Time to read: 10 min
There have been countless times when I’ve been putting something together and wondered, “Why was this designed this way?” If you’ve ever assembled your own prototypes or even furniture, you probably know what I mean. The best way to design for assembly is often to put prototypes together yourself throughout the process, but it helps to consider assembly from the start.
Inefficient design decisions made early in the process can lead to costly manufacturing, supply chain issues, and delayed product launches. These challenges underscore the crucial need for strategies that consider downstream production realities from the outset.
Design for Manufacturing and Assembly (DFMA) addresses inefficient design decisions by emphasizing manufacturing and assembly considerations in the earliest phases of product design. DFMA guides engineers to simplify part structures, reduce component count, and optimize for efficient and scalable production.
DFMA encompasses the features of two design methodologies: Design for Manufacturability (DFM), which focuses on simplifying the fabrication of individual parts, and Design for Assembly (DFA), which emphasizes ease and efficiency of part assembly. This integrated approach offered by DFMA best practices not only improves product reliability but also accelerates time-to-market and reduces total lifecycle costs.
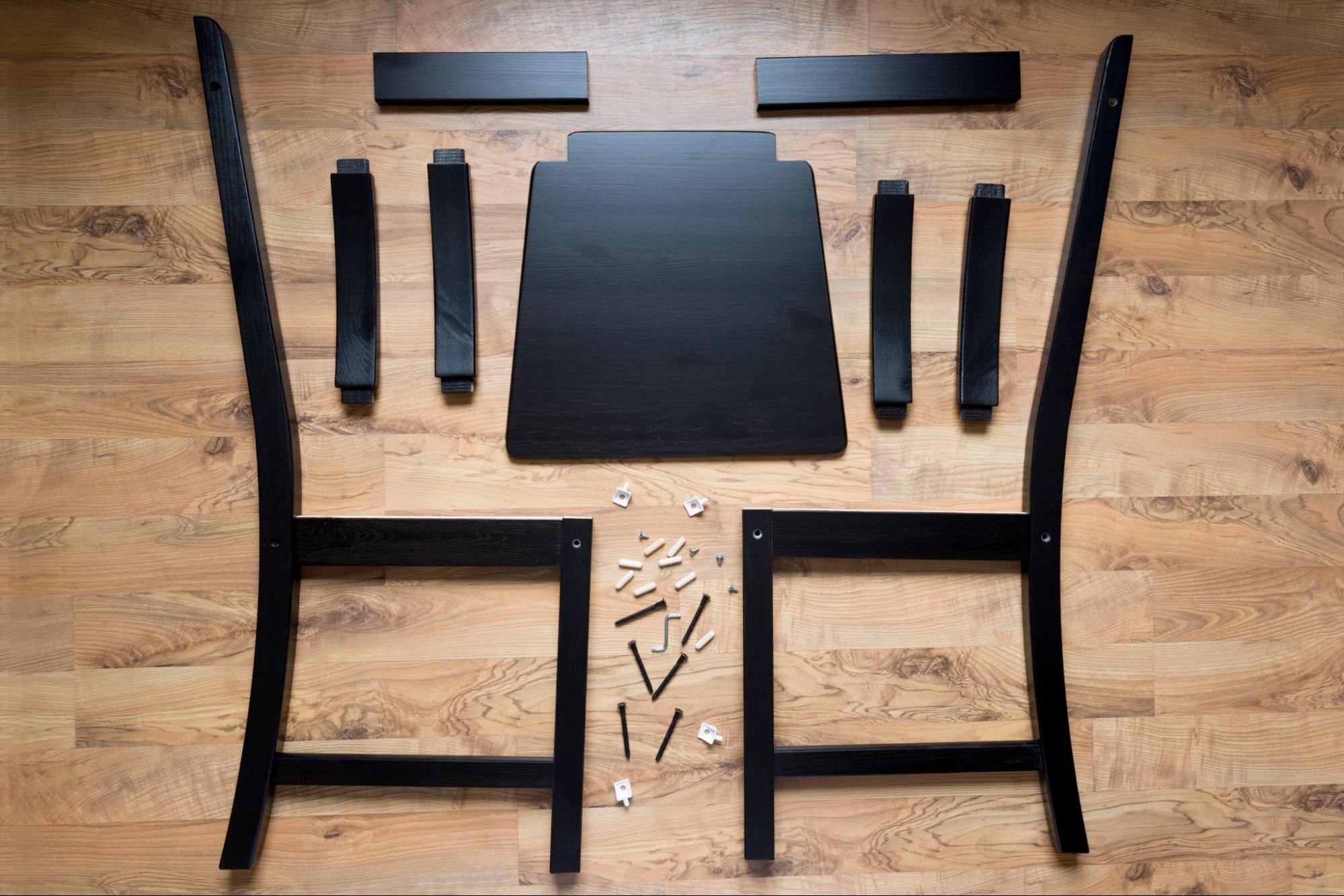
What is DFMA (Design for Manufacturing and Assembly)?
