In 2006, Nintendo took the world of interactive gaming by storm. The launch of the Wii welcomed gamers and, more importantly, non-gamers alike to physically interact with a virtual world. Whether the user was playing a competitive round of Wii Tennis or customizing their Mii, the Wii remote (otherwise known as the Wiimote) invited users to get up, move around, and be an active part of the game.
Naturally, the success of the technology behind such an impressive device created an open invitation for the manufacture of deceivingly similar counterfeit remotes. Thus, it is only fitting that we discover why the original one was, and remains, a BIG DEAL!
Before we begin our teardown, here’s what we know so far:
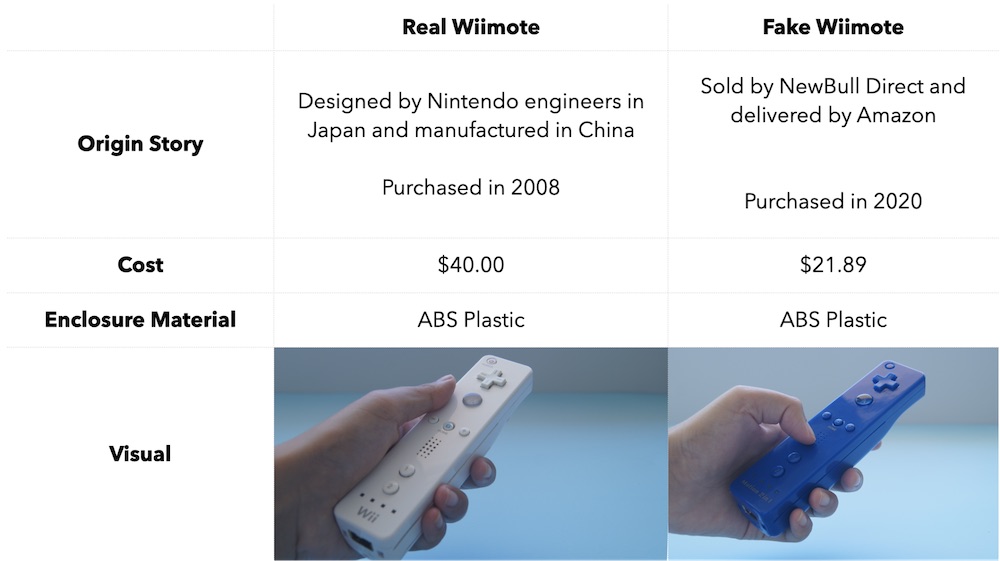
For this comparative teardown, we’re focusing on these features of interest:
- User Experience
- Manufacturing Processes
- Design for Assembly
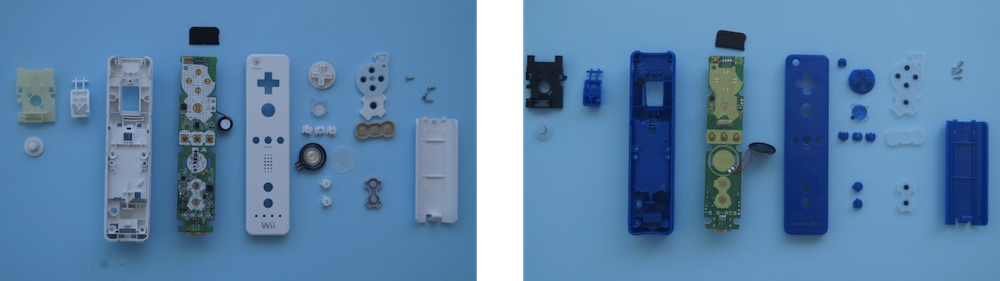
User Experience
As we will learn throughout this teardown, the fake Wiimote is a result of meticulous reverse engineering. Thus, it only makes sense to begin our comparative investigation analyzing what these controls were designed to do best — be used as a tool for interactive gameplay!
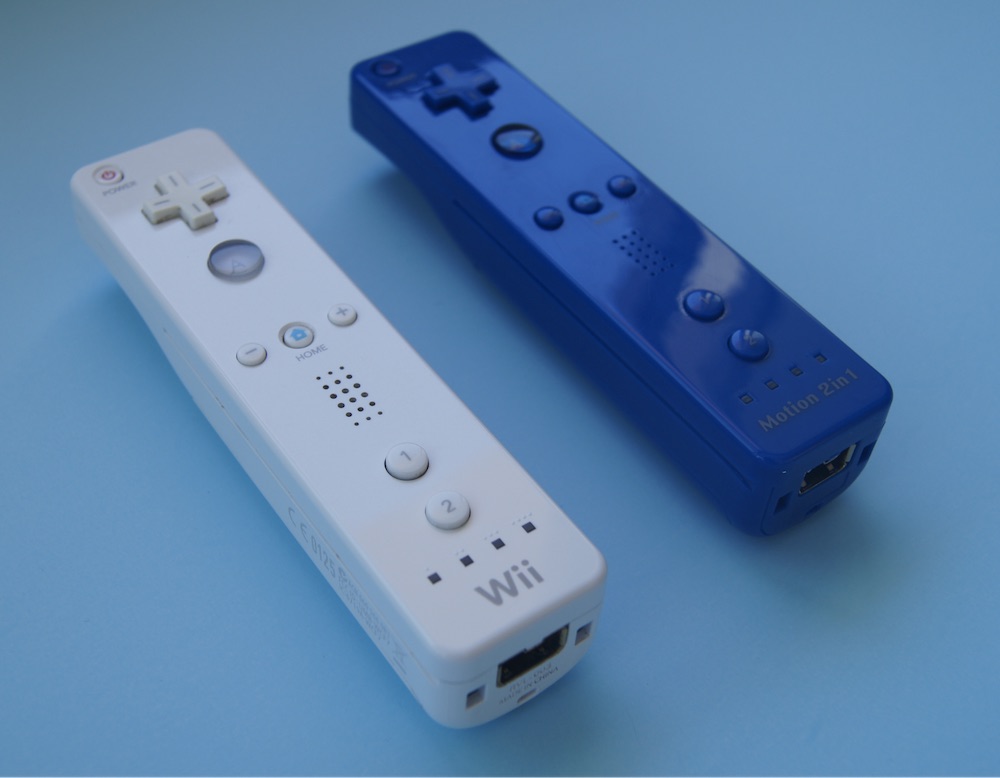
In order to test out initial functionality, we observed the simultaneous behaviors of the original Wiimote and the counterfeit remote, as they are being programmed to connect to the same Wii console.
