Time to read: 7 min
3D printing, also known as additive manufacturing, has long been recognized for its capabilities in prototyping. However, can it also be used for mass production? The answer is yes—recent advancements have enabled 3D printing to transition into higher-volume manufacturing. Nonetheless, it is important to note that it may not always be the best choice.
This shift towards mass production is driven by innovations that address the traditional limitations of 3D printing, such as slow production speeds, high costs, and material constraints. As companies seek more agile and cost-effective manufacturing solutions, 3D printing is becoming a viable alternative to traditional methods like injection molding, CNC machining, and die casting.
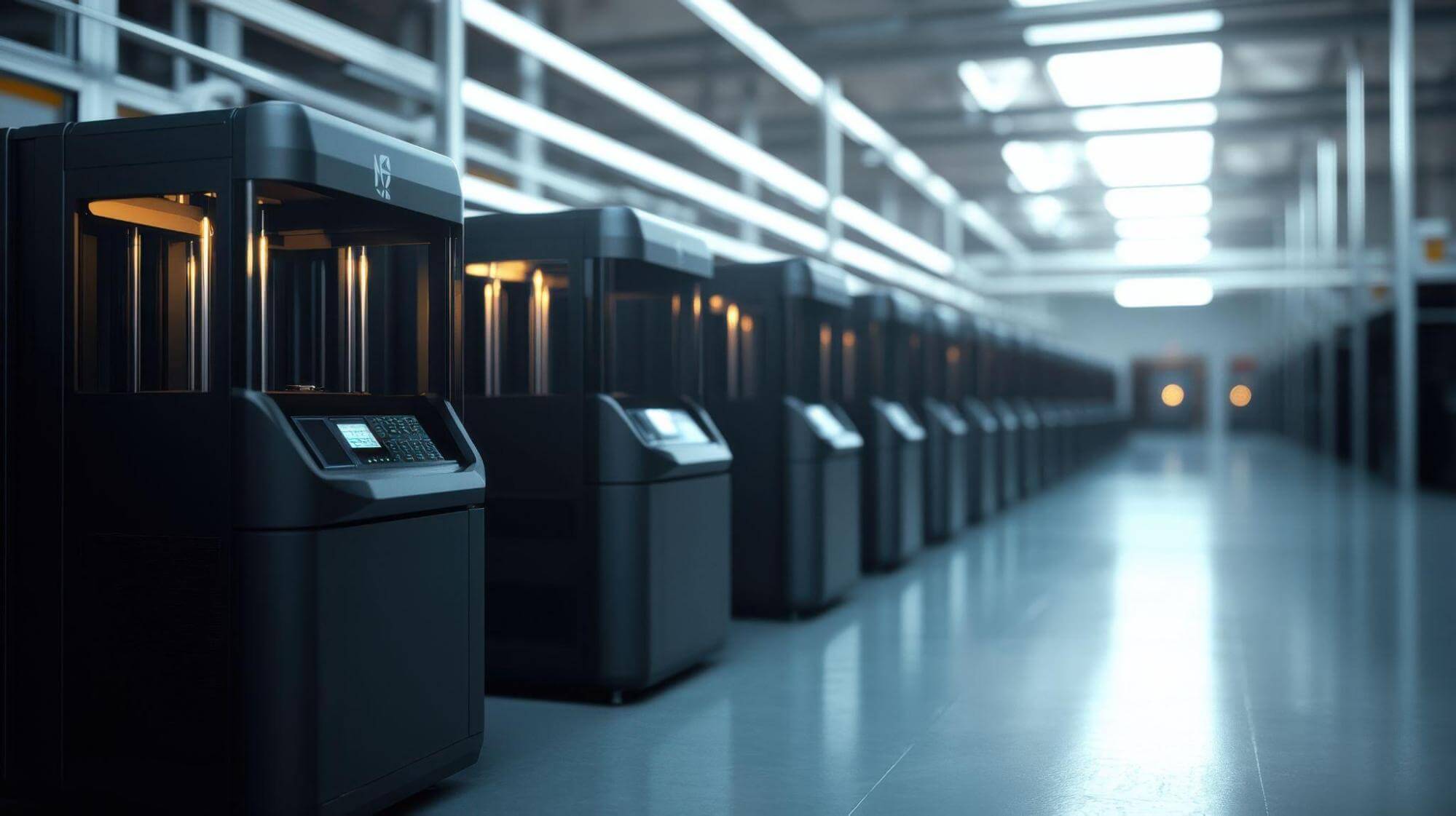
If you are thinking about scaling up your 3D-printed parts for larger-volume production, it’s important to evaluate the strengths and limitations of 3D printing to see if it suits your production needs. This article will help you assess the evolution of 3D printing for mass production, compare it with traditional manufacturing techniques, and explore real-world applications that demonstrate its advantages and challenges.
