Time to read: 10 min
The journey from initial prototype to mass production is a complex transformation for the development lifecycle of any product. While the progression isn’t perfectly linear, this guide highlights critical aspects of the process – from prototyping to testing and validation to bridge production to mass production.
To help explain each key stage, we’re tapping into the collective knowledge of ChatGPT (which also powers our Materials.AI assistant), with insightful advice from several Fictiv manufacturing experts including Joanne Moretti, CRO; Tom Smith, Senior Product Manager; Ashwin Kasirajan, Manufacturing Engineer; and Tessa Axsom, Product Marketing Manager.
Together, we’ll demystify the complexities, address common challenges, and offer expert insights to streamline this journey for you and your team. Let’s start by jumping right into the prototype stage of development.
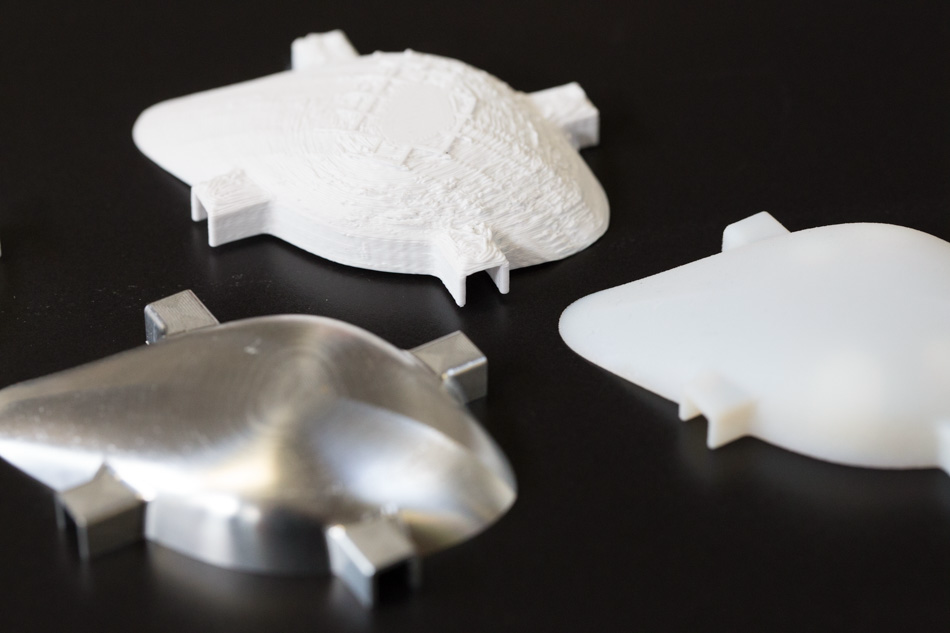
Understanding the Role of the Prototype
The prototype, the first physical iteration of your product idea, is an invaluable step in product design validation. This stage is not just about bringing a design to life but also rigorously testing, refining, and perfecting it. It’s where potential issues are identified and resolved, laying a solid foundation for subsequent production phases.
Working with an experienced manufacturing partner from the outset offers a streamlined path for parts procurement through the product development process and helps mitigate risk down the road. For example, Fictiv’s manufacturing engineers are experts across various processes and materials as well as have experience within certain use cases in automotive, medical, aerospace, etc. From 3D printing’s versatility and speed to CNC machining’s precision and injection molding’s repeatability – these manufacturing experts, coupled with the power of the Fictiv computational geometry, can help ensure that the prototype is not just a concept but a viable predecessor to the final product and moreover designed for manufacturing.
There can be big differences between engineering a product for prototype and engineering the product for manufacturing, and good manufacturing partners should bring this level of acumen to the table, including design for manufacturability (DFM) and design for supply chain (DfSC) expertise.
This level of partnership creates consistency through the various stages and helps identify and resolve potential issues early on, significantly reducing the risk of costly redesigns and delays in later stages. In addition to design risks, the other risk is around cost. Any manufacturing partner worth their salt should be working with both the supply chain manager and the product manager early to ensure costing and, ultimately, pricing on a product is nailed!
What else should you consider in the prototype stage? According to Joanne Moretti, Fictiv CRO and a former product manager:“One of the hardest things to do on a product is pricing. If you get that wrong, the entire program goes off the rails.”
