Time to read: 9 min
In manufacturing, low-volume production comes with unique challenges for businesses looking to improve processes and reduce overall costs. Compared to high-volume production, low-volume production involves smaller batch sizes, which can lead to higher costs per unit. You may be tasked with budget control, cost-cutting, or cost-effective low-volume production as an engineer. Or, you may be charged with continuous improvement efforts and decide that focusing on cutting costs for low-volume production is a good start.
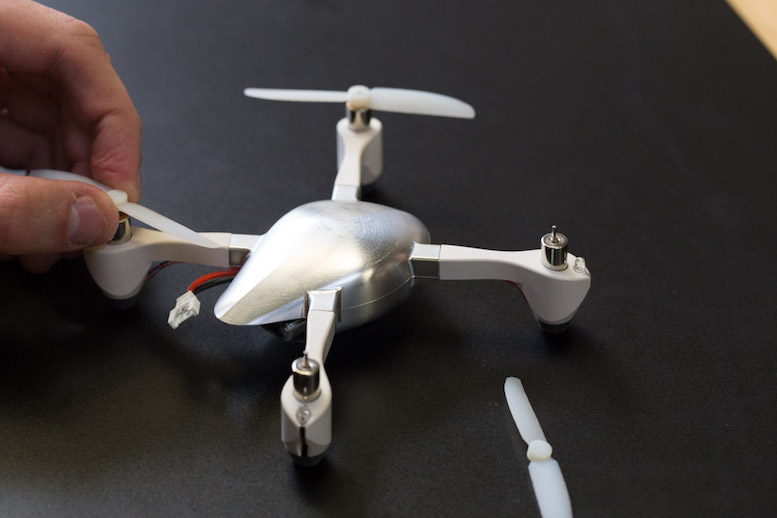
It might be overwhelming to venture into cutting costs for low-volume production. However, there are various effective ways for companies to overcome these challenges and find cost-saving solutions while maintaining high quality standards. At Fictiv, we make it faster, easier, and more efficient to source and supply mechanical parts. We help customers innovate faster and with less risk and reduced costs. In this article, we will share the best approaches from our experience that can assist organizations in improving efficiency and therefore cutting costs in low-volume production scenarios.
What is Low-Volume Manufacturing?
First, let’s define low-volume manufacturing or production so we are on the same page. Low-volume manufacturing, also known as low-volume production, is simply the production of parts on a small scale. Low-volume production may be utilized to define a wide range of scenarios, such as:
- Bridge manufacturing from prototyping during product development to full-scale production. Low volumes may be needed to provide units for testing, fit-up checks, or display to potential customers.
- Small-quantity production runs of a few to a few hundred parts due to customized products or insufficient demand for mass production as products are first introduced to the market. This allows manufacturers to test the market and determine demand before mass production.
- Fabrication of obsolete or discontinued parts for spare inventory or replacement components.
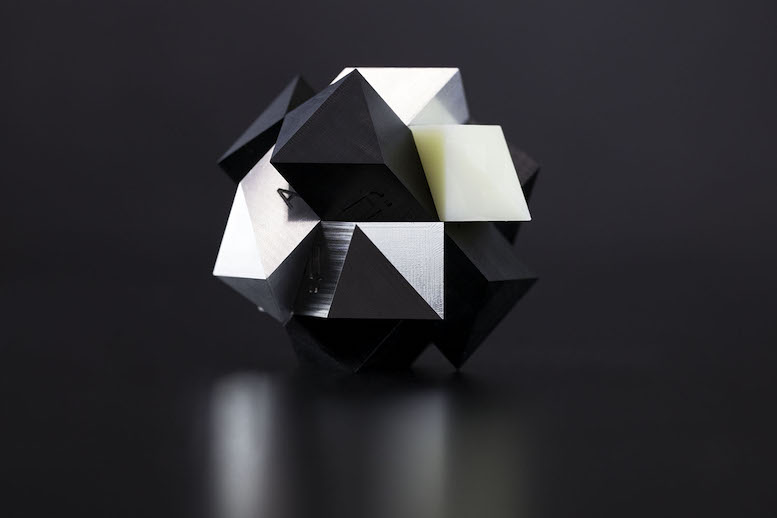
Is Low-Volume Manufacturing Expensive?