How 3D Printing Is Scaling for Mass Production
Traditionally, 3D printing has faced limitations that have hindered its adoption for mass production. These include slow production speeds, high cost per part, manufacturing constraints, and limited material options, which make the process less viable than traditional methods.
However, recent advancements are overcoming these challenges to make 3D printing more scalable. Technologies such as Carbon’s Digital Light Synthesis (DLS), HP Multi Jet Fusion (MJF), and Selective Laser Sintering (SLS) have significantly increased print speeds. At the same time, automated 3D printing farms enable continuous production, reducing downtime and improving efficiency.
Furthermore, the development of improved materials has enhanced the strength, heat resistance, and overall functionality of 3D-printed parts, solidifying the technology as a competitive option for large-scale manufacturing.
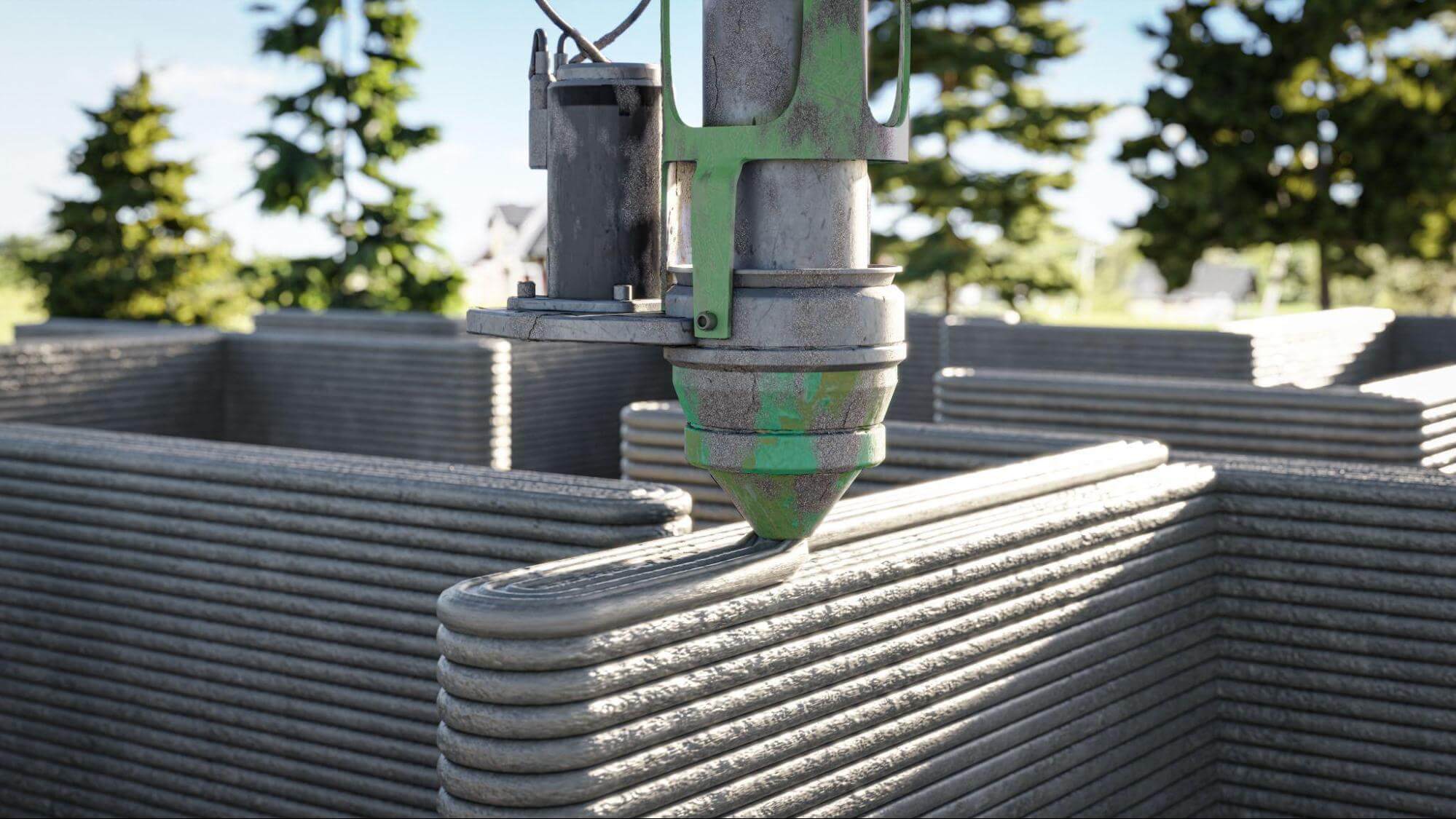
High Volume 3D Printing Production vs. Conventional Mass Production Methods
While 3D printing offers advantages in setup costs and low-volume production runs, it struggles to compete with other conventional manufacturing methods in terms of price per part for larger volume runs. Table 1 below compares 3D printing for production compared to other conventional methods:
Factor | 3D Printing | Injection Molding | CNC Machining | Die Casting |
Setup Costs | Low (no tooling) | High (tooling required) | Medium | High |
Per-Unit Cost | High for large volumes | Low | Medium-High | Low |
