Time to read: 4 min
The mechanical hardness of a material is defined as the ability of it to resist deformation. Hardness is measured by the amount of indentation made by a standardized applied force to the surface of a material.
Hardness is an important characteristic to consider when designing components that interact with each other. For example, when designing a shaft-support bearing interface, the shaft should be harder than the support bearing to prevent indentation of the shaft.
There are also specific considerations when CNC machining hard metals vs soft materials. A basic understanding of what makes a material hard or soft is needed in order to leverage a material’s physical properties to get the best performance from your CNC machined parts. Read on to learn more.
What Makes a Metal Hard or Soft?
There are microscopic differences between hard and soft materials, and there’s a strong relationship between microscopic (and even nanoscale) features of a material and the material’s properties. The hardness of a material is the most important factor to consider when designing for structural applications.
There are two types of hardness: mechanical hardness and chemical hardness. Chemical hardness is a measure of the reactivity or stability of the chemical bonds. Mechanical hardness can be related to chemical bonds because hardness is a measure of the energy required to break chemical bonds by shearing pairs of atoms. Hardness is not a measure of cohesive energy, or the energy required to separate atoms.
For metals, their cohesive energy is dependent on the mobilities of dislocations, the interaction between the dislocations, and the ability of the dislocations to mitigate from the point of impact. Specifically for metals, the hardness is more so dependent on interactions between the dislocations, not the interactions amongst atoms. This dislocation mobility is directly correlated to elastic resistance to shearing.
Hardness is a measure of a material’s resistance to an applied shear force that results in shearing one part of the material over another, or the shearing of atoms relative to each other. It’s also dependent on local polarizability and the valence electron density, as these factors have an impact on the shear modulus (remember: the shear modulus is the response to shear deformation). The shearing of atoms relative to each other is related to valence electron density because it involves a rearrangement of chemical bonds first. Therefore, hardness is closely related to chemical bond configuration and strength.
The table below shows a side-by-side comparison of hardness vs shear modulus vs ultimate tensile strength for some commonly CNC machined metals.
Metal | Hardness | Shear Modulus | Ultimate Tensile Strength |
17-4 PH Stainless Steel | 85 Rockwell B | 11200 ksi | 200 ksi |
Kovar | 78 Rockwell B | 7500 ksi | 75 ksi |
Grade 2 Titanium | 80 Rockwell B | 5510 ksi | 49.9 ksi |
Grade 5 Titanium | 36 Rockwell B | 6380 ksi | 138 ksi |
2024 Aluminum | 75 Rockwell B | 4060 ksi | 27 ksi |
6061-T6 Aluminum | 60 Rockwell B | 3770 ksi | 42 ksi |
6063 Aluminum | 50 Rockwell B | 3740 ksi | 28 ksi |
7075-T6 Aluminum | 87 Rockwell B | 3770 ksi | 83 ksi |
360 Brass | 80 Rockwell B | 5370 ksi | 58 ksi |
304 Stainless Steel | 92 Rockwell B | 12500 ksi | 73.2 ksi |
316 Stainless Steel | 95 Rockwell B | 11000 ksi | 79.8 ksi |
Zinc | 63 Rockwell B | 35 ksi | 5.3 ksi |
CNC Machining Hard Metals vs Soft Metals?
Because the hardness of a material is a measure of its ability to withstand shear forces before deformation, it also determines the material’s wear resistance, which impacts CNC machining. A softer material cannot withstand as much shear force as the material starts to slide across itself and deform, so it will have a higher tendency to smear during CNC machining. Expert machinists know how to manage this characteristic to precision machine even the softest metals, however.
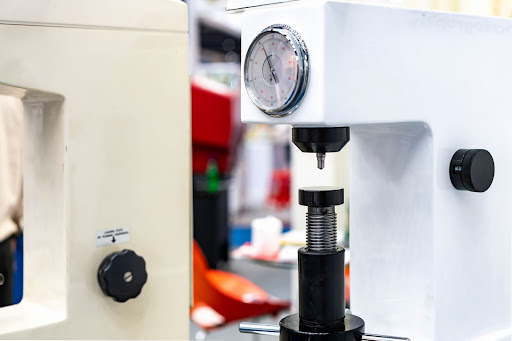
Along with increased hardness comes increased wear resistance because harder materials are more difficult to cut through. A material’s ability to be cut and the type of tooling capable of cutting the material are directly correlated to the hardness of each material. For harder materials, diamond-infused cutting tools are a good choice, as are carbides and ceramics. Conversely, soft metals can be machined with almost any tooling, but managing the speed of the tool well is critical to get clean cuts without smearing.
Pro-tip: Regardless of your tooling material, roughing is a good technique for the beginning phase of CNC machining hard materials. Roughing is pre-machining materials before annealing or hardening treatments.
Harder metals are not as forgiving when it comes to tooling chatter, so they must be machined with more rigid, higher precision tooling. Also, using the right tool shapes is key to successfully CNC machining hard metals. For example, ball end mills are great for finishing or roughing hard metals because they disperse heat well and limit workpiece deformation. Corner radius tools are good for hard metals with broad or flat shelf portions, but they can cause chipping.
Sourcing Simplified – Start Your Next Project With Fictiv
Whether you’re using brass, tool steel, or any number of other metals for your next project, Fictiv has you covered. We are your operating system for custom manufacturing that makes CNC machined part procurement faster, easier, and more efficient. In other words, Fictiv lets engineers, like you, engineer. Create an account and upload your part to see what our instant quote process, design for manufacturability feedback, and intelligent platform can do for you. Our CNC machining service can create quality precision parts in as little as 2 days!