Time to read: 8 min
Steel comes in many forms: sheet metal, plates, bars and beams of various geometries, pipes, and of course, the solid stock material used when CNC machining steel. Steel is used for so many applications and by so many industries that it makes sense for there to be many different types of steel. But what’s the difference between stainless and low carbon steel? Free machining and tool steel? In this article, you’ll learn about the many machining steel grades, their properties, and how to CNC machine steel successfully.
What is Steel?
Steel is a broad term for an alloy of iron and carbon. The amount of carbon (0.05% – 2%) by weight), along with the addition of other elements, determines the specific alloy of steel and its material properties. Other alloying elements include manganese, silicon, phosphorus, sulfur, and oxygen. Carbon increases the hardness and strength of the steel, while other elements can be added to improve corrosion resistance or machinability. Manganese is also often present in larger quantities (at least 0.30% and up to 1.5%) to decrease the brittleness of the steel and increase its strength.
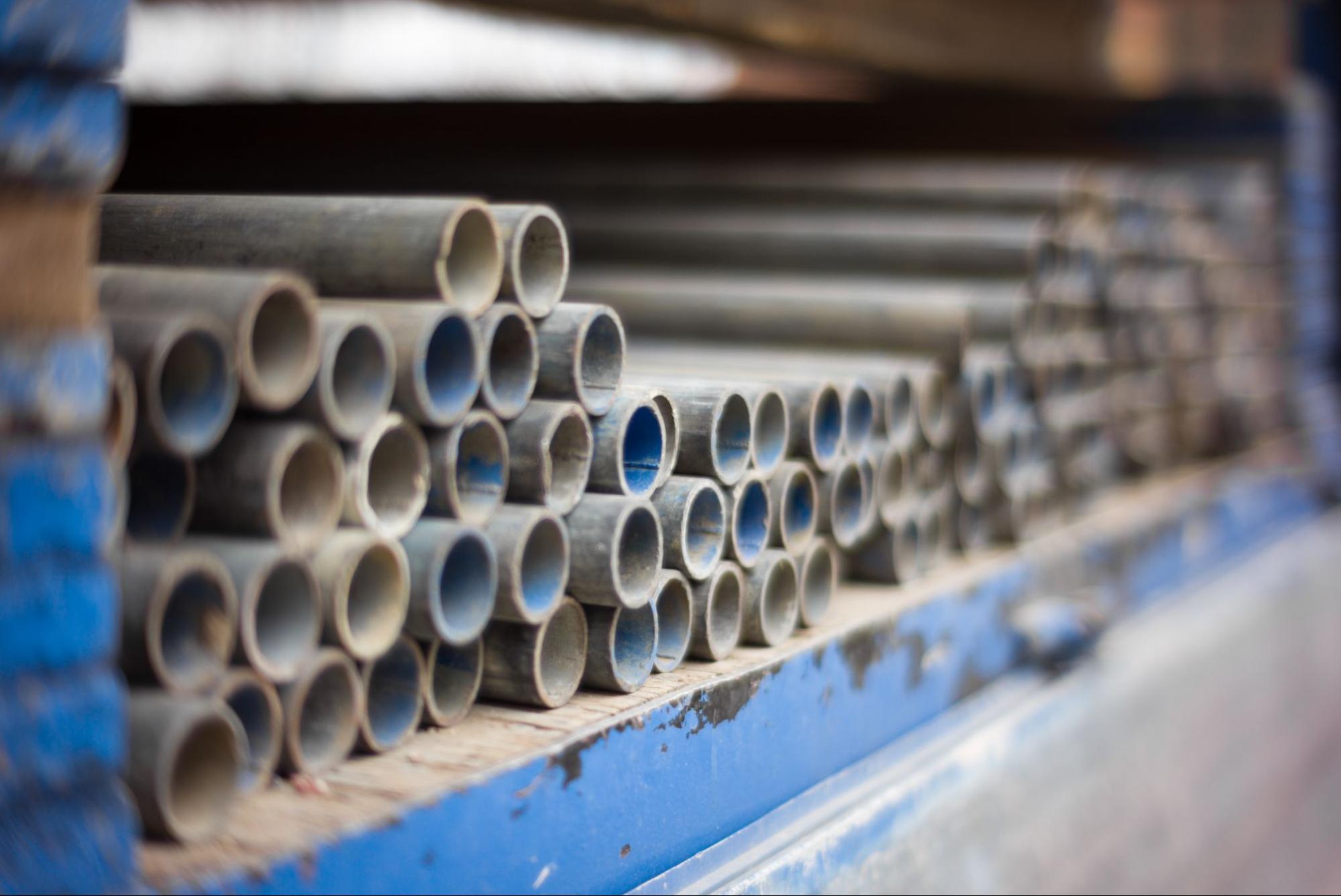
The strength and hardness of steel are some of its most sought-after properties. They’re what make steel suitable for construction and transportation applications because the material can last a long time under heavy and recurring loads. Some alloys of steel, namely the stainless varieties, are resistant to corrosion, which makes them the best choice for parts operating in extreme environments.