Part Production Speed | Moderate | Fast | Slow | Fast |
Material Options | Expanding | Extensive | Extensive | Limited |
Best for | Low-to-mid volumes, complex parts, on-demand production | High-volume standardized parts | Precision metal parts | High-volume metal parts, thin features |
Table 1: 3D Printing vs. Injection Molding vs. CNC Machining vs. Die Casting
Advantages of 3D Printing for Mass Production
No Tooling Costs & Faster Iteration
Traditional injection molding requires an upfront tooling investment that can be costly, and the lead time for fabrication can take weeks to months. Production 3D printing does not require tooling, which enables rapid product development and helps manufacturers remain competitive in their respective markets. However, there are common misconceptions about these factors in injection molding vs. 3D printing worth noting.
Mass Customization
3D printing can create unique products without increasing costs commonly associated with traditional manufacturing methods, such as tooling fabrication and the labor required for machine setup and operation. Some examples of 3D-printed products include Invisalign (for teeth alignment), medical implants, and custom-fit consumer goods.
Lightweight Lattice Structures
3D printing can create stronger yet lightweight designs without the limitations of injection molding. A 3D-printed lattice structure reduces the product’s overall weight while improving its rigidity. These characteristics benefit industries like aerospace, automotive, and footwear, which require strong, lightweight products.