- The initial powering up was characterized by a similar blue light at the bottom of the remote, and no striking lags were present when attempting to connect the controllers.
- Since the Wiimote’s pointer effect works by means of IR tracking, we chose to test this out by attempting to customize a Mii character.
- The original remote had fluid movement when being dragged from one corner of the screen to another.
- Unfortunately, the counterfeit was met with various occasions in which the onscreen cursor did not reflect the live positioning of the remote.
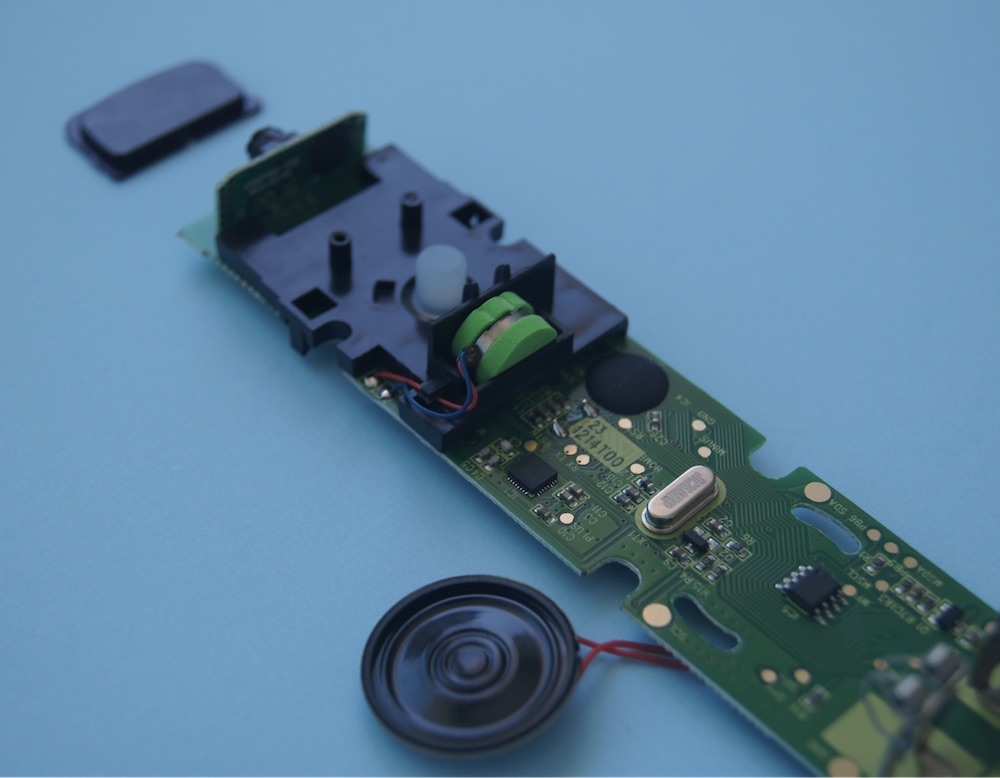
- After a quick solo match of tennis on the beloved Wii Sports game, the superiority of the original Wiimote’s haptic feedback became extremely apparent.
- An obvious difference was the quality of sound being emitted by the remote speaker. More so than the original remote having a much clearer sound, the sounds being produced by the speaker in the counterfeit remote were incredibly muffled. Although it wasn’t apparent whether this was due in part to speaker placement or the speaker itself, one thing was for sure—it did not increase gameplay quality.
- The more disappointing difference was the intensity of the haptic “Rumble” Motor in the remotes, which was magnified by the interactivity of the game at hand. Once again, the vibration felt through the original enclosure was much more intense in comparison to the diluted vibrations felt through the counterfeit. The lack of crisp vibrations removed a layer of immersion from the user experience and didn’t effectively match the energy exhibited by the characters on the screen.
- Despite the rare lags and the underwhelming haptic feedback, we must acknowledge that the engineers behind the counterfeit Wiimote were successfully able capture the feel of the original Wiimote.
- A particularly amazing job was done in mimicking the feel of pressing the original buttons and interacting with the “B” Push Button.
