Time to read: 7 min
Most injection molds are made of steel or aluminum. Conventional wisdom holds that steel molds are more expensive, and that aluminum is more cost-effective for lower part volumes. However, that’s not always true – at least if you choose Fictiv for your next injection molding project. There are important differences between different types of steel and aluminum alloys, and there are different ways to build a mold that affect its cost.
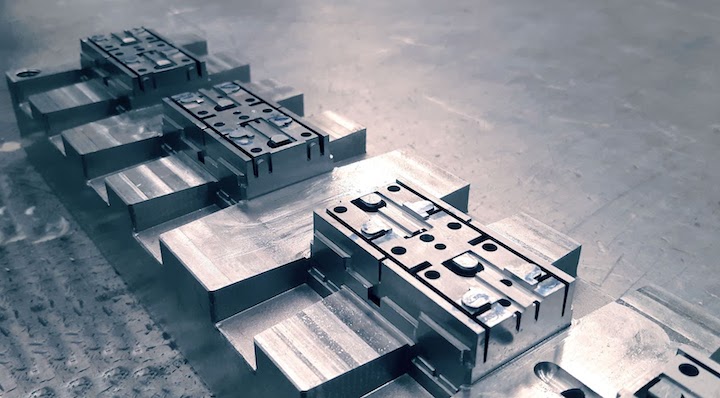
Key Considerations
If you’re designing a part for plastic injection molding, you should ask yourself these two questions:
- How long do you need a new tool to last?
- How many parts do you need the tool to produce annually?
If you don’t know the answers yet, then get them before investing in a tool, which is a major expense for any injection molding project.
Fictiv can help. Our design for manufacturing (DFM) experts have a wealth of injection molding knowledge, including helping you optimize your tooling for your needs. Remember, what looks like a good deal now could cost you more in the end if you don’t have a lot of experience with injection molding tools — especially if you have to replace a tool or aren’t getting high quality parts.
There’s a lot to consider when comparing steel vs. aluminum for injection molds, so I’ll begin with a quick history lesson, then discuss material hardness, machining, welding, processing, mold inserts and tool life.
A Brief History of Steel vs. Aluminum Molds
Throughout much of the twentieth century, steel was the tooling material of choice. During the 1990s, however, the global steel industry entered a structural crisis as the geographic location of steelmaking shifted. Meanwhile, advances in aluminum metallurgy offered a cost-effective substitute for steel molds. Honda America even encouraged its Tier One suppliers to use more aluminum molds for production parts.
During the first decade of the twenty-first century, China became the world’s leading producer of steel, in part because of government subsidies. As these subsidies continued, overproduction resulted and steel prices fell. Chinese steel production has slowed recently, but Chinese steel prices remain competitive despite U.S. tariffs, especially since Western sanctions have removed Russian steel from many international markets. Today, the world’s top steel producers include China, Japan, the United States, and Germany.
Alloys and Hardness
All countries use the same basic steelmaking processes, but German steels tend to be harder and Japanese steels tend to be more flexible due to their alloying ingredients — and Chinese steels have different grades than U.S. steels.
Tool steels from any country are the primary steels used in molds, but there’s also a role for stainless steel in mold bases. Rockwell hardness, a measure of resistance to indentation, provides a standardized way to compare steels and other metals, such as aluminum, that are used in injection molds.
Steel is harder than aluminum, but some grades of steel cannot withstand the higher pressures of more powerful injection molding machines. A mold’s hardness is also critical because harder surfaces support more polishing, finer part finishes, and are more resistant to abrasion and wear. When choosing an injection molding tooling material, it helps to divide steels into soft and semi-hardened steels such as P20 and NAK80, and hardened steels such as H13 and S136.
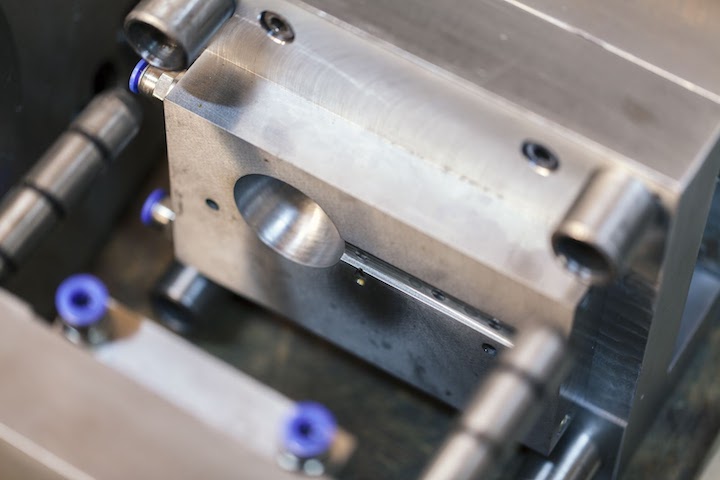
EDM Machining vs. CNC Machining
Fictiv’s Manufacturing Partners make molds from all of these steels (and aluminum) using electrical discharge machining (EDM) or computerized numerical control (CNC) machining. EDM machining uses electrical discharges (sparks) to cut through the metal via two basic processes: wire EDM and sinker EDM. CNC machining uses a sharp cutting tool to remove material.