It’s no secret that the cost per piece increases with lower volumes. I am a fan of bulk stores like Sam’s Club and Costco, where I can get ridiculous amounts of home goods and groceries for lower prices (who doesn’t love a good discount?). Well, the same logic can be applied to manufacturing industrial parts. You typically buy and save more, especially with manufacturing processes like injection molding and CNC machining. So, low-volume production can be more expensive on a part-by-part basis when compared to mass production.
But, like most things in life, there is a tradeoff. You may not see as much upfront cost with low-volume production because you can choose methods like 3D printing or low-volume CNC machining that don’t require as much upfront cost in tooling, for example. There are even cost-friendly ways to utilize injection molding for low-volume manufacturing (check out our article, “Low Volume Injection Molding Use Cases,” for more detail).
Something is to be said about the reduced risk for low-volume production when producing prototypes or product development. If your design is in the development stage, it is less risky to produce less product that may have to be scrapped when a new design or a design change is made. This can help to rationalize the often higher cost of low-volume manufacturing.
- Streamlining Processes
Process streamlining is a fundamental way to cut costs in low-volume production. By carefully analyzing the production flow, businesses can identify and eliminate unessential steps, reduce cycle times, and improve efficiency. It is imperative to outline the step-by-step process for the entire manufacturing process, from sourcing the raw materials to delivering the final product. This allows organizations to identify bottlenecks and areas for improvement. By optimizing the flow of materials and information, companies can minimize idle time and maximize output, resulting in cost savings.
While experts may tell you to use a continuous improvement or lean manufacturing approach to streamline your process, that isn’t always the case. I was able to streamline and revamp an entire maintenance program at a plating shop with software she helped develop, all by analyzing the footprint of the maintenance department, performing time studies, implementing tedious planning tasks, and working with the members of the department to optimize their time and produce efficiency gains of 130%.
Here are some tips for anyone looking to streamline a process:
- First, you should be intimately familiar with the process you are trying to streamline. A process map is an excellent place to start. While commonly used to identify and resolve quality issues, they can also streamline a process. With process mapping, you identify inputs and outputs, outline every process step, measure time and resources, and study the flow.
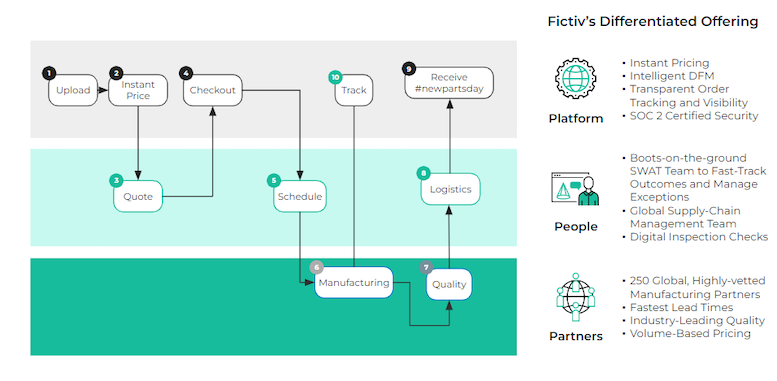
- With your process map in hand, analyze the workflow and identify areas for improvement. For this step, a lot of charting and spreadsheets are needed. Try out different layouts and combinations that you can test. I was inspired by the movie about McDonald’s, “The Founder,” where they use lean manufacturing techniques to help the fast-food kitchen streamline processes. Watch the clip here:
- Add up all available person-hours and ensure you correctly utilize them. Look for places where processes could be improved with artificial intelligence or even with robotics on a small scale. Look for versatile AI or robotics improvements that can be utilized across various parts you produce at low volumes. This will ensure you get the most value for your investment.
- Test, iterate, and refine over time. You don’t have to get it right the first time, and you should be willing to amend the process once you have streamlined it.
- Optimizing Inventory Management
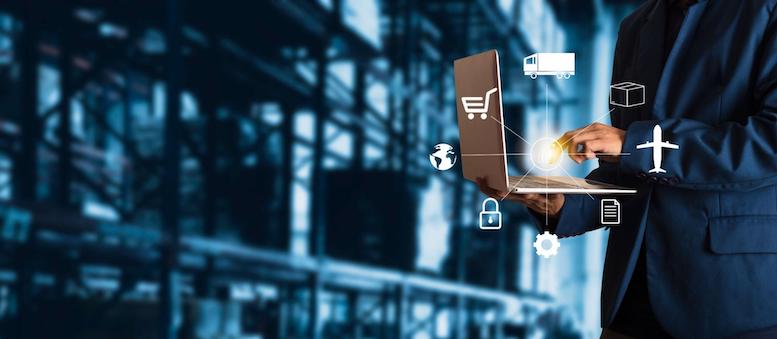
Efficient inventory management is vital for reducing costs in low-volume production. Having excess inventory ties up capital and increases carrying costs. Effecting just-in-time (JIT) inventory management systems can help to minimize inventory levels while ensuring materials and components are available when needed. Regularly analyzing demand patterns and supplier performance can help identify inventory optimization opportunities. Organizations can reduce storage, obsolescence, and carrying costs by keeping inventory levels lean and aligning them with customer demand.
You might also consider outsourcing to a rapid machine shop that can provide you with a just-in-case (JIC) inventory scheme at JIT footprint requirements. This can be done by partnering with a supplier, like Fictiv, who offers rapid, high-quality parts that can fit seamlessly into your supply chain. Sign up for an account here to see all that Fictiv can provide.
- Leveraging Technology and Automation
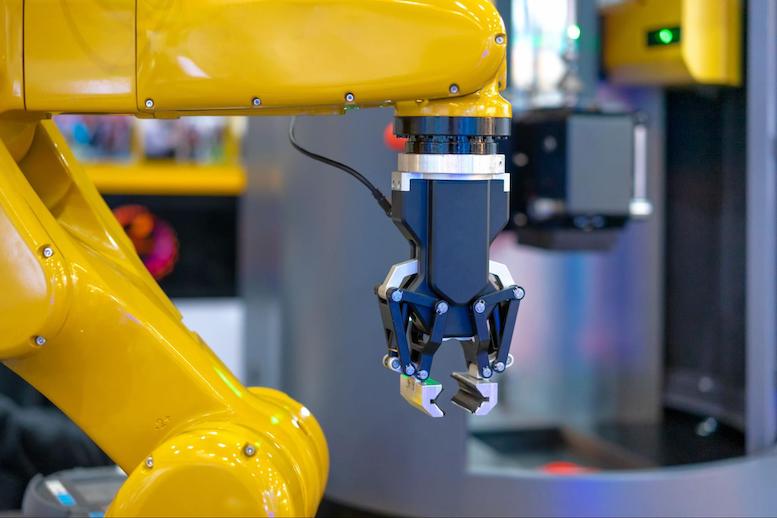
More than half (51%) of companies surveyed invest in technology solutions to drive productivity gains, while 85% say their companies already adopt AI solutions (source: Fictiv’s 2023 State of Manufacturing Report). Embracing technology and automation can result in significant cost savings in low-volume production. Implementing robotics, computer numerical control (CNC) machines and other automated systems can also reduce labor costs, improve precision, and increase production speed. The excellent news for low-volume manufacturing is that the technology can often be utilized for many processes and products, which lowers the per-part investment.
Technology, like AI, can also assist in monitoring and optimizing production processes, abating defects, and improving overall product quality. While there may be a significant initial investment, the long-term benefits of increased efficiency and reduced labor costs make technology adoption a wise choice for cost-conscious businesses.
Check out these Fictiv articles to learn more about utilizing technology and AI in manufacturing:
- Artificial Intelligence: A Digital Manufacturing Catalyst
- 5 Ways AI is Impacting 3D Printing
- CNC Machining with Robotics – Outlook and Manufacturing of Cobots in CNC Machining
- Using Robotics for CNC Machine Tending
- Outsourcing Non-Core Activities
As a company, you must decide what processes or manufacturing techniques you would like to perform in house and classify them as your core activities. What are core activities? While most machine shops utilize bar or sheet stock, they are likely not mining the raw materials, melting them down to the correct alloys, and forming the sheet or bar stock. These processes are all considered non-core and are often outsourced.
