During pandemic lockdown, I noticed several issues with my home, including the broken sprinkler head, dog stains on the carpet, and my mother’s spice cabinet. My mother has a metric ton of spices that used to have labels that have rubbed off after constant use. I bought a portable label maker to replenish the labels and make it easier to find spices (which means we can eat sooner). This product is cheap, portable, and aesthetically appealing, and I figured it was about time to see what was happening on the inside.
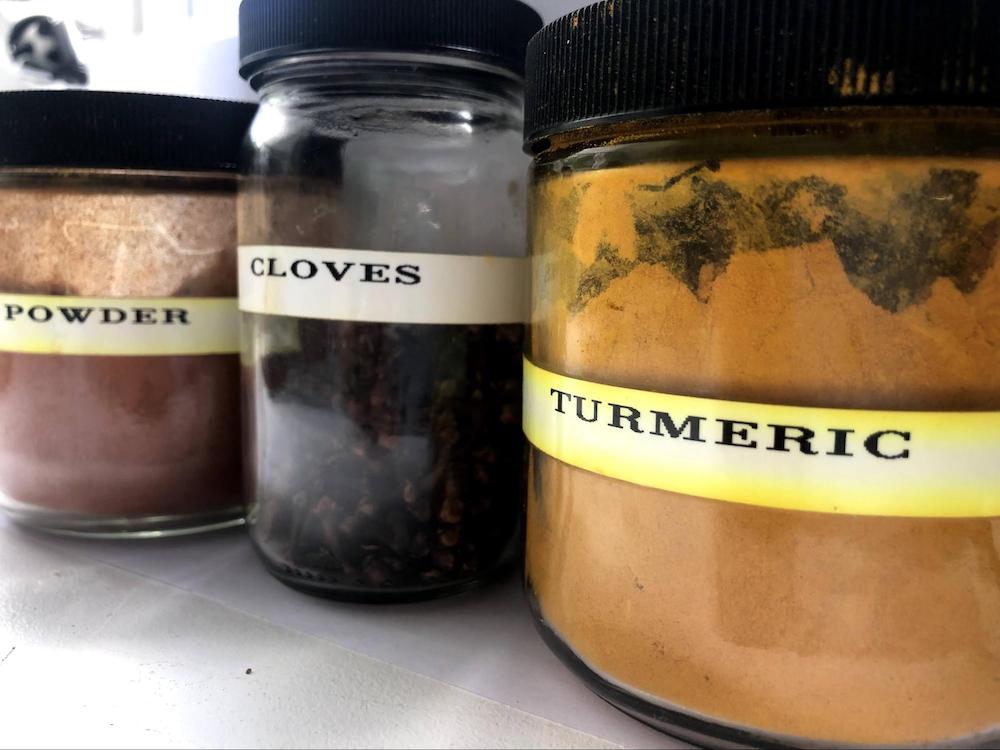
The LW-300 is marketed as a portable label maker that can print in many different fonts, colors, and styles. It is compatible with all Epson cartridges and uses a full QWERTY keyboard, along with a monochromatic LCD. The colorful print and cut buttons, as well as the rounded corners project the image for an easy to use experience. Diving inside, we’ll be focusing on the following:
- Sub-Assembly Designs
- The array of Plastic Components
- Electronics
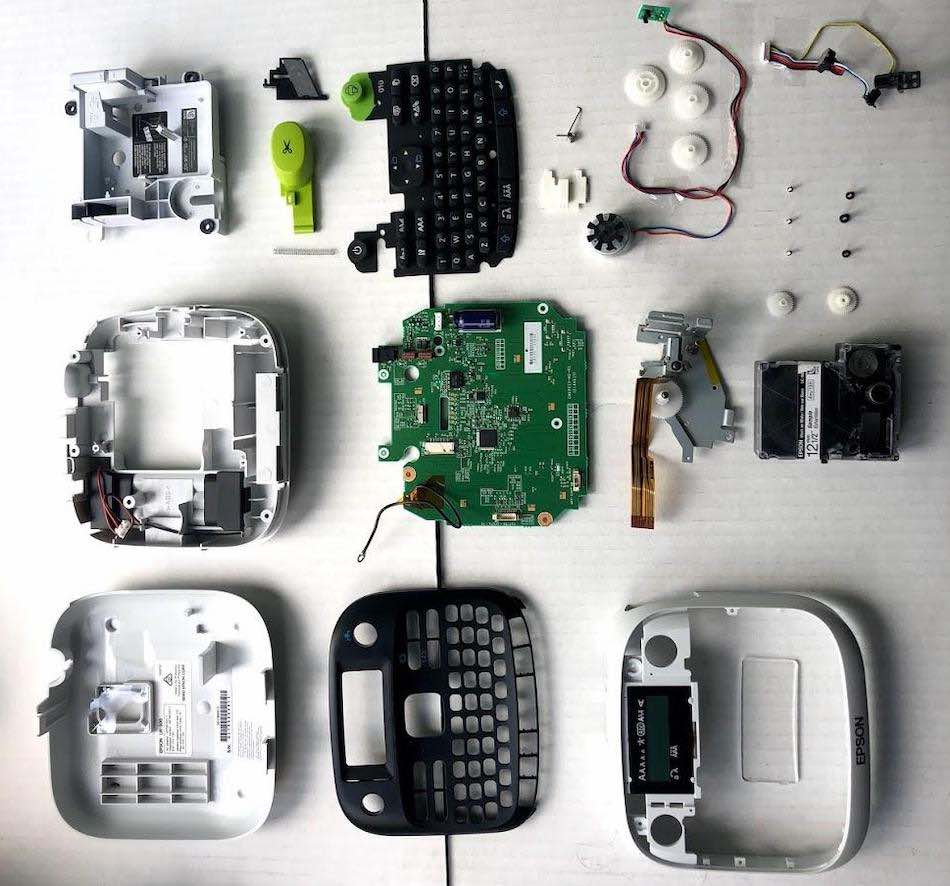
Sub-Assembly Designs
Upon opening the label maker, we identify two main sub-assemblies: the ink-cassette housing and the blade assembly.
- The ink-cassette housing’s main components are the driver gear, the ribbon cable, and the metal bracket. This housing screws into the center of the label maker to provide rigidity.
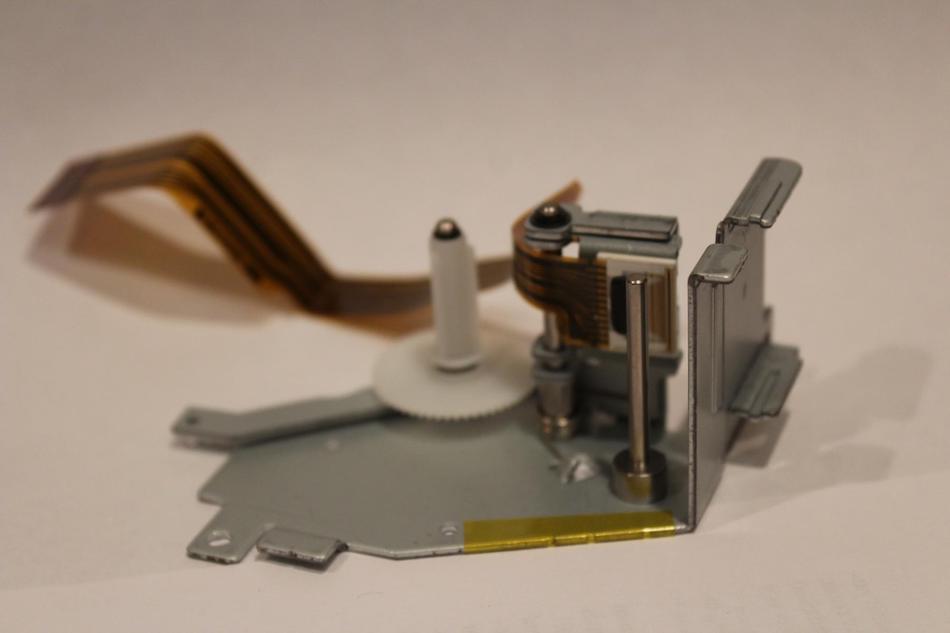
- The multi-pin ribbon cable affixed to the bracket reads the corresponding IC on the cartridge so the LW-300 can identify the color, material, and other properties of the label itself. This part was likely made out of aluminum, due to the precision nature of cassette style printers.
