Time to read: 5 min
Post-processing improves the properties of plastic injection molded parts so that they are ready for end-use. It includes corrective actions that remove surface defects and secondary processes for decorative or functional purposes. For example, post molding operations can remove excess material (known as flash) or apply part numbers.
As its name suggests, post-processing always occurs after injection molding is complete. It adds costs, but these costs may be less than what you would pay by using more expensive tooling or materials. For example, painting parts after molding may cost less than using an expensive colored plastic.
With injection molding, there are six common types of post-processing activities.
- Gate Trimming
- Painting
- Laser Marking
- Pad Printing
- Heat Staking
- Ultrasonic Welding
Within each process, there may be variations. For example, there is more than one way to paint injection molded parts. By understanding all of your options, you can choose the right post-processing for your next project.
Gate Trimming
Flash mars the finish of molded parts and can interfere with sealing, sealing, and assembly. Typically, this surface defect occurs when excess plastic is forced from a mold cavity at the parting line or ejector pin locations. Quality tooling limits the amount of flash that is created, but gate trimming may still be needed as a secondary operation.
Gates are openings that allow the molten plastic to enter the mold cavity. Although most of this plastic solidifies inside of the cavity to form the part, some material solidifies at the gates and protrudes. Gate trimming, or degating, removes these protrusions either inside the injection molding machine or after part has been ejected.
Painting
Painting is a form of post-processing for plastic injection molding that adds colored coatings to molded parts. Injection molders can use colored plastic instead, but pigmented polymers tend to be more expensive. In-mold painting is another option but may not be as cost-effective as painting after the fact. Coatings that provide shielding against electromagnetic interference (EMI) are also considered to be post-process painting.
Typically, however, plastic injection molded parts are painted for decoration or to hide surface defects. Prior to painting, cleaning or sanding may be required so that the paint will more readily adhere. Plastics with low surface energy, such as polyethylene and polypropylene, require plasma treatment instead. This process increases surface energy so that there is a stronger molecular attraction between the paint and the plastic. Plasma treatment is cost-efficient, especially in comparison to deep cleaning.
There are three parts-painting methods.
- Spray painting is the simplest process and can use self-curing paints that air-dry. Two-part paints that cure with ultraviolet (UV) light are also available.
- Powder coating applies a powdered plastic and requires UV curing to ensure surface adhesion and to help avoid chipping and flaking.
- Silk screening is used when parts need two different colors. For each color, a screen is used to mask, or hide, the area that should remain unpainted.
With each of these processes, it’s possible to achieve virtually any color in a gloss or satin finish.
Laser Marking
Laser marking is a fast, tool-less process that can eliminate the need for surface preparation while imparting high-resolution effects to plastic injected molded parts. Like painting, it provides an alternative to in-mold painting and mold-in graphics, both of which apply decorative effects during the injection molding process.
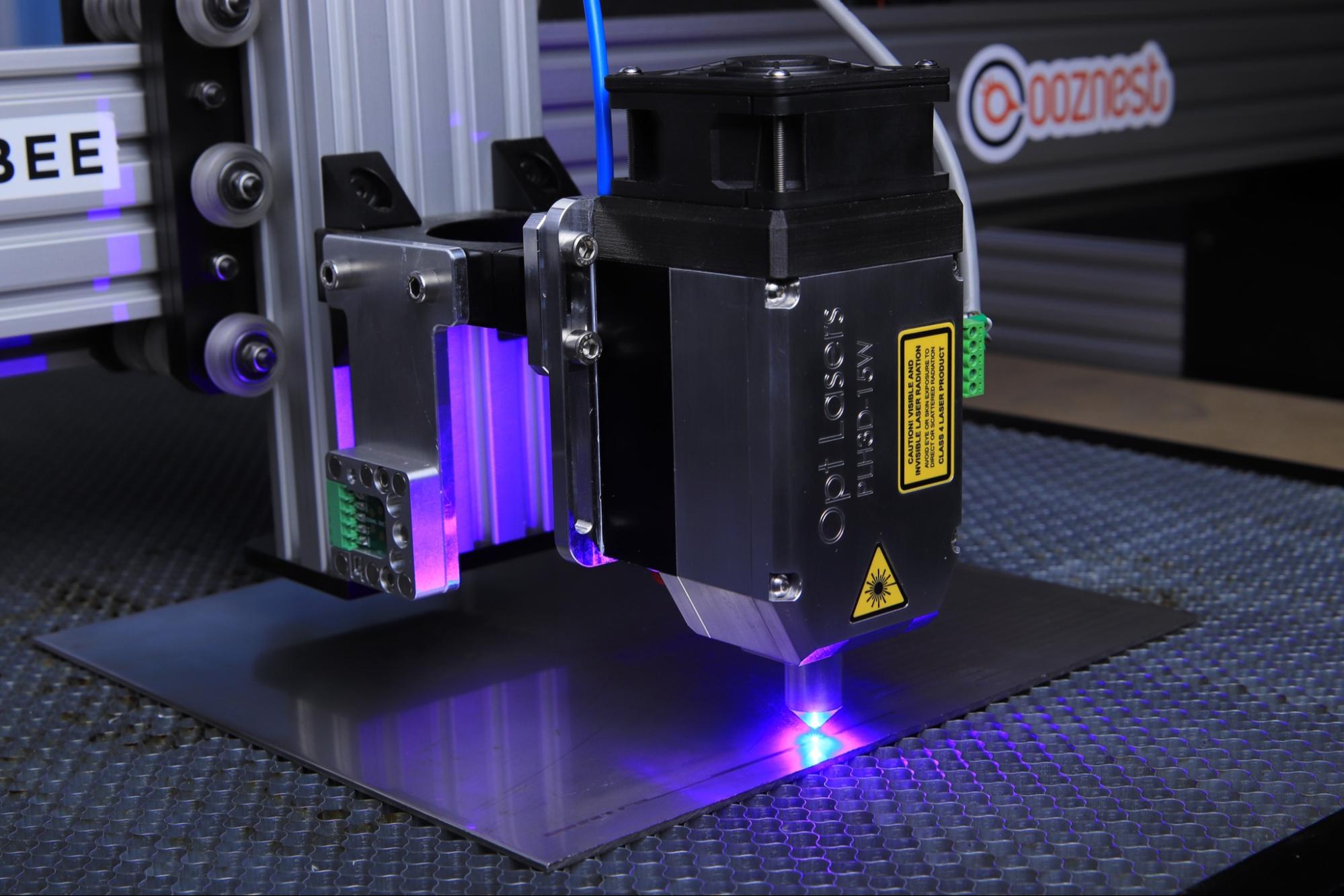
During laser marking, injection molded plastics undergo visible surface changes made by a solid-state pulsed laser. For crisp, clear markings, the light from the laser needs to have a wavelength that the molded plastic will absorb. Often, laser marking is used to produce logos or apply unique identifiers to parts that require traceability. Examples include medical devices and aerospace parts.
