Time to read: 6 min
Plastic injection molding can apply a specific type of finish — described in terms of polish or texture — to molded parts, and many different polishes and textures can be achieved. The desired surface finish is applied toward the end of the mold-making process, and during plastic injection molding, the finish is transferred from the mold to the surface of the molded parts.
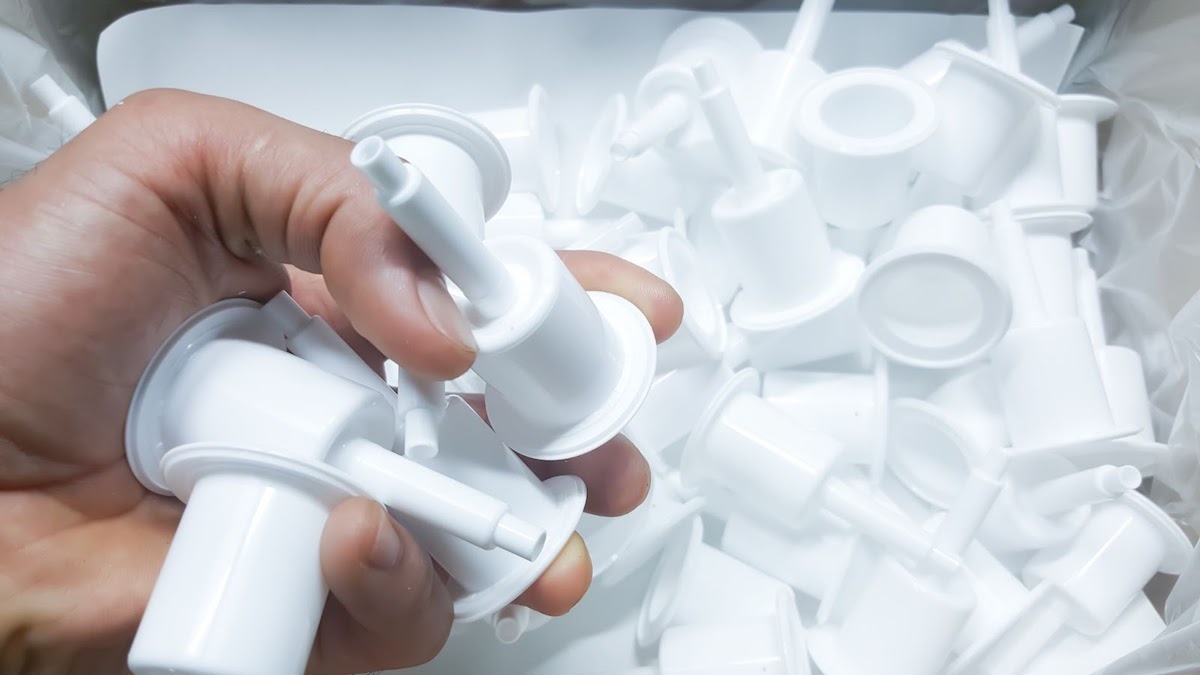
Other manufacturing processes, such as 3D printing and CNC machining, typically finish parts through secondary operations. This approach is more time-consuming and more expensive, especially with higher part volumes. Compared to plastic injection molding, there are also fewer options for polishing plastic and adding texture.
Mold Polishing and Mold Texture Standards
Trade associations and companies define standards and designations for injection molding finishes and textures. The Society of the Plastics Industry (SPI) and the Society of German Engineers / Verein Deutscher Ingenieure (VDI) are two of these trade associations, while Mold-Tech (MT) and Yick Sang (YS) are companies that have developed their own standards. That’s why you’ll hear terms like “SPI finishes” and “Mold Tech textures” during design for manufacturing (DFM) discussions.
Injection Molded Finish Options
Within each surface finish standard, there are hundreds of different options. For identification purposes, each surface finish callout consists of the organizational acronym followed by letters or numbers. For example, SPI-A2 is from the Society of the Plastics Industry (SPI) and indicates a high gloss or transparent finish. MT-11010 is a Mold-Tech designation for light mold texture.