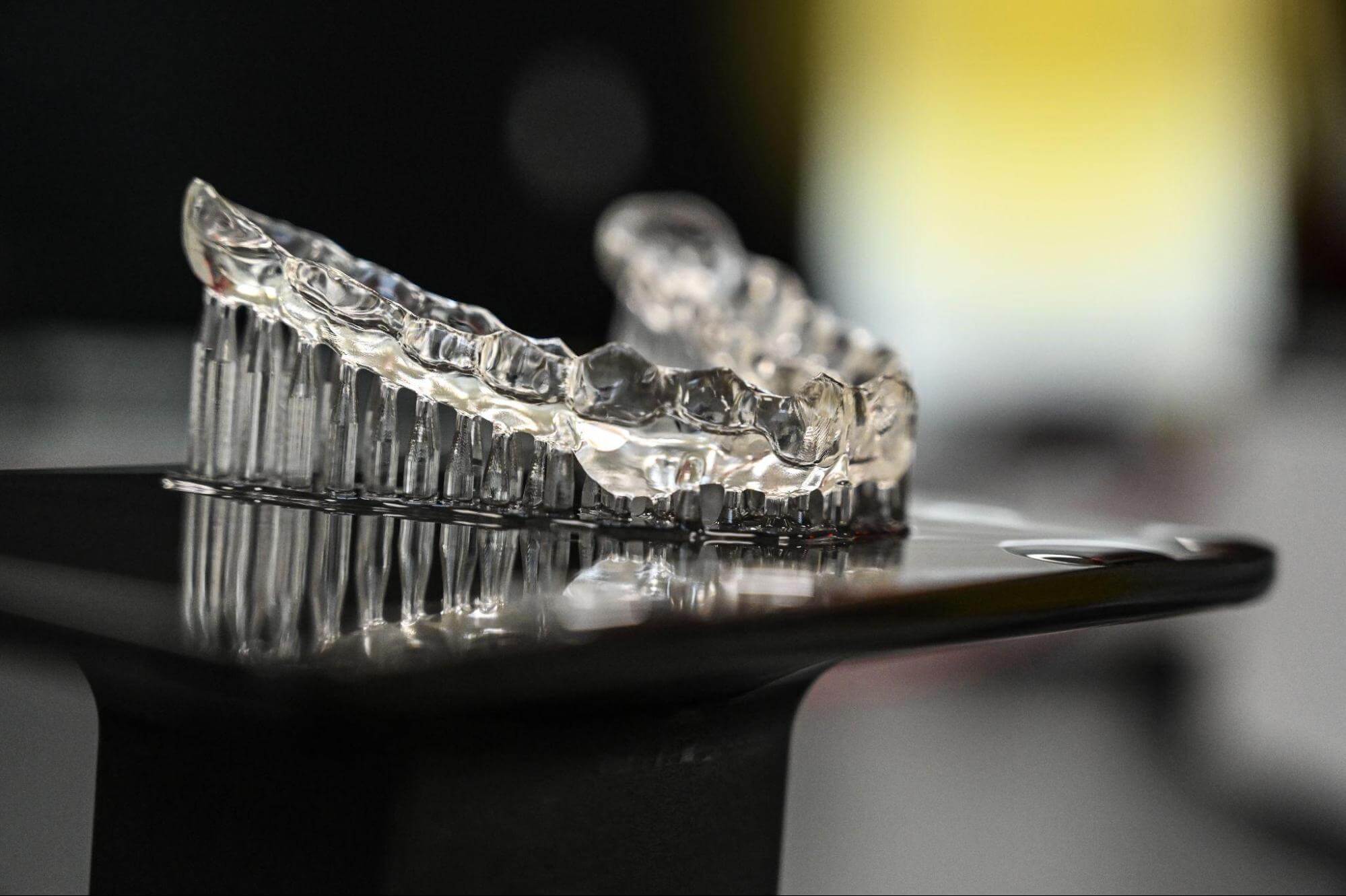
Localized, On-Demand Production
3D printing reduces reliance on overseas manufacturing and warehousing, which helps reduce lead times and machine downtimes while also simplifying inventory. For instance, manufacturers can 3D print spare parts like rollers, bearings, and linking arms.
Challenges and Limitations of 3D Printing for Mass Production
3D printing for mass production is not without its disadvantages and limitations. Listed below are some disadvantages of 3D printing compared to traditional methods.
Cost Per Part vs. Injection Molding
Although 3D printing has become more cost-effective, it remains more expensive than injection molding for large-scale production. You reach a crossover point at a specific volume, which can be as low as 500 parts. When producing more units than this, the cost per part with 3D printing becomes significantly higher due to material expenses and slower production speeds. In contrast, injection molding benefits from economies of scale, where the high upfront tooling costs are offset by extremely low per-unit costs for mass production.
Print Speed & Throughput
One major limitation of production 3D printing compared to more traditional manufacturing is its print speed and overall throughput. Injection molding can produce thousands of parts per hour with multiple cavities, making the process highly efficient for large-scale production.