DFMA is a product design approach that simplifies manufacturing and assembly processes. It aims to reduce production costs, minimize component counts, and improve product quality by integrating key manufacturing considerations early in the design phase.
Originating in the 1980s, DFMA was developed by Geoffrey Boothroyd and Peter Dewhurst, who recognized the inefficiencies in conventional product design. Their goal was to shift the focus from downstream problem-solving to upstream design optimization. Since then, DFMA has evolved into a critical practice in various industries, including automotive, aerospace, electronics, and consumer products.
At its core, DFMA aims to:
- Reduce the number of parts in a product
- Simplify manufacturing and assembly operations
- Increase consistency and quality
- Minimize production time and costs
- Enable more sustainable and scalable designs
Printed circuit boards (PCB), seen in the figure below, are one of many products that are regularly developed with DFMA practices in mind.
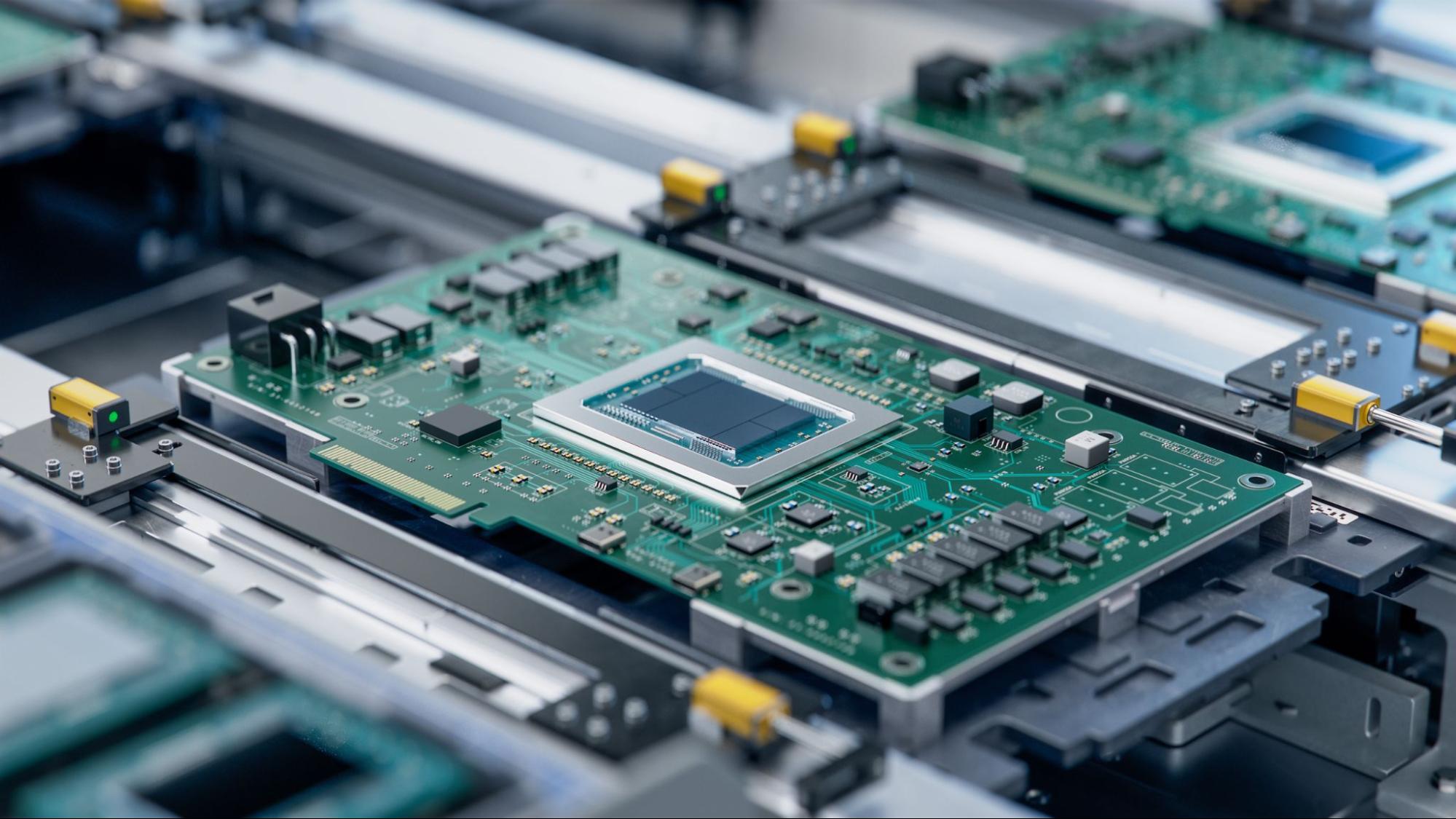
The Difference Between DFM and DFA
Design for Manufacturability (DFM) is the process of designing products in a way that simplifies manufacturing operations. It involves selecting materials for products that are cost-effective, easy to manufacture, and readily available; designing with tolerances suitable for production processes; and minimizing machining complexity.
Meanwhile, Design for Assembly (DFA) focuses on how easily parts can be assembled. It encourages the use of fewer parts, easy alignment, and modular designs that reduce the time and effort required for assembly.
DFMA combines both DFM and DFA, offering a comprehensive strategy that enhances both manufacturability and ease of assembly. This integration leads to designs that are efficient, cost-effective, and production-ready.
DFM vs. DFA vs. DFMA
Feature | DFM | DFA | DFMA |
Focus | Manufacturing processes | Assembly processes | Both manufacturing and assembly |
Goal | Simplify fabrication | Simplify joining parts | Optimize entire production life cycle |
