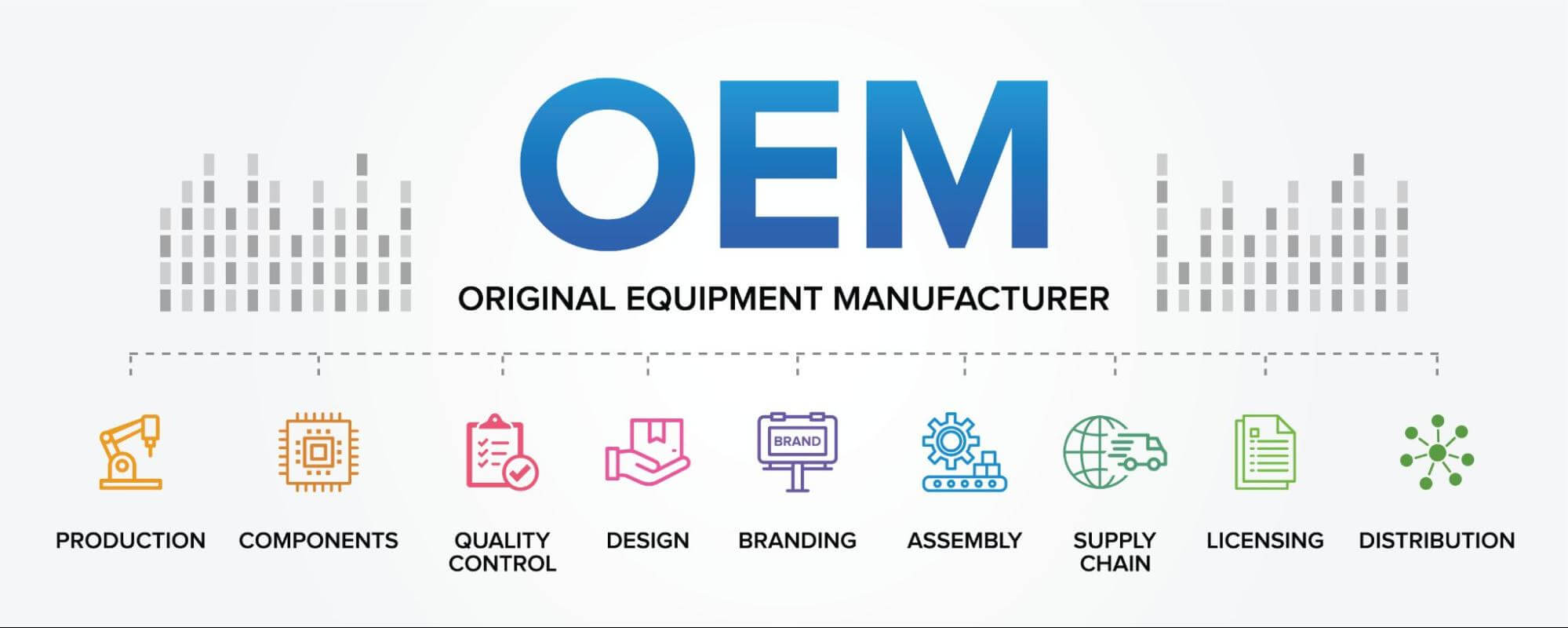
Once complete, the finished product is branded and sold by the outsourcing company, which also handles distribution, marketing, and post-sales support. An example of an OEM relationship is a company that owns the design of a product, but has it manufactured by another company (the OEM). For example, Apple outsources the manufacturing of a product to Foxconn, and the product is made exactly according to Apple’s design specifications. Importantly, Apple owns all rights to the design.
This model is ideal for businesses that want to retain full ownership of their product IP and differentiate their products from those of competitors through custom design. It’s commonly used by established companies with strong in-house design teams but limited manufacturing capacity. OEM partnerships help these businesses avoid the capital expense and complexity of setting up manufacturing operations. This makes it easier to scale production and enter new markets.
Pros and Cons of OEM
Pros | Cons |
Full control over product design and IP | Higher upfront costs: NRE (Non-Recurring Engineering; the one-time costs incurred by R&D) and the design process (including testing) of a new product |
Ability to switch to a different manufacturer in the future | Longer ramp-up time (technical alignment on design, process, and quality) |
Strong brand identity | More risk ownership (associated with the investment in R&D and design resources) |
Table 1: Pros and cons of OEM
What Is ODM (Original Design Manufacturer)?