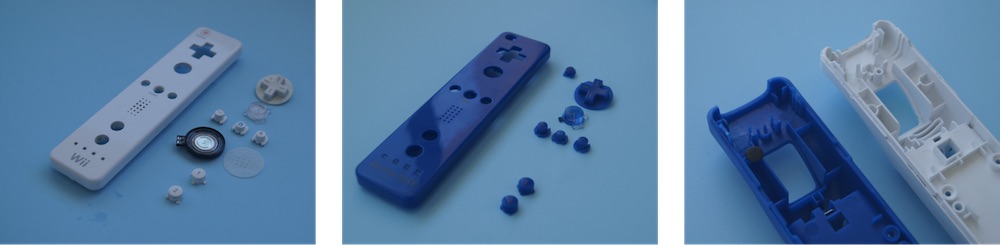
The original Wiimote button experience is known for sensitivity, meaning that the harder you press, the more immediate the movement present on the screen should be. The sensitivity is near exact on the counterfeit remote—even when you overpress, the button springs back to its original positioning.
With regard to the “B” Push Button, the interaction is much better on the counterfeit than the original. This is due in large part to the button experiencing a little more resistance when being pressed, which, although less smooth, ends up making the interaction much more intentional.
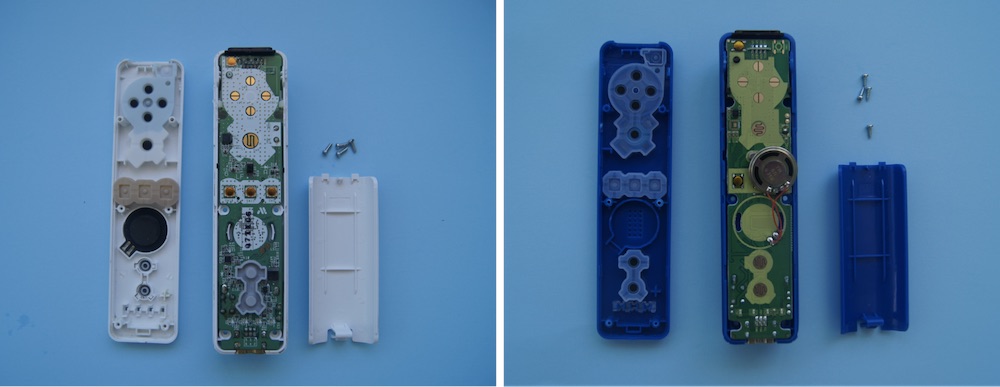
As expected, the vast majority of the Wiimote components, original and fake, were made out of injection molded ABS plastic, a couple of silicone rubber keypads, and a PCBA.
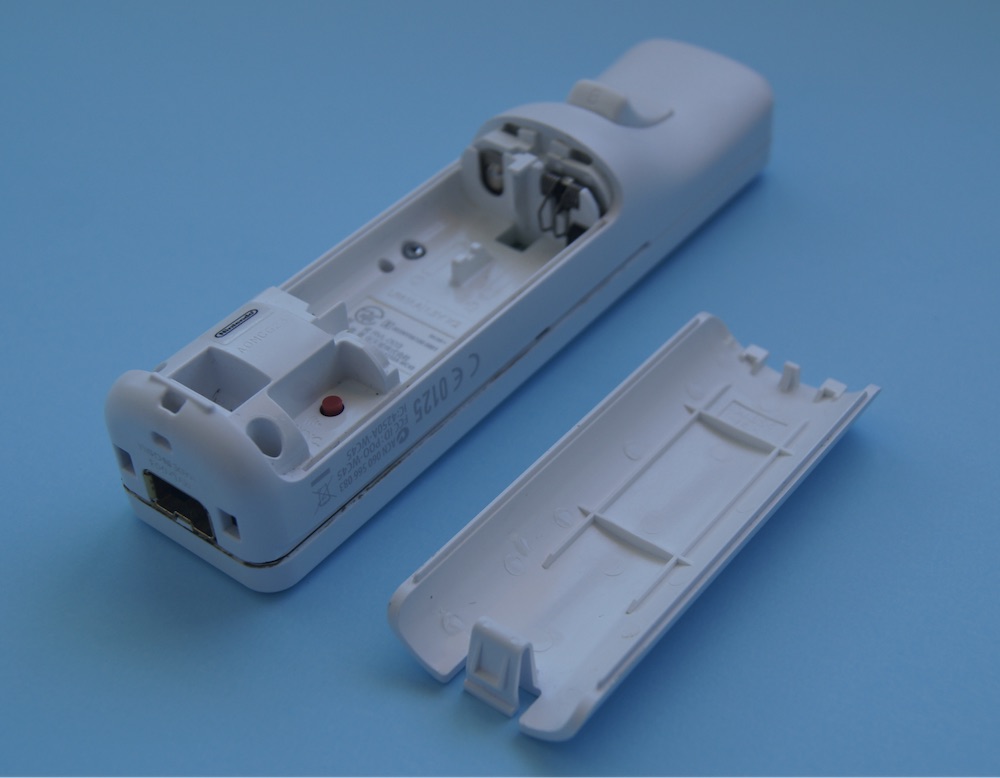
- When designing a plastic part, such as a remote, it is important to consider a variety of mechanical properties during material selection. In the case of this remote, ABS (a midrange polymer in both cost and performance) was chosen for the following reasons:
- Dimensional Stability: The material’s shrink rate, strength, and stiffness are conducive to parts that can precisely fit with other parts — a quality central to an enclosure.
