Time to read: 6 min
Plastics are widely used in a range of applications due to their low cost, low weight, ease of processing, and a wide variety of material properties. However, most commodity and engineering plastics do not handle high temperatures very well. However, there is a group of plastics that not only have excellent thermal resistance but also excellent mechanical properties — which makes them ideal for a wide range of advanced applications.
This article explains how heat-resistant plastics are classified, the differences between amorphous and semi-crystalline plastics, and some common heat-resistant plastics.
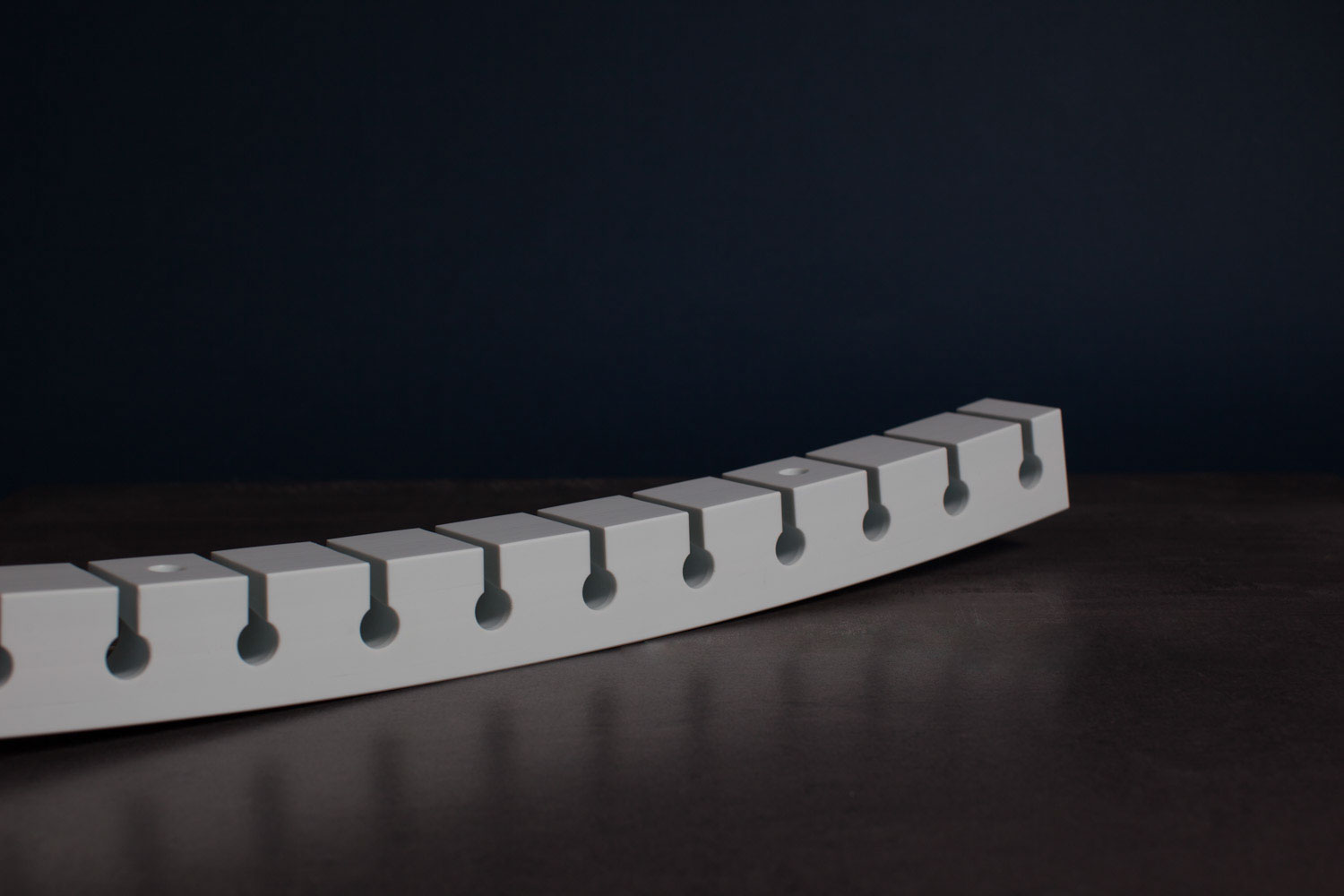
Amorphous vs. Semicrystalline Plastics
Thermoplastics generally fall within two categories that define how they react when heated. Here are the differences between amorphous vs semicrystalline plastics:
- Semicrystalline: Semicrystalline plastics have a semi-ordered molecular structure, with ordered crystalline areas interspaced in between unordered amorphous areas (randomly ordered molecular structure). These plastics have a sharp transition from solid to liquid. As such, semi-crystalline plastics have a defined melting point. Semicrystalline plastics are the most widely utilized plastic for the production of fibers, films, blends, and composites. Examples include PE, PET, PTFE, and PP.