In contrast, 3D printing is typically limited to batch production, where multiple parts are printed simultaneously at a much slower rate. Advancements in high-speed 3D printing technologies, such as Carbon’s DLS and HP Multi Jet Fusion, are improving throughput, but 3D printing still lags behind traditional methods in high-volume manufacturing.
Material & Mechanical Constraints
Despite significant improvements in 3D printing materials, some 3D-printed thermoplastics still do not match the durability, flexibility, or heat resistance of injection-molded plastics. Certain industries, such as aerospace and automotive, require materials that can withstand extreme conditions, and traditionally manufactured parts continue to have an advantage.
Additionally, post-processing steps such as sanding, coating, or additional curing are often required to achieve the desired surface finish and mechanical properties, which adds time and cost to the 3D printing production process.
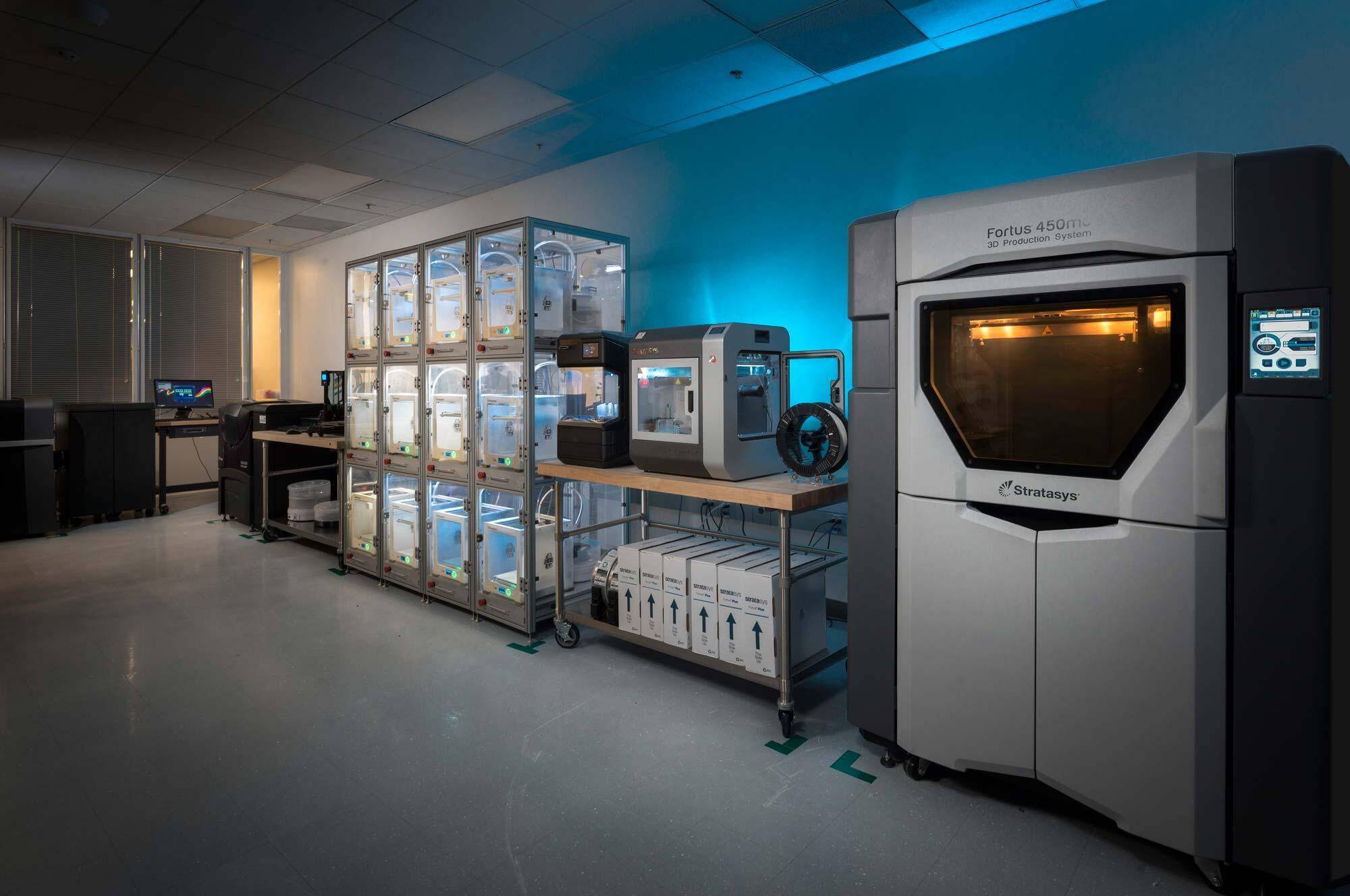
The Role of 3D-Printed Molds in Hybrid Manufacturing
3D printing also plays an essential role in traditional manufacturing by producing molds for injection molding, thermoforming, and casting. One of the primary benefits of using 3D-printed molds is the ability to quickly iterate and refine mold designs without the high costs associated with traditional steel or aluminum tooling. This approach significantly reduces both cost and lead time for early-stage production and makes it ideal for companies looking to test designs before committing to expensive steel molds.