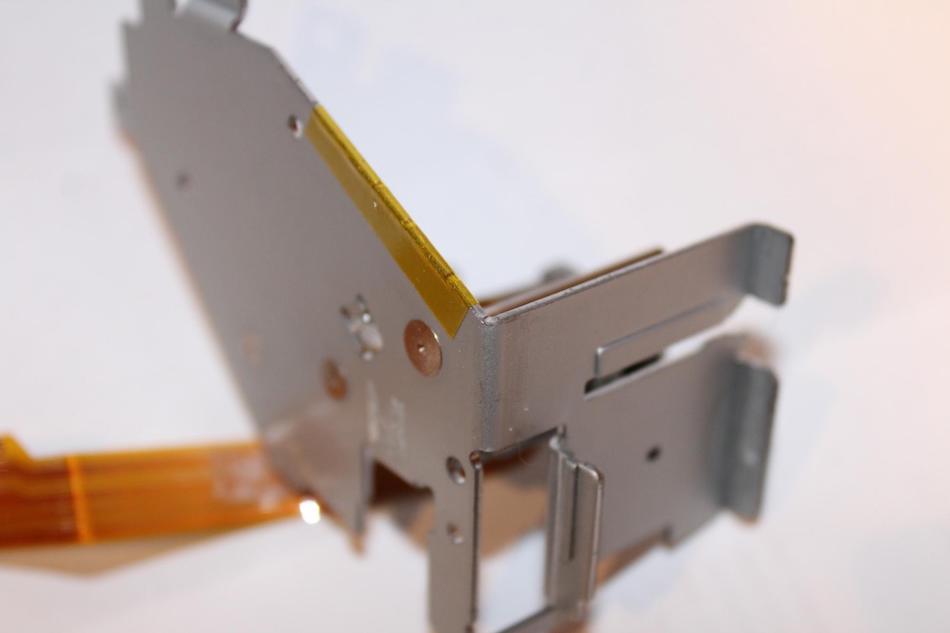
- The main metal bracket was sheet metal stamped, drilled, and then bent with a secondary bending press. A telling sign of bending due to a press is the slight curve on each of the bends due to the die used.
- Since the paper spool is printed at a constant rate, the metal bracket must stabilize the ink cassette so as not to induce errors on printing, hence the choice of a rigid metal over a pliable plastic. Additionally, the plastic component the housing snaps into has rubber bushings to isolate any vibrations during operation.

- The entire cutting operation was, perhaps unsurprisingly, a simple manual spring-actuated blade. The assembly consists of the button itself, a return spring, and the blade. It’s a straightforward, but reliable design that isn’t dependent on any electromechanical components.
Array of Plastic Components
- Epson decided to use compression molding for the flexible keyboard with two different pigments: a black and light green. The light green on the print and ‘cut’ buttons serve as eye-catching indicators to the most important functions of the product.
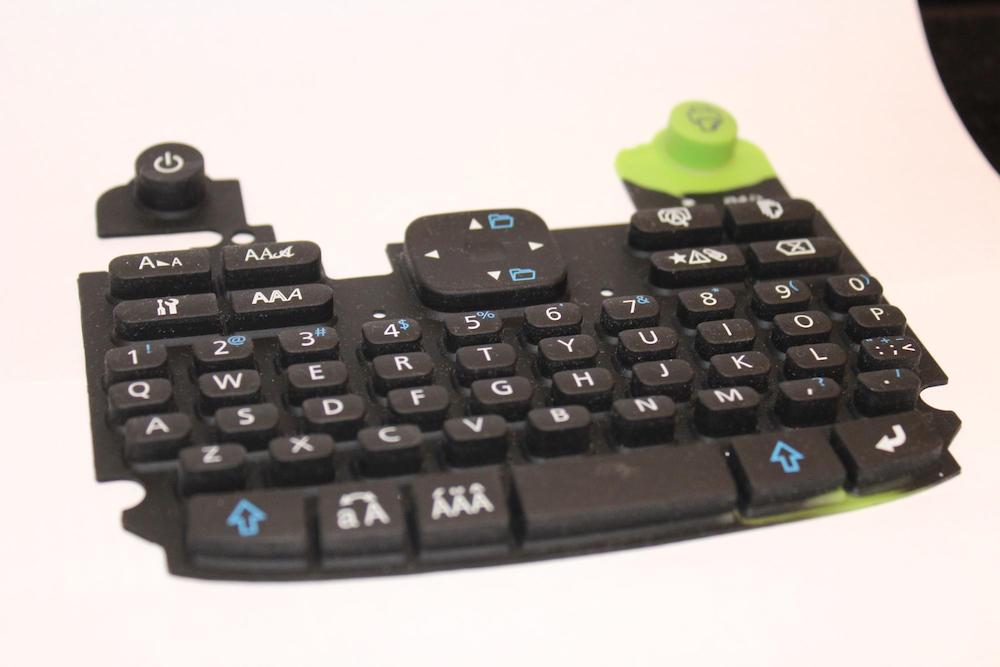
- Elastomer compression molding is a cheap and effective process for making key switches, as opposed to using mechanical switches with moving parts. After compression molding, a secondary screening process applies the graphics. This process allows Epson to easily change languages and keyboard styles by simply altering the post-processing, instead of creating a new mold for the keyboard.
