Time to read: 6 min
As a mechanical engineer or designer, how much time do you spend thinking about how your parts are going to be machined? Even more specifically, do you know what kinds of tools will be used to make different features or geometries? This article will be your guide to the most common tools used in CNC machining and what they can do.
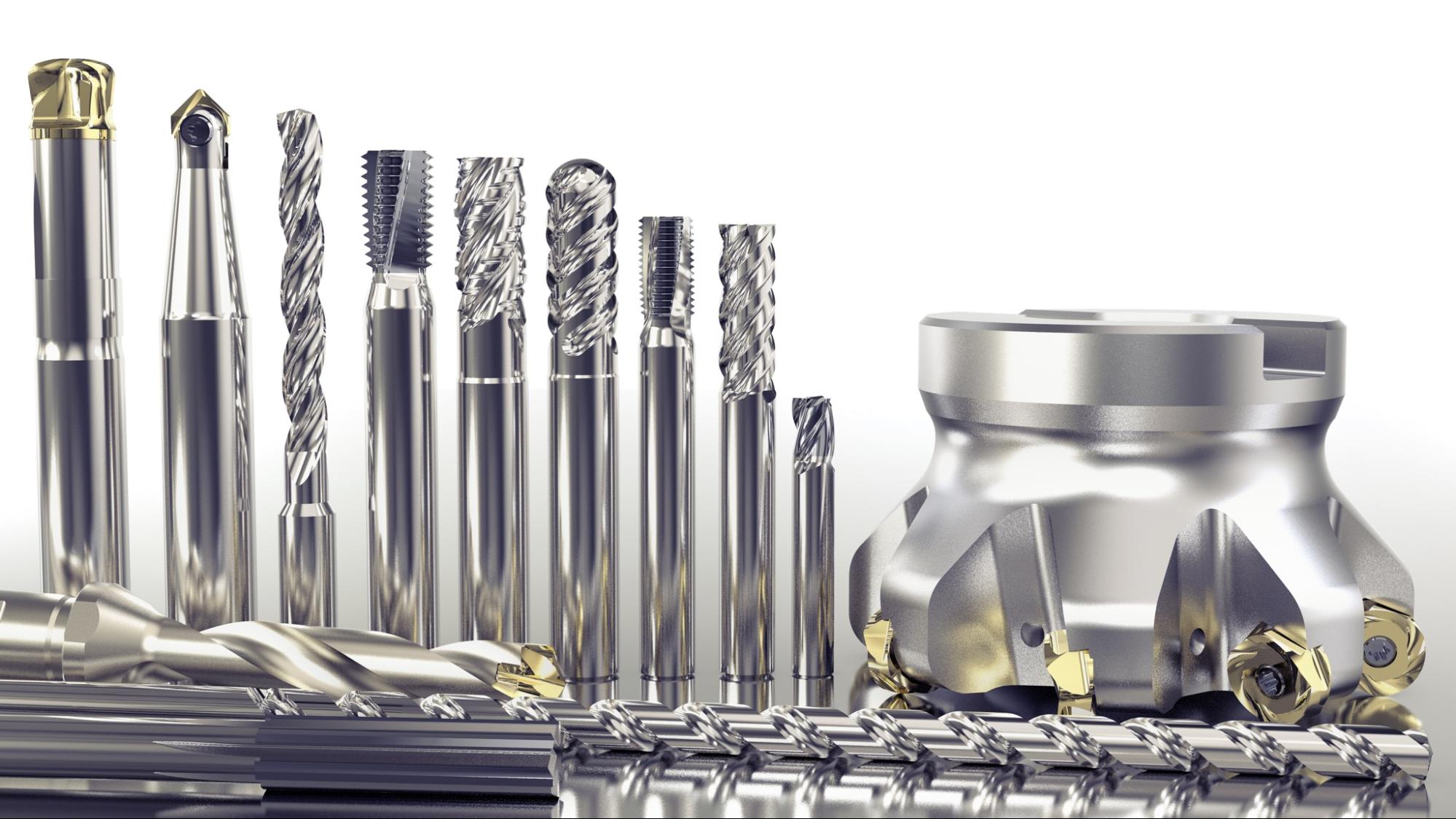
The Importance of Tool Selection
You may be wondering, what difference does it make? There are so many tools out there, they should definitely have the right one for the job. Unfortunately, that is not always the case. Certain geometries, like fillets, do matter in choosing a tool. The radius of a fillet has to be at least half the diameter of the end mill being used. Any smaller, and it becomes more difficult to achieve or requires a tool change, which may otherwise be unnecessary.