- Impact Strength: Since hand-held electronic products experience forces of varying magnitudes and frequencies, the chosen material must exhibit the ability to withstand these load cases.
- Finish: ABS that is manufactured through emulsion polymerization results in an aesthetic high gloss part.
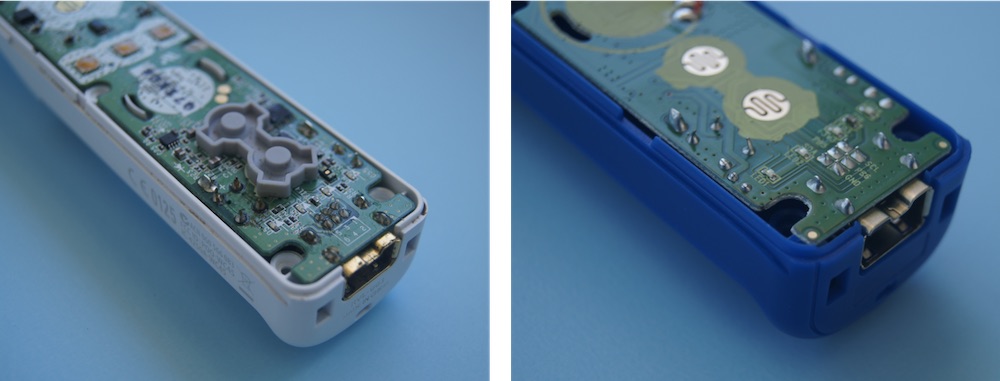
- When it comes to injection molding, a material is only as good as the part geometry, and in the case of this comparative teardown, it is a defining factor in both the price and the quality of the product at hand.
- Traditionally, engineers choose to design enclosures with thinner walls because they cool faster; it shortens the cycle time of the mold; it results in a quick ejection without warping; and the reduced time on the injection molding machine creates a product that is less expensive to produce.
- Additionally, engineers choose to design enclosures with uniform walls, so that when the plastic part is cooling, the entire part will shrink away from the mold uniformly and will end up with a much nicer cosmetic finish.
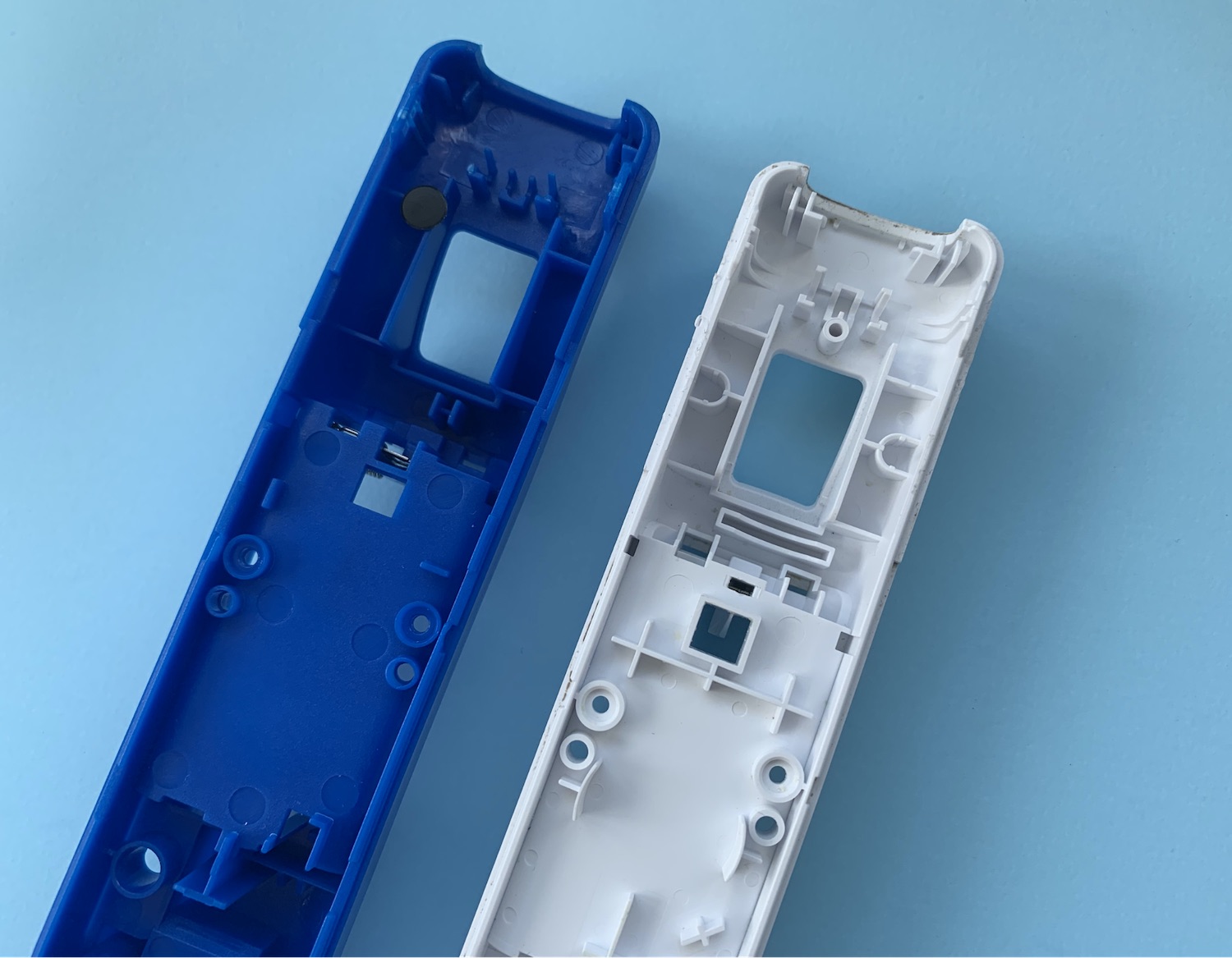
Before talking about the major geometric changes made to reduce production cost of the counterfeit controller, it is important to note that the internal side of both the Top and Bottom enclosures have fewer features when compared to the original Wiimote.
