Time to read: 4 min
Glass transition temperature (Tg) plays an important role in plastic injection molding because it determines when a polymer (such as a thermoplastic) changes from a rigid state to a semi-flexible state. During plastic injection molding, Tg affects processing conditions, cooling times, and post-molded properties such as a part’s thermal, mechanical, and optical characteristics.
This article examines Tg and the factors that influence or affect it. You’ll also learn about the differences between glass transition temperature (Tg) and melting point (Tm) — they’re both thermal properties of plastics, but Tg and Tm are not the same.
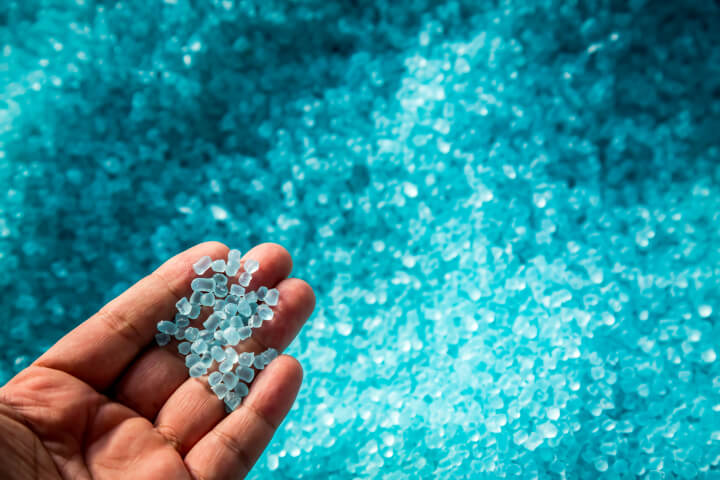
The plastic pellets that are used in injection molding are rigid and solid before they are heated.
Glass Transition and Thermoplastics
Glass transition refers to the reversible change in the physical properties of certain materials (such as thermoplastics) as they are heated or cooled through a specific temperature range. At low temperatures, these materials are brittle. As they are heated, however, these materials reach their glass transition temperature and become ductile instead.
For an example, consider the difference between the plastic pellets that are fed into the hopper of an injection molding machine and the molten plastic that enters the injection mold. The plastic pellets are solid and rigid, while the molten material is semi-flexible and rubber-like.
Glass transition temperature (Tg) is the temperature at which a polymer begins to undergo this transition. Based on their molecular structure, the thermoplastics used in injection molding generally fall into two categories:
- Amorphous plastics have a disordered molecular structure and no crystalline regions. Examples include PS, PC, PSU, and PVC.
- Semicrystalline plastics have a semi-ordered molecular structure with ordered crystalline areas interspersed between unordered amorphous areas. Examples include PE, PET, PTFE, and PP
Although glass transition temperature is related to processing, it’s not the same as melting point.
What’s the Difference Between Tg and Tm?
Glass transition temperature (Tg) and melting point (Tm) are two distinct temperature phenomena that characterize the behavior of polymers.
- Tg describes how amorphous plastics or the amorphous portion of semi-crystalline plastics transition from a rigid, glass-like state to a more flexible, rubbery state.
- Tm refers to the critical temperature at which the crystalline regions in semi-crystalline plastics flow and transition from a solid to a viscous liquid state.
Semi-crystalline plastics exhibit a gradual softening above Tg; however, they do not demonstrate true fluid behavior until reaching the Tm range.
In general, the melting point (Tm) of semi-crystalline plastics is higher than their glass transition (Tg) temperature. Often, the temperature difference between Tg and Tm is called the “rubbery region” because a plastic that reaches Tg is rubber-like. The image below illustrates the melting and softening phenomena of amorphous and amorphous plastics.
