Time to read: 6 min
To compete in an evolving manufacturing industry, it’s important to evaluate new techniques and technologies that aim to improve productivity. One such technology is machine-tending CNC robotics. CNC robot systems are widely used in the automotive and FMCG (fast-moving consumer goods) industries due to the productivity gains they provide.
Machine-tending CNC robots have, until recently, been prohibitively expensive, but they’re becoming cheaper as more players enter the market. This article will describe what machine tending is and how to automate it, then discuss applications of machine tending and the advantages/disadvantages of these systems.
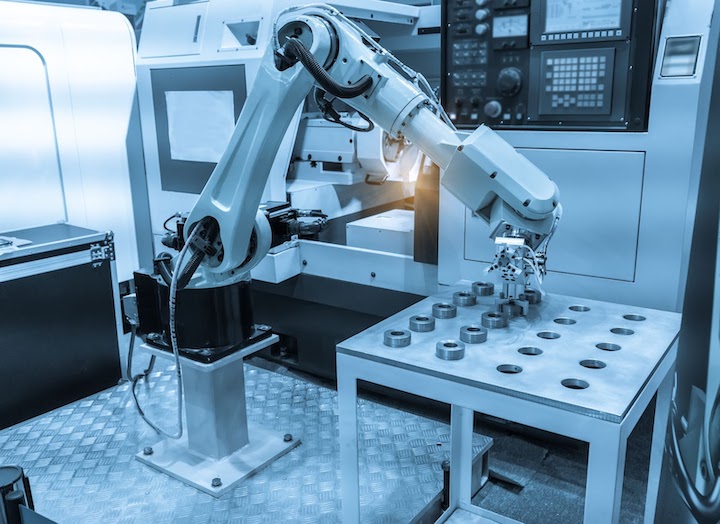
What is Machine Tending?
Machine tending, in the context of CNC operations, often refers to the process of loading raw material into and unloading completed parts from a CNC machine. Ordinarily, these actions are performed by the human operator, but that means the employee needs to be present for the entire production cycle. This can be expensive, time-consuming, and tedious for operators.
When it comes to large-quantity production runs, cycle time becomes critical since any wasted time is compounded by starting and stopping production at shift end, for example, which is reduced because the CNC machine tending robots don’t switch shifts or have to stop for breaks. This wasted time can mean the difference between meeting or missing an important deadline while also increasing the cost per part — which is why machine-tending CNC robots are so effective at improving overall productivity and profitability.
Applications of CNC Robotics for Machine Tending
CNC robots have a wide range of potential applications:
- Picking: Raw material can be collected from either a structured tray or rack or, if the robot has a suitable vision system, from an unstructured bin. Robotic vision systems are becoming more popular but are not yet 100% accurate.
- Door Opening: Not all CNC machines have automated doors. A CNC robot can be programmed to open the door to add or remove materials, saving the operator precious time.
- Placing & Removing: Raw material can be precisely placed into an automated vise inside the CNC machine. After machining, the part is removed from the vise by the machine-tending robot — this works best with simple fixturing.
- Tool Changing: While integrated automated tool changers are available for most CNC machines, robotic arms can also be used to swap out tools. And a robot arm can be a better financial choice if you use it for multiiple tasks — the CNC robot can perform many operations whereas a tool changer can only change tools.
- Cleaning: Once the part is removed from the machine, it can be placed into an automatic part cleaner and/or drier to remove any metal residue, lubricants, or coolant.
- Post Processing: Some parts may need to be deburred or polished after machining, which can be performed by a robot. CNC-tending robots offer more consistency and precision than human operators.
- Basic Assembly: The tending robot can place newly machined parts directly into the assembly where they belong. This reduces assembly time and eliminates the need for human hands in the assembly process.
Parts of a Typical Machine Tending System
Now that we understand the functions a machine-tending CNC robot, lets review these robots’ components. Machine-tending CNC robots are relatively simple in terms of their components, and each is described in more detail below:
Robot Arm
The robot arm is the core of any machine-tending automation system. Robot arms can either be collaborative (cobot) or traditional. Traditional robots can be hazardous to humans in their operational space, so safeguards must be constructed around them.
Collaborative CNC-tending robots, on the other hand, don’t need to be enclosed behind safety barriers and can operate near humans with minimal risk. They’re designed to sense any human presence and stop if there is a collision risk. They’re also programmed using visual scripting, which makes them significantly easier to set up when compared to traditional robot-arm systems. Some key considerations when selecting a robot arm are:
- The required payload capacity
- The reach of the arm
- Ability to precisely repeat placement actions
- The degrees of freedom available on the robot arm
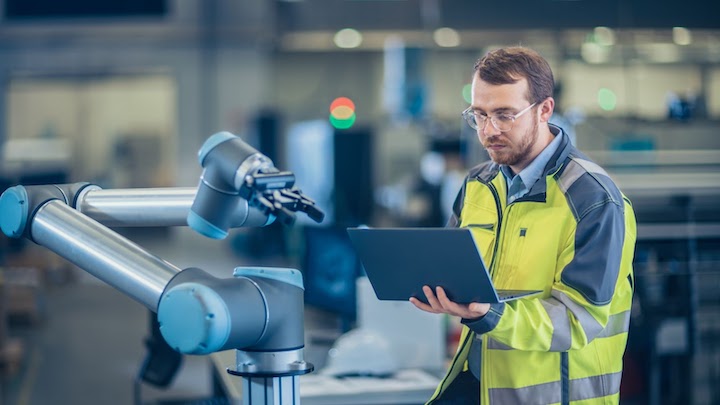
Gripper
The gripper, or end-effector, is used to grip onto the raw material and finished part. Different gripper designs are available, and your choice should account for current and potential future part geometries. Key considerations when selecting a gripper are: the stroke of the gripper fingers, the grip force, and how many gripper mechanisms are available.