Because the term “laser marking” is sometimes used to describe several different laser technologies, it’s important to discuss your requirements with your service provider. Traditionally, laser marking refers to the process of producing surface discoloration in black or gray to create letters, numbers, or logos. Laser marking provides an alternative to conventional printing but is not suitable for plastics that resist color changes.
Pad Printing
Pad printing is a conventional marking process that transfers a two-dimensional (2D) image onto a three-dimensional (3D) object. First, a transfer pad is pressed onto an ink-filled plate that has been etched with the desired image. The inked pad is then placed over the injection molded part and pressed against the part’s surface to transfer the ink and apply the image.
Pad printing can be used on irregular shapes or surfaces. It’s ideal for transferring detailed images and provides good print quality. Quick-drying inks speed processing times and help to avoid problems with dripping, running, or smearing that can occur when ink is applied. Transfer pads and inks are subject to airborne contaminants, however, so quality assurance is a critical part of the process.
As a form of offset printing, pad printing can be used to add single-color or multi-color graphics and lettering to a wide range of plastic materials. Applications include toys, sporting goods, and housings for electronics and appliances. Although pad printing equipment varies, most machines have an ink cup, shuttle, and transfer pad. Process automation supports higher volumes.
Heat Staking
Heat staking installs metal inserts into plastic bosses and housings. Typically, these inserts are threaded to support the use of screws during product assembly. With thermoplastic staking, as this process is sometimes known, heat is applied to the metal insert so that the plastic softens as it is pushed into the part. Like the injection molding process itself, heat staking melts the plastic at a specific temperature and pressure to achieve optimal fill.

Applications for heat staking include joining molded plastic housings to printed circuit boards (PCBs). This assembly technique is also used with the plastic bosses in automotive door panels. In addition, there are applications for heat staking with consumer appliances such as coffee makers. For almost any type of plastic, thermoplastic staking can produce strong joints. Its low insertion force also supports the use of metal inserts with thin plastics that could split or shatter.
Ultrasonic Welding
Ultrasonic welding is a joining process that uses high-frequency ultrasonic acoustic vibrations to create a solid-state weld between two pieces of plastic. An ultrasonic horn vibrates between 20,000 and 40,000 times per second while maintaining slight contact with the plastic. This vibration produces friction and, in turn, enough heat to melt the plastic. To ensure that parts don’t move as they cool, a clamping force is applied for a specific hold time.
Like heat staking, ultrasonic welding provides an alternative to insert molding, the process of molding a plastic around a non-plastic part. Whether vibrations or heat are used to melt the plastic, the softened resin flows into voids and then hardens to form a firm bond with the insert itself. Often, ultrasonic welds are used in medical devices because they eliminate the need for chemical solvents and adhesives that may raise biocompatibility concerns.
Preparing for Post-Processing
Post-processing for plastic injection molding is the last part of the production process. However, that doesn’t mean you have to wait until the end of your design process to consider flash removal, painting, laser marking, pad printing, or whether to handle threaded inserts with heat staking or ultrasonic welding. In fact, thinking about post-processing sooner rather than later could save you time and money in the end. Fictiv wants to help you with your next molding project, and our experts can help figure out which type of post-processing is right for you! Contact Fictiv for a quote today.