However, that strength and hardness also contribute to longer machining times and increased wear on cutting tools. And steel is a high-density material, which makes it too heavy for some applications. However, steel’s strength-to-weight ratio is high, which is why it’s among the most commonly used metals in manufacturing.
Types of Steel
Let’s get into some of the many types of steel. To be considered steel, carbon must be added to iron. The amount of carbon varies though, causing the properties to vary considerably. Carbon steels often refer to steels other than stainless and are identified by the 4 digit grade of the steel, and more broadly as low, medium, or high carbon steels.
- Low Carbon steels: Less than 0.30% carbon (by weight)
- Medium carbon steels: 0.3 – 0.5% carbon
- High carbon steels: 0.6% and above
The main alloying element of the steel is referred to by the first digit in the four-digit grade. For example, any 1xxx steel, like 1018, is going to have carbon as the main alloying element. 1018 steel has 0.14 – 0.20% carbon and small amounts of phosphorus and sulfur, along with manganese. This general-purpose alloy is commonly used to machine spacers, shafts, gears, and pins.

Free machining grades of carbon steel are resulfurized and rephosphorized, which causes the chips to break off into smaller pieces. This prevents long or large chips from becoming entangled with the tool as it cuts. Free machining steel can lead to faster machining times but may decrease ductility and impact resistance.
Stainless Steel
Stainless steel contains carbon, but also contains around 11% chromium, which increases the material’s corrosion resistance. More chromium means less rust! Adding nickel can also increase rust resistance and tensile strength. Additionally, stainless steel has good heat resistance, making it suitable for aerospace and other applications in extreme environments.
Stainless steel is broken down into five types, based on the crystalline structure of the metal. These five types are austenitic, ferritic, martensitic, duplex, and precipitation hardening. Stainless steel grades are identified using three-digit numbers rather than four. The first number represents the crystalline structure and main alloying elements.
For example, the 300 series of stainless steels are austenitic chromium-nickel alloys. 304 stainless is the most common grade and is also referred to as 18/8, for its 18% chromium and 8% nickel content. 303 stainless steel is the free machining version of 304 stainless. The addition of sulfur reduces its corrosion resistance, so Type 303 stainless steel is more likely to rust than Type 304.
Stainless steel can be used in a wide range of industries. Type 316 stainless steel, when processed properly, can be used in medical devices, such as valve components in machines and tubing. 316 stainless is also used to machine nuts and bolts, many of which are used in the aerospace and automotive industries. 303 stainless steel is used for gears, shafts, and other components that are essential for both aircraft and cars.
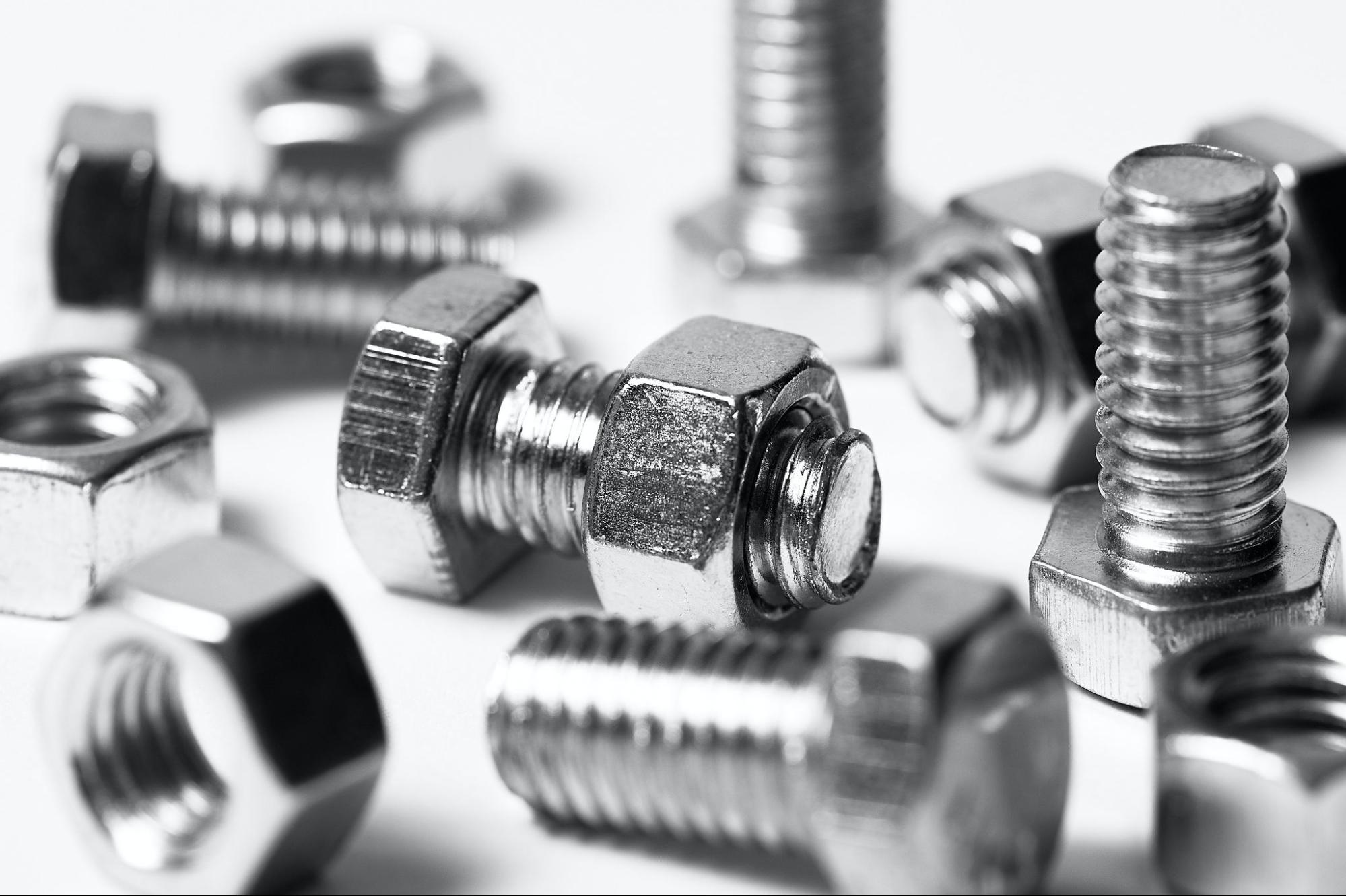
Tool Steel
Tool steel is used to make tools for various manufacturing processes, including die-casting, injection molding, stamping, and cutting. There are many different alloys of tool steel tailored for different applications, but they’re all known for their hardness. Each can stand up to wear and tear over many uses (a steel mold for injection molding can stand up to a million shots of material or more) and have high-temperature resistance.
One prevalent application of tool steel is injection molding tooling, which is CNC machined from hardened steel to produce the highest quality production parts. H13 steel is often chosen for its good thermal fatigue properties — its strength and hardness can withstand long exposures to extreme temperatures. H13 tooling is well-suited for advanced injection molding materials with high melting temperatures because it provides a longer tooling life than other steels – 500,000 to 1 million shots. Meanwhile, S136 is stainless steel that has a tooling life of over one million shots. This material can be polished to the highest level and is used for specialty applications when parts require high optical clarity.