Metrics | Machining time/complexity, material waste | Assembly time, part count | Total cost, time-to-market, quality |
Application Stage | Design for process capability | Design for ease of assembly | Holistic design from the concept stage |
Key Principles of DFMA
Effective DFMA implementation is built on a foundation of key design principles:
- Minimize the Total Number of Parts: Additional parts in an assembly or product can add complexity and cost. By reducing part count, designers simplify both manufacturing and assembly, which reduces manufacturing risks and streamlines logistics.
- Design Multifunctional Parts: Instead of using multiple components to achieve different functions, designers can integrate multiple functions into a single part when feasible.
- Use Standard Components: Utilizing off-the-shelf (OTS) parts reduces the need for custom tooling and simplifies procurement. This leads to both cost savings and reduced lead times.
- Optimize for Ease of Assembly: Parts should be self-locating and self-fixturing where possible. These features reduce assembly time and lower the risk of human error.
- Design for Automated Assembly: If automation is part of the production strategy, parts and assemblies should be compatible with robotic handling and positioning.
- Design for Error-Proofing: Design techniques such as poka-yoke (Japanese for “mistake-proofing”) ensure that parts can only be assembled in the correct orientation.
An example of these principles in practice comes from Fictiv’s “Keep the Assembly Line Happy” approach, which stresses the importance of intuitive part orientation, clear assembly sequences, and minimizing fasteners to reduce human labor/error and assembly time.
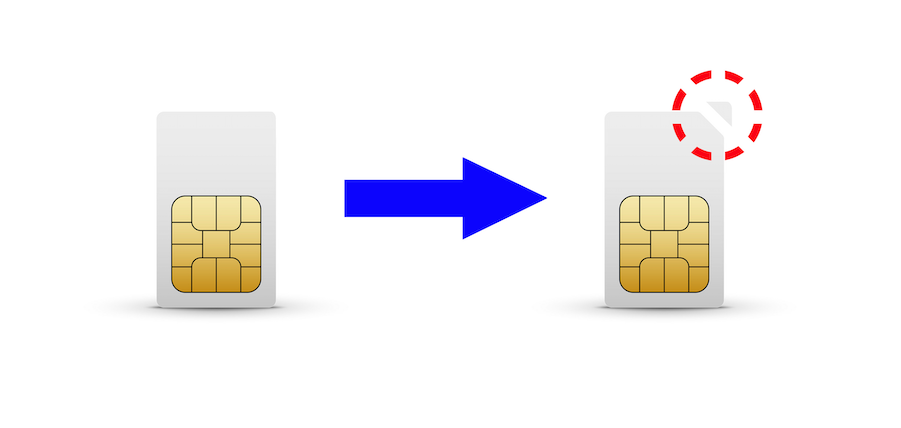
Why DFMA Matters: Business and Engineering Benefits
The adoption of DFMA offers a wide array of benefits for both businesses and engineering teams:
Reduced Manufacturing and Assembly Costs
DFMA streamlines design complexity and eliminates unnecessary features, each of which contributes to lowering material usage, tooling expenses, and labor costs. Fewer parts also translate into fewer fasteners, less need for jigs, and reduced part handling.
Faster Production and Time-to-Market
With fewer parts and simplified geometries, manufacturing and assembly steps become faster and easier to execute. This directly contributes to accelerated product launches and improved responsiveness to market trends.
Improved Product Reliability and Quality
Having fewer components reduces the potential for defects and variation. As a result, assembly becomes more consistent, which leads to fewer defects, recalls, and customer complaints.
Easier Sourcing and Fewer Supply Chain Issues
Standard components and simplified BOMs (Bills of Materials) make sourcing easier and less prone to supply chain disruption. This refers to commonly available items, such as screws, pins, clips, springs, and wheels, but also encompasses more complex components. Why design your own microcontroller, motor, or sensor if someone else can supply you with a suitable one at an acceptable price?
Reduced Rework, Scrap, and Labor Overhead
Early design simplification helps prevent costly fixes during production and final assembly. This directly translates into savings from reduced scrap rates and lower labor costs associated with material handling.
When to Apply DFMA in Product Development
To fully benefit from DFMA, it should be integrated as early as possible in the product development process. The different stages of the product development process, as well as various industries that benefit from DFMA, are described below.
- Early-Stage Concept: During initial design phases, DFMA principles guide foundational decisions that influence the entire development life cycle.
- During Prototyping and Validation: Applying DFMA helps refine concepts into feasible, scalable designs that can be validated with physical or virtual prototypes using finite element analysis software and computer-aided manufacturing software.
- At Design Freeze Before Production Ramp: Before finalizing a design for mass production, DFMA checks elements like: verifying runner design in plastic injection molds; or that form and fit of assembled parts ensure manufacturability and assemblability are fully addressed.
- In High-Regulation or Tooling-Intensive Industries: Industries like aerospace, automotive, and medical devices, where changes are costly and timelines are tight, benefit immensely from DFMA-driven designs.
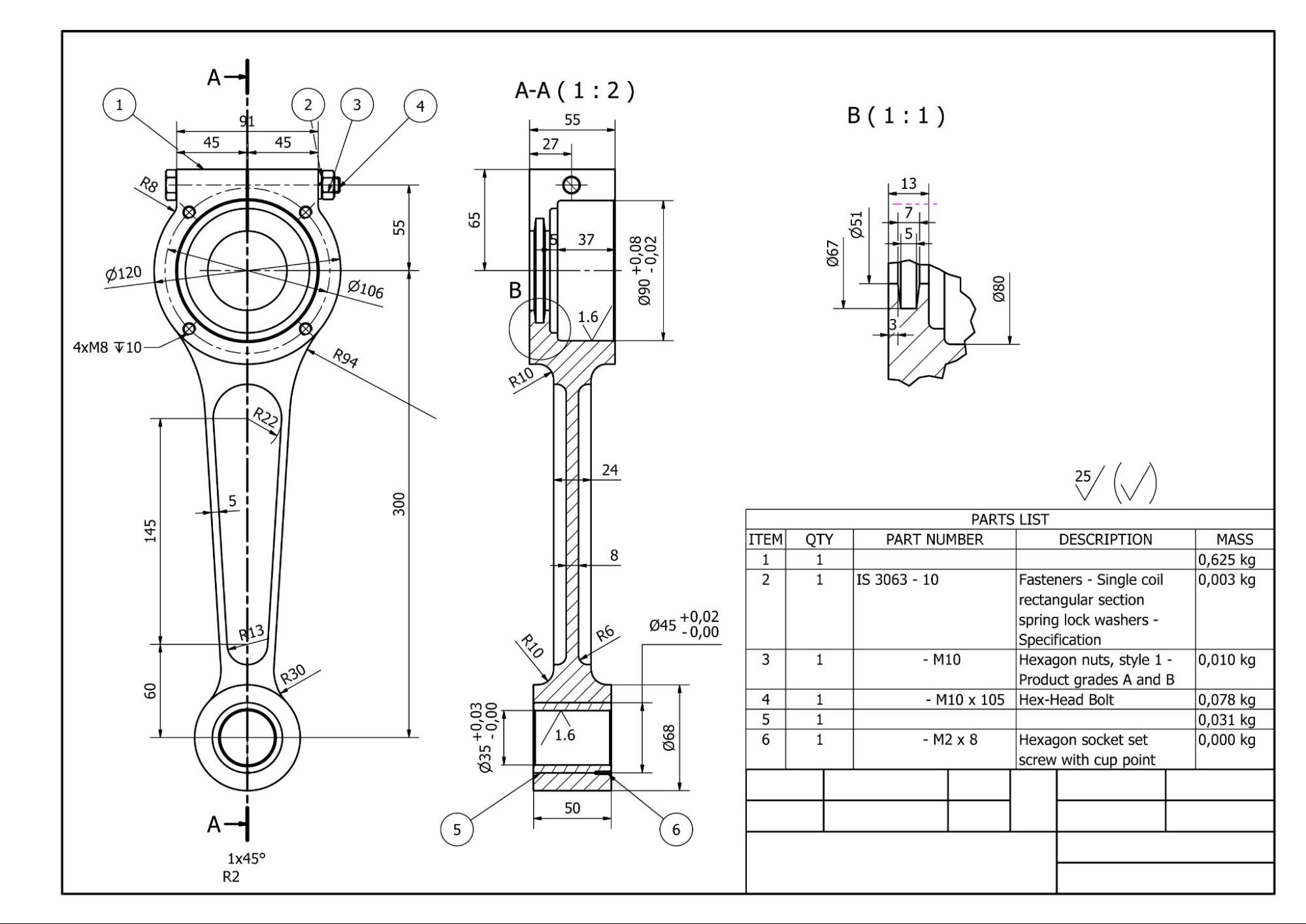
DFMA Guidelines for Common Manufacturing Processes