When designing features on your part, you want to make sure that they can be machined with standard tool sizes. For instance, if you have drilled holes, make sure they are designed to commonly available drill bits, rather than a millimeter over or under. If possible, you should also design features to be standardized when possible, by sticking with one hole size when you can.
Knowing the tools that are commonly available can also help you design the geometry of your part to be machined more easily. Below is a list of commonly available CNC milling tools that most machines should have on hand. If your design requires a different tool, the machine shop may need to spend extra time or money sourcing a custom tool.
Commonly Available Tools
Face Mill/Shell Mill
A face mill or shell mill is typically the first tool used in a CNC machining operation. These tools are commonly a few inches in diameter and good for removing material from a wide area, making them great for an initial roughing pass to level off the face of your stock material. Then you have a nice even surface to begin machining.
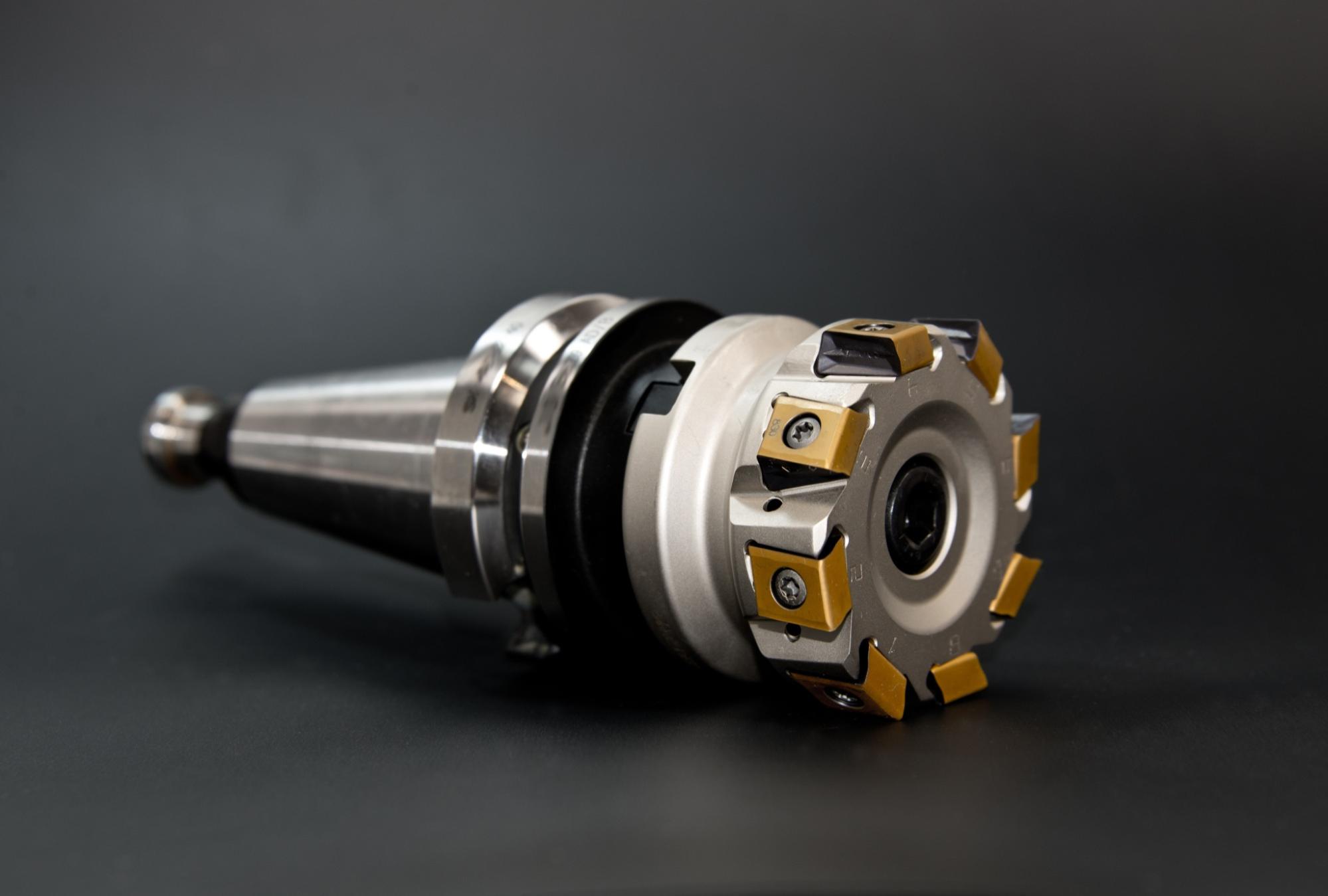
Square End Mill
The square end mill is the most standard tool that every machine shop will have in multiple sizes. Both the bottom and sides can be used for cutting, so these tools can be used for facing the top and sides of a part and for coring out cavities.
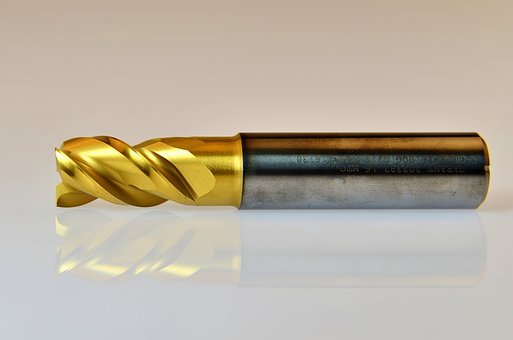
Bullnose End Mill
A bull nose end mill is very similar to a square end mill, but with a slightly rounded edge on the bottom of the tool. This creates a filleted edge between the bottom of a pocket and the side wall, which can be a nice touch.
Ball End Mill
A ball end mill is fully round on the bottom. The diameter of this surface is the same as that of the tool itself. This makes the ball end mill great for surfacing operations like 3D contours. Unlike a square end mill, this tool will not leave sharp corners when machining features.
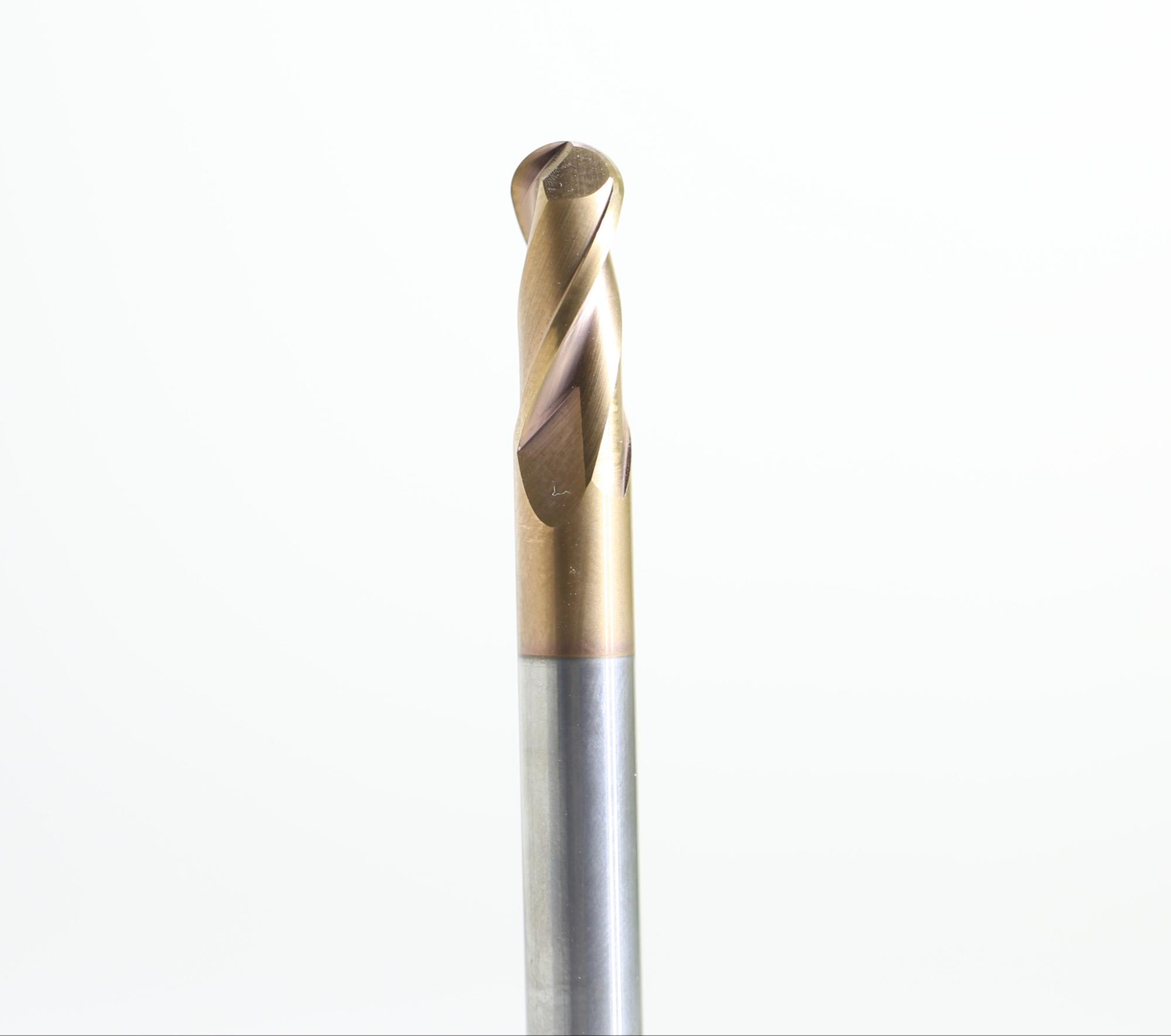
Drill Bit