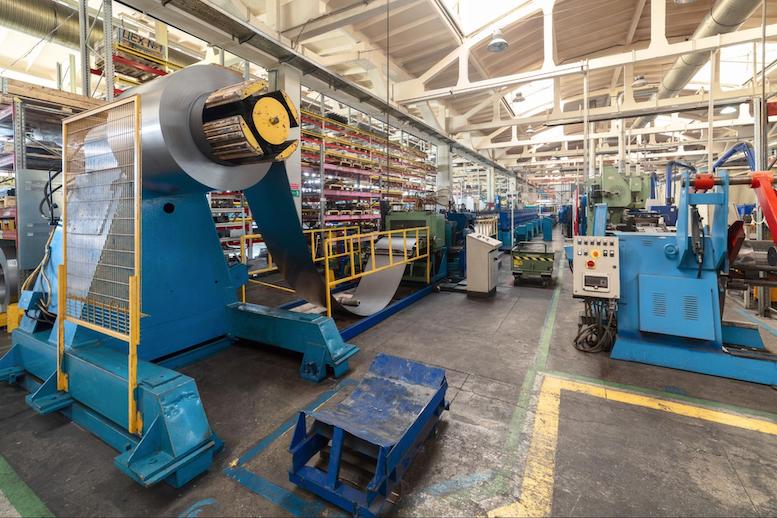
Subcontracting non-core activities can be a viable cost-cutting strategy for low-volume production. By partnering with expert vendors or contract manufacturers, organizations can leverage their expertise, infrastructure, and economies of scale, consequently reducing costs linked with in-house production. Outsourcing activities such as component manufacturing, packaging, or logistics allow companies to focus on their core competencies and allocate resources more efficiently. Additionally, outsourcing provides flexibility in production capacity, allowing businesses to scale up or down based on demand without bearing the fixed costs of maintaining a large workforce or production facility.
I would like to share a story about outsourcing from my personal experience when I was working as an aircraft design engineer. We were building a helicopter, and as you might expect, completing a whole assembly required various production processes. The project involved the typical design, analysis, testing, and manufacturing of components.
Each step was highly costly, and a substantial amount of workforce was necessary to complete the project. We had sufficient workforce and expertise for the design and analysis phases. Still, to fully execute the manufacturing phase, which required processes such as sheet metal, forging, CNC machining, casting, coating, and so on, we would need to hire more experts in each of those manufacturing fields and purchase equipment for each field. The capital expenditure was very high.
Therefore, we could significantly reduce expenses if we outsourced most manufacturing tasks rather than performing them in-house. So 60–70% of the manufacturing processes were outsourced, resulting in cost savings because we did not need to purchase the majority of the equipment nor hire the workforce. We were able to save initial capital expenditures and tap into the already existing expertise in each of these fields.
- Implementing Continuous Improvement Practices
Adopting a culture of continuous improvement is vital for achieving cost savings in low-volume production. Methodologies such as lean manufacturing or Six Sigma focus on eradicating waste, reducing defects, and increasing overall efficiency. Organizations can achieve sustainable cost reductions over time by encouraging employee involvement and empowering them to identify and address process inefficiencies. Continuous improvement practices enable companies to optimize their operations, streamline workflows, and make incremental changes, leading to significant cost savings.
Learn more about lean manufacturing here: Design for (Lean) Manufacturing.
Pro-Tip: Set up a continuous improvement team within your organization and have personnel from the various processes you utilize submit requests to the continuous improvement team to review. Reward the best or most impactful ideas with gift cards or some other form of compensation/recognition.
- Negotiating Favorable Supplier Agreements
Establishing favorable supplier agreements is a crucial aspect of cost reduction in low-volume production. Negotiating lower prices, good payment terms, and longer-term contracts can support organizations in securing cost advantages. Building solid relationships with suppliers and exploring opportunities for joint process improvement and collaborative cost-saving initiatives can further enhance the overall value chain. By working closely with suppliers, businesses can identify areas for cost reduction, negotiate better terms, and foster partnerships that drive mutual cost savings.