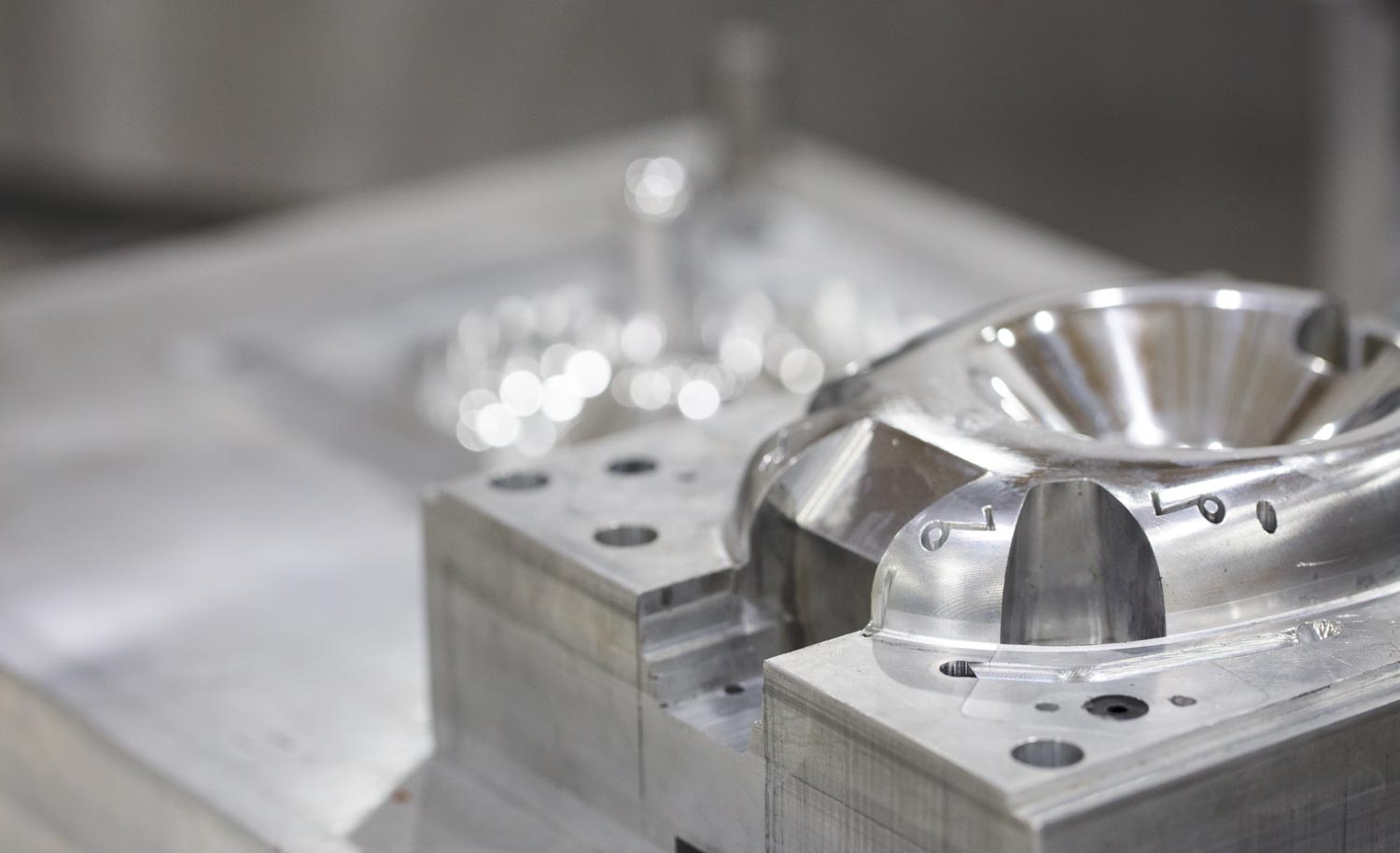
Steel Grade Comparison Chart
The table below shows some common grades of steel and their properties. The elemental makeup of each alloy is provided to show how different grades change with different additives. Keep in mind that each of these grades’ properties can be further manipulated by heat treatment or forming.
17-4 (Type 630) | Type 304 (18-8, stainless) | Type 316 (stainless steel, annealed bar) | 1018 (mild steel, cold drawn) | 1045 (medium carbon steel, cold drawn) | H13 tool steel | |
Density (g/cc) | 7.8 | 8.00 | 7.85 | 7.87 | 7.87 | 7.8 |
Tensile Strength, Yield (MPa) | 1379 | 215 | 240 | 370 | 485 | 1650 |
Tensile Strength, Ultimate (MPa) | 1448 | 505 | 550 | 440 | 515 | 1990 |
Hardness, Rockwell C | 45 | n/a | n/a | n/a | n/a | 28-54 (depending on treatment) |
Hardness, Rockwell B | n/a | 70 | 80 | 71 | 86 | n/a |
Carbon Content | .07% | .08% | .08% | 0.14-0.2% | 0.42-0.5% | 0.32-0.4% |
Manganese Content | 1% | 2% | 2% | 0.6-0.9% | 0.6-0.9% | |
Phosphorus Content | .04% | .045% | .045% | .04% | .04% | |
Sulfur Content | .03% | .03% | .03% | .05% | .05% | |
Chromium Content | 15-17.5% | 18-20% | 16-18% | 5.13-5.25% | ||
Nickel Content | 3-5% | 8-10.5% | 10-14% | |||
Copper Content | 3-5% |
Steel Treatments
Some of the most useful properties of steel come from extra treatment and processing steps. These methods can be done before the machining process, to change the properties and make the steel more machinable. Keep in mind that hardening the material before machining makes for longer machining times and increased tool wear, but steel can be treated after machining to add strength or hardness to the finished product. Which is to say, it‘s important to consider upfront any planned treatments that you’ll need to apply to achieve the necessary properties for your parts.