Drills are your standard tool for making holes in a material. Holes can be used for many things: clearance holes, threaded holes, press fits, or locating. Drills work for all of these. As with other tools, there are standard sizes of drill bits. When you design a hole for your part, look up standard drill sizes so that you are making the machining process as easy as possible. Additionally, design all holes in your part to be the same size where possible to avoid unnecessary tool changes.
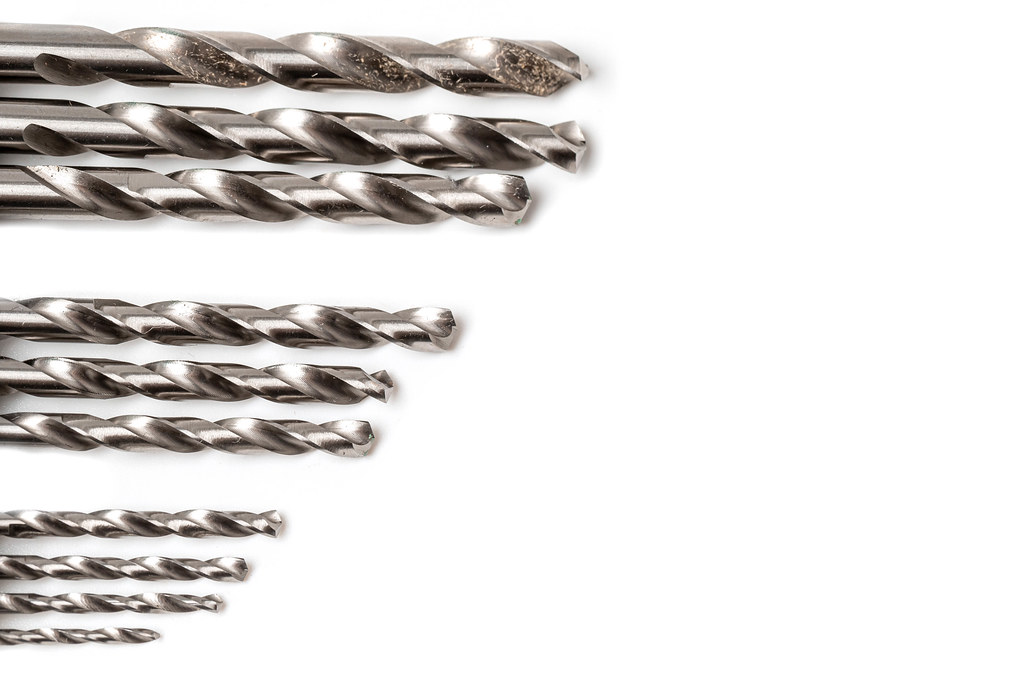
Tap
Once you drill holes, you may want to tap some of them! Tapping is the commonly used term for creating a threaded hole, although there are multiple ways to do it. Cutting taps and forming taps achieve the same end goal, but in different ways. Each requires a hole to be drilled first.
A cutting tap removes more material from this hole, creating the internal threads. As it removes material, it also produces chips. A through hole might be better suited to a cutting tap because the chips have somewhere to go.