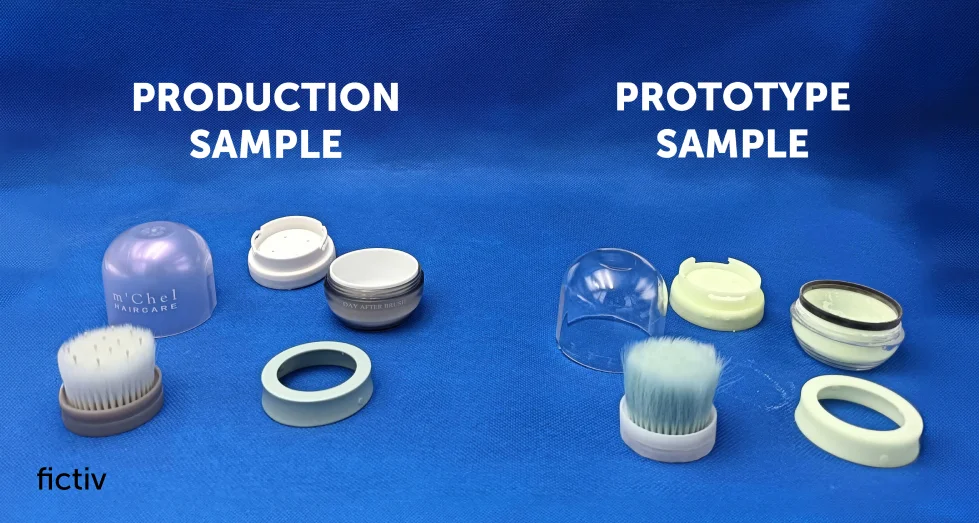
Moving from Prototype to Low Volume or “Bridge Production”
Transitioning to low-volume production is like shifting gears from a test drive to a road trip. It involves scaling up the manufacturing process while maintaining the design intent of the prototype. This transition can be complex, involving material consistency, cost management, and maintaining design fidelity.
- Material Consistency: Ensuring material consistency from a one-off prototype to a low-volume run can be challenging, as materials may behave differently at different scales or in different manufacturing processes.
- Cost Management: Balancing cost efficiency while scaling up production is tricky, particularly if the cost and scalability of manufacturing methods weren’t considered during the prototyping stage.
- Design Fidelity: Maintaining the design integrity of the prototype in low-volume production can be difficult, especially if changes in manufacturing or assembly methods require transitioning from one manufacturer to another.
Partnering with Fictiv at the prototype stage allows us to understand the project’s full context deeply and provide Design for Manufacturability (DFM) feedback with the final production in mind. For example, selecting prototyping materials that closely match the characteristics of the eventual production materials ensures a seamless transition from prototype to low-volume production. This approach not only streamlines the development process but also aligns early design decisions with the ultimate production goals, enhancing efficiency and reducing the risk of material-related challenges as the project scales.
Tom Smith, a senior product manager at Fictiv, also suggests gaining an understanding of Design for Assembly (DFA) for the transition from prototype build to production assembly. According to Smith: “This can help reduce issues faced when assembling products on a large scale. Frequently, there are challenges when transitioning from manually assembling prototypes to automated production lines and robotics.”
