Time to read: 5 min
Polycarbonate injection molding is used to produce parts from polycarbonate (PC) plastic, a tough, transparent, and heat-resistant polymer with applications ranging from automotive parts and electronic components to consumer products and medical equipment. Polycarbonate is a commonly used thermoplastic that combines high durability and impact resistance with excellent mechanical properties such as high strength, stiffness, and resistance to both impact and heat.
Importantly, polycarbonate has excellent optical properties. Many grades have 80% to 90% light transmission, meaning that most light passes through. Even when pigmented, this amorphous plastic maintains its durability and strength. Sometimes, polycarbonate is used instead of acrylic because PC maintains its physical properties over a wider temperature range. Polycarbonate can also be used as a lightweight replacement for glass that provides significantly greater impact resistance.
There isn’t just one type of polycarbonate, however, so part designers must compare different PC grades with each other and with other types of materials. This article describes different types of injection moldable polycarbonate and examines typical material properties, general advantages, and common applications along with polycarbonate design guidelines and processing parameters. If you’re a part designer or an engineer, you can also learn about general best practices in Fictiv’s Injection Molding Design Guide.
Download Fictiv’s Injection Molding Design Guide
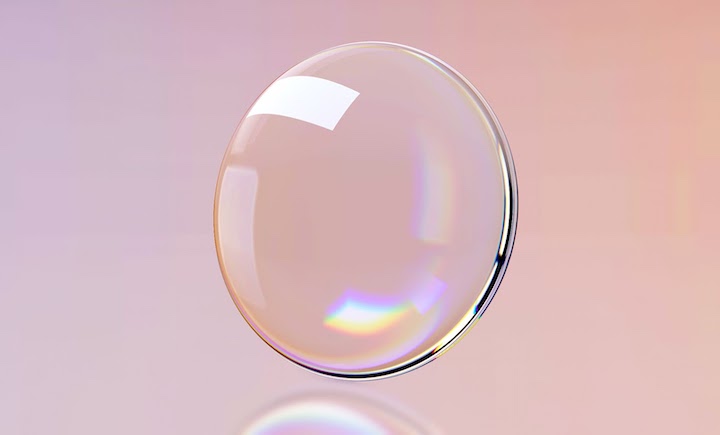
Polycarbonate Types
If you’re considering polycarbonate for your injection molding project, you can choose a generic PC grade or one that contains fillers or additives. Some PC plastics are filled with glass or contain a relatively small percentage of stainless steel fiber for added strength. There are many different polycarbonate suppliers, but well-known resins include Lexan® from SABIC and Makrolon® from Bayer MaterialScience. For SABIC Lexan® alone, over 100 different resins are available.
Polycarbonate plastic includes optical grades for injection molded parts that are optically clear and have near-total light transmittance and a very low haze factor, the percentage of perpendicular incoming light that deflects from a straight line at an angle of more than 2.5%. Polycarbonate plastic can also include UV additives that provide protection against direct, long-term exposure to sunlight. In addition, there are PC grades that meet UL 94 standards for flammability or that contain mold release agents.
Polycarbonate Material Properties, Advantages, and Applications
The table below lists some typical properties of polycarbonate plastic.
Category | Property | Typical |
Mechanical | Tensile Strength | 9,500 |
Tensile Modulus of Elasticity | 345,000 | |
Tensile Elongation | 135 | |
Flexural Strength | 13,500 | |
Flexural Modulus of Elasticity | 345,000 | |
Compress Strength | 12,500 | |
Hardness | M70, R118, Shore D 80 | |
Izod Impact | 12.0 – 16.0 | |
Thermal | Coefficient of Linear Thermal Expansion | 3.8 |
Heat Deflection Temperature | 280 270 | |
Max. Continuous Service Temperature | 240 | |
Electrical | Short-Term Dielectric Strength | 380 |
Optical | Light Transmittance | 86 |
Haze | <1 |
Table 1: Polycarbonate Properties
The use of fillers and additives can increase or decrease typical values; however, polycarbonate’s general advantages remain. There are five that are especially important, as shown by their applications.
- High strength and temperature resistance: Polycarbonate is a strong and durable plastic that can withstand high impacts and extreme temperatures. Applications include automotive tail light housings and LED lighting fixtures.
- Versatility: Polycarbonate injection molding can produce parts with complex shapes and intricate designs. Examples include enclosures for devices and equipment such as scientific instruments and medical robots.
- Cost-effective: Polycarbonate injection molding is a cost-effective manufacturing process that supports high-volume parts production. Applications for high-volume PC parts include brackets and medical tubing.