The ODM model goes a step further by offloading manufacturing and much of the design work. In this setup, the outsourcing company provides general requirements, and the ODM is responsible for both product design and production. The final product is typically branded by the outsourcing company—a process often called white labeling (e.g., white-label consumer electronics).
For companies looking to reduce product development costs and speed up time to market, this is a strong option. The ODM brings its own engineering resources, economies of scale, a greatly streamlined supply chain, and advanced production techniques, which can be especially beneficial for startups or businesses with limited technical bandwidth.
However, there are trade-offs. ODMs typically retain ownership of the design and any associated IP. They may also offer the same base product to multiple customers—even your competitors. Flexibility is also limited—customization, minimum order quantities, and regional support may vary. That makes ODMs great for standard products, but less ideal if differentiation and IP control are key to your business.
Pros and Cons of ODM
Pros | Cons |
Faster time to market | Minimal control over design (often) |
Lower R&D and tooling costs | Limited differentiation from competitors |
Simplifies your supply chain | IP and licensing rights are usually retained by the ODM |
Table 2: Pros and cons of ODM
What Is JDM (Joint Design Manufacturer)?
JDM is a collaborative model that merges the strengths of both OEM and ODM approaches. In this setup, the outsourcing company and the manufacturer cooperate closely on many or all aspects of the design and manufacture of the product. This shared approach allows companies to retain control over critical design elements while benefiting from the technical capabilities and manufacturing efficiency of their partner.
JDM is especially valuable for businesses that lack in-house expertise in specific areas or need to accelerate product development without building everything from scratch. However, with shared responsibilities comes the need for clear communication—especially around IP. From the outset, both parties must align on IP ownership, licensing rights, and how co-developed assets will be managed. When managed effectively, the JDM model offers a good midway between OEM and ODM, with the flexibility to innovate while still maintaining strategic control. A good example of JDM would be startups co-developing robotics or IoT devices with manufacturing partners.
Pros and Cons of JDM
Pros | Cons |
Shared expertise | Requires strong communication and aligned incentives |
Faster development | Potential complexity in IP ownership if not defined early |
Lower risk than full OEM | May be expensive in the long run (e.g., revenue-sharing agreements) |
Table 3: Pros and cons of JDM
Comparison: OEM vs. ODM vs. JDM
Now let’s consider how these models measure up against one another. Table 4 compares the three models based on the typical features that companies might look for:
Feature | OEM | ODM | JDM |
Design Ownership | Brand | Manufacturer | Shared |
Customization Level | High | Low to medium | Medium to high |
Time to Market | Slower | Faster | Moderate |
Cost Efficiency | Moderate (brands save on manufacturing at scale but may invest more in design) | High (brands can limit design & development expenses) | Moderate (higher upfront development costs that can pay off in the long run) |
Ideal Company Type | Mature companies | Low-risk launches and startups | Startups/collaborative development |
IP Control | Full | Limited | Negotiable/Shared |
Table 4: Comparison of JDM vs. ODM vs. OEM
When to Use Each Model
Choosing the best option for you and your company all depends on the type of company, the company size, how established your company is, your IP and customization needs, and technical resources. Let’s take a look at what model is better suited for which scenarios.