Since increased part complexity results in increased production cost, most alignment ribs were either removed or redesigned to have a much thinner wall thickness.
Although, at first glance, the overall dimensions of the injection molded enclosures seem identical, further inspection of the wall thickness and part weight points to the reality that the counterfeit controller has altered geometry — but at what cost?
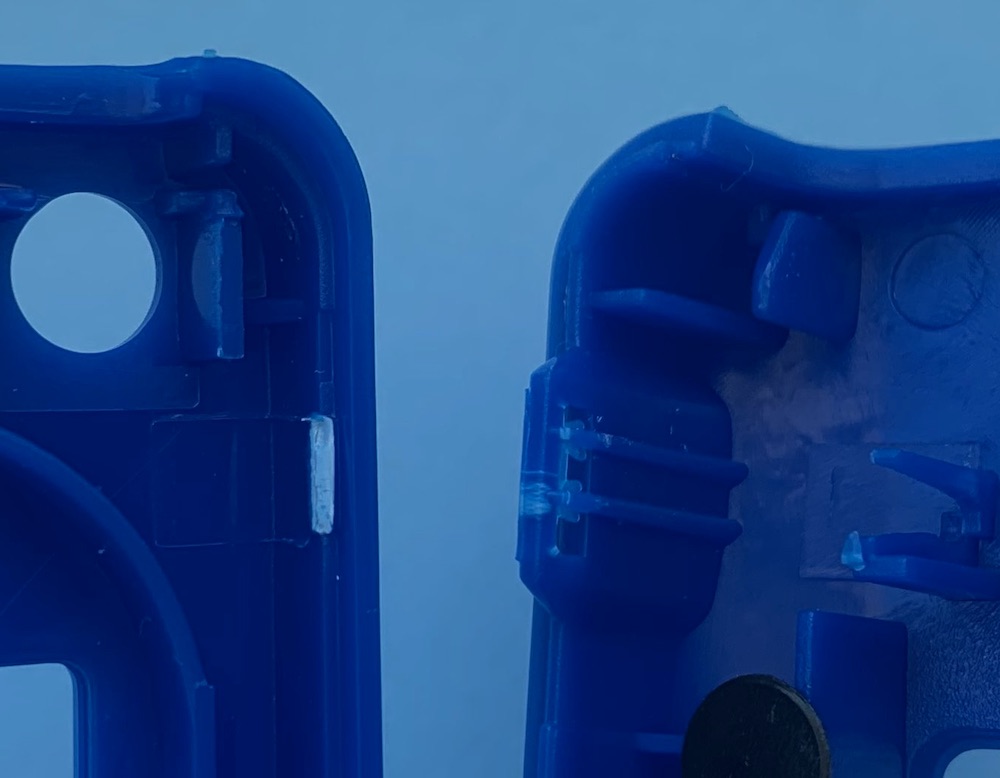
The original Wiimote has thin and uniform walls throughout, with a blemish-free surface and a component weight that is comfortable to hold for long periods of time.
Despite the original remote having a great selection of dimensions, the engineers behind the counterfeit remote seemed to want to reduce the cost of production even more by significantly decreasing the thickness of the plastic walls.
However, there is such a thing as too thin — the altered dimensions are then responsible for many of the key internal features becoming a lot more brittle (i.e., the cantilever tabs and the button alignment ribs).