EDM machining is recommended when sharp internal corners are needed and very deep cuts are required. This cutting method is also a good choice for hard workpiece materials (like tool steels) and for injection molds that require a mirror finish. EDM is not recommended for heat-affected zones (HAZ) where welding occurs, and wire EDM cutting is slower than CNC machining. Sinker EDM is also used for making injection molds since it does not impart stress to the mold material. CNC machining is faster than electrical discharge machining and capable of achieving complex geometries using 5-axis (or greater) CNC mills. Generally, CNC machining is recommended for molds with ribs, even though these features require tooling that is more apt to deflect or break. When making cost comparisons, it’s important to consider the specific type of EDM or CNC machining that will be used. Also, while conventional machining is still used with some injection molds, it’s typically just for small jobs or for mold refurbishment.
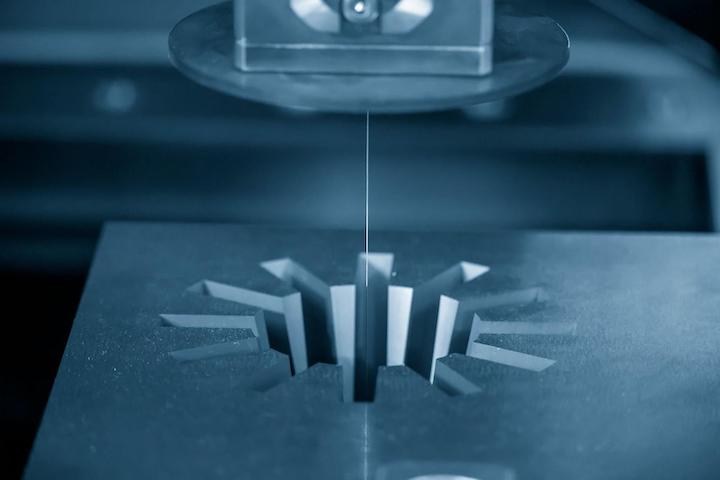
Machining, Welding, and Processing Considerations
Aluminum is easier to shape than steel. Therefore, mold makers can machine and polish aluminum molds more quickly and with less machine time — a key cost driver in mold making. Depending on the specific aluminum alloy, aluminum’s CNC machining rates are between three to ten times faster than steel. EDM machining is usually four to five times faster because aluminum has high electrical conductivity. With its greater thermal conductivity, aluminum also supports simpler and less expensive cooling systems for injection molds.
When a tool requires welding, however, aluminum’s thermal conductivity means that higher heat inputs are required because of the greater heat dissipation. Generally, aluminum welding is regarded as more difficult than steel welding because greater skill and surface cleanliness is required. Additionally, some grades of aluminum are more difficult to weld than others. With a new mold, welding may be needed for any insert sections. During mold repairs, welding is typically used along parting lines and gates.
Aluminum’s properties also have implications for material selection, part volumes, and temperature control. Because it’s relatively soft, aluminum is not suitable for use with abrasive plastics such as glass-filled nylon. Aluminum also tends to wear more quickly than steel, which makes steel a better choice for high part volumes. The comparatively high thermal conductivity of aluminum means that steel is better at maintaining heat during long production runs. In plastic injection molding, temperature control is essential for avoiding problems such as shrinking and warping.
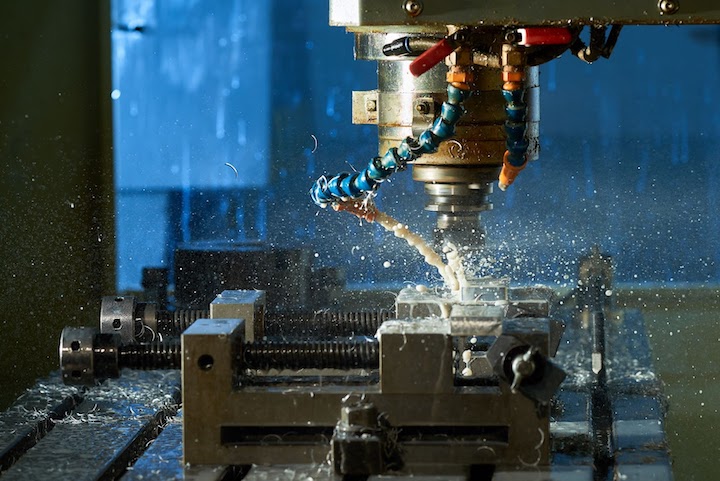
Standalone Molds vs. MUD Inserts
Injection molds include a core and a cavity that are held together in a machine, or press, between metal plates and other mold components. The core is the raised, or convex, part of the mold and contains the part ejection mechanism. The cavity is the recessed, or concave, part of the mold and is filled with molten plastic. The core and cavity are critical in any injection molding project, but part designers have a choice between standalone molds and MUD inserts.
Standalone molds, or free-standing molds, include not just the core and cavity, but all of the other tooling components that are required for plastic injection molding, including the metal plates that provide a framework for mounting the mold within the machine. These additional components increase tooling costs, but the only practical limitation on the size of a part is the size of the injection mold that the machine or press will support.
MUD inserts, or master unit die (MUD) molds, are universal frames that fit into the press and hold a removable insert. They reduce machining costs because the only time that’s spent cutting is for the removable core and cavity. Because a single MUD frame can accommodate different inserts, a molder may be able to use an existing frame for a new project. Part size is limited by the size of the frame, but MUD inserts reduce up-front tooling investments and accelerate project timelines.
Importantly, MUD frames can make steel inserts cost-competitive with aluminum standalone molds. This facilitates the use of steel tooling with prototyping and low-volume injection molding, and dispels the myth that steel molds are always more expensive. Yet, inserts made of aluminum alloys can also be used. Typically, they are made of 7075 aluminum, an alloy that contains zinc. QC-10 high-strength aluminum mold plate is also used in tools, and 6061 aluminum can be used for low-volume bridge tools.
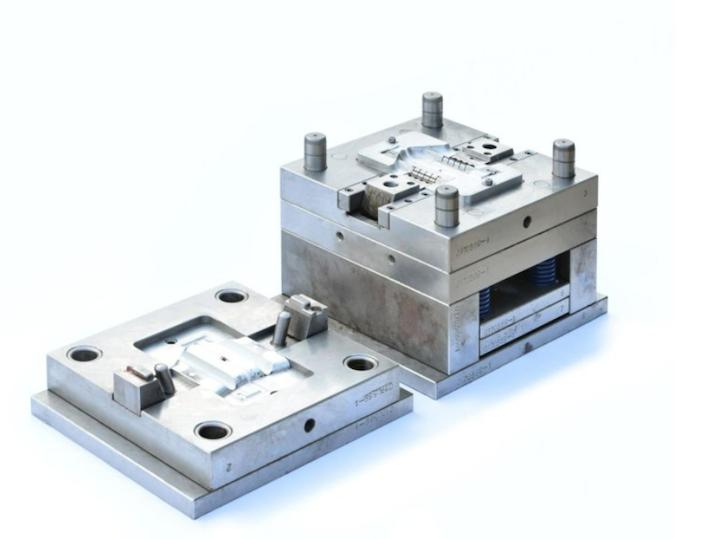
Tool Life
Eventually, all injection molds experience wear. But how soon until the tool wears out and needs to be replaced? Maintenance and refurbishment can extend the life of a tool, but the term “tool life” is often misunderstood. For starters, tool life isn’t about years. What matters are cycles, and you may see the symptoms of mold wear — such as flash along the mold’s parting line — long before the end of the quoted “tool life”. That’s why proper mold maintenance and injection molding are important, but part design is, too.
Draft, a taper that’s applied to the faces of an injection molded part, helps to prevent part damage during ejection and reduces the scraping and wear on the mold itself. Material selection is also a factor in tool wear. For example, super-high-heat thermoplastics such as PEEK have high melting points and because metal expands with heat, the injection molds undergo more compressive stresses. High temperatures can also cause the lubricants that are used with a mold’s moving parts to deteriorate more quickly.
Contrary to conventional wisdom, steel tooling isn’t always more expensive and aluminum tools aren’t always limited to a maximum of 10,000 shots. With the proper mold construction and under the right injection molding conditions, a tool can last for 50,000 to 100,000 cycles.
So, when you’re ready to start your next injection molding project, create a Fictiv account and get expert DFM feedback along with your quote. Our injection molding experts can help you dial in your designs and give you the guidanc eyou need to construct the right tooling for your project.