Multi-gripper setups significantly reduce cycle time, as the CNC robot can pick up raw material in one gripper, open the machine, remove any previously finished part with the other, and place more raw material into the machine. This allows the arm to perform both the unload and load operations in one motion.
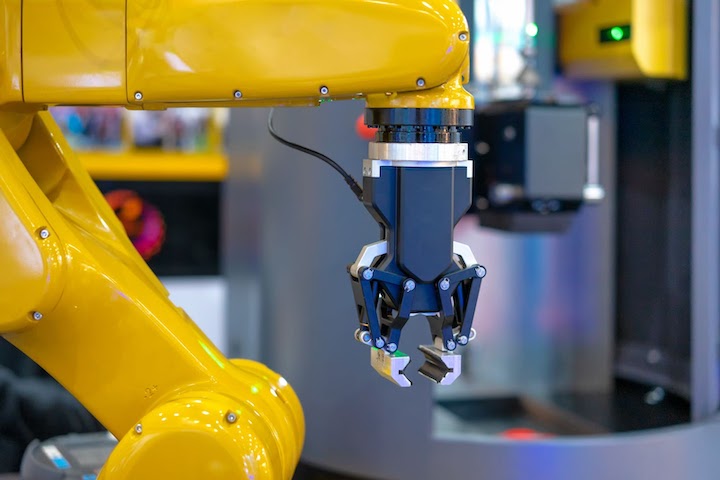
Figure 3: Robot Gripper
Vision System
Many machine-tending CNC robots can accept attached vision systems. These systems can be purely vision based or may incorporate 3D scanning systems to more accurately define the shape of the part being handled. Vision systems allow for improved flexibility. For example, raw materials can be supplied in an unorganized bin, and the vision system can scan the bin’s contents and choose how best to collect the raw material. This removes the requirement for humans to load a structured tray system and ultimately reduces the cost per part.
Automated CNC Vise
To incorporate a machine-tending system into an existing CNC cell, an automated CNC vise is required. Such a vise automatically grips the raw material when the robot arm has positioned it and releases the finished part once it has been gripped by the robot.
Advantages of CNC Robotics for Machine Tending
Machine-tending CNC robots are becoming more popular because they add so much value to most operations, and these are some of the advantages of CNC robotics:
- Reduced Cycle Times: One of the main benefits of using robotics for CNC machine tending is reduced cycle time. Processes can be completely automated and optimized to minimize the time between loading and unloading operations.
- Lights-Out Manufacturing: Being able to turn the factory lights off and know that parts will continue being made is the dream of every owner. The machines generate profit while the employees sleep. CNC robotics make this possible as they will continue to perform the required actions without deviating or tiring.
- Predictable Lead Times: CNC robots can meet KPIs with remarkable consistency. If the tending system can produce 100 parts per hour, its pace is unlikely to change as long as it has access to enough raw material. This means that you can quote precise lead times.
- Labor Reassignment: Robotics are often met with hostility due to the assumption that they will replace humans. However, it usually means that workers are reassigned to tasks such as programming parts, R&D, and workflow optimization. Loading and unloading tasks are tedious, low-value activities.
- Maximize Machine Tool Utilization: A CNC machine must be running to make money. So, every second it’s not cutting material is a waste of potential revenue. CNC robotics lets you maximize machine utilization so your equipment experiences as little downtime as possible. And one CNC robot can tend two machines, which reduces the payback period of the robot while also increasing production and revenue.
Disadvantages of CNC Robotics for Machine Tending
Despite the many advantages, there are disadvantages that you should understand before deciding to invest in machine-tending CNC robots:
- High Cost: CNC robots have become cheaper and more accessible, but the cost is still prohibitive for many companies. And, their integration must be carefully planned in light of production volumes and training costs.
- Integration: It can be difficult to integrate a CNC robot with an existing CNC machine because they may have incompatible communication protocols that requires custom programming to overcome.
- Complexity: While newer collaborative CNC robots have reduced the barrier to entry, it’s still challenging to fully optimize these systems — and the price tag makes failure expensive.
- Safety: Collaborative robots have essentially eliminated the dangers of using CNC robotics around humans. However, larger, more traditional systems must be completely enclosed to avoid dangerous situations.
- Limitations: CNC robots excel at repetitive tasks, but are less effective in operations where production and products see many changes. In such situations, it may be cheaper to use a human operator to load material and remove finished parts.
Leverage Fictiv’s Automated Partners
Implementing robotic automation systems into existing manufacturing plants is an excellent way to boost productivity and increase profits. However, these systems can be costly and are not the best solutions for everyone. Alternatively, you can make use of Fictiv’s large network of world-class manufacturers who already have implemented these systems; you gain the benefits without the capital investment. To learn more about Fictiv and their CNC machining services, create an account and then click on the “Get Instant Quote” button.