Heat Treating
Heat treating refers to several different processes that involve manipulating the temperature of the steel to change its material properties. One example is annealing, which is used to decrease hardness and increase ductility, to make the steel easier to work with. The annealing process slowly heats the steel to the desired temperature and keeps it there for a period of time. The time and temperature required depend on the specific alloy, and both decrease as carbon content increases. Finally, the metal is cooled slowly in the furnace or surrounded by an insulating material.
Normalizing heat treatment relieves internal stresses in the steel while maintaining higher strength and hardness than annealed steel. During normalizing, the steel is heated to a high temperature, then air-cooled to obtain increased hardness.
Hardening steel is another heat treatment process that, you guessed it, hardens the steel. It also increases the strength but can make the material more brittle as well. The hardening process involves heating the steel slowly, soaking it at a high temperature, then cooling it quickly by dousing the steel in a liquid like water, oil, or a brine solution.
Finally, the tempering heat treatment process is used to relieve some of the brittleness that comes from hardening steel. Tempering steel is almost exactly the same as normalizing: you heat it up slowly, let it sit at the chosen temperature, then air cool the steel. The difference is that tempering is performed at a lower temperature than the other processes, which decreases both the brittleness and the hardness of the tempered steel.
Precipitation Hardening
Precipitation hardening increases the yield strength of steel. Certain grades of stainless steel may include PH in the name, meaning that they have precipitation hardening properties. The main difference of precipitation hardening steels is that they have extra elements: copper, aluminum, phosphorus, or titanium. Many different alloys are possible here. To activate the precipitation hardening properties, the steel is formed into the final shape, then put through an age-hardening process. The age-hardening process heats the material over an extended period to cause the added elements to precipitate — form solid particles of different sizes — which increases the strength of the material.
17-4PH (also known as 630 steel) is a common example of a precipitation hardening grade of stainless steel. This alloy has 17% chromium and 4% nickel, along with 4% copper to contribute to the precipitation hardening. Because of the increased hardness, strength, and high corrosion resistance, 17-4PH is used for helicopter deck platforms, turbine blades, and nuclear waste casks.
Cold Working
The properties of steel can also be changed without applying high amounts of heat. For example, cold working steel makes it stronger through the process of work hardening. Work hardening can occur when a metal undergoes plastic deformation. This can be done intentionally by hammering, rolling, or drawing a metal. Work hardening can also happen unintentionally while machining if the cutting tool or workpiece gets too hot. Cold working can also increase the machinability of steel. Low carbon steel is well suited to cold working.
Steel Design Considerations
When designing steel parts, it’s important to remember the material’s unique properties. The very properties that make it perfect for your application may require some extra consideration of Design for Manufacturing (DFM).
Due to the hardness of the material, machining steel takes longer than other, softer materials like aluminum or brass. You need to use the correct machine settings to optimize the quality of the machining and minimize the wear on the tools. Practically, that means slower spindle speeds and feed rates to protect your part and tooling.
