Time to read: 6 min
There are a lot of CAD (computer-aided design) file types out there, each with its own names, formats, and parameters. From STEP files to STL files, to IGES and more, it can be difficult to differentiate between them. This article will help you understand the difference between these file types, and which are best for uploading to a 3D printer’s CAD software or sending to a 3D printing service.
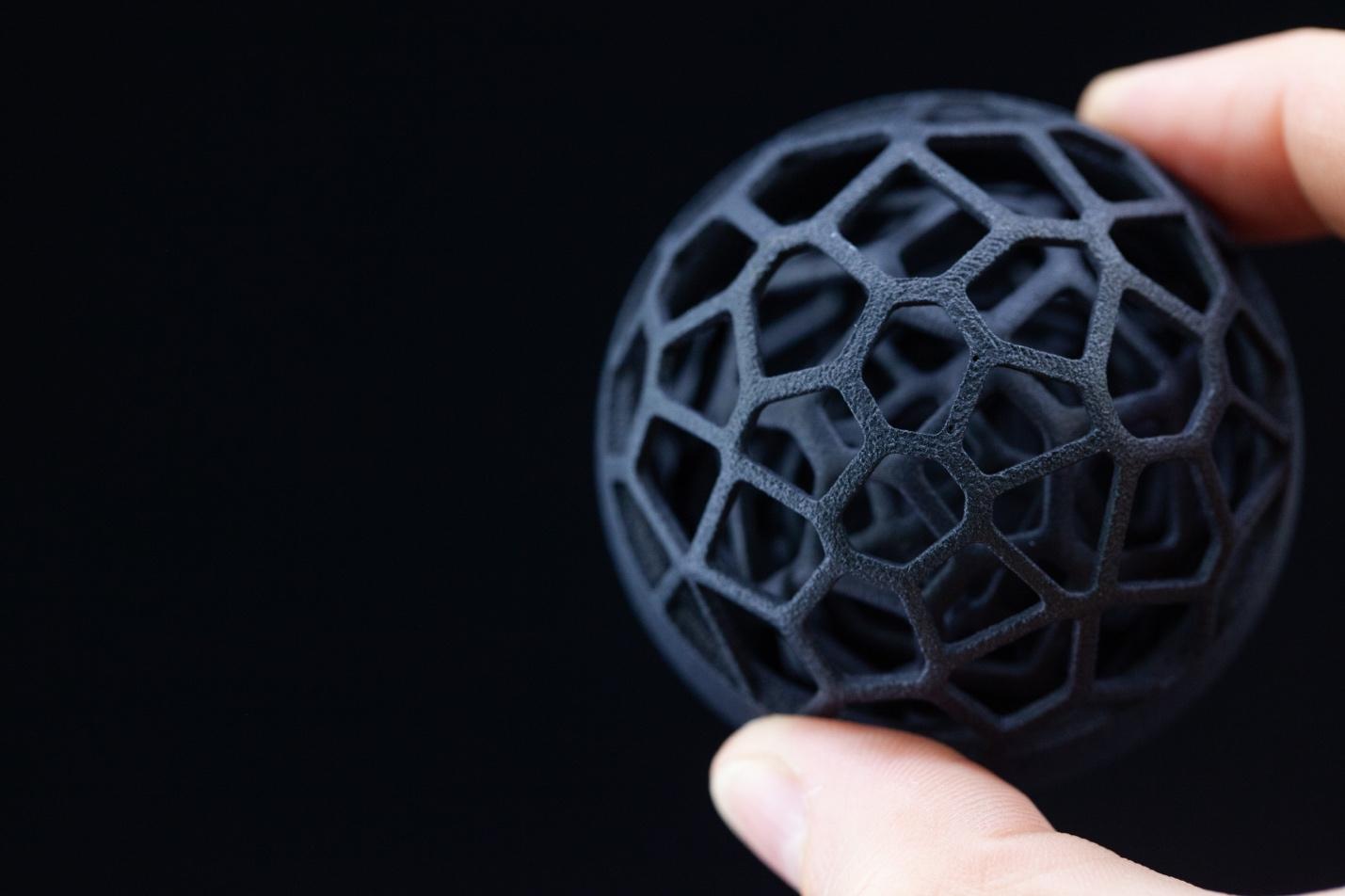
Overview: CAD Model Types
Before we review the steps for CAD file formatting for 3D printing, here’s a brief overview of the different CAD formats.