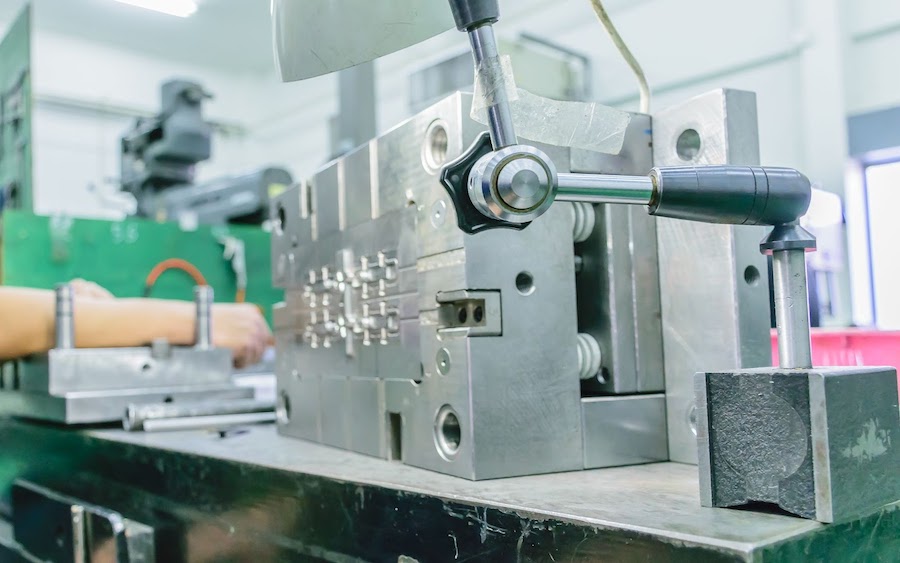
Surface Finish for Plastic Parts
Although there are different surface finishing standards, they all define polished and textured finishes and divide them into subcategories based on either on appearance or method.
- Polished Finishes
- High glossy or transparent
- Semi-glossy
- Matte
- Textured Finishes
- Bead blasting
- Chemical etching
- Mirror EDM
Keep reading to learn about some common types of mold polishes and mold textures, plus design tips that’ll help you get the best results when polishing and finishing your parts — Fictiv’s Injection Molding Design Guide provides even more information and injection molding insights.
Download the Injection Molding Design Guide
Polished Finishes
Injection molds are machined with CNC or EDM equipment, and when machining is complete, the mold core and cavity have milling marks or EDM marks. The two halves of the mold are then sanded and polished to remove these surface imperfections. Different finishing methods are used, but the industry standard for mold polishing comes from SPI. There are nine levels of standard polished finishes, and typically each type is done by hand by highly-skilled technicians.
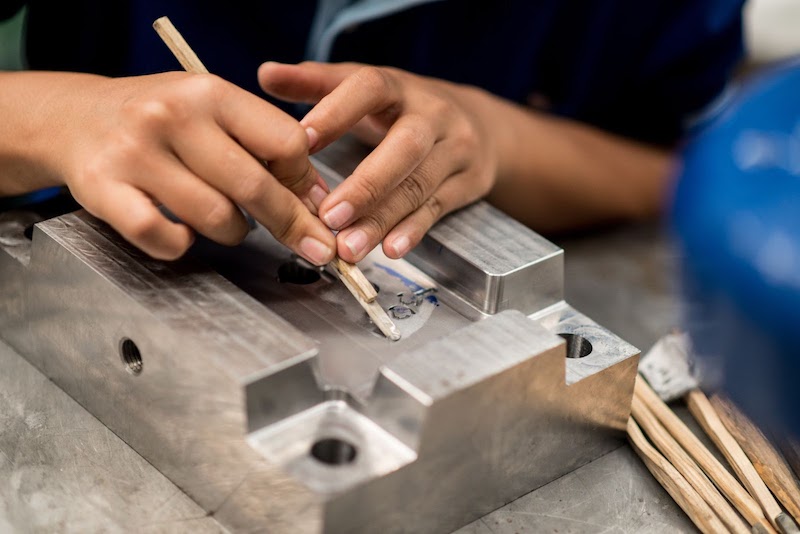
High Glossy or Transparent Finishes
SPI standards A-1, A-2, and A-3 are the highest levels of mold polishing. They produce either a high gloss or transparent finish on plastic parts — for opaque grades of plastics, the finish is glossy. For clear grades of plastics, the finish is transparent. All three SPI A-levels require heavy mold polishing with a rotary tool and diamond buffing paste.
Fictiv typically recommends a hardened steel mold to achieve SPI levels A-1, A-2, or A-3. Stainless steel is used for A-1 and NAK80 steel is used for A-2 or A-3. Hardened steel withstands potential ripples, sags, and crests from the rotary tool and polishes better than molds made from aluminum or softer steels.
The following surface finish chart describes SPI A-level standards, their finished methods, and surface roughness measurements. Note that higher levels of surface finishing and the use of hardened steels effects mold pricing and lead times.
SPI Standard | Description | Finishing Method | Surