Time to read: 8 min
Welcome to the world of post-CNC heat treatment! Now that you’ve successfully CNC machined your parts, it’s time to give them the TLC they deserve. Don’t let those raw components go out into the world without a little extra oomph. Once you’ve finished CNC machining your parts, your work isn’t done. Those raw components might have ugly finishes, may not be strong enough, or only one part of a multi-part complex product. Regardless, post-machining processes are necessary for a range of applications, and we’re here to walk you through some considerations so you can choose the right secondary operations for your project.
This article is part of a three-part series covering options and considerations for heat treatment processes, finishes, and hardware installation. Any or all of these may be necessary to take your part from its machined state to customer-ready. Here, we discuss heat treating, while Parts II and III examine finishes and hardware installation.
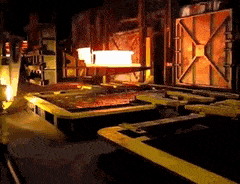
Pro-Tip: Fictiv is your provider for CNC machined part heat treatment. Check out our ebook on our other CNC finishing options, or upload a part for a quote today.
Heat Treating Before or After Machining?

Heat treatment is a processing operation option before or after machining. Why use one method over the other? Both pre-CNC-machining and post-CNC-machining heat treatment processes are common, and both offer specific benefits and considerations. The order in which you choose to heat treat and machine your metal can affect the material properties, the machining process, and the tolerances of your part.
Heat Treating Prior to CNC Machining
- Advantages
Choosing a pre-heat-treated metal does have some advantages. With hardened metal, your part can hold tighter tolerances, and sourcing your material is easier because pre-heat-treated metals are readily available. And, if you wait until after machining, heat-treating adds another time-consuming step in the production process.
- Disadvantages
Using a material that has already been heat treated affects your machining (harder materials take longer to machine and wear down tooling faster, which adds to machining costs). Depending on the type of heat treatment applied and how deep below the surface the material is affected, if you cut away the hardened layer of the material, you’ll defeat the purpose of using hardened metal in the first place. There’s also a chance that the machining process will generate enough heat to increase the hardness of the workpiece. Certain materials, like stainless steel, are more prone to being work-hardened during machining, and extra care is necessary to prevent this.
Heat Treating Post CNC Machining
- Advantages
On the other hand, heat treatment after machining gives you more control over the process. There are multiple types of heat treating, and you can choose which to use to get the material properties you need. Heat treating after machining also ensures that the heat treating effects are consistent across the surface of your part. With pre-heat treated material, the heat treating may have only affected the material to a certain depth, so machining may remove the hardened material in some places and not others.
- Disadvantages
As mentioned, heat treating after machining adds cost and lead time due to the extra step of outsourcing this process. Heat treating can also cause parts to warp or otherwise deform, affecting the tight tolerances achieved during machining. It is more difficult to hold tight tolerances because of the variability experienced during heat treatment. From first-hand experience, it is difficult to hold temperatures with precision in large ovens, which is something to consider when heat treating CNC machined parts.
Heat Treatments
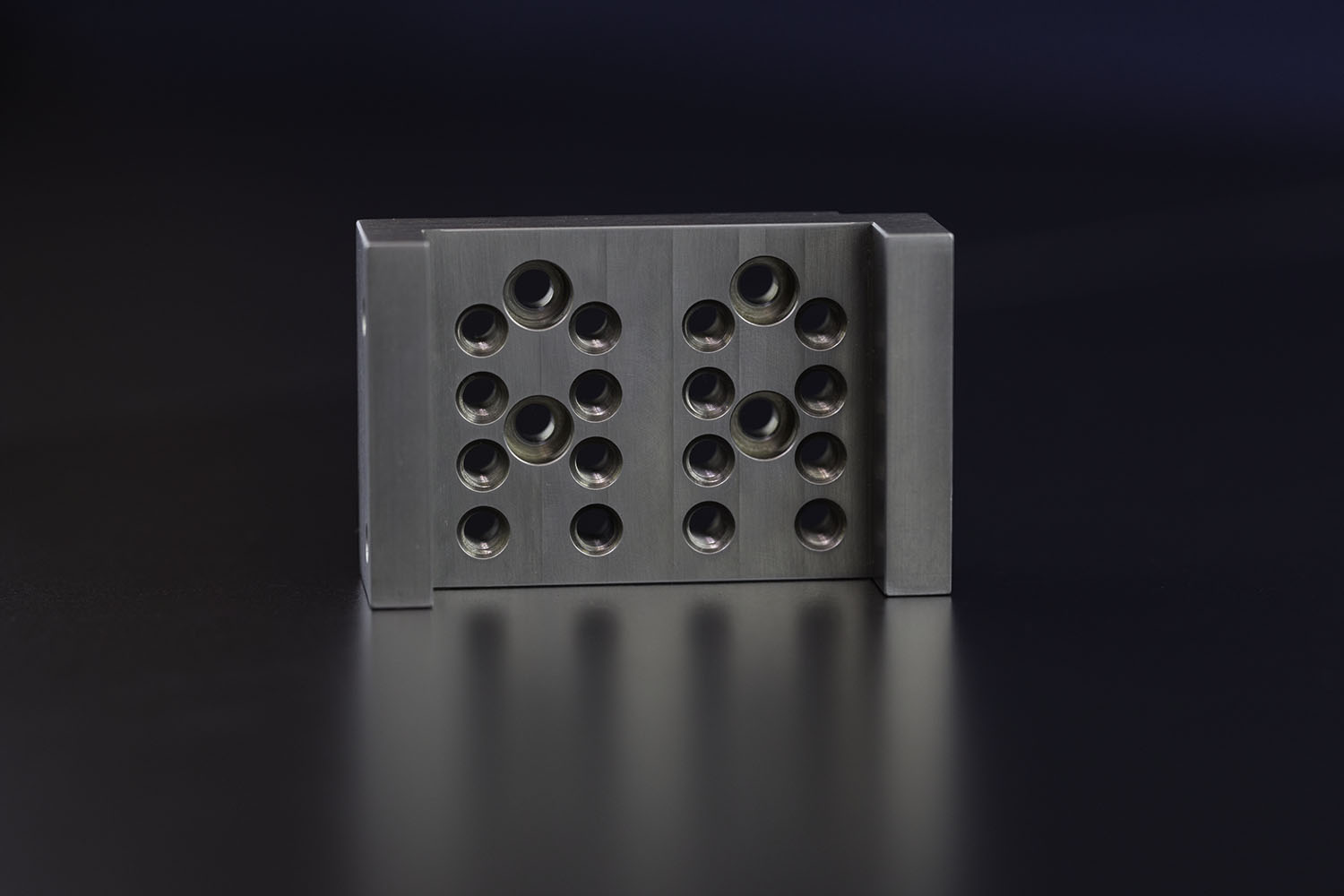