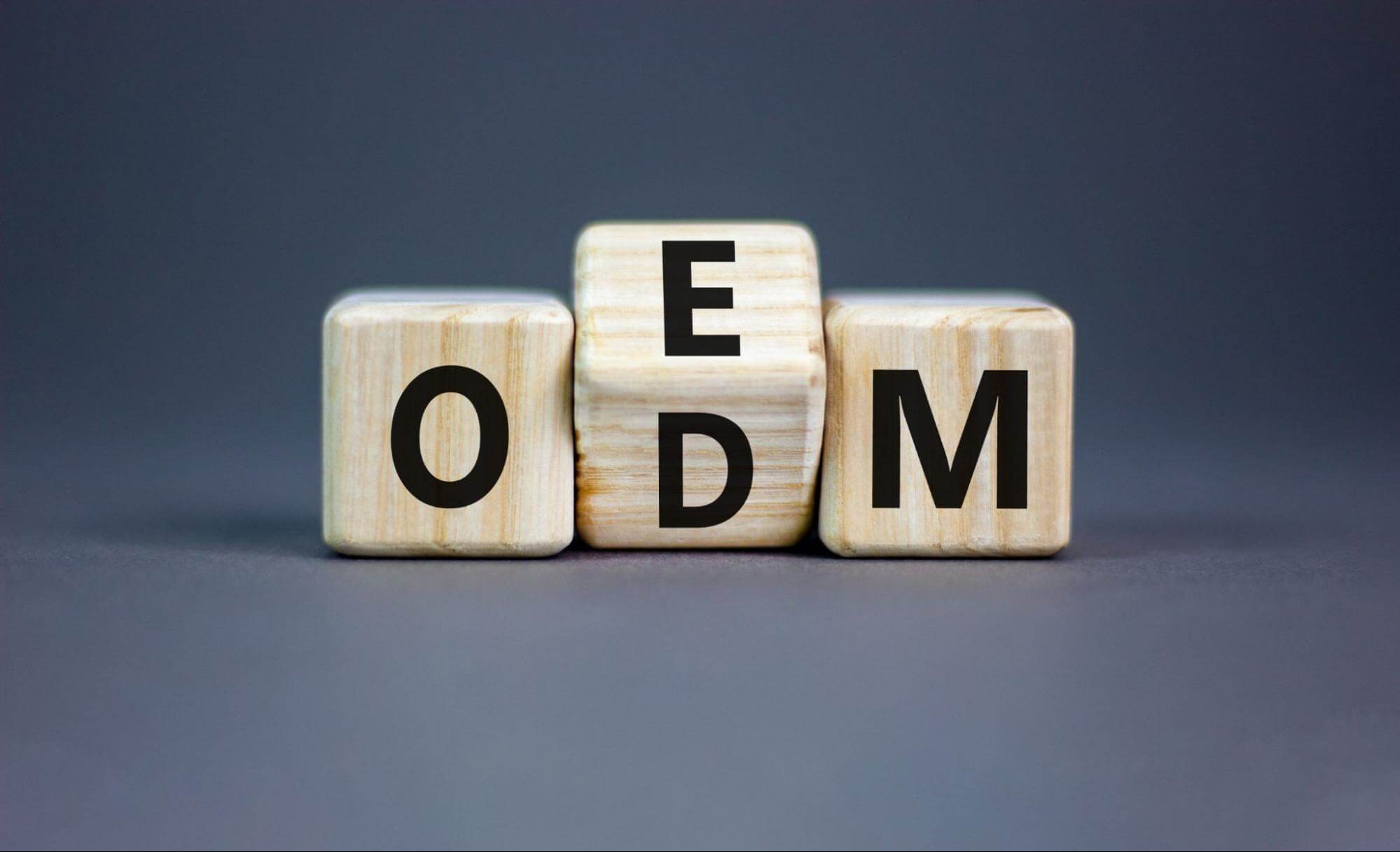
When to Use OEM
The OEM model is best suited for companies with established engineering teams, proprietary designs, and a strong focus on IP control. These enterprises typically want to offload the burden of manufacturing while retaining full control over product design, performance, and branding.
Choose an OEM if your company:
- Has in-house engineering and proprietary product designs
- Wants complete control over IP and branding
- Can manage the complexity of product development
- Is willing to invest in a longer and costlier manufacturing process for higher product differentiation
When to Use ODM
The ODM model is a strong choice for startups and small- to mid-sized companies looking to minimize development costs and time to market. It allows enterprises to leverage the ODM’s design expertise and infrastructure, reducing the need for internal engineering and R&D. While the outsourcing company may lose control over the product’s underlying IP, partnerships enable quicker entry into competitive markets with standardized or lightly customized products. This approach works well when product uniqueness isn’t the core value proposition.
An ODM is ideal if your company:
- Prioritizes faster time-to-market and lower development costs
- Doesn’t require full IP ownership or highly customized products
- Prefers leveraging existing designs and manufacturing resources
- Is entering new markets or scaling quickly with a limited technical staff
When to Use JDM
JDM strikes a balance between the OEM and ODM models. It is ideal for companies with partial in-house development capabilities but limited resources or gaps in specific technologies. In this model, responsibilities for design and manufacturing are shared. It’s particularly beneficial for scaling complex systems or when co-innovation is needed.
A JDM partnership works well when your company:
- Has some internal R&D capability but lacks resources for full-scale production
- Wants to collaborate on design while outsourcing manufacturing
- Needs flexibility for co-development of complex systems or components
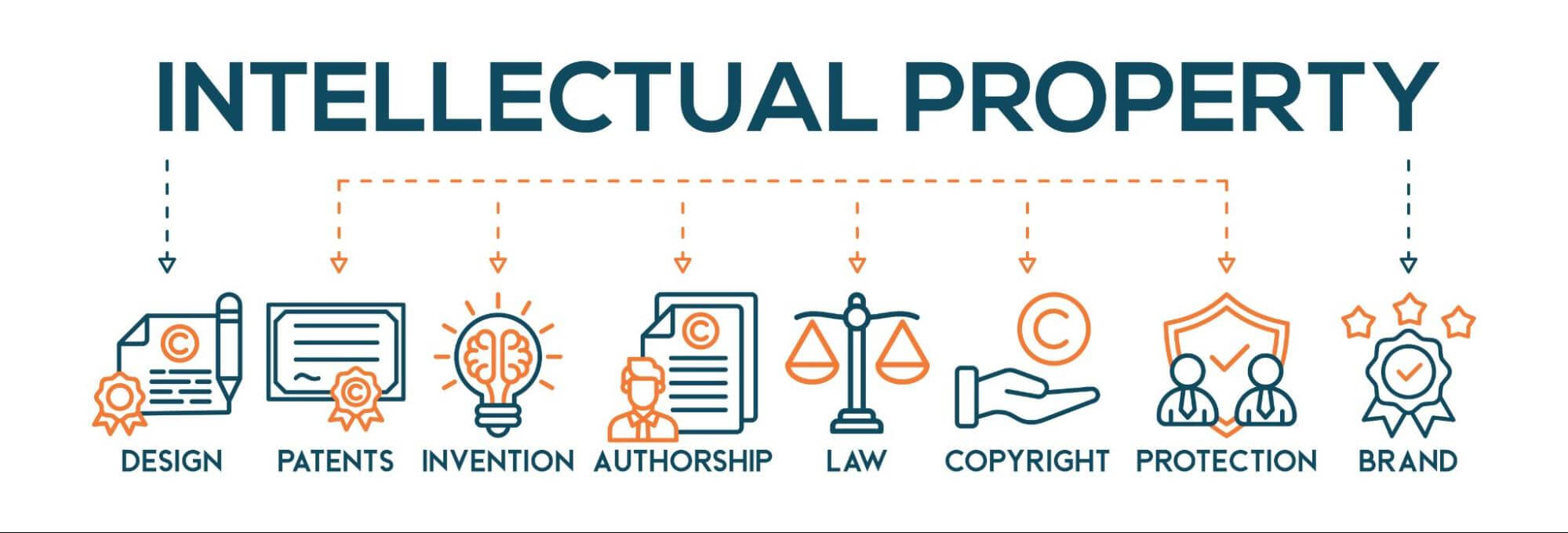
Benefits of Digital Manufacturing in JDM, ODM, and OEM Models
No matter which manufacturing model you choose (OEM, ODM, or JDM), success depends on how quickly and efficiently you can move from idea to execution. That’s where digital manufacturing platforms come in. By bridging the gap between design, engineering, and production, digital manufacturing adds a layer of agility, visibility, and control that traditional methods often lack.
Here’s how an effective digital platform will enhance each model:
Accelerated Prototyping
OEM and JDM strategies often require rapid iteration on custom designs. On-demand manufacturing streamlines the prototyping process—allowing teams to test, validate, and refine products rapidly.
Improved Supply Chain Transparency
When outsourcing manufacturing or design responsibilities, communication and transparency are key. Real-time production tracking and centralized communications reduce uncertainty and build trust in complex global supply chains.
Risk Mitigation Through DFX and Early Validation
Design for manufacturability (DFM) and other DFX principles are critical in all three models. A powerful digital platform helps identify manufacturability issues early, reducing rework and delays down the line.
Seamless Collaboration Across Teams and Time Zones
Whether you’re co-developing with a JDM partner or managing multiple suppliers in an ODM scenario, digital tools support version control, design reviews, and centralized documentation.
Support Across All Models
An ideal digital manufacturing platform is designed to support OEM control, ODM speed, and JDM collaboration. This gives businesses the flexibility to scale and shift as their needs evolve.
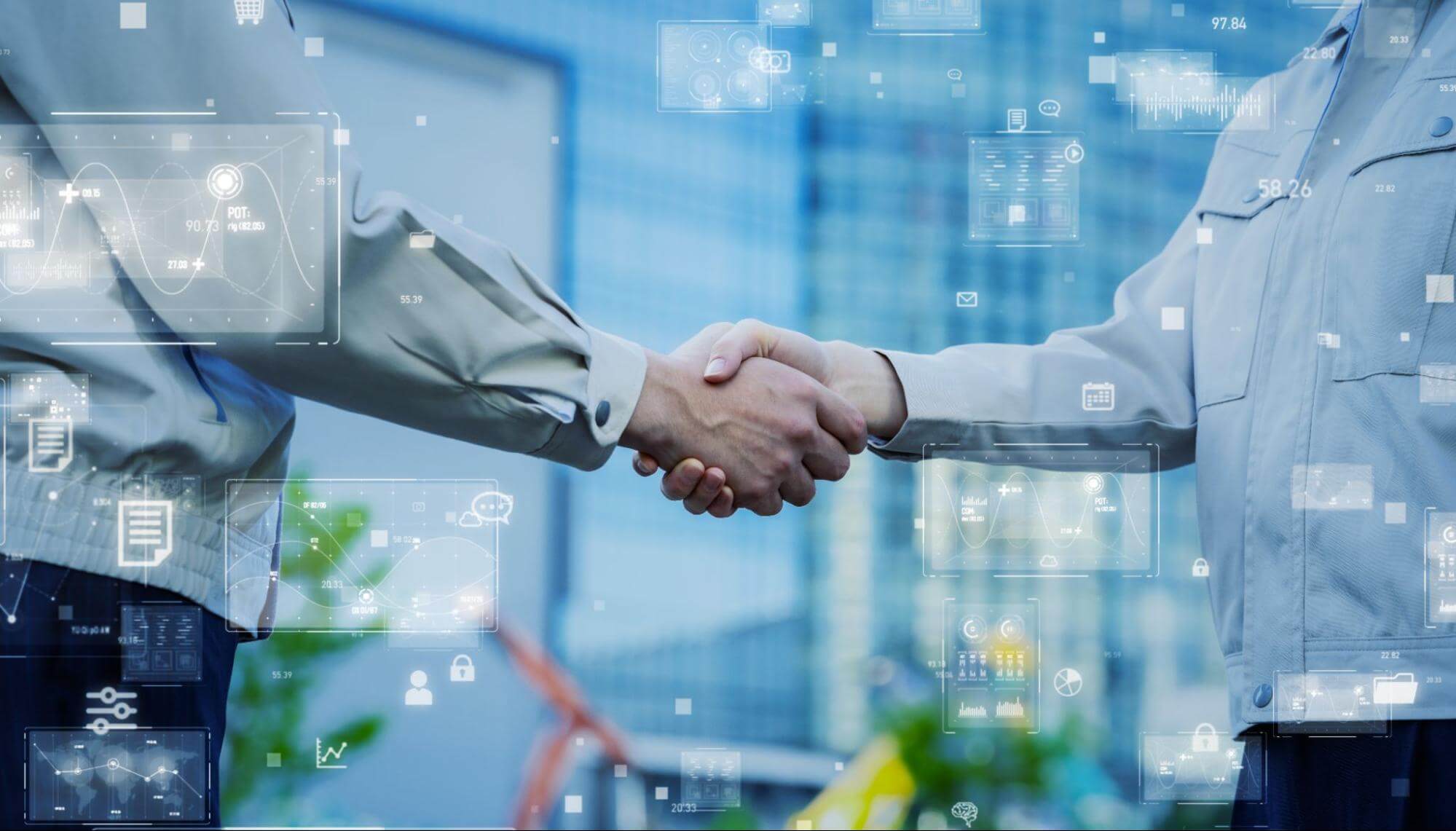
Choosing the Right Model—Backed by the Right Partner
Selecting between OEM, ODM, and JDM models comes down to your product goals, available resources, and the level of control you need over design and intellectual property.
- OEM is ideal for teams that need full control over design and IP—and have the in-house capability to develop from the ground up.
- ODM is useful when speed and cost matter most, and product differentiation is less critical.
- JDM strikes a balance—allowing for customization while sharing design responsibility with a partner.
But whatever model fits your needs, one thing remains true: You’ll still need a flexible, scalable way to prototype, iterate, and manufacture—especially as you move from concept to production.
That’s where Fictiv comes in. We’re your on-demand manufacturing partner, helping you speed up and de-risk your development with:
- Instant DFM feedback and quoting
- Rapid prototyping and production-grade parts
- Global supply chain infrastructure with full transparency and control
Stay in control of your IP, your strategy, and your timeline—while we streamline the rest.
Get started with an instant quote and see how Fictiv can help you bring your product to market—faster, smarter, and on your terms.