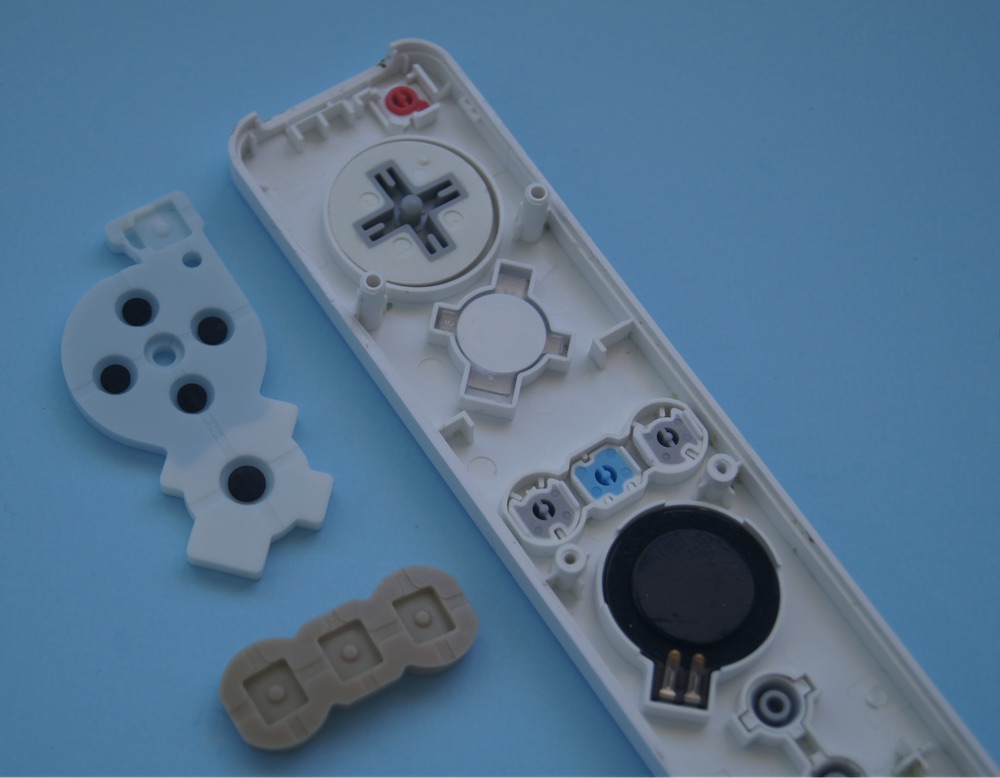
- Between all the buttons and their respective contact points on the PCBA, you will find silicone rubber keypads of different shapes.
- The keypads are made by placing silicon rubber directly on a tool (manufactured by EDM and CNC), where heat and pressure will form the silicone into the configuration of the mold tool.
- In the case of both the Wiimote and the counterfeit, carbon impregnated silicone pills are used as the element that makes contact with the printed circuit board every time the user presses a button, triggering the appropriate command.
Design for Assembly
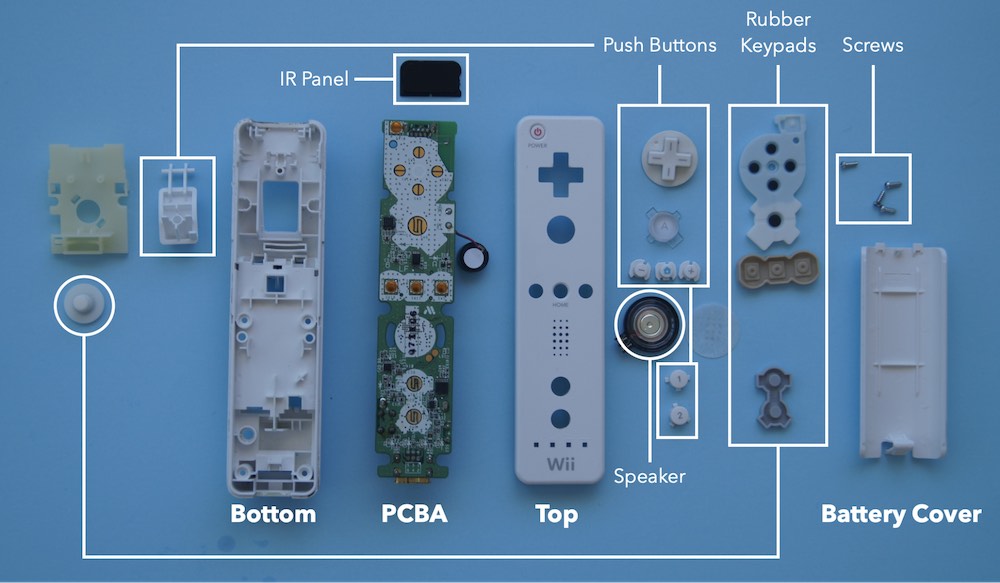
Once the four screws are removed, two plastic cantilever tabs are what keep the top and bottom from coming apart. To disengage these clips, the tabs must be pushed inward.
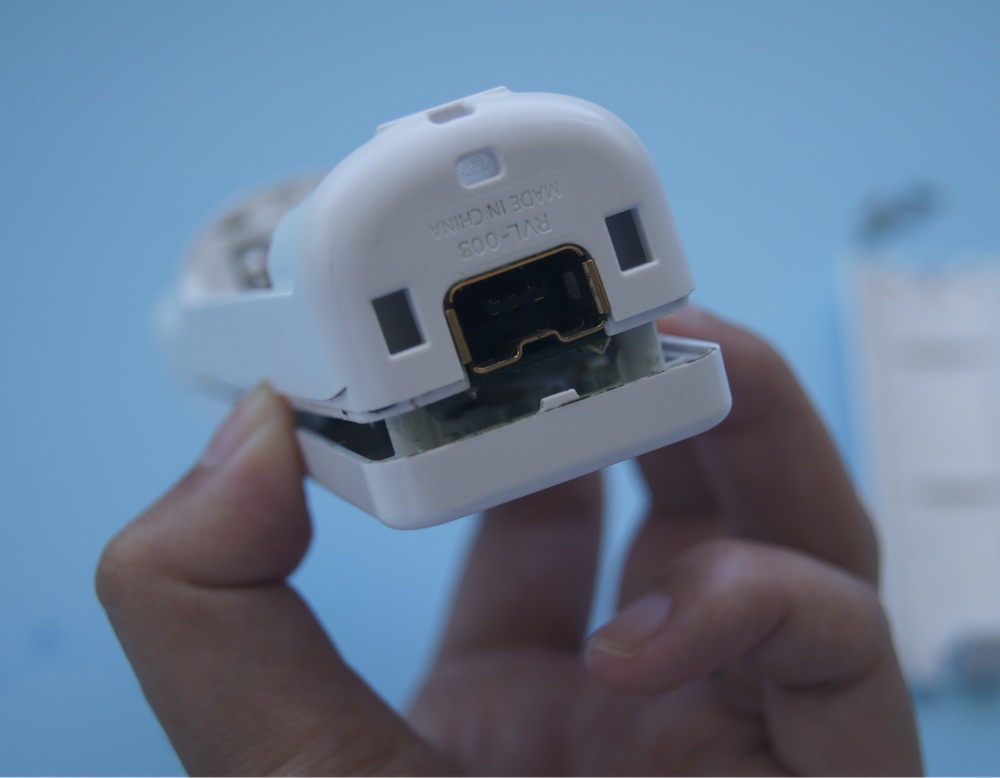
Disengaging these clips in the original controller proved quite difficult without the help of a pry tool. Both the thickness of the tabs and their hidden placement are great design choices that ultimately make it difficult for young users to access the internal electronics unless truly necessary.
