Time to read: 5 min
I still remember the first Chinese electronics factory I visited like it was yesterday: It was an old tier-3* contract manufacturer somewhere in the sprawling Dongguan City. Its white tile facade was yellowed from acid rain, and despite the sweltering midsummer heat, only a few ceiling fans feebly circulated the muggy air on the factory floor. The harsh fluorescent lights were only turned on over the assembly stations to save electricity. I was wearing an XXL sized polyester lab coat and shoe covers, sweating like a can of soda.
The conditions were a far cry from the Canadian SUV manufacturer where I cut my teeth. However, I learned a lot more about low-cost ways to increase assembly efficiency on the dimly-lit factory floors of Dongguan. These factories survive on cutting costs while maintaining high throughput. There are no robots, only low-tech solutions.
If you’re assembling a low-volume run of an MVP in your garage, with the help of family, friends, and strangers from Craigslist, you too can adopt some of these practices to get the job done faster. Here’s what you’ll need.
* tier 3 = the secret subcontractor to the secret subcontractor to the giants like Foxconn, Flextronics, and Jabil
Hang work instructions overhead for easy reference
Print out work instructions, so people who didn’t design the product can easily participate in assembly.
Good work instructions should contain:
- Material required (e.g., 2 screws, superglue).
- Equipment required (e.g., Phillips screwdriver).
- Photo of incoming subassembly at this station.
- Photo of subassembly completion at this station.
- Instruction steps in words, with accompanying photos. You can also include inspection steps (IPQC).
Here’s an example of very clear work instructions:
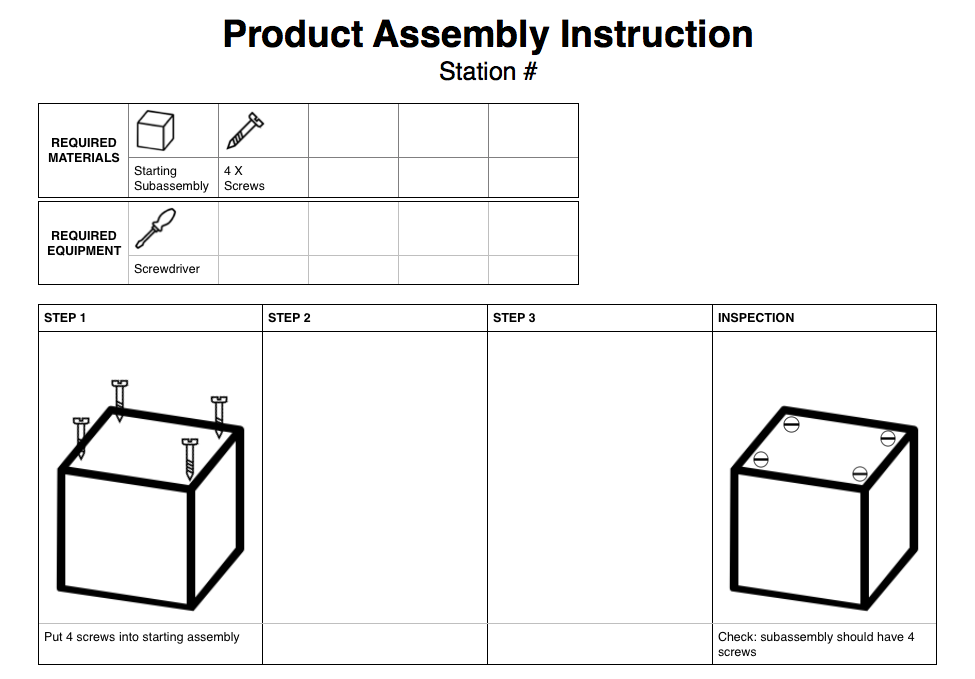
Motorized torque screwdrivers with magnetized tips
Torque screwdrivers prevent you from stripping threads by over-tightening. Factories use them to ensure an equal amount of tightening from unit to unit, from operator to operator. The motor also prevents carpal tunnel in workers and speeds up the assembly.
Motorized torque screwdrivers are quite expensive in the U.S., but if you go on eBay or Aliexpress, you can find some for under $100. It might be worth it if you use a lot of fasteners!
You can magnetize any screwdriver tip. Just get a piece of strong magnet and pass your screwdriver over one of its surfaces a few times.
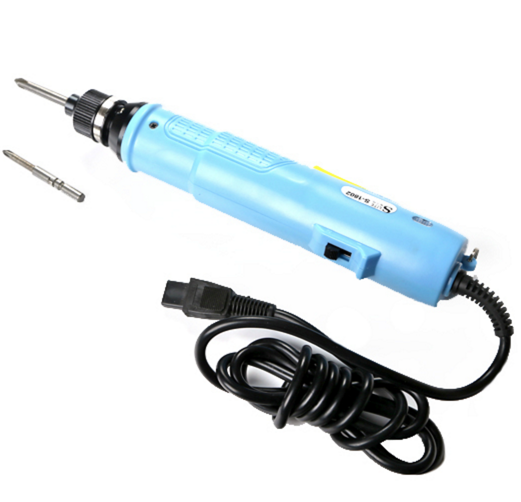
A nicer way to dispense screws
Someone will inevitably knock over a little paper cup of 500 M2 screws, but it’s easy to make this scenario less likely.
The nicer factories have automatic screw dispensers. However, even the lowest tier factories have magnetic trays for screws. Sometimes, the dispenser’s actually just a plastic tray with a piece of magnet inside. Just make sure the magnet isn’t so strong that you can’t pick up the screws with your magnetized screwdriver tip.
Ready-made trays are available on Aliexpress and Amazon. We’ve even seen them at Daiso in San Francisco. You can also cobble together your own with some magnetic sheets and any small tray or dish.
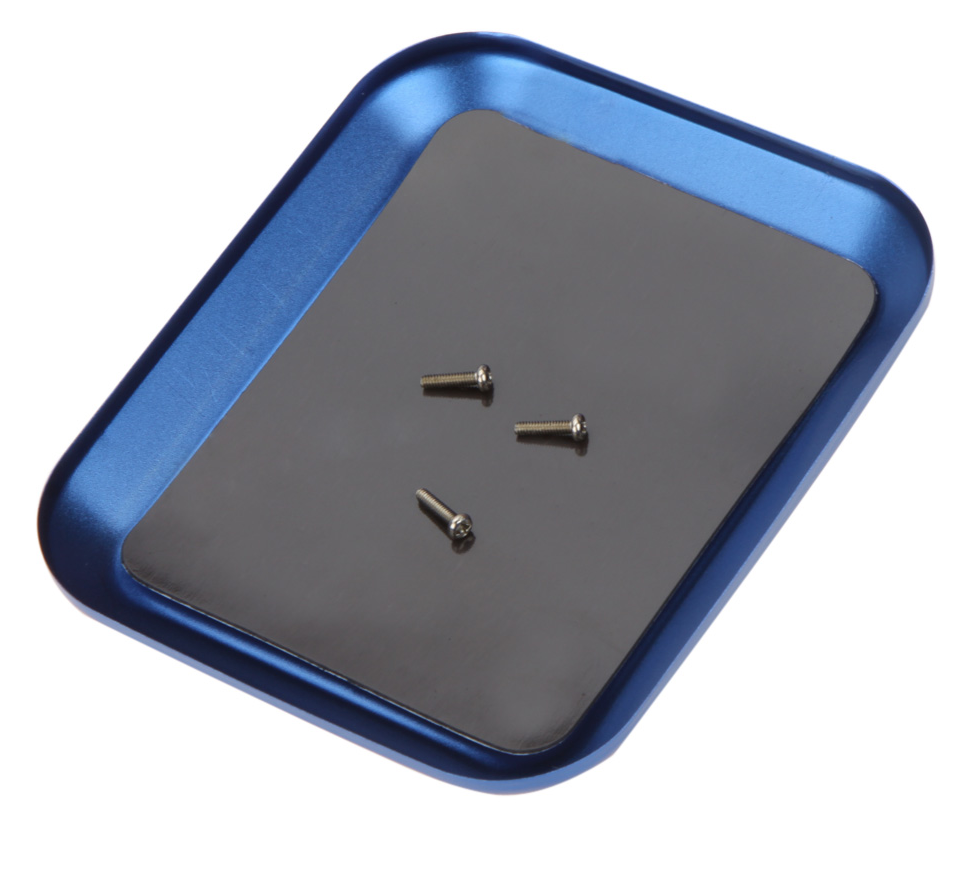
ESD mat and wrist strap
These are standard-issue anti-static devices used to protect sensitive electronics during assembly. They help to dissipate the static electricity that builds up on workers’ bodies. When you’re assembling electronics at home, it’s better to be safe than sorry, so always strap in!

Holding fixtures
Holding fixtures improve working ergonomics, and they prevent your product’s exterior from scratching and marring. They’re especially helpful when your product doesn’t lie flat on the table while you’re working on it. The CAD image below shows an example design of a fixture used to hold a mouse upside down. Such a fixture allows the underside of the mouse to be worked on easily.
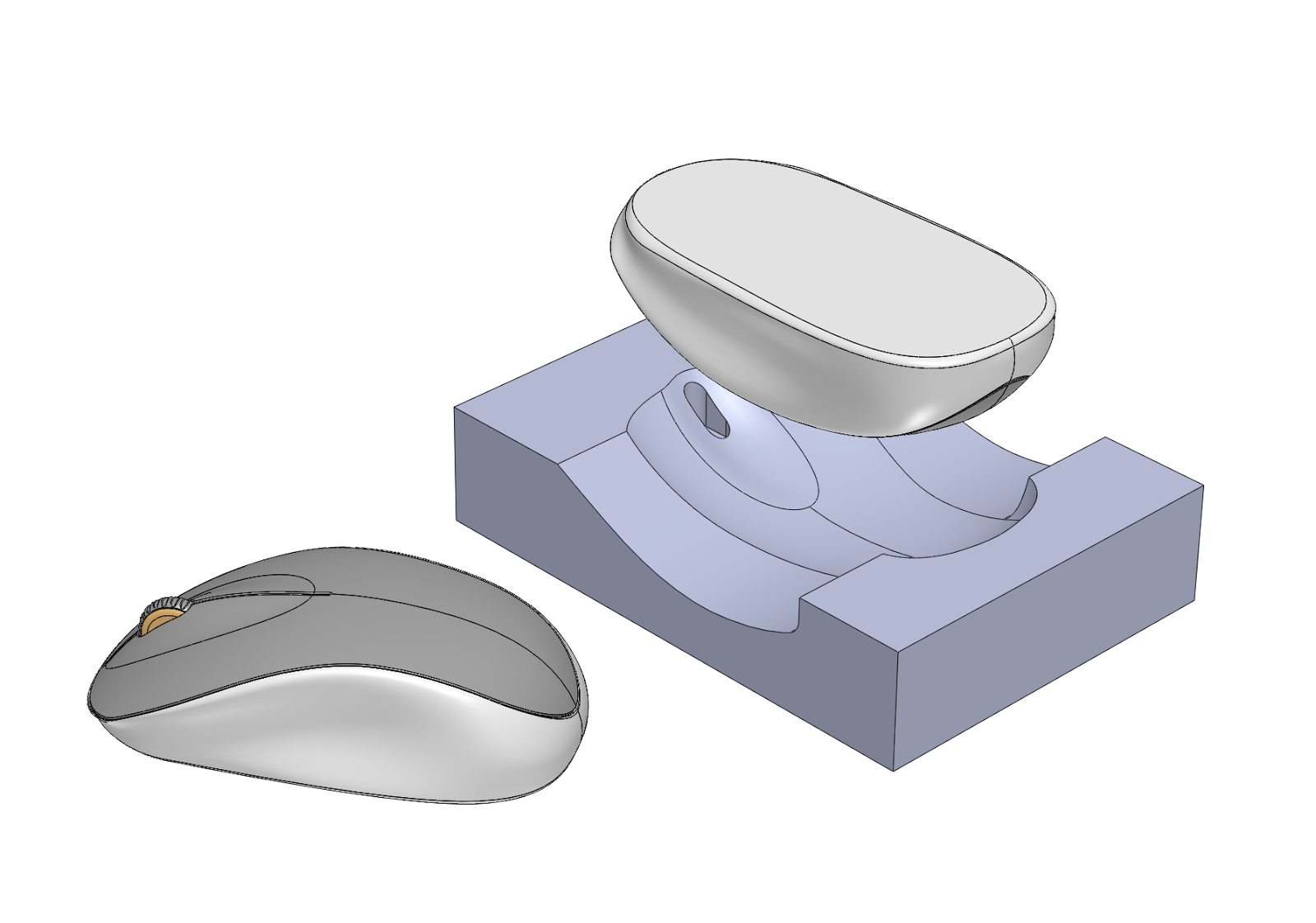
In the factories, holding fixtures are typically CNC milled with machining wax, then inserted into a base made with “antistatic wood” (which is actually Phenolic resin, aka Bakelite). 3D printing and CNC milled Delrin are great for making holding fixtures, too.
Locating fixture for shims and labels
If locating features are not designed in, adding locating fixtures can help increase the speed at which you can apply labels and shims. It’s often sufficient to locate two edges of a rectangular shim or label.
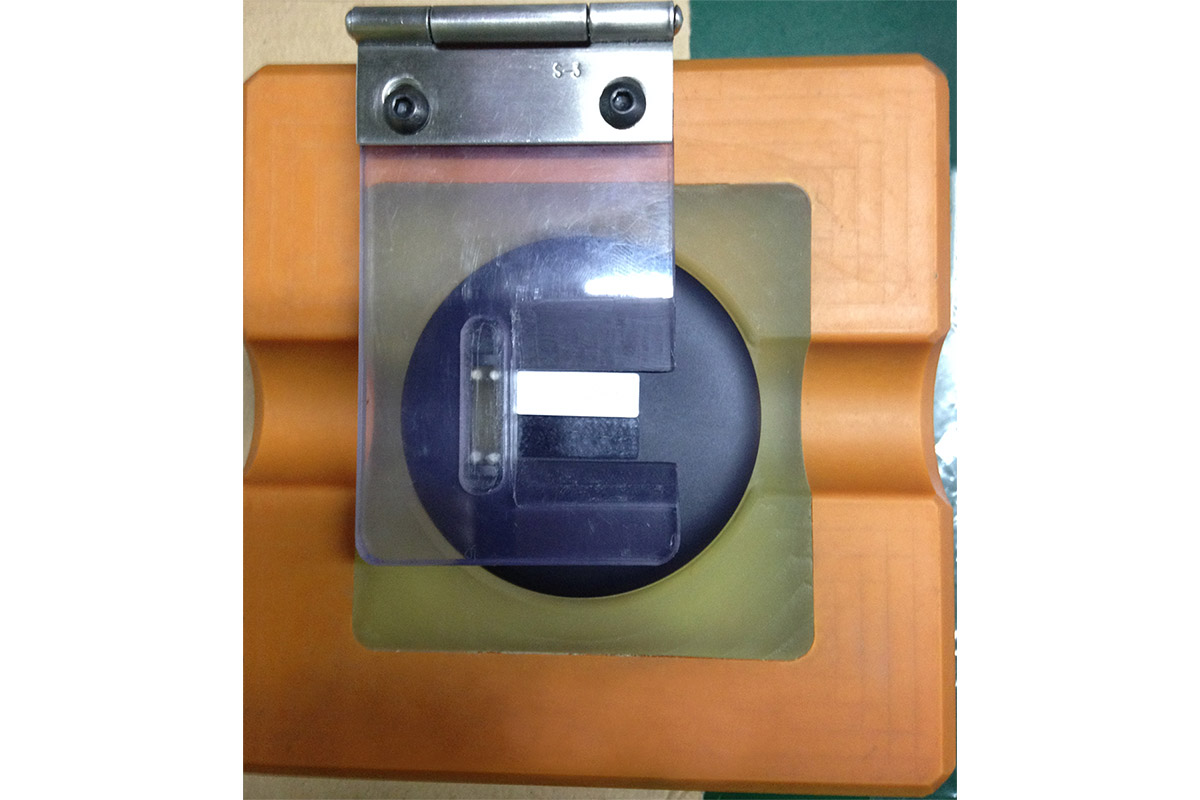
Heat-staking fixture (or soldering iron)
Heat-staking is one of my favorite assembly methods. It saves money on fasteners and is really fast. Heat-staking fixtures tend to be custom; a semi-automatic unit costs thousands of dollars.
However, a cheap soldering iron does the job, too. You can make it even better by adding a heat staking tip. Read more about heat staking here for inspiration on designing your own tip. This technique is great for joining 3D printed ABS parts.
Syringe to dispense glue
If you need to use liquid adhesives, consider getting syringes like these to control your application a little more precisely. Electrical engineers already use these to dispense solder paste.
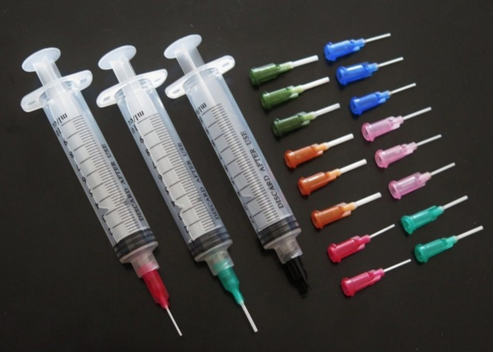
Divided trays to hold and separate your units
Factories always get custom vacuum-formed PET trays to move subassemblies between stations. They stack well and prevent the subassemblies from banging against each other.
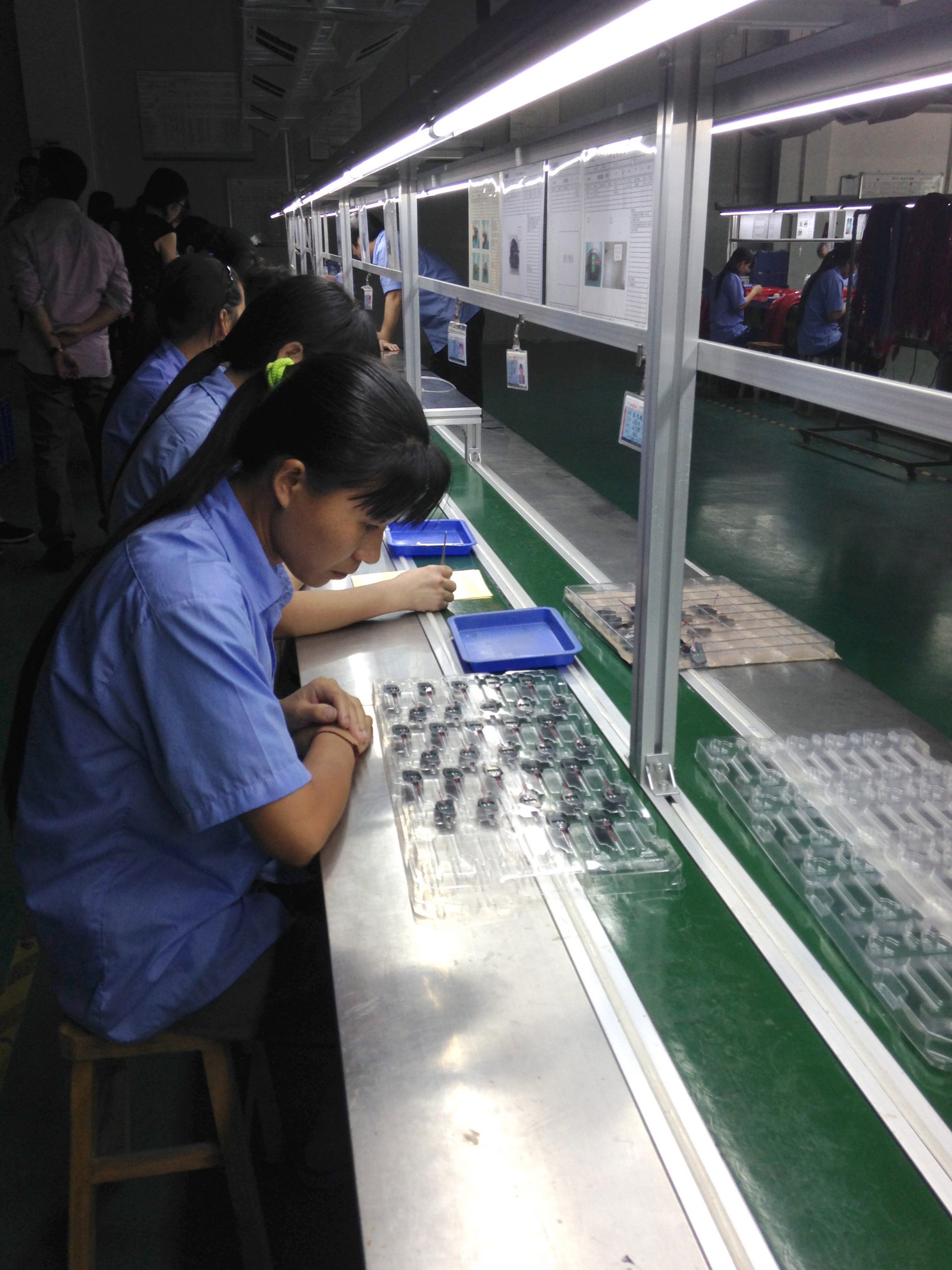
Garage assembly lines usually don’t have this luxury, but you can easily make your own. Check out this tutorial for drawer dividers, replace the cardboard with half-inch sheets of foam, and place your DIY divider in a shallow plastic bin (optional: line with felt or thin sheets of foam), and you’re set!
No food and beverages at the assembly station
A spilled cup of coffee might undo an hour of work. Food has no place near soldering irons and adhesives. Instead, put a snack and drinks table in a corner of the assembly room, so people can stay hydrated away from your precious products.
Wear clothes that can get dirty…or ruined
You don’t need to require your garage assembly line volunteers to wear polyester lab coats and shoe covers, but let them know to come ready to work, in clothes they don’t care about. Provide smocks, aprons, gloves, and shoe covers if you think your assistants are designer clothing types.
Pump techno
In some factories, you can hear a pin drop. In others, the machines are so loud you can’t hear yourself talking. However, there are a few that believe in the power of music to energize their workers. Does this sound like some hip startup’s open office plan, or what?
Hopefully, these tips will give you the confidence to start your own home assembly line with family and friends and crank out a low-volume run of your MVP. Let us know how it goes and if you have tips of your own to share after you’ve given home assembly a whirl!