On the other hand, a forming tap does not remove material but instead cold forms the material into threads. Forming taps require a slightly larger diameter hole to begin with and can only be used with certain materials. These materials include non-ferrous metals like aluminum. Forming taps are useful for blind holes because they do not produce chips, so you don’t have to worry about chips filling the bottom of the hole. Formed threads are also considered to be stronger. However, cutting taps are able to be used on a wider range of materials.
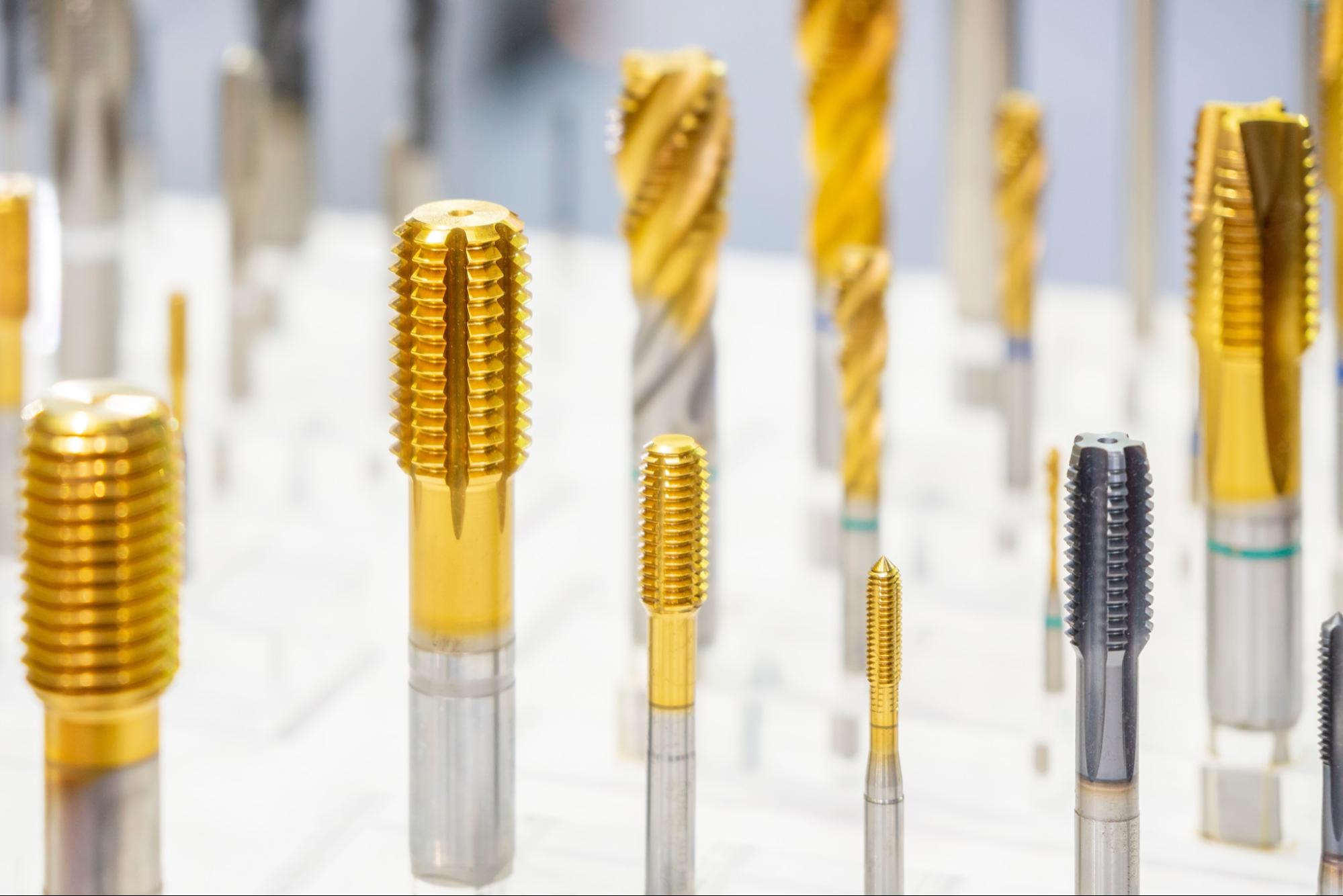
Chamfer Mill
A chamfer mill is self-explanatory; this tool creates external chamfers on sharp corners. THey can also be used to machine countersinks. Chamfer mills are commonly available with 30, 45, and 60 degree angles. This is one instance where this knowledge can help you decide how to design your part: you want to stick with one of these standard angles.
Keyseat Cutter