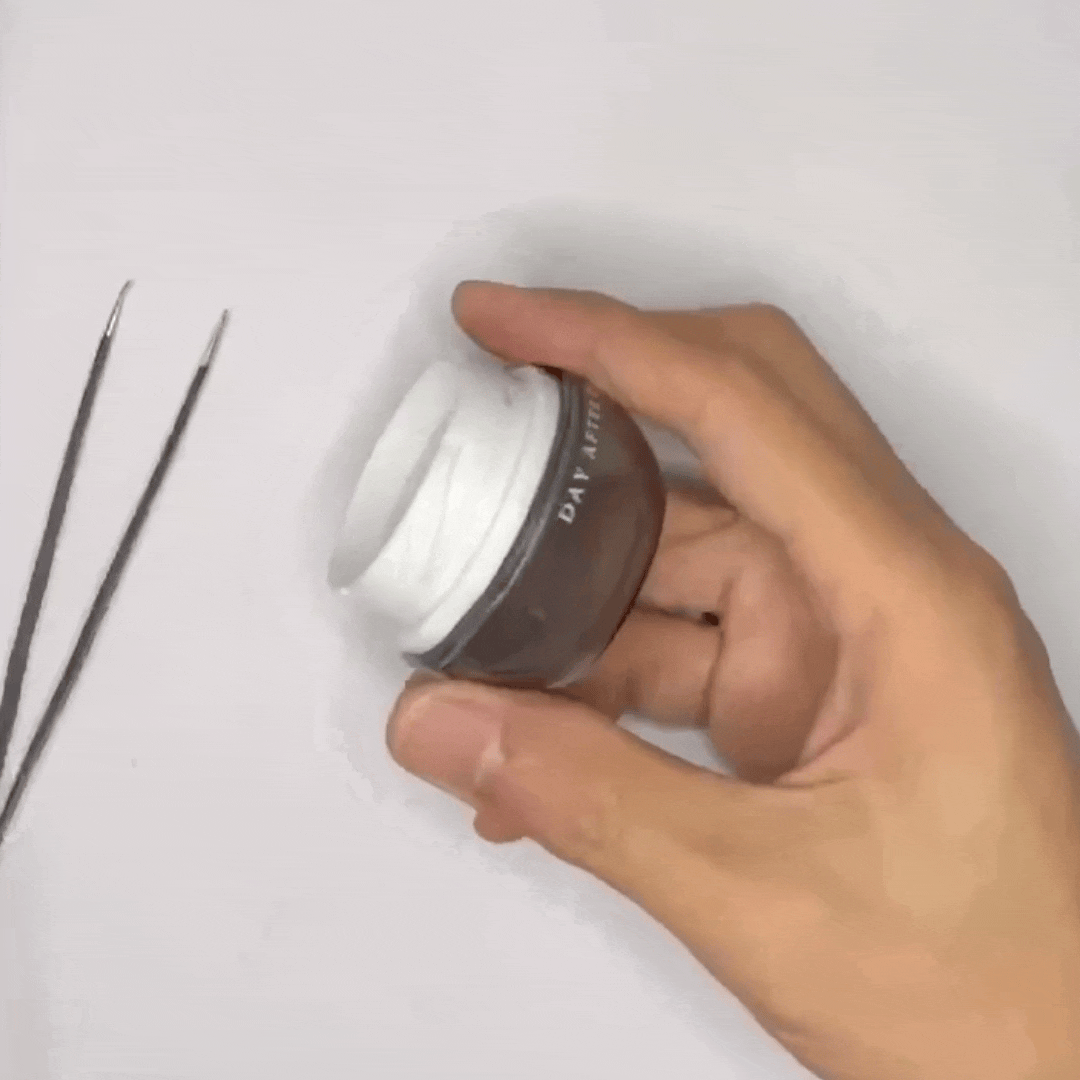
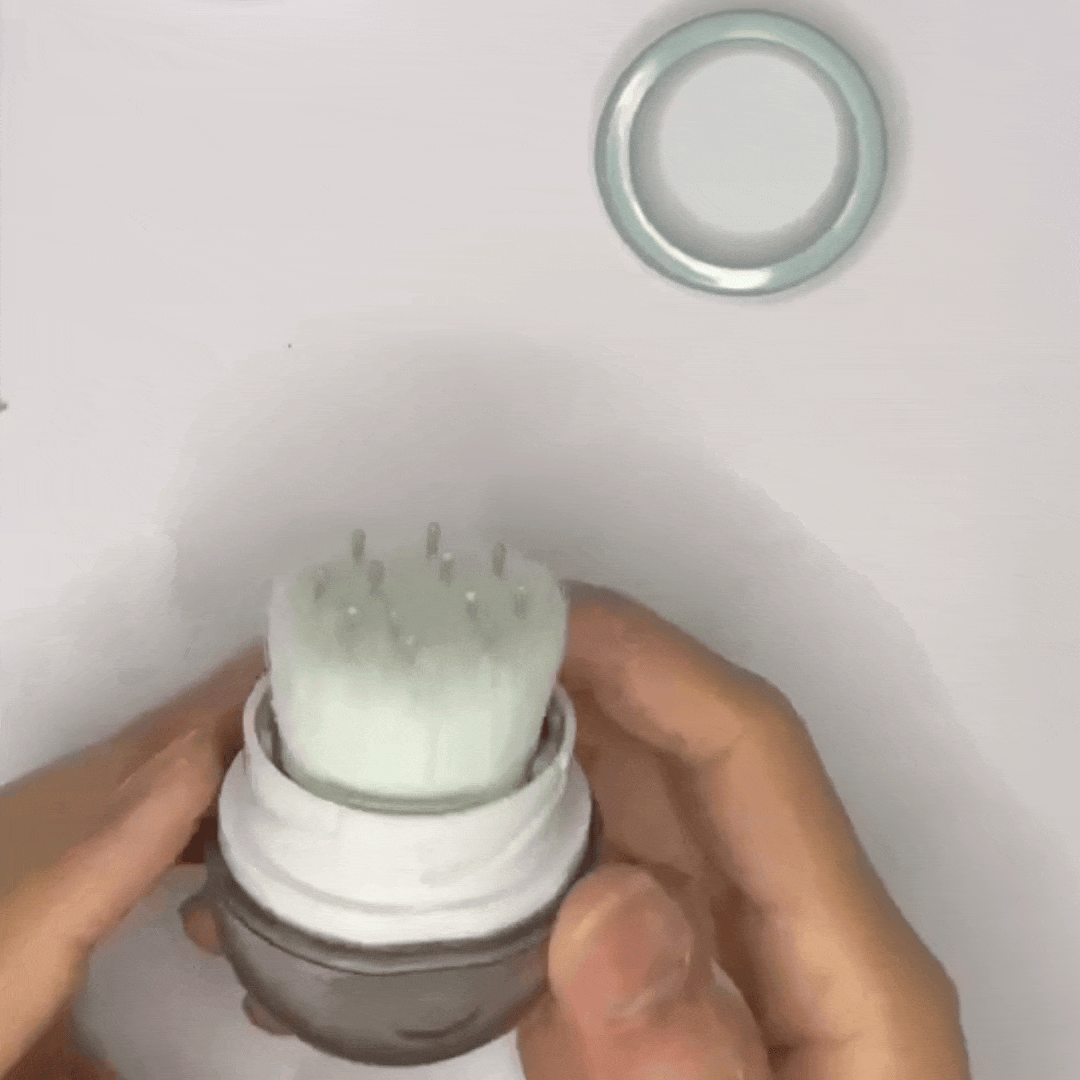
Understanding Low-Volume Production
Low-volume production acts as a crucial intermediary phase, offering a chance to refine the product further through limited production runs. It’s a testing ground for both the product and the production process, preparing both for the demands of mass production. Ashwin Kasirajan, a manufacturing engineer at Fictiv, explains, “Low-volume typically refers to quantities ranging from the tens to the hundreds of thousands of units, depending on the business and product.”
“With service providers like Fictiv, the flexibility of low-volume manufacturing is now accessible to more companies. They can produce on-demand, based on their actual needs, thus reducing the need for large and lengthy production cycles, and associated costs. This mitigates the risks of overproduction and warehousing large quantities of unsold products.”

These advantages can be critical to the success of a project, as Kasirajan points out, “Companies can quickly iterate on production designs, adapt to industry changes or introduce new features based on immediate feedback.”
However, key challenges during low-volume production include quality control, managing costs, and validating designs for assembly.
- Quality Control: Establishing rigorous quality control in low-volume production can be challenging, as the process isn’t as streamlined or automated as in mass production.
- Cost: Optimizing production processes for low-volume runs can be complex, as the economies of scale present in traditional mass production are not yet in play. Often, suppliers require minimum order quantities that may not match your needs, leading to difficult negotiations, higher component quantities than truly needed, and paying a substantial premium for a smaller number of production-quality parts.
- Design for Assembly: DFA is a critical aspect of low-volume production, focusing on simplifying the assembly process to reduce production time and costs. It involves designing components in a way that makes them easy to assemble, minimizing the number of parts, and simplifying assembly operations.
In the low-volume production phase, Fictiv plays a critical role in optimizing production efficiency and establishing rigorous quality control. Our team of manufacturing engineers, quality engineers, and logistics specialists collaborates closely with you to navigate the complexities of small-scale manufacturing, ensuring the highest standards of service and quality. Plus, Fictiv has low or even no minimum order quantities to match the specific needs of your development stages.
These were important factors as Fictiv helped this consumer products company take their innovative product idea from prototype to production.
Transitioning from Low Volume to Mass Production
The jump to mass production is a major leap, requiring a significant upscaling of manufacturing processes. This stage calls for meticulous planning in areas like supply chain management, quality control, and cost optimization. Scaling production and developing the supply chain are key challenges during this transition.