- The main shells of the label maker are made of ABS and Polystyrene. ABS is used on the internals of the label maker, where the parts aren’t required to have pretty finishes or sanded witness marks like on the keypad holder, for example. The keypad holder has a minimal surface area shown to the user, and it’s easy to spot the ejector pin locations on the inner-facing surface. ABS is also a cheaper alternative to Polystyrene – it makes sense to spend less on what isn’t highly shown to the users.
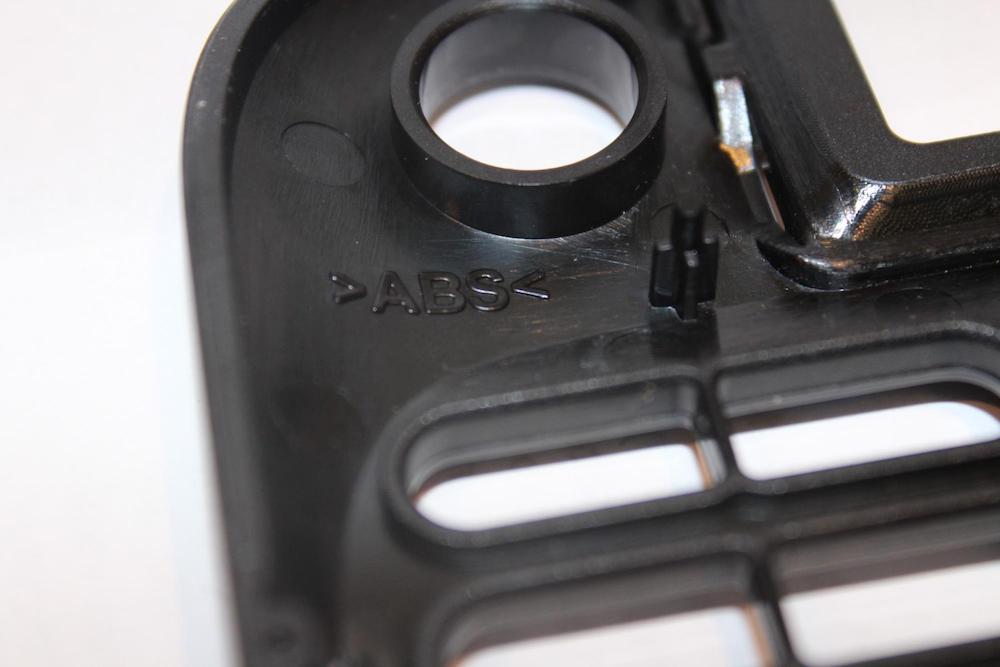
- Now, looking at the top and rear shells of the label maker, Epson goes for PS-HI or Polystyrene – High-Impact. This material is impact resistant and also smooth to the touch, making it a great material to grip onto and to survive any minor bumps or rough handlings the product might experience in its lifetime.
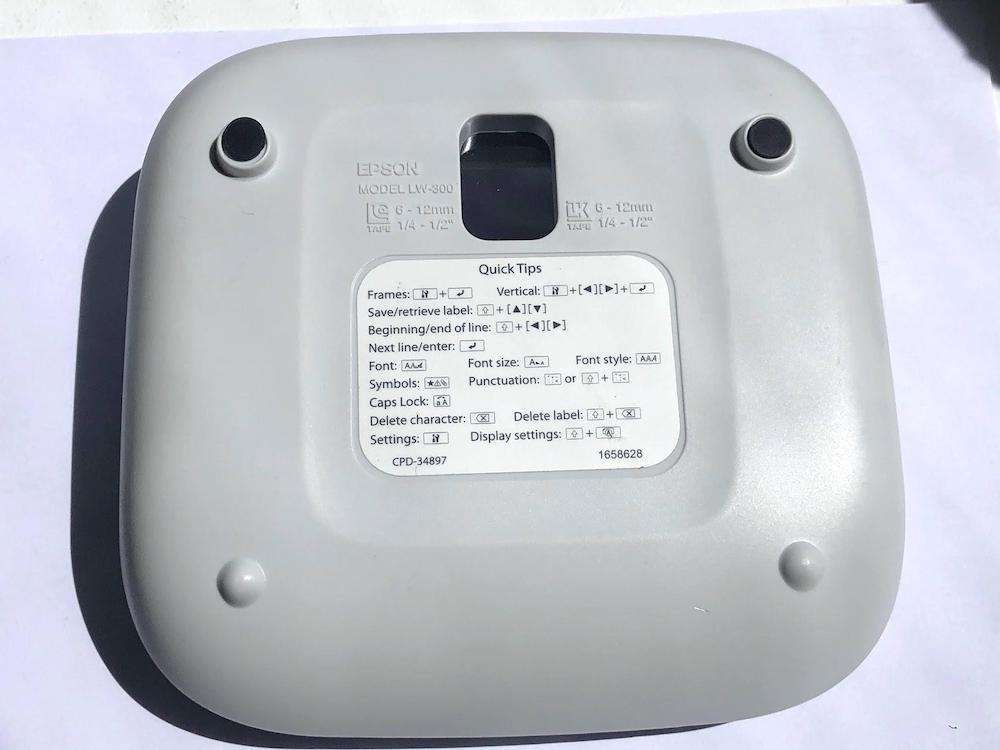
Electronics
- Looking at the components on the single PCB of the label maker, it becomes quite clear how they cut costs yet provide a quality experience. The Epson CB690Y2000 is a custom chip manufactured in-house and likely used in products such as printers, scanners, etc. By using their own chip in multiple devices, Epson can lower manufacturing costs, as the rest of the chips on the PCB are bought off-the-shelf for specific purposes.