In general, heat treatment of a metal is an exposure of metal to a specified temperature over a period of time to modify the material properties like strength, ductility, and toughness or to alleviate residual stress built up in the material. Usually, this means increasing the strength and hardness of the metal so that it can stand up to more extreme applications. However, certain heat-treating processes, like annealing, actually reduce the hardness of metals, or soften them. Let’s take a look at the different heat-treating methods.
Hardening
Hardening is used to — you guessed it — make metal harder. A higher hardness means the metal is less likely to dent or be marked when impacted. Hardening of a metal actually improves its resistance to plastic deformation. Hardening also increases the tensile strength of the metal, which is the force at which the material fails and breaks. Higher strength makes the material more suitable for certain applications. Hardening typically applies to ferrous metals (like steel) although other metals like titanium or aluminum can undergo a similar process called nitriding.
What is happening when a metal is hardened?
In the hardening process, the workpiece is heated to a specific temperature above the metal’s critical temperature or the point at which its crystal structure and physical properties change. The critical temperature is where the metal undergoes a phase change (such as when steel becomes austenite) or when solute-rich precipitates dissolve. The metal is held at that temperature and then cooled by quenching it in water, brine, or oil.
The quenching process allows the formation of a very fine solution-rich precipitate which inevitably stabilizes the crystalline structure of the metal and leaves less room for deformation at the grain boundaries. This increases the hardness and yield strength of the metal. The quenching liquid depends on the specific alloy of the metal. Each quenching liquid has a unique cooling rate, so it’s chosen based on how quickly you need to cool the metal.
Case Hardening
Case hardening, or surface hardening, is a type of hardening that only affects the outer surface of the material. This process is often done after machining to create a durable outer layer.
The case hardening process is for steel alloys and works by diffusing carbon, nitrogen, or boron (known respectively as carburizing, nitriding, and boriding) into the outer layer of the steel at a high temperature and then heat treating to improve the hardness. The depth of the penetration of carbon, nitrogen or boron is dependent on the time of exposure and the temperature of exposure.
The outer layer of a part is often case hardened to be pressure and impact resistant, while the inside of the part can remain softened and ductile. This combination of a soft core and hard shell allows for improved fatigue and high stress resistance and is especially useful for gears and bearings.
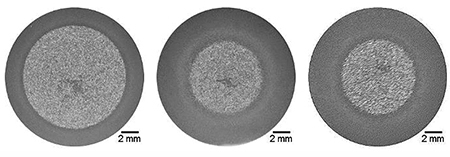
Precipitation Hardening
Precipitation hardening is a heat treatment process that takes place at low temperature and is used on specific metals that have certain alloying elements. These elements include copper, aluminum, phosphorus, and titanium. There are three phases of precipitation hardening:
- Solution annealing, where a metal is treated with a chemical solution below the metal’s eutectic temperature to allow the precipitation of specific elements;
- Quenching, which allows for the solubility of the precipitated elements, and
- Aging, where the parts are heated and a two-phase, matrix alloy is formed. When heated over an extended period, these elements precipitate or form solid particles within the solid metal. This affects the grain structure, increasing the strength and corrosion resistance (most often) of the material.