For low-to-medium production runs, 3D-printed molds or castings offer a cost-effective alternative to traditional methods. However, aluminum or steel molds remain the superior option for large-volume runs beyond a certain threshold due to their durability and cost efficiency at scale.

Real-World Case Study: Adidas and Carbon 3D Printing
Adidas leveraged 3D printing and Carbon’s DLS technology to mass-produce midsoles for the Futurecraft 4D shoe line, showcasing the viability of 3D printing in large-scale manufacturing. With Carbon’s DLS technology, Adidas eliminated the need for expensive tooling required in traditional foam molding while also significantly reducing production costs and time.
3D printing also enabled the creation of intricate lattice structures to enhance performance and reduce the overall weight of the midsoles. This innovation allowed Adidas to produce over 100,000 pairs, proving that high-volume 3D printing for mass production is achievable.
This approach has major implications for the future of manufacturing, particularly in customization at scale. 3D printing allows for unique midsoles tailored to individual athletes and accelerates design iteration without the need for new molds, streamlining the development of new product versions.
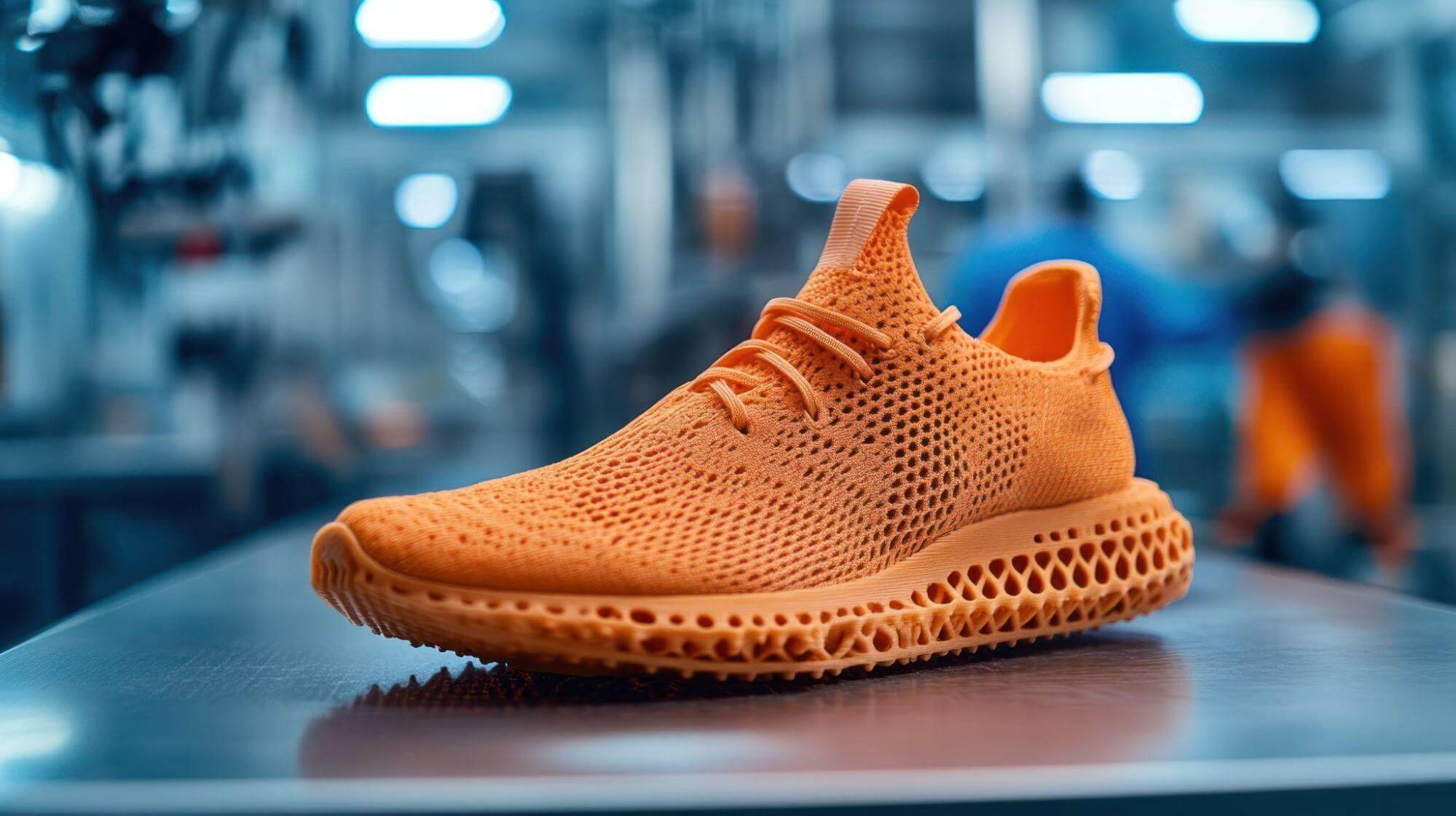
The Future of 3D Printing for Large-Volume Production
Despite its shortcomings compared to other traditional methods for high-volume production, 3D printing continues to grow and advance as a technology. Here are some ways 3D printing will shape the future of high-volume production:
Automation & AI in Additive Manufacturing
Advancements in automation are enabling 3D printing farms to operate 24/7, significantly improving production capabilities. Additionally, AI-driven print optimization is enhancing efficiency by reducing material waste, optimizing print paths, and improving part quality. These innovations are making large-scale additive manufacturing more practical and cost-effective.
Hybrid Manufacturing: Combining 3D Printing with Injection Molding
Hybrid manufacturing is emerging as a viable approach that leverages the strengths of both 3D printing and traditional manufacturing methods. For example, 3D printing is ideal for creating complex geometries that would be difficult or costly to achieve with traditional processes, while injection molding remains the best option for producing standardized parts in high volumes. By combining these methods, manufacturers can achieve greater flexibility and efficiency.
Emerging High-Speed 3D Printing Technologies
Many emerging 3D printing technologies are poised to revolutionize large-scale manufacturing:
- Carbon’s DLS – High-speed production of elastomers and resins, ideal for footwear and medical applications.
- HP’s Multi Jet Fusion (MJF) – Efficient plastic part manufacturing with high resolution and consistency.
- SLS, SAF, and P3 – Advanced powder-based additive manufacturing techniques offering better material properties.
- Desktop Metal’s Production System – High-speed metal additive manufacturing, enabling mass production of metal parts.