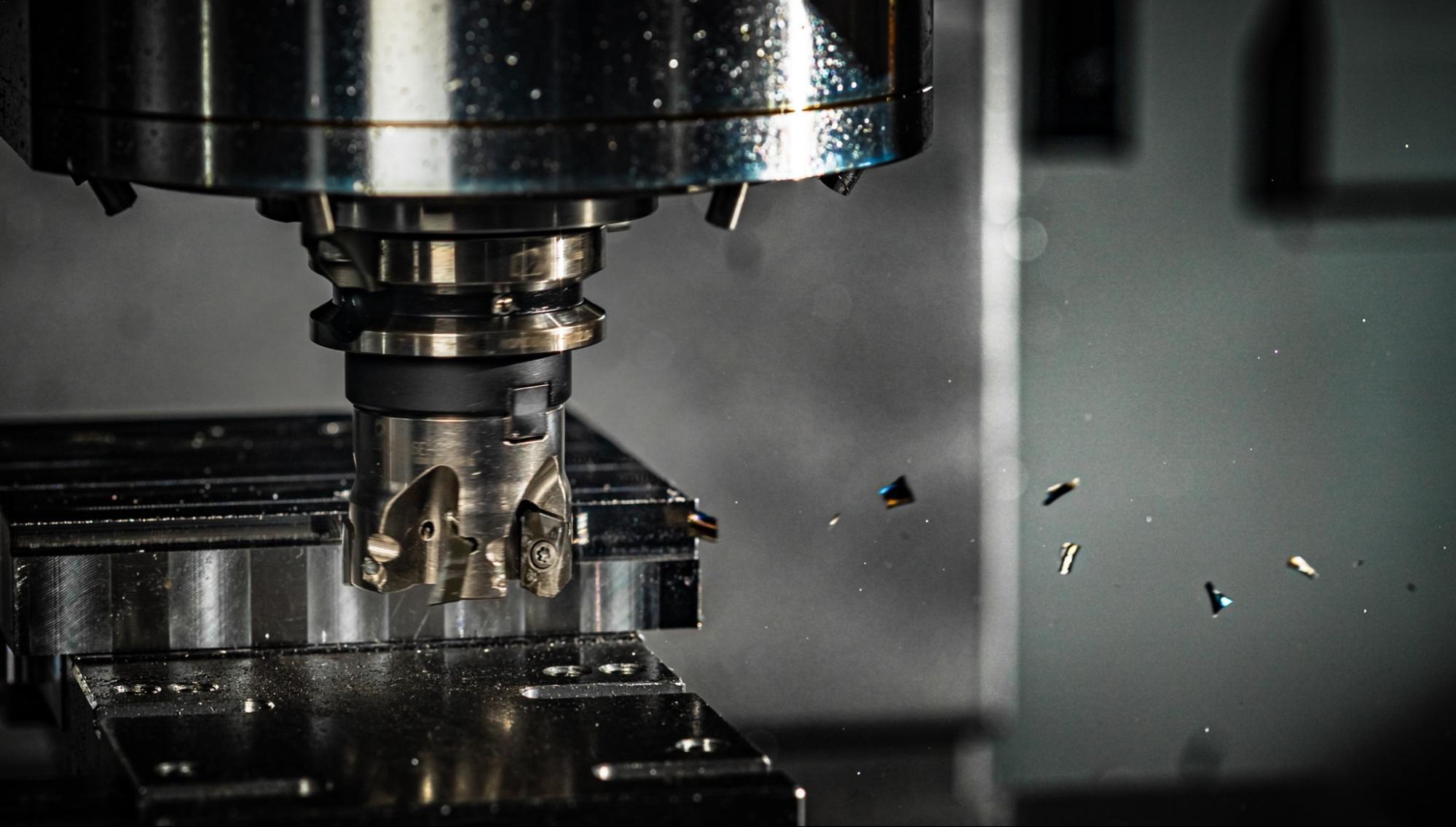
Even if you’re not doing the machining itself, you should still evaluate the steel grades suited to your project not only for hardness and strength but also to account for differences in machinability. For example, stainless steel will take about twice as long to machine as carbon steel. When deciding between different grades, you also want to consider which properties are the highest priority, and which steel alloys are readily available. Commonly used grades, such as 304 or 316 stainless steel, are available in a wider range of stock sizes and take less time to find and source.
Conclusion
With the wide range of applications for CNC machined steel and its robust physical properties, it’s no wonder steel is the material of choice for manufacturers around the world. The infinite number of alloys possible provides an endless number of steel grades with useful properties. And when designing your next CNC machined steel part, remember to weigh the properties you need against the material’s machinability to ensure you get a lead time that works for you.
Looking for a manufacturing partner experienced with CNC machining steel who can help you find the right balance? Fictiv has a network of experienced manufacturers who can guarantee quick lead times and high-quality parts. Create a free account and upload your model and see how our CNC machining services work.