There are, in general, two main CAD file format categories:
Native
- Native CAD files are copyrighted intellectual property of the system/CAD program for which they are utilized. They contain the most detail and functionality because they don’t consolidate or gloss over areas of a 3D CAD design file for 3D printing
- Examples: .dwg, .blend, .x_t, .sldprt, .sldasm, .ipt, .iam, .skp
Neutral
- Neutral CAD files are open-format and not copyrighted intellectual property of any system or CAD program. They are useful for sharing files across two or more different CAD platforms, but they result in a small amount of fine detail loss when converting to a neutral file type
- Examples: .stl, .amf, .obj, .stp, .step, .3mf, .iges
Pro tip: For an in-depth review of each format, check out our article on 3D file types.
CAD files may also be distinguished based on the method by which they were created and how they are structured:
- Parametric (solid)
- Mesh (NURBS)
Parametric Modeling
In 3D modeling, a parametric model is one that consists of solid blocks or vectors that have both magnitude and direction. Parametric modeling is a process whereby the shape of a model’s geometry is automatically changed when a dimension value is altered; it’s based on designing features and constraints of a solid body or assembly.
The implementation of parametric modeling originates through the CAD software’s programming, which determines the dimension and shape of the solid model. Typically, parametric modeling software (such as 3D AutoCAD) utilizes feature-based modeling tools to allow the manipulation of a model’s attributes.
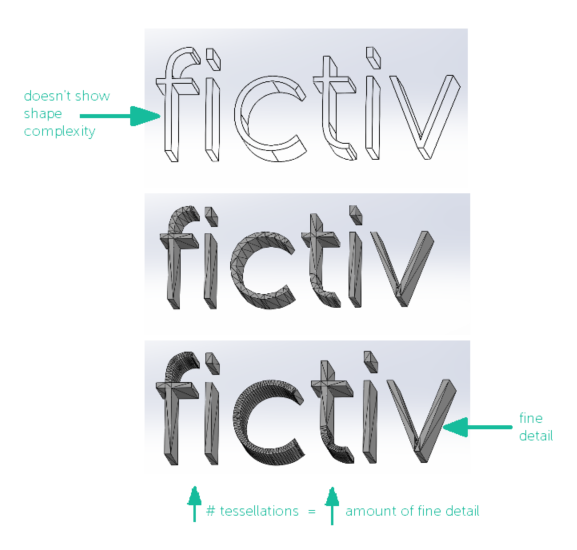
Mesh Modeling
A mesh model, on the other hand, is a collection of small triangles (tessellations) that make up a surface. A mesh model is typically created when a part is 3D scanned, which results in a copious amount of data points (dots) that comprise a point cloud. The mesh is created by resolving these points into variably sized triangles by connecting the dots. Although uncommon due to the complexity and tediousness of the process, a mesh may also be manually created.
Mesh files are primarily utilized for the following scenarios:
- Inspection of a part to determine if it conforms with designed dimensions or features. This involves 3D scanning a part and overlaying the 3D scan on a parametric, solid CAD model. The areas where the two do not overlap are utilized to determine if a scanned part is out of tolerance.
- Engineering analysis of a design. Mesh models are utilized for a variety of engineering simulations and analyses, such as finite element analysis.
- 3D scanning of legacy parts to source them and/or reverse engineer them.
- 3D printing directly from a scan. 3D printer files support STL files so a mesh in an STL format can be directly printed.
If you compare these two types of models to a 2D image file, a parametric model is like a vector file (.AI, .SVG, .DXF) while a mesh model is more like a pixel image (.PNG, .JPEG). Just as a pixel image approximates a vector file, when converting a parametric model to a mesh model, a mesh file (.STL) approximates a parametric file (.STEP).
Pro tip: If you’re looking for an in-depth comparison, check out this article about mesh modeling vs solid modeling.