- Amorphous: Amorphous plastics have a disordered molecular structure and no crystalline regions. These plastics tend to gradually soften when exposed to increasing temperatures. As such, amorphous plastics do not have a defined melting point like semi-crystalline thermoplastics. Examples include PS, PC, PSU, and PVC.
Thermal Properties of Heat-Resistant Plastics
Determining the applicable properties of heat-resistant plastics is a complicated topic due to the many different ways a plastic’s heat resistance is classified. Here are some common parameters used to describe heat resistance of plastics:
- Melting Point: The melting point is defined as the point at which plastic transitions from an ordered molecular structure to a disordered one. Semi-crystalline plastics have a precise point at which this change occurs, whereas amorphous plastics gradually soften when heated.
- Heat Deflection Temperature: The heat deflection temperature is defined by a test during which a specific load is applied to a sample at a specific temperature. The heat deflection temperature is a measure of how well a material maintains its stiffness under an applied load and is also known as the heat deflection temperature under load (HDTUL).
- Continuous Operating Temperature: This refers to the maximum safe operating temperature of plastic for long-term use (but not forever – this is limited to the point at which the material deteriorates). This value is normally measured when the plastic is exposed to air, and note that water and chemical solutions can dramatically reduce a plastic’s maximum continuous operating temperature.
- Glass Transition Temperature: The glass transition temperature (Tg) refers to the point at which a material transitions from a ductile to a brittle material. For some plastics, this value is well below zero degrees Celsius. As such, it is not always a useful measure of heat resistance. It’s also known as the temperature at which an amorphous plastic polymer changes from a hard material (sometimes referred to as a glassy state) to a softened (rubbery-like state) state. As the plastic is heated further, it turns into a viscous fluid.
- Flame Resistance: A plastic’s resistance to burning is measured in accordance with UL 94 (Tests for Flammability of Plastic Materials for Parts in Devices and Appliances). This standard is used to determine a plastic’s resistance to ignition – whether or not it produces flammable plastic drops – and how it performs when consistently exposed to elevated temperatures. A plastic’s flammability is rated on a scale, and plastics with V-0, V-1, and V-2 ratings are accepted for use in consumer products.
Heat-Resistant Plastics
Some of the most popular heat-resistant plastics are: PEI, PEEK, PTFE, PAI, and PPS. These are all thermoplastics, which means they will melt or soften when heated, but will re-solidify and regain their properties, provided they are not heated to the point of burning. Thermosets, on the other hand, are a type of plastic that will break down chemically if heated past their maximum operating temperature and will not regain their properties once cooled.
Polyetherimide – PEI – ULTEM®
Polyetherimide (PEI) is a high-performance amorphous thermoplastic with high tensile strength, and favorable chemical and temperature resistance. It also has high dielectric strength, which means it behaves as an electrical insulator. This material is often referred to by its trade name Ultem®.
Typical applications include electrical circuit boards, sterilizable medical equipment, food processing equipment, and aircraft components. Ultem® is, however, a very high-cost material. The table below lists some key properties of Ultem 1000, a common grade of this plastic:
Property | Value |
Tensile Strength (MPa) | 117 |
Hardness (Rockwell R) | R125 |
Density (g/cm3) | 1.28 |
Softening Point (°C) | 200 |
Heat Deflection Temperature (@264 PSI) (°C) | 204.4 |
Continuous Service Temperature in Air (°C) | 171.1 |
Short-term Service Temperature (°C) | 182.2 |
Glass Transition Temperature (°C) | 210 |
Flammability (UL 94) | V-0 |
Polyether Ether Ketone – PEEK
Polyether ether ketone is a high-performance semi-crystalline thermoplastic with excellent thermal and chemical resistance. PEEK also has excellent hydrolysis and steam resistance, but has poor UV resistance and is a high-cost material.