Annealing
Don’t roll your eyes, but annealing is like a wellness retreat for metals. Annealing is used to soften the metal, as well as to relieve stress and increase the ductility of the material. This process makes the metal significantly more machinable. On a microstructure level, the metal is more refined and therefore softened. You can anneal steel, copper, aluminum, and brass alloys.
How is the Annealing Process Completed?
To anneal a metal, the metal is heated slowly to a specific temperature (above the material’s critical temperature), held at that temperature, and finally cooled at a slow, set rate. This slow cooling process is accomplished by burying the metal in an insulating material or keeping it in the furnace while both the furnace and the metal cool.
There are three metallurgical phases or stages in the annealing process:
- Recovery, which happens during the heating process; removal of crystal defects (primarily linear dislocations in the crystalline structures); results in a lowering of the internal stress within the metal;
- Recrystallization, which occurs during the controlled cooling process; results in the grain nucleation and growth to replace any areas of deformation due to internal stresses; encourages homogeneity of the grain structure and softening of the metal;
- Grain growth may occur if the annealing process is continued for too long; results in coarse microstructure, which will limit ductility and may cause a weakening of the metal;
From a thermodynamics perspective, annealing actually speeds up the spontaneous process of internal stress relief (acts as a catalyst by adding heat) which is technically a reduction in the Gibbs free energy of metal. The cooling actually promotes the elimination of lattice vacancies within the metal to reduce stress by creating a more homogenous, robust crystal structure.
Tempering
Tempering is a special process that is performed on hardened and quenched metals to relieve stress and soften them—similar to the annealing process. The tempering process is basically re-heating already hardened metals. Tempering typically occurs at lower temperatures than hardening and results in a phase transformation (i.e., bainite, martensite, and ferrite in steel alloys) via precipitation of intermetallic particles that result in strengthening and ductility. Aging is a specific type of tempering for aluminum alloys.
Precipitation hardened alloys must undergo a solutionizing process whereby the metal is heated to allow uniform distribution and dissolution of alloying elements and quenching at a fast rate to prevent these elements from falling out of solution. These precipitation hardened alloys are tempered at lower temperatures than the solutionizing temperature. The mechanism is similar to how tempering of steels works, but the specific mechanism is the precipitation of intermetallic compounds, which add strength to the metal by preventing the formation of dislocations within the crystalline structure. The amount and general size of these intermetallic compound precipitates is controlled by time and temperature during the tempering process.
Final Thoughts
Heat treating CNC machined parts is often necessary to achieve the physical properties needed for a given application. And while heat treating material before CNC machining can save overall production time, it adds cost to the machining process. Meanwhile, heat-treating parts after CNC machining makes it easier to machine the material, but adds an extra step to the production process.
Depending on your application, you’ll have to weigh the benefits of added hardness and tighter tolerances against the disadvantages of longer machining time associated with pre-heat-treated material. The good news is that Fictiv now offers hardening, case hardening, and tempering as finishing options for select CNC machined materials. Plus our experts can help you choose the right material for your next CNC project.
Material | Fictiv Heat Treatment Processes Available |
A286 Stainless Steel | Hardening, Case Hardening, Tempering |
410 Stainless Steel | Hardening, Case Hardening, Tempering |
416 Stainless Steel | Hardening, Case Hardening, Tempering |
420 Stainless Steel | Hardening, Case Hardening, Tempering |
440C Stainless Steel | Hardening, Case Hardening, Tempering |
1018 Mild Steel (Low-Carbon Steel) | Hardening, Case Hardening, Tempering |
A36 Steel | Hardening, Case Hardening, Tempering |
1045 Carbon Steel | Hardening, Case Hardening, Tempering |
12L14 Carbon Steel | Hardening, Case Hardening, Tempering |
1215 Carbon Steel | Hardening, Case Hardening, Tempering |
A514 Alloy Steel | Hardening, Case Hardening, Tempering |
4140 Alloy Steel | Hardening, Case Hardening, Tempering |
4340 Alloy Steel | Hardening, Case Hardening, Tempering |
4130 Alloy Steel | Hardening, Case Hardening, Tempering |
8620 Steel | Hardening, Case Hardening, Tempering |
Cast Iron | Hardening, Case Hardening, Tempering |
Grade 2 Titanium | Hardening, Case Hardening, Tempering |
Grade 5 Titanium | Hardening, Case Hardening, Tempering |
A2 Tool Steel | Hardening, Case Hardening, Tempering |
D2 Tool Steel | Hardening, Case Hardening, Tempering |
O1 Tool steel | Hardening, Case Hardening, Tempering |
Create an account and upload a part to see what our CNC machining services can do for you today!