- Optical transparency: Polycarbonate has excellent optical clarity and transparency, making it ideal for applications that require clear or see-through parts. Examples include eyeglass lenses, safety goggles, and hard hat visors.
- Lightweight: Polycarbonate is a lightweight plastic that can reduce the total weight of a product. That’s important for the automotive and aerospace industries, and for handheld consumer products.
Polycarbonate Injection Molding Design Guidelines
When designing parts for polycarbonate injection molding, there are some general guidelines to follow that ensure your PC parts meet your end-use requirements.
- Wall thickness: Injection molded polycarbonate can support thin walls and complex geometries. The minimum recommended wall thickness is typically 0.040 inches (1 mm) with a maximum of 0.150 inches (3.8mm).
- Rib thickness: Ribs can be used to provide additional strength or support for polycarbonate parts. For the best results, make the thickness of a rib between 0.5 and 0.6 times the thickness of the adjoining wall. It is not recommended to use a rib height that is more than three times the thickness.
- Corner radii: Avoid sharp corners that can result in stress concentrations. With injection molded polycarbonate, use a corner radius of at least 0.125 inches (3 mm).
- Draft angle: Polycarbonate parts need a taper, or draft angle, to assist with part ejection from the mold. For many PC parts, a draft angle of 0.5° to 1° per side is sufficient. Depending on the angle and the shape of the part, however, 1° to 3° degrees per side may be needed.
- Gate location: Locate gates — the openings in the mold through which molten polycarbonate is injected — where the flow of plastic will cause the least amount of stress. A mold flow analysis can determine the optimal gate location.
- Surface finish: Polycarbonate supports gloss and high-gloss finishes, but matte finishes can be used to soften images and reduce glare in applications such as control panel overlays. Non-glossy finishes can also be used with screw caps.
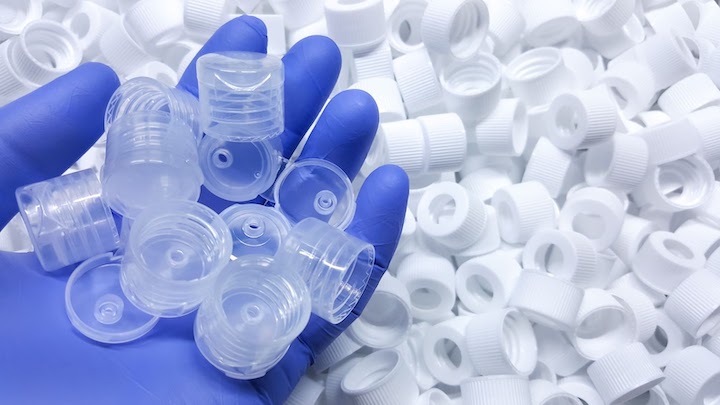
Polycarbonate Material Processing
Polycarbonate grades with greater mechanical properties have a higher molecular weight. Consequently, these injection moldable plastics have a lower melt flow rate and are more challenging to process. Designers need to select a PC grade that can meet end-use requirements, but molders must also consider that grades with higher impact resistance have a lower melt flow rate (MFR). For optimal processing, polycarbonate grades with a higher MFR are generally preferred.
Injection molders also need to consider these four factors during material processing.
- Drying: Because polycarbonate absorbs moisture, it’s important to pre-dry PC before injection molding. Typically, drying requires 100° to 120°C conditions for 3 to 4 hours. Molders need to keep the moisture content below 0.02% before processing begins.
- Mold temperature: Typically, the recommended mold temperature is between 150° and 174°C; however, the specific temperature depends on the grade of polycarbonate that is being molded. Higher temperatures are required for low MFR grades, and lower temperatures are required for high MFR grades.
- Injection pressure: The recommended injection pressure for polycarbonate is typically 70-100 MPa; however, this may vary depending on the size and complexity of the part. In general, molders need to keep the pressure as high as possible to enable faster molding.
- Injection speed: For smaller gates and edge-style gates, molders need to use slower injection speeds. For larger gates and other types of injection molded polycarbonate parts, use higher speeds instead.
Succeeding with Polycarbonate Injection Molding
Injection-molded polycarbonate parts have excellent properties such as impact and heat resistance, however, PC is challenging to process because some grades have low melt flow rates. That’s why having an experienced and knowledgeable manufacturing partner, like Fictiv, to help you through the process will get you the best results.
When you partner with Fictiv, you get free design for manufacturing (DFM) feedback along with your quote within 48 hours, and access to our vetted network of manufacturing partners with extensive polycarbonate injection molding experience. Our experts guide you through the production process to ensure you get quality parts no matter how complex your designs are.To get started, create your free Fictiv account and request a polycarbonate injection molding quote today — we make complex injection molded parts at ridiculous speeds!