Typical applications include oil and gas components, sliding bearings, cable insulation, and catheters. The table below lists some key properties of unfilled, virgin PEEK:
Property | Value |
Tensile Strength (MPa) | 110.3 |
Hardness (Rockwell R) | 126 |
Density (g/cm3) | 1.31 |
Heat Deflection Temperature (@264 PSI) (°C) | 160 |
Continuous Service Temperature in Air (°C) | 248.8 |
Plastic Melting Temperature (°C) | 340 |
Flammability (UL 94) | V-0 |
Polytetrafluoroethylene – PTFE – Teflon®
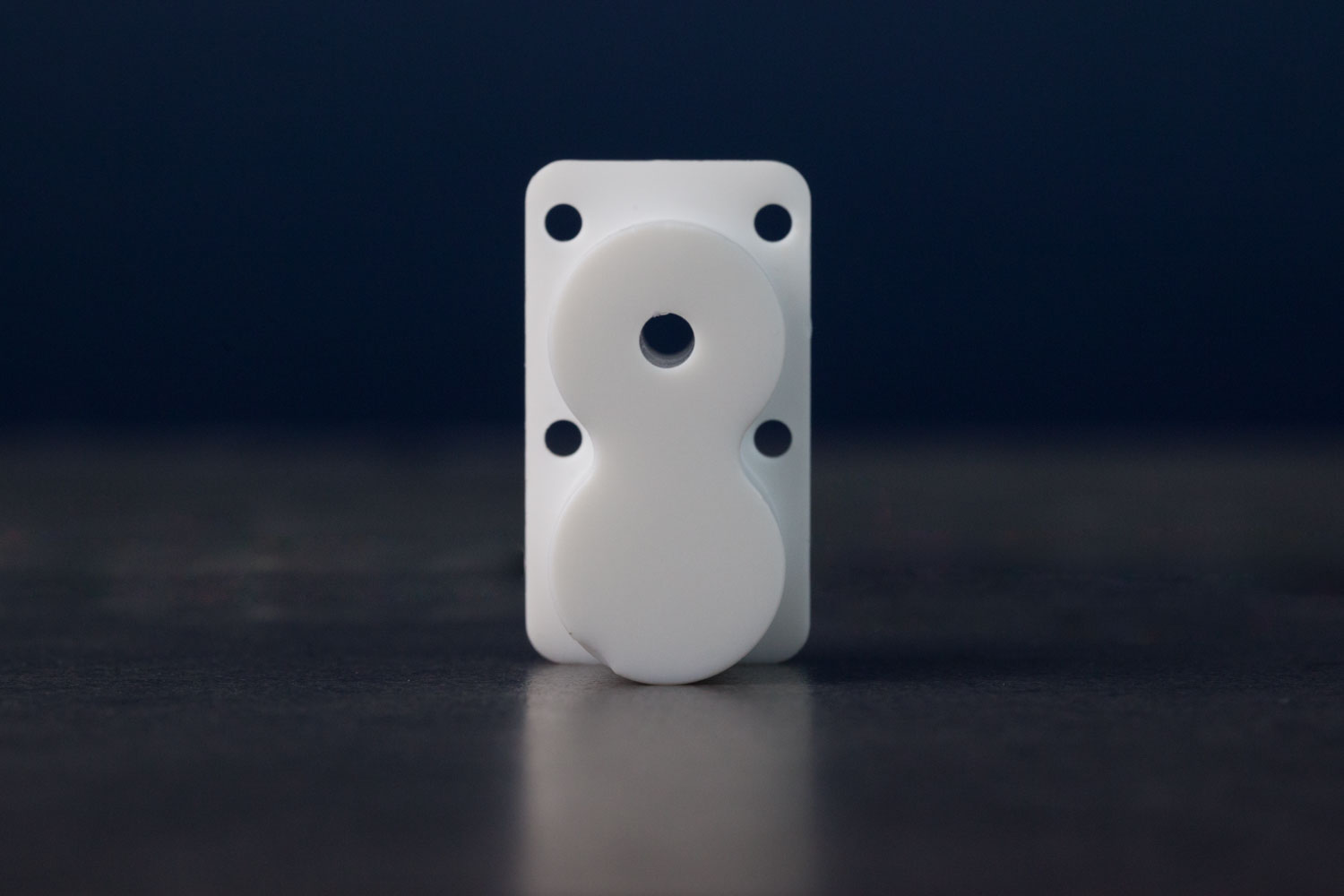
PTFE is a high-performance, semi-crystalline thermoplastic that is chemically inert, meaning it is unaffected by most chemicals. PTFE, often referred to by its trade name Teflon®, also has very low friction and is wear resistant. PTFE is widely used as a non-stick coating for pans and cookware as well as for chemical storage containers. It’s relatively low cost when compared to other high-temperature resistant engineering plastics, but is highly inelastic. Additionally, most adhesives do not work with PTFE. The table below lists some key properties of unfilled, virgin PTFE:
Property | Value |
Tensile Strength (MPa) | 20.7 |
Hardness (Rockwell R) | 60 |
Density (g/cm3) | 2.22 |
Heat Deflection Temperature (@66 PSI) (°C) | 121.1 |
Continuous Service Temperature in Air (°C) | 287.8 |
Plastic Melting Temperature (°C) | 325–335 |
Flammability (UL 94) | V-0 |
Torlon® – PAI
Polyamide-imide (PAI) is a very high-performance amorphous thermoplastic that maintains its mechanical properties at elevated temperatures for extended periods. PAI, sometimes referred to as Torlon®, is widely considered to be the highest-performing thermoplastic, with excellent mechanical strength, radiation resistance, and corrosion resistance. Torlon®, however, is a high-cost material.
Typical applications include clip nuts for aerospace applications and as a metal replacement in high-temperature zones in automotive applications. The table below lists some key properties of PAI:
Property | Value |
Tensile Strength (MPa) | 138 |
Hardness (Shore D) | 90 |
Density (g/cm3) | 1.41 |
Heat Deflection Temperature (@264 PSI) (°C) | 278 |
Continuous Service Temperature (°C) | 200–220 |
Plastic Melting Temperature (°C) | 275 |
Flammability (UL 94) | V-0 |
Polyphenylene Sulfide – PPS
PPS is a semi-crystalline thermoplastic that has a good balance of mechanical and thermal properties. PPS is inherently flame-resistant and has good chemical resistance, but has poor dielectric strength. PPS is not an excessively costly material and so is ideal for less advanced applications like frying pan handles, centrifugal pump components, and rod guides. The table below lists some key properties of PPS:
Property | Value |
Tensile Strength (MPa) | 50–80 |
Hardness (Shore D) | 90–95 |
Density (g/cm3) | 1.35 |
Glass transition Temperature (°C) | 85–95 |
Heat Deflection Temperature (@264 PSI) (°C) | 100–135 |
Continuous Service temperature (°C) | 200–220 |
Plastic Melting Temperature (°C) | 275–285 |
Flammability (UL 94) | V-0 |
Methods for Improving Heat Resistance
Despite the baseline performance of the materials listed, there are ways to further improve the thermal behavior of plastic. Two common techniques are the use of additives and fillers:
- Additives: Thermal stabilizers with antioxidants are used to improve the thermal behavior of the plastic. Fire retardant additives are also used to improve materials’ flame resistance.
- Fillers: Fillers can be added to plastic to significantly improve its thermal resistance properties. Typical fillers include chopped glass fiber strands or ceramic powder. Note that thermal resistance is often increased at the expense of mechanical strength when fillers are added.
Which Heat Resistant Material Is the Best
When choosing a high-temperature plastic, it’s important to consider more than just a plastic’s melting point. The environment, load case, and economic factors must also be considered. If temperature resistance and high corrosion resistance are required, then PTFE may be the right choice. However, if long-term exposure to high temperatures in critical aerospace applications is desired, then a specialty polymer like Torlon® may be the way to go. In short, the best heat-resistant plastic is entirely dependent on the application.
Sourcing Simplified – Start Your Next Project With Fictiv
If you want to learn more about which high-temperature plastic is ideal for your specific application, we’re here to help! Fictiv is your operating system for custom manufacturing that can help with all your injection molding material selection, part manufacturing and finishing needs. We’re experts at producing custom mechanical parts in a variety of materials, and we simplify custom part sourcing with intelligent, streamlined, automated workflows.
Our platform is designed to make injection molding part procurement faster, easier, and more efficient.
Create an account and upload your part to see what our instant quote process, design for manufacturability feedback, and intelligent platform can do for you. Our injection molding service delivers T1 sample parts in as fast as 2 weeks!