- Value Engineering
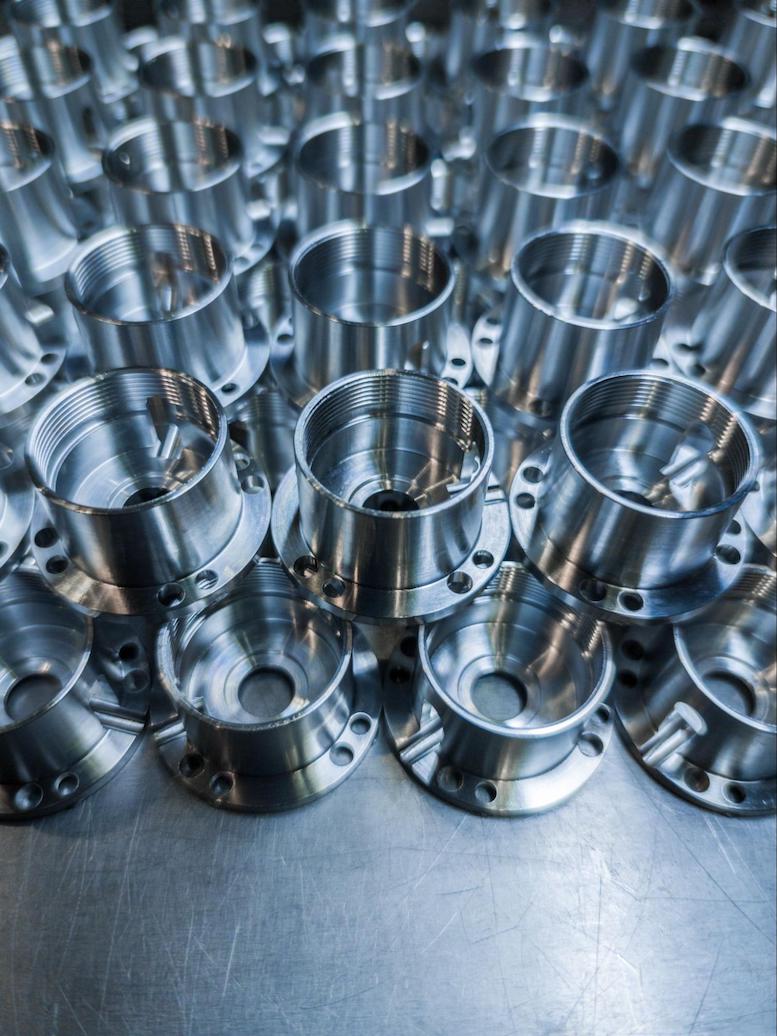
Value engineering involves analyzing the design and functionality of a product to identify opportunities for cost reduction without compromising its performance or quality. This is typically performed during a preliminary design phase. Businesses can find alternatives by reviewing the product’s specifications, materials, and manufacturing processes.
For example, in low-volume manufacturing, you can perform value engineering analyses to look at the manufacturing methods you use for your parts. You may choose manufacturing methods, like 3D printing, to reduce the capital investment you have to make upfront for things like tooling. This type of change may result in a shift in the part’s design, but you should be able to maintain functionality.
At Fictiv, engineers like myself love to help our customers optimize their designs. We often review designs for potential areas of design optimization, such as material change, tolerance relaxation, etc. We have been able to partner with our customers to drop production costs in the past.
Low-volume production poses unique challenges for businesses aiming to optimize processes and reduce costs. However, by implementing the strategies discussed in this article, organizations can successfully navigate these challenges and achieve sustainable cost reductions without compromising quality.
Each organization should assess its needs, capabilities, and constraints to identify the most relevant areas for cost optimization and develop a tailored approach. It is essential to recognize that cost-cutting measures should not compromise quality standards. Organizations should strive to balance cost reduction and delivering products that meet or exceed customer expectations.
By embracing these cost-cutting strategies and continuously evaluating and improving their processes, businesses can achieve long-term success in low-volume production while optimizing costs and maintaining high quality standards.
Quick FAQ:
What are some ways to cut costs for low-volume production?
Streamlining processes, optimizing inventory management, leveraging technology and automation, outsourcing non-core activities, implementing continuous improvement practices, negotiating favorable supplier agreements, supporting value engineering, focusing on energy efficiency, driving waste reduction, implementing cross-training and workforce-optimization programs, championing standardization and modular design, and investing in research and development are all practical approaches to cutting costs in low-volume production scenarios.
What are the benefits of cutting costs in low-volume manufacturing?
By adopting these strategies, businesses can enhance their ability to reduce costs, improve efficiency, and maintain competitiveness in low-volume production.
Fictiv: Your Low-Volume Manufacturing Partner
If you want to source low-volume manufactured parts, look no further than Fictiv. The traditional way to source custom mechanical parts has roadblocks and bottlenecks. At Fictiv, we make it simple. Say goodbye to hours and weeks spent getting quotes and tracking orders from hundreds of vendors via fragmented systems. Fictiv is your gateway to global manufacturing through a single, easy-to-use platform. We offer a wide range of capabilities — tight tolerance CNC to multiple surface finishes to 3D printing — to speed up your development cycles and get the high-quality parts you need at unprecedented speeds.
Create an account and upload your design today!