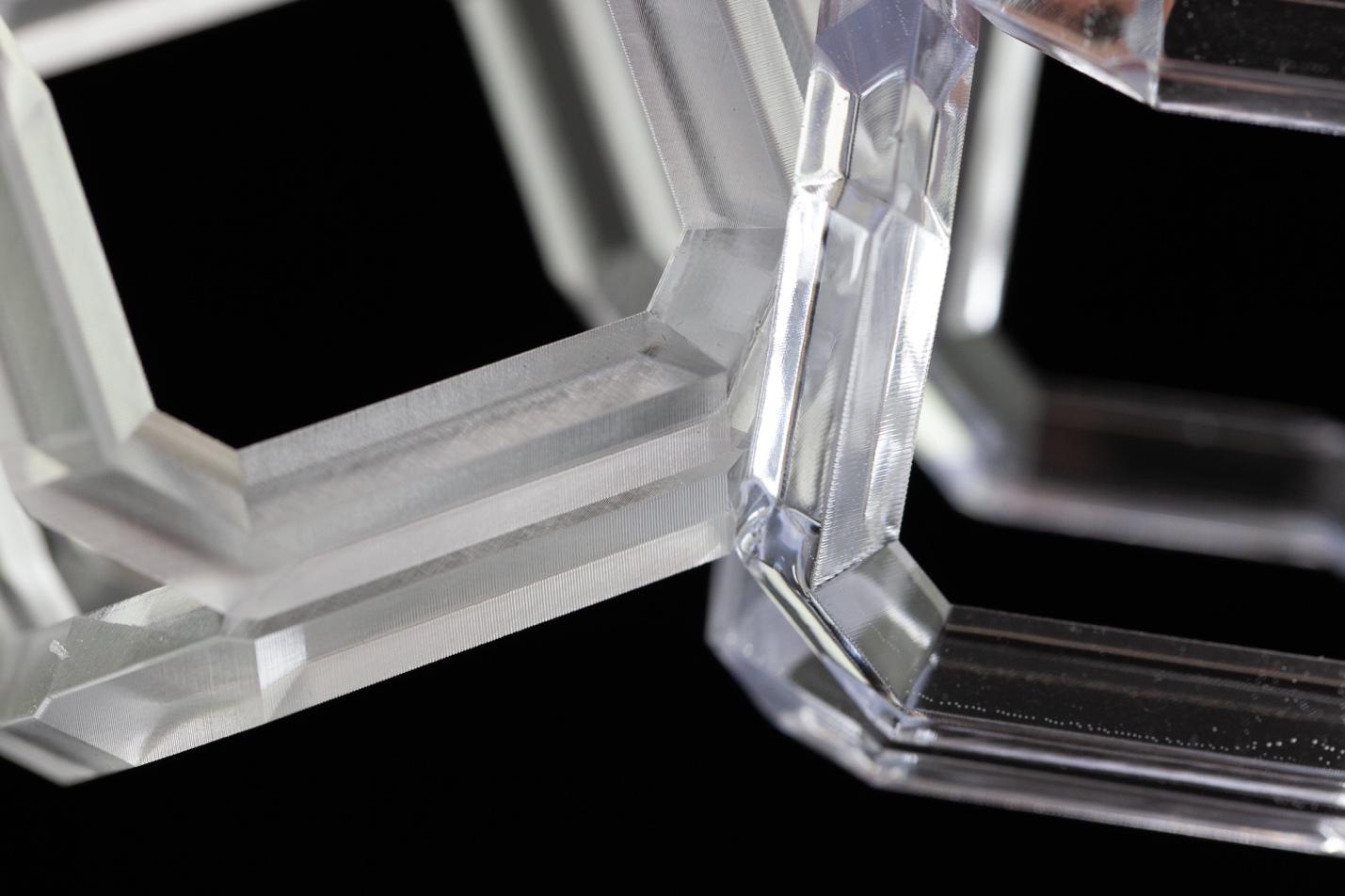
Best Parametric File Types for 3D Printing in 2022
For 3D printing, both mesh and parametric structured file types are acceptable. Let’s dive into the optimal CAD models for 3D printing and which types of CAD files Fictiv experts recommend.