Due to the Fake Wiimote’s tabs having such a small wall thickness, prying apart the top and bottom causes them to break immediately, making reassembly impossible.
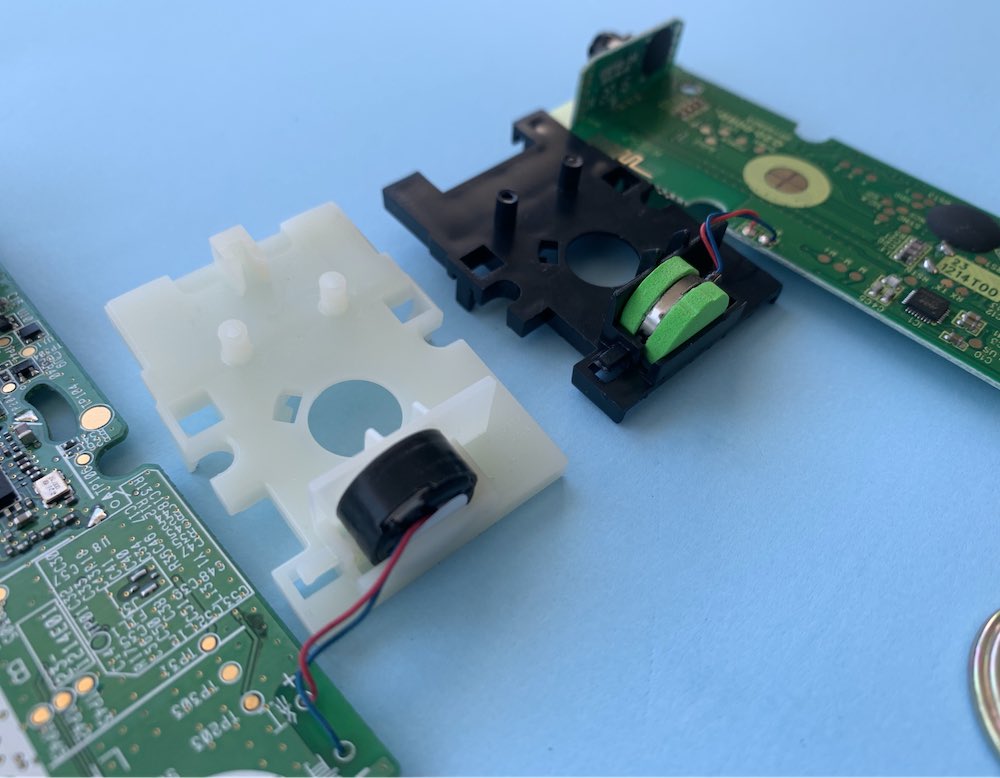
- The haptic “rumble” motor is fixed within a plastic bracket that sits snug around the top end of the PCBA. Although the method of positioning is near identical in both remotes, the different motor thicknesses result in different approaches taken to simplify the assembly process.
- The thickness of the original motor allows for a near perfect allowance between the top/bottom of the motor and the bracket.
- Rather than a perfect allowance, the significantly thinner counterfeit motor is capped with two foam rounds that create a variable gap, which results in a similar, less elegant, fixed effect.