- Scaling Production: The challenge lies in scaling production processes efficiently while managing costs and maintaining product quality.
- Supply Chain Management: Developing a reliable and efficient supply chain for mass production can be complex, especially as the volume of materials and components increases.
Fictiv’s expertise in efficiently scaling up production, coupled with our ability to optimize supply chain management, ensures a smooth transition to mass production.
“One of my favorite ways to ensure efficient and cost-effective scale-up from production to prototype, is a Six Sigma technique known as process mapping,” explains Tessa Axsom, a CNC machining and metals expert at Fictiv. “So, you start with the prototype process, mapping out each phase of raw material acquisition to incoming inspection, manufacturing, cleaning, post-processing, inspection, assembly, and even shipping.”
“You include all the required inputs, actions, and outputs. This helps you to ensure you have the correct procedures, manpower, equipment, and other resources in place for each type of manufacturing and allows you to make quick comparisons between the two phases of manufacturing. It’s also a good tool to refer back to if you do have quality issues that arise.”
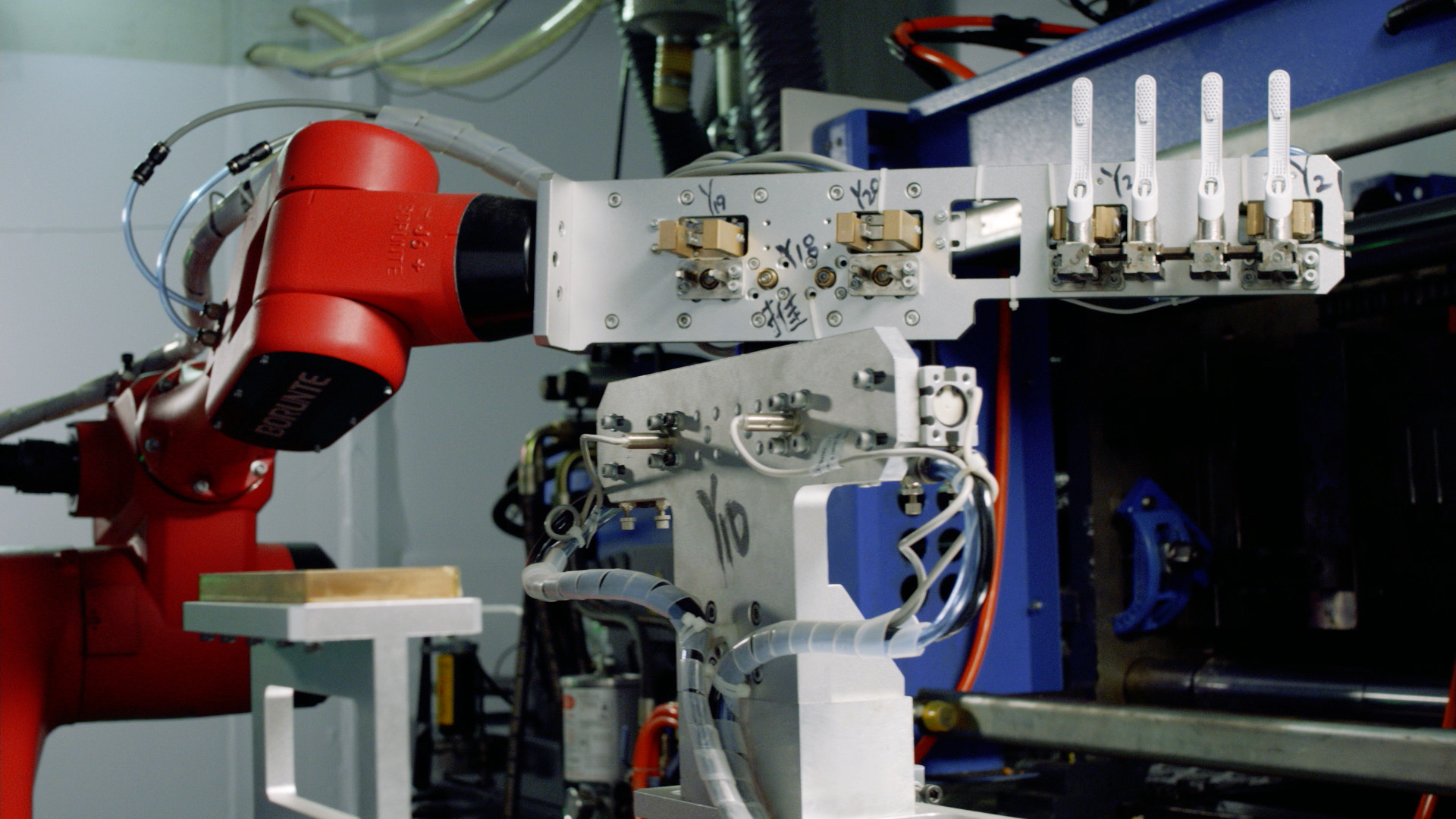
Understanding Mass Production
Mass production is the final frontier in the product’s manufacturing journey, characterized by large-scale production, efficiency, cost-effectiveness, and consistent quality. Understanding the dynamics of industrial-scale manufacturing and economies of scale is crucial, especially as it relates to these challenges.