Collaborating closely with manufacturing engineers helps ensure that a product design aligns with process capabilities. This collaboration is key to eliminating costly redesigns and production delays. Each manufacturing process, from CNC machining and sheet metal fabrication to injection molding and 3D printing, has unique considerations that DFMA must address.
CNC Machining
To harness the benefits of DFMA in CNC machined products, avoid deep cavities that require long, fragile tools. Minimize tool changes by designing features that can be machined with fewer operations. Furthermore, use consistent wall thickness to maintain product strength and to reduce cycle time. Limit setups and minimize tool changes to increase throughput.
Injection Molding
When it comes to DFMA in injection molding, maintain uniform wall thickness to avoid warping and sink marks, include draft angles for easy part ejection from the mold, and avoid undercuts unless necessary for product function or assembly. Additionally, use ribs or gussets to maintain structural integrity.
Sheet Metal Fabrication
DFMA in sheet metal fabrication calls for maintaining a minimum bend radius to prevent cracking. Keep holes away from bends to maintain structural integrity and simplify tooling. Optimize flat patterns to minimize material waste and improve nesting efficiency.
3D Printing
The benefits of DFMA in 3D printing come from combining parts into a single print when feasible to avoid assembly. If it is not possible to avoid assembly, ensure that part orientation supports both strength and surface quality. Use self-fixturing features to streamline post-processing. Avoid unsupported overhangs and orient parts to minimize support material.
Resources like “How to Design Assemblies to Be Self-Locating and Self-Fixturing” provide deep insight into best practices for assembled parts.
Common DFMA Mistakes and How to Avoid Them
While DFMA offers numerous benefits, common pitfalls can undermine its effectiveness. Avoiding these pitfalls requires a conscious effort to balance design innovation with practicality.
Overcomplicating Part Interfaces
While designing intricate part interfaces may look visually appealing in some cases, it often complicates tooling and alignment. This can be counterintuitive to DFMA as it can make part manufacture and assembly more difficult due to higher tooling costs and tolerance issues. Instead, design parts that assemble easily through snap-fits, guides, and visual markings.
Ignoring Assembly Access and Tooling
Designs sometimes overlook how tools or operators will interact with the part. Disregarding product assembly methods can make production and maintenance of the product during its life cycle difficult. For DFMA, parts should be designed with sufficient clearance for tools and hands to reach during assembly.
Failing to Collaborate With Manufacturers
Designers may assume feasibility without confirming with suppliers. This leads to parts that are difficult or expensive to make. Engage with fabricators early to validate assumptions.
Not Accounting for Tolerance Stack-Up
Misaligned tolerances across assemblies can lead to fit issues and functional failures. Consider tolerance stack-up when designing assemblies with multiple components, and use software tools and tolerance stack-up calculators to model outcomes.
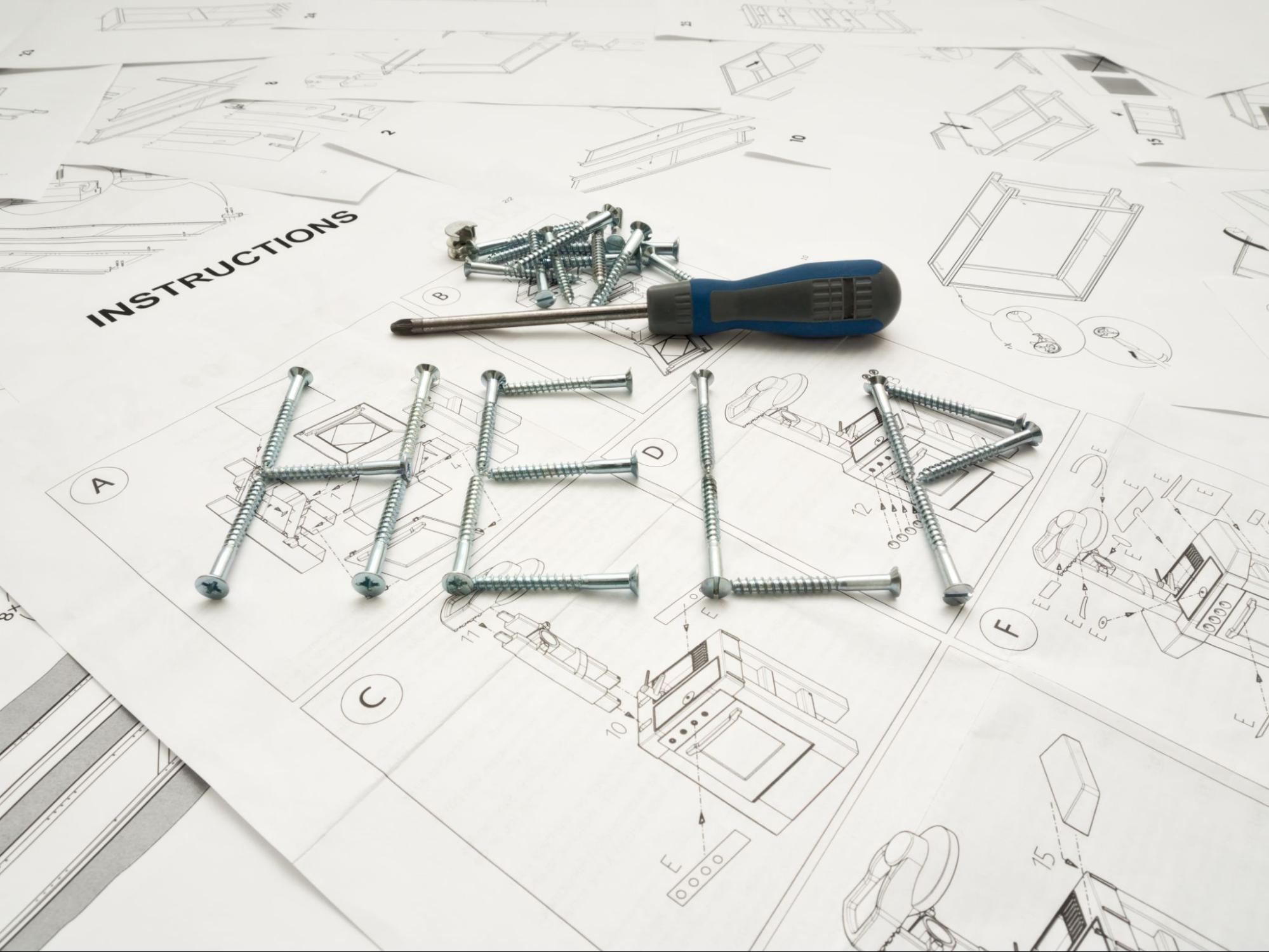
Real-World Examples of DFMA in Engineering Practice
Two prominent manufacturing companies in different industries, Logitech and John Deere, leveraged the DFMA methodologies to improve the efficiency of their product design and manufacturing processes.
Case 1: Logitech’s Electronics Enclosure Redesign
Logitech applied DFMA principles in the redesign of one of their wireless mouse products. By integrating multiple PCB supports into a single molded housing and using snap-fit features instead of screws, they reduced part count by over 40%. This cut assembly time in half and led to significant savings in production costs.
Case 2: John Deere’s Mechanical Assembly Optimization
John Deere redesigned a mechanical linkage assembly using DFMA guidelines. The team adjusted part tolerances to enable self-locating features and standardized fasteners across multiple product lines. These improvements reduced the need for skilled labor, decreased assembly errors, and increased production throughput across their facilities.
Insights from our article “Secrets From a Factory Assembly Line” reinforce these cases, emphasizing how early design decisions dramatically impact manufacturing efficiency. For instance, avoiding parts that require special tools or complex orientations can slash cycle times and reduce assembly worker frustration.
Read the Nightside case study to see how Fictiv supported a complex yet elegant lamp assembly.
How to Start Designing Products With DFMA
Adopting DFMA requires a deliberate, structured approach. By starting small and building on early wins by implementing DFMA practices, organizations can cultivate a culture where product quality and process efficiency are deeply ingrained within the company. Here are practical measures to integrate DFMA into your workflow:
Form Cross-Functional Teams
Include design engineers, manufacturing experts, and quality assurance professionals early in the design process. This ensures multiple perspectives are considered to allow for optimization across the entire product development process.
Identify High-Impact Assemblies
Start with products or subassemblies that have high complexity, cost, or failure rates. Prioritize those with the biggest return for a redesign.
Create DFMA Checklists and Guidelines
Institutionalize DFMA through standardized documentation that teams can reference throughout the product life cycle.
Use Iterative Design Loops
Incorporate DFMA checks into design reviews. Use prototyping and feedback to gradually refine designs. Make sure feedback from production teams is integrated into each loop to further hone in on an optimized product design.
Partner With Suppliers
Engage key manufacturing partners early to validate feasibility, identify opportunities for process-specific optimizations, and build a network of trusted suppliers. Additionally, building long-term supplier relationships can also uncover DFMA insights that are not obvious from design software alone.
Educate and Train Teams
Provide ongoing DFMA training to engineers and managers to build a culture of continuous improvement and optimization.
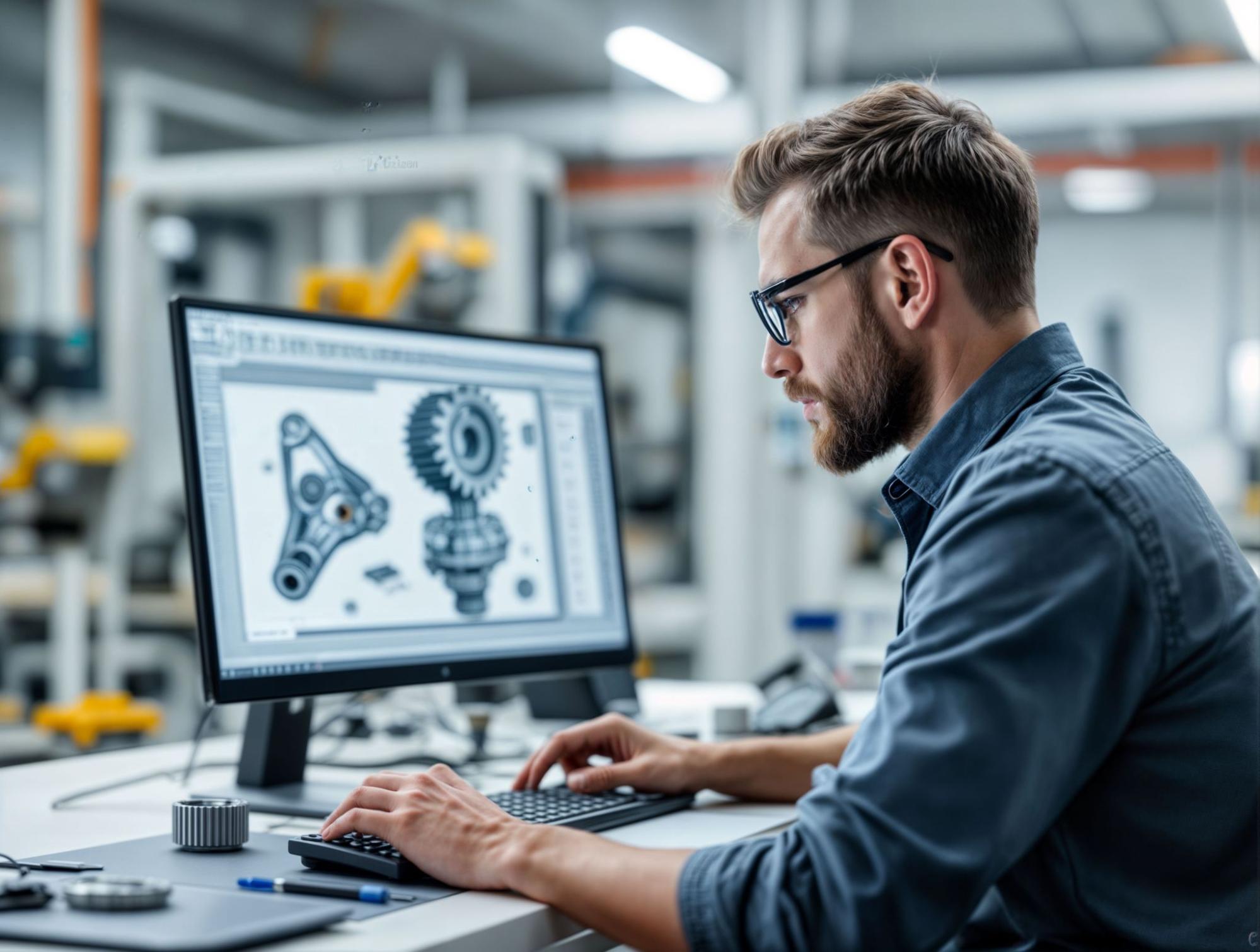
DFMA Tools and Software
Modern DFMA practices are supported by a growing ecosystem of digital tools and software, some of which are described below:
DFMPro
Integrated with major CAD systems like Creo and SolidWorks, DFMPro provides real-time manufacturability checks, alerts, and design improvement suggestions tailored to specific processes such as injection molding and machining.
Boothroyd Dewhurst DFMA Software
Known for its part count analysis and DFA Indexing features, this tool helps engineers quantify the efficiency of an assembly and identify consolidation opportunities. It is widely used in the automotive and aerospace industries for reducing production costs and optimizing assembly workflows.
CAD Platforms (Fusion 360, Siemens NX)
These platforms increasingly feature built-in simulation, digital twin technology, and design rule verification to flag potential manufacturing issues before prototyping. Siemens NX, in particular, integrates tightly with production planning tools to bridge the gap between design and manufacturing execution.
Fictiv’s Cloud-Based Platform
Our platform offers on-demand manufacturing with integrated DFMA feedback and automated quoting. Additionally, our system identifies design concerns and recommends changes before production, further accelerating development cycles. Fictiv also connects users to a vetted network of manufacturers, which helps to simplify sourcing and reduce procurement delays.
Simulation, digital twins, and virtual prototyping are also gaining popularity within Fictiv’s platform, offering an early glimpse into how designs behave under real-world constraints. These tools help bridge the gap between conceptual design and manufacturing feasibility.
Optimizing Product Development With DFMA
Design for Manufacturing and Assembly (DFMA) offers a proven framework for streamlining product development, reducing costs, and enhancing quality. By incorporating manufacturing and assembly considerations from the earliest design stages, DFMA enables teams to simplify product architectures, shorten development timelines, and improve manufacturability.
Begin or revisit your designs with DFMA in mind and leverage modern tools, such as Fictiv’s digital manufacturing platform, for support. With DFMA as a core design strategy, your team can bring better products to market faster and more affordably than ever before.
Ready to optimize your product designs for manufacturing and assembly efficiency? Get a free quote and explore how Fictiv’s digital manufacturing platform can help you implement DFMA principles.