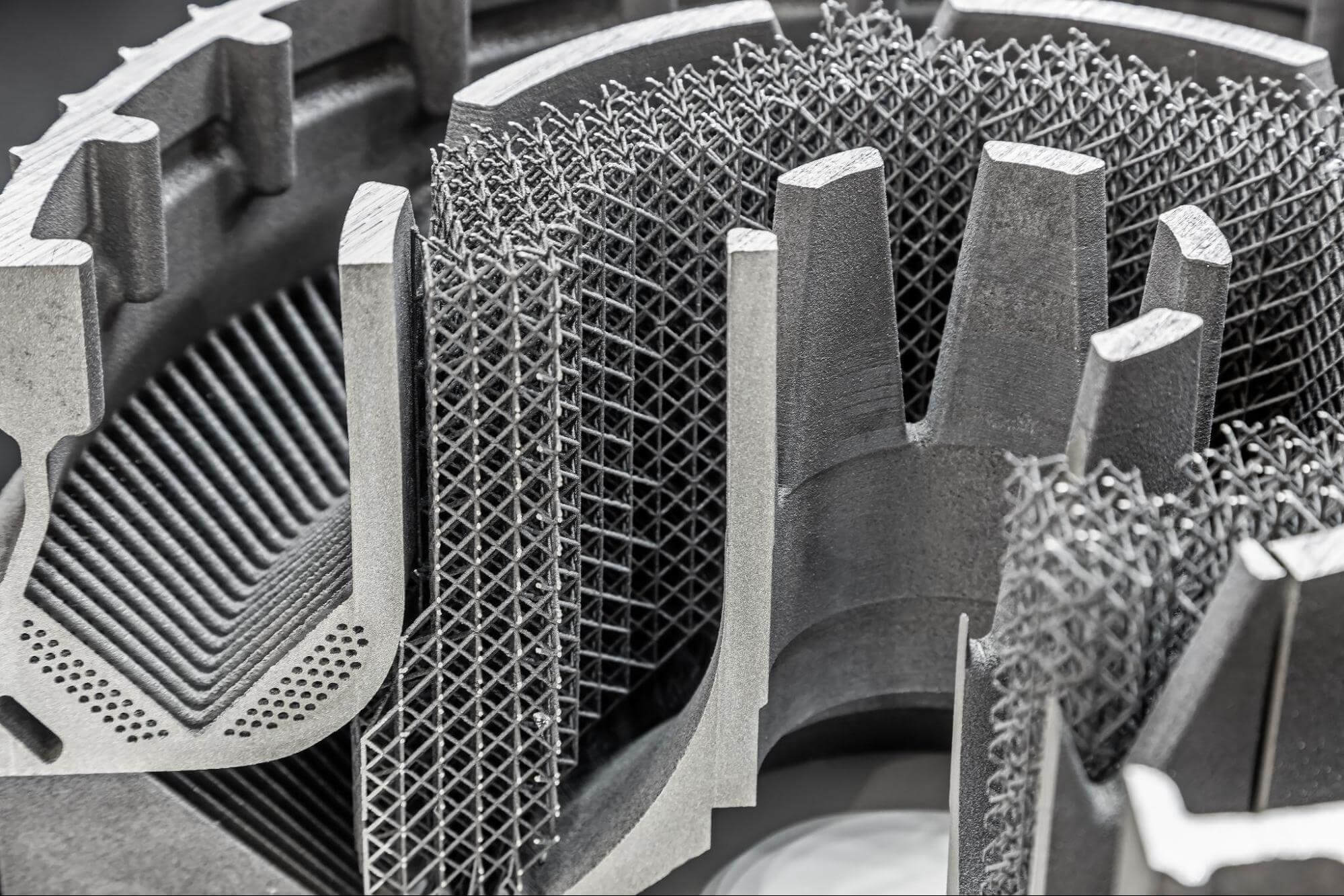
Can High-Volume 3D Printing Replace Traditional Mass Production Manufacturing Methods?
While 3D printing is unlikely to replace traditional methods for higher-volume manufacturing in most scenarios, it is proving to be viable for low-to-mid-volume production. Injection molding and die casting still dominate for producing large quantities of identical parts efficiently.
However, hybrid manufacturing, which combines 3D printing with traditional techniques, offers the best of both worlds. Additionally, 3D-printed molds are bridging the gap between prototyping and full-scale production, making manufacturing more agile and cost-effective. Businesses looking to scale production should consider leveraging 3D printing in cases where it provides a competitive advantage. Fictiv leverages both traditional and additive manufacturing methods to produce high-quality parts. Get a quote today to explore how 3D printing with Fictiv can scale and streamline your production process.