- Process Optimization: Fine-tuning manufacturing processes like injection molding or CNC machining for high efficiency and low waste is crucial.
- Quality Consistency: Ensuring consistent product quality in mass production can be challenging, particularly when transitioning from more manually controlled processes.
- Bill of Materials Cost Down: At this stage of production, any costs saved in production can be added directly to the revenue generated from these products. Removing unnecessary costs at this stage is the primary concern.
- Demand Forecasting: Accurately predicting market demand is critical in mass production to avoid overproduction or underproduction. Effective demand forecasting involves analyzing market trends, historical sales data, and other relevant factors to estimate the quantity of product needed.
Tom Smith emphasizes the importance of demand forecasting in the mass production stage. “Working with a manufacturing partner capable of scaling production up or down, from 1,000 to 100,000 units a month, using the same processes and without constraints, can be paramount to success.”
Maintaining Quality in Mass Production
In mass production, maintaining high-quality standards is paramount. We believe that the robust quality control systems and monitoring established by Fictiv in earlier production stages help sustain product integrity and customer satisfaction through mass production, which is essential for the product’s market success.
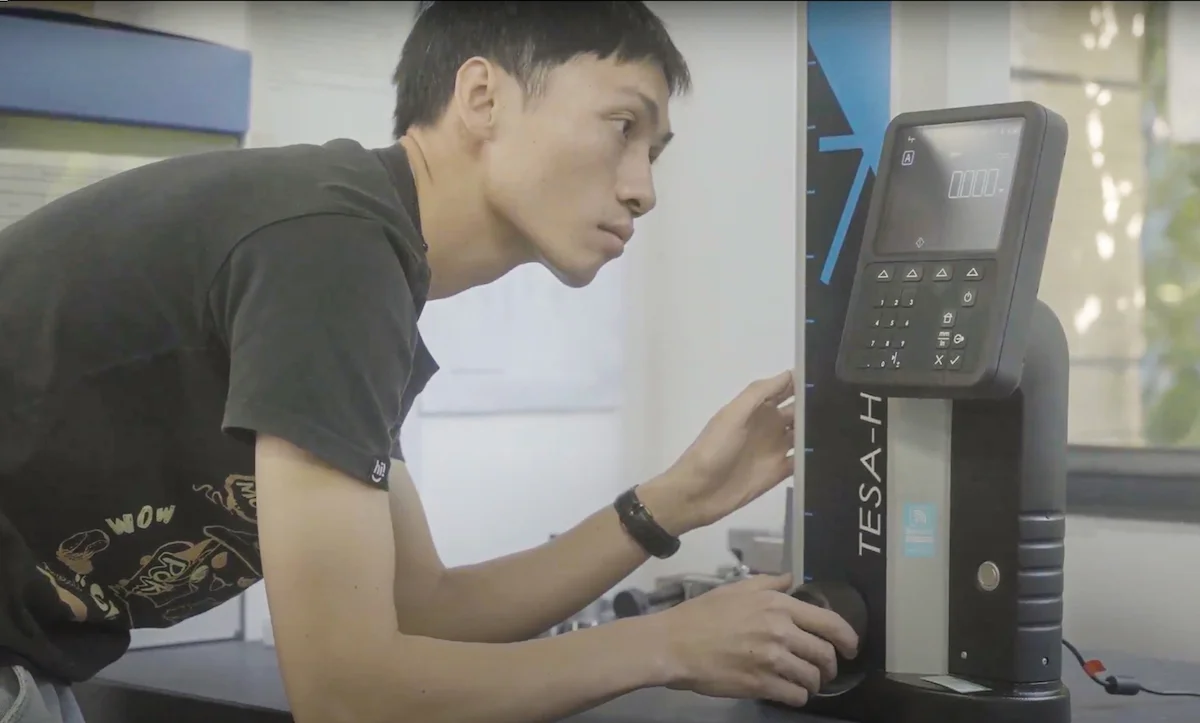
“A good tip for ensuring quality in mass production is to build quality into your production design,” says Tessa Axsom. “Designing for high quality and for inspection is an advanced skill, but you can begin with asking some important questions.”