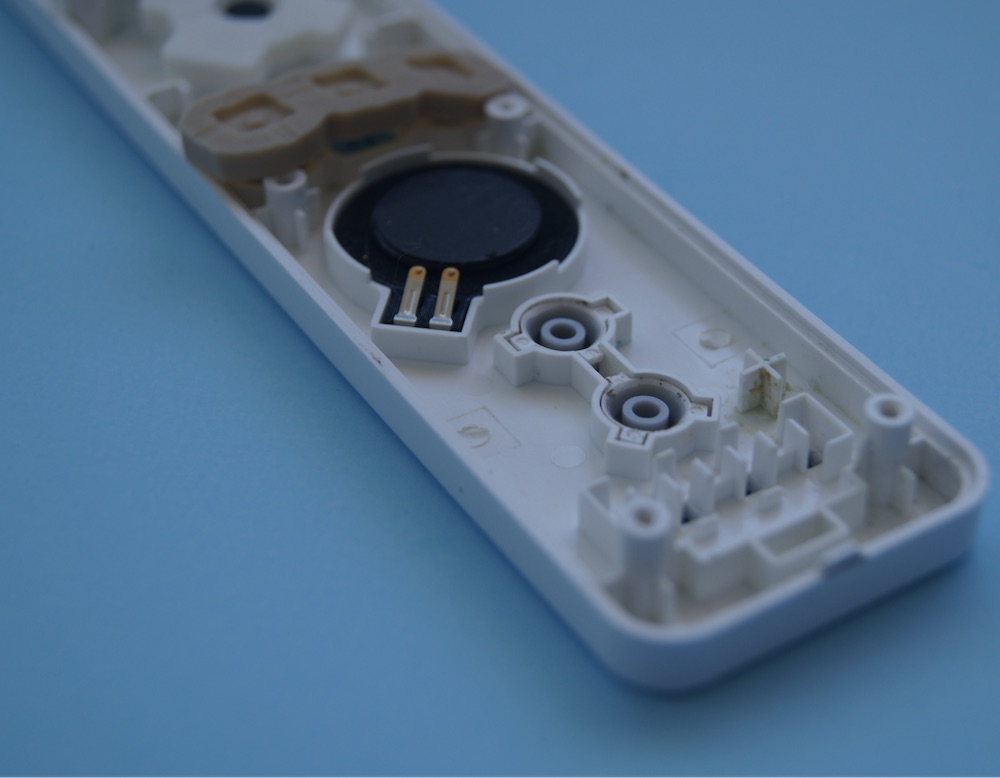
An important component of player experience is the audible feedback that originates from the remote’s speaker, making repeatable placement an incredibly important part of the Wiimote’s assembly process.
The original assembly contains a speaker element with leads that make contact with two contact points on the PCBA. The rib on the internal side of the top enclosure not only keeps the speaker in place and in consistent contact with these points, it also places the speaker closer to the PCBA to prevent gaps that would create a rattling noise when the remote is being used.
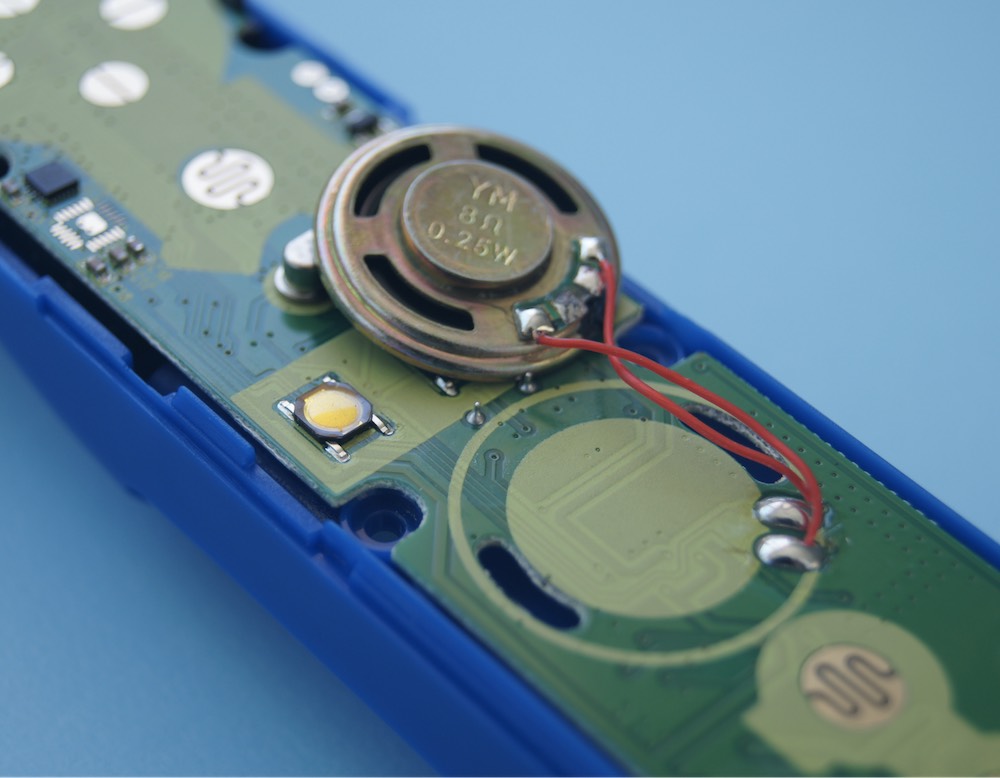
Rather than being an isolated speaker element, the speaker in the fake Wiimote is soldered onto the PCBA — a different, but equally reliable connection. However, the wiring makes it a lot more difficult to assemble and maintain the speaker within the already poorly dimensioned imitation rib — such was the case in our remote, for the speaker was heavily shifted, and the sound was dampened by this unintended partial covering.
Main Takeaways
This comparative teardown presents an interesting case study of the design trade-offs that can occur in the process of making an already viable product less expensive to manufacture. Moreover, we are exposed to the relationship between manufacturing trade-offs and how they directly impact the user experience of a consumer product. Despite the discrepancies in the Fake Wiimote’s haptic interactions, its engineers were successful in creating a fully functioning remote capable of completing the tasks it was created to do (connect to the console, select items on screen, etc).
In an effort to further investigate the Wiimote and Fake Wiimote, I would be interested in increasing the sample size of the Fake Wiimote to more accurate evaluate its quality consistency, the product’s life cycle, and its environmental impact.