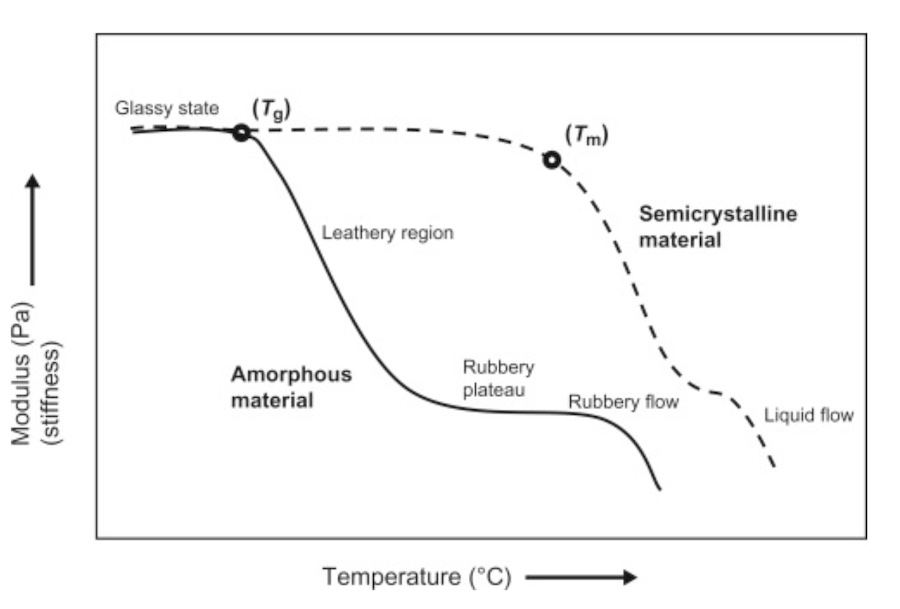
The table below lists Tg for some plastics that Fictiv works with.
Material | Tg (°C) |
General Purpose Polystyrene (GPPS) | 100 |
High Density Polyethylene (HDPE) | -120 |
Liquid Crystal Polymer (LCP) | 120 |
Liquid Silicone Rubber (LSR) | -125 |
Polycarbonate (PC) | 145 |
Polyetheretherketone (PEEK) | 140 |
Polyetherimide (PEI) | 210 |
Polymethyl methacrylate (PMMA) | 90 |
Polypropylene (atactic) (PP) | -20 |
Polyphenylene sulfone (PPSU) | 90 |
Polysulfone (PSU) | 190 |
Syndiotactic Polystyrene (SPS) | 100 |
Table 1: Glass Transition Temperatures
Why Is Tg Important in Plastic Injection Molding?
There are four main reasons why glass transition temperature (Tg) is important in injection molding:
- Mechanical Properties – Below Tg, polymers have limited flexibility, but above Tg, polymers are capable of deformation without fracturing. This supports processing.
- Processing Temperatures – By heating the polymer above its Tg, an injection molder can cause the material to flow and take the shape of the tool.
- Material Selection – Selecting a thermoplastic with an appropriate Tg ensures it can maintain its properties while withstanding application temperatures.
- Physical Properties – Tg influences physical properties such as thermal expansion, electrical conductivity, and optical transparency in the final molded products.
Which Factors Affect the Tg of Polymers?
There are many different factors that affect a polymer’s glass transition temperature (Tg), including:
- Molecular Structure – Polymers with flexible molecular chains, such as polyethylene, tend to have lower Tg values. On the other hand, polymers with more rigid and inflexible molecular structures, such as polycarbonate, exhibit higher Tg values.
- Molecular Weight – Generally, higher molecular weight polymers have higher Tg values. Because there are more entanglements and interactions between polymer chains, the strength of intermolecular forces is stronger and the Tg is higher.
- Presence of Plasticizers – Plasticizers interact with the polymer chains, reducing the intermolecular forces and increasing molecular mobility. As a result, the Tg of the polymer decreases, making it more flexible and less brittle.
- Thermal History – Polymers that have been rapidly cooled from a molten state may exhibit different Tg values than slowly cooled or unprocessed polymers.
- Chemical Cross-Linking – Cross-linking restricts molecular motion and increases Tg. As the degree of cross-linking increases, the polymer becomes more rigid and Tg rises.
- Crystallinity – Crystallinity restricts the movement of polymer chains and increases Tg. Because semi-crystalline polymers have both amorphous and crystalline regions, the overall Tg is influenced by the proportion and arrangement of these regions.
Succeeding in Plastic Injection Molding With Fictiv
You don’t have to be a material scientist to succeed with plastic injection molding. However, as a part designer, it’s important to understand glass transition temperature because Tg affects everything from processing conditions and cooling times to post-molded properties like thermal conductivity and optical clarity.
To get the best results for your project, it’s important to partner with plastic injection molding experts who can help you to select the right material based on a number of criteria. Fictiv has some of the best injection molders in the world with experience working with a variety of materials for a range of applications. Our experts can help with material selection and provide detailed DFM feedback to ensure your designs are optimized for injection molding. So, create an account and upload your part today!