- Can this feature be inspected?
- Can all the associated standard or specification requirements be met?
- What testing will be required to ensure parts meet requirements?
- Is this design unnecessarily risky for production? Can it be simplified in any way?
- Are there tolerances that account for machining AND finishing?
- Does the manufacturing team have all the information to ensure the successful production of the part via drawing notes, or is additional documentation required?
Axsom adds, “Designing high-quality parts goes beyond design for manufacturability or design for assembly; it ensures that the requirements you stipulate can be inspected and are achievable consistently.”
Simplify the Transition from Prototype to Production with Fictiv
The journey from prototype to mass production is multifaceted and challenging, yet crucial for the successful scaling of a product. Each stage – prototype, low volume, and mass production – presents unique challenges and requirements. Choosing to work with an experienced partner like Fictiv ensures the necessary guidance, expertise, and support to navigate these stages effectively, ensuring a smooth and successful transition towards ultimate success.
Get started by creating your free Fictiv account and uploading your part design today!
FAQs: Transitioning from Prototype to Production
What is Low Volume Manufacturing?
Low-volume manufacturing is the production of smaller quantities of a product, typically ranging from a few dozen to several hundred thousand units. This stage is essential for bridging the gap between a prototype and full-scale mass production. It allows for further testing, market evaluation, and refinement of the product and production process without the significant cost and commitment of large-scale manufacturing.
Why Do You Need a Prototype Before Production?
A prototype is crucial as it’s the first real-world test of your product concept. It helps identify design flaws, test the functionality, and gather user feedback, which are vital for refining the product. Prototyping also aids in verifying manufacturing feasibility and can be used to attract investors or for marketing purposes. It’s a risk-reduction step ensuring that the product is viable before investing in mass production.
What is the Transition from Prototype to Production?
The transition from prototype to production involves moving from a single, often hand-crafted, model of your product (the prototype) to a process where the product can be manufactured consistently and at scale. This transition requires considerations of materials, manufacturing processes, cost, scalability, and quality control to ensure that the product can be produced efficiently and to standards suitable for the market.
How Do You Go from Prototype to Product?
Going from a prototype to a product involves several steps: Refining the design based on prototype testing, selecting appropriate manufacturing processes, sourcing materials and suppliers, setting up production lines, and establishing quality control procedures. This often requires collaboration with manufacturing partners, engineers, and other stakeholders to ensure the product is manufacturable and meets market demands.
What are the Challenges When Moving from Prototype to Mass Production?
One of the main challenges is scaling the production process while maintaining quality and cost-effectiveness. This includes ensuring the design is suitable for mass production, managing supply chain logistics, securing consistent material quality, and implementing efficient manufacturing processes. Additionally, maintaining the design integrity and functionality of the prototype in mass production can be challenging.
What is the Next Step After Making a Prototype?
After creating a prototype, the next steps include thorough testing and refinement of the product based on prototype performance. This often involves design adjustments, materials testing, and functional evaluations. Concurrently, preparing for the next production phase (low volume or mass production) by planning manufacturing processes, sourcing materials, and estimating costs is essential.
How Do You Mass Produce a Product or Part?
Mass-producing a product or part involves setting up large-scale manufacturing processes that are efficient, cost-effective, and capable of producing high volumes of product consistently. This includes choosing the right manufacturing technology (like injection molding, CNC machining, etc.), designing for manufacturability, securing reliable supply chains, establishing quality control systems, and often automating processes to increase efficiency and reduce costs. Collaboration with manufacturing experts and facilities is key to successfully scaling up production.