- The BA6220 is a motor controller specifically meant for high precision cassette applications. The other two ICs are the Texas Instruments SNx4AHC08 power sequencing chip used to tell if the processor is working as intended; the other IC is an STM 25Px35UC, which is a simple timing chip.
- To the right is the DC Motor and Encoder controlled by the BA6220 chip. Put all together and they can drive the DC Motor with precision so the spool can spin accurately; a DC motor as opposed to a stepper motor is more price-effective and is also used in other cassette driven products.
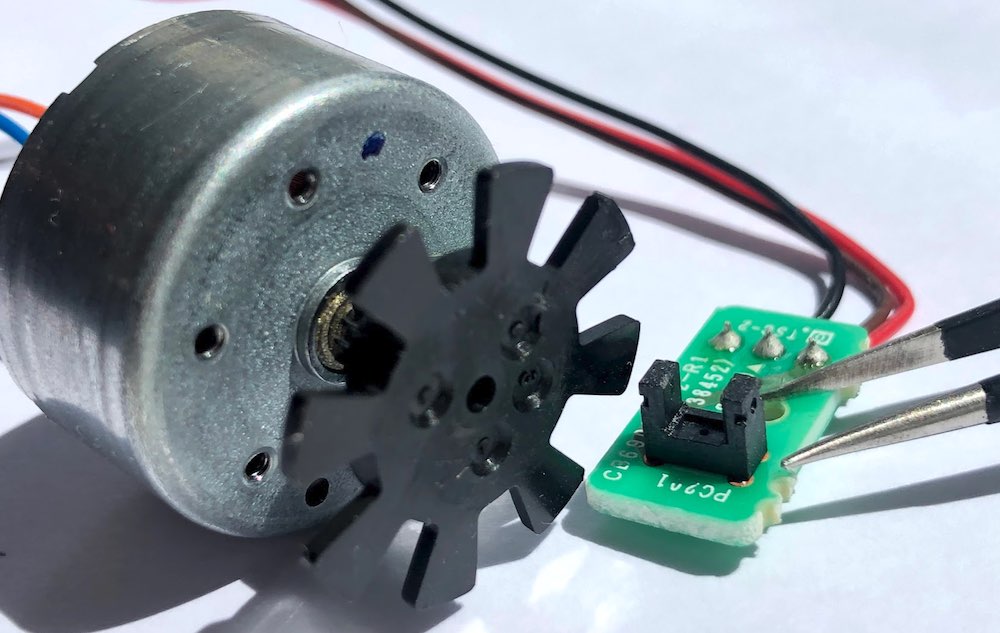
Main Takeaways
It is evident that Epson made some calculated decisions to make sure its label maker would be long-lasting and print labels consistently and precisely, without many flaws. The use of high impact polystyrene for the backplates allows the label maker to take a beating, and, combined with the metal cassette bracket, ensures rigidity in different printing scenarios. The use of a compression-molded keyboard cover gives Epson the flexibility to distribute the product across regions with different languages by simply screen printing new graphics, instead of molding a new part every time.
Though the letters may scrub off after time, it is an understandable cost-cutting measure. Finally, the use of off-the-shelf components, paired with only one custom IC, allows Epson to simplify the overall inventory of their line of products and saves the trouble of producing electronics specific to different applications. The amount of thought and dedication that can go into a product as standard as a label maker is noticed by its variety of users. Epson has shown with the LW-300 that diversified manufacturing processes can help bring costs down yet still provide a reliable, inclusive product that can help anyone anywhere make their life a little less chaotic.