There are 3 main parametric file types used in 3D printing:
- STL (Stereolithography or Standard Tessellation Language)
- STEP (Standard for the Exchange of Product model data)
- Native CAD
First Choice: STL Files
There are two types of STL files:
- ASCII: Large file size and not recommended
- Binary: Compressed file, which is better for saving and sharing
STLs were originally developed by 3D Systems specifically for additive manufacturing and are widely known as the industry standard. They are neutral and easy to implement.
However, STL files for 3D printing aren’t without their shortcomings. For example, there are no associated units (dimensional ambiguity) and holes or gaps (watertightness) can cause issues when producing parts. Experts say that STL files may be replaced by newer and better optimized file formats.
Second Choice: STEP Files
There are 2 main types of STEP files:
- AP203: Originally created for the aerospace industry
- AP214: The newest standard, originally created for the automotive industry
We believe that STEP files are the best file format for transferring CAD data. STEP files carry all the parametric data required for manufacturers to accurately read the size and geometry of the part you need.
Pro tip: STEP AP214 will save the colors and layers in your CAD program when exporting as an STL. When saving for multi-material prints, we prefer this standard since it helps to distinguish the different solid bodies.
Third Choice: Native Files
As a reminder, native CAD files are copyrighted intellectual property of the system/CAD program for which they are utilized. There are many different CAD programs and even more native file types. Here are some of the popular programs and file types Fictiv accepts:
- Autodesk: .ipt
- Dassault Systèmes: .sldprt, .3dxml, .catpart, .catshape, .cgr, .dlv, .exp, .model, .session
- PTC: .prt
- Siemens PLM: .jt, .par, .prt, .x_t, .x_b
- Other programs: .3dm, .vda, .prt, .x3dv, .ifc., .mf1, .neu, .prc, .sab, .sat, .u3d, .vda, .xas, .xpr
Best Mesh File Types for 2022
At Fictiv, we’re also able to print directly from 3D CAD model mesh files. Our preferred mesh file types are: .stl, .3ds, .collada, .dae, .obj, .off, .ply, .v3d, .pts, .tri, .acs, .x3d, .wrl.
How to Export an STL File for 3D Printing
The basic steps for exporting an STL file for 3D printing are:
- Modeling: Obtain a solid model or mesh model of the component you wish to 3D print. Note, it is best to utilize neutral or open-source file formats.
- Slicing: Convert the 3D model into something which can be printed. This utilizes slicing software and requires some of the printer information to be input.
- Obtaining a 3D-printable model: Create a file containing the instructions for the 3D printer to perform the printing (toolpath information). The most common format is a G-code.
Common STL Export Considerations
It’s common to run into problems when exporting an STL file. Since a lot of people use STLs, we’ll point out a few important considerations and walk through specific exportation steps for the most common CAD programs.Alternatively, you can skip the export to STL and upload your native CAD files for an instant quote on our platform today.
Resolution
The most important consideration is the resolution of your model. If you try to export an STL with a low resolution, your model will look faceted. If you export an STL with too high of a resolution, your model will become very large and difficult to share.
Two Main Program Settings
There are two main settings to consider with every CAD program:
- Chordal Tolerance or Deviation: This is the maximum distance between the surface of the original design and the surface of the STL triangle created.
- Angle Control: This is the allowable deviation between adjacent triangles. You should think about approximating a curved surface with lots of flat triangles. The more shallow the angle, the closer the approximation is to the curved surface.
Specific Settings by CAD Program
- File > Save As
- Set save as type to STL (*.stl)
- Click on Options
- Set Deviation to 0.0005in and the Angle to 5 deg
- Click save to export the file
- File > Save Copy As
- Save as Type > STL
- Click the Options button, and choose the High detail level
- Save
Check out our expert article with tips and tricks for exporting to Rhino. If you’re looking to convert a STEP file to an STL file, check out one of the numerous free, online tools that can do the work for you!
Fictiv is the ultimate manufacturing partner that provides an intelligent platform to upload your 3D models and 2D drawings for an instant quote and DfM feedback. We’re experts in CNC Machining, Injection Molding, Urethane Casting, and 3D Printing. You can learn more about our preferred file types for each process here. If you’re ready to start uploading your 3D printing design files, visit Fictiv for an online quote in minutes.