Usually, undercuts would be impossible to create without an extra setup to put your part in a different orientation. However, keyseat cutters allow you to easily machine undercuts or T-slots in the existing setup. These tools can either be passed completely through a part, to machine a T-slot, or along the side of a part, to create a one-sided undercut. Keyseat cutters are available as straight edges tools or with radii on the corners to create a rounded undercut.
Slitting Saw
A slitting saw is kind of like a very thin keyseat cutter. The radius of the actual cutting surface is usually wider, allowing it to cut deep slots or even split a part. These tools can be very useful and have a lot of different applications.
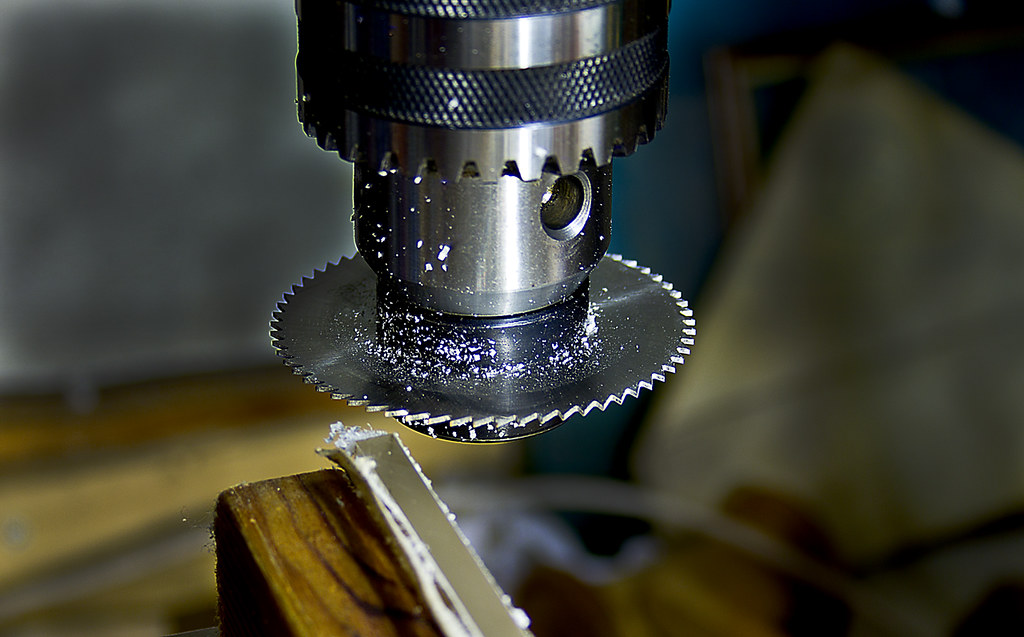
Less Common Tools
The tools above have a wide range of applications and are commonly available everywhere. There are also a myriad of other tools out there that have more specialized uses. If you can think of it, someone has probably created a tool for it. The ones below are less common and not necessarily used on every part, but are still useful!
Reamers
Reamers cannot be used to create a hole, but are very useful for widening an existing hole to the exact diameter needed. They leave a nice surface finish and can hold tighter tolerances than drill bits.
Fly Cutters
Fly cutters are similar in purpose to a face mill, but have just one cutting surface that is mounted on a bar. This bar can be shifted in the tool to create a larger or smaller cutting diameter.
External Radius Cutter
External radius cutters are specialty tools that allow you to add a radius to an external edge, like around the rim of a pocket.
Engraving Tool
Engraving tools are good for engraving text or outlines of shapes on the surface of a part.
Countersink Tool
Countersink tools add a countersink (what!) to a drilled hole. These can also be used to cut chamfers.
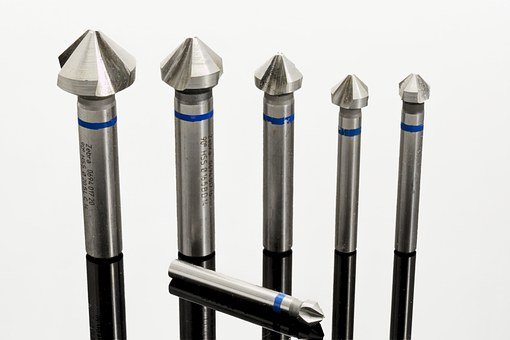
Dovetail tool
A dovetail tool cuts a special kind of undercut into your material.
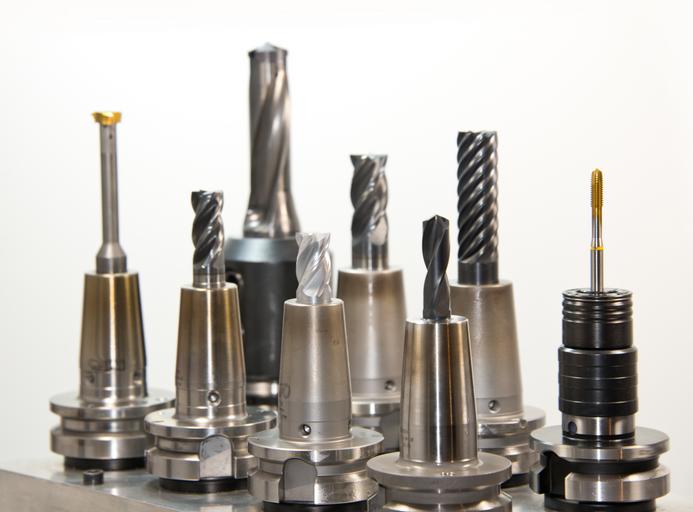
As an engineer, you may not be the one choosing the tools for your CNC machining operation. However, you can think critically about the design of your part to reduce the number of different tools used, and ensure that the tools that are needed are standard and available at most machine shops.
Considering your tool selection is just one part of Design for Manufacturability. To learn other ways to reduce manufacturing effort in your designs, check out our CNC machining services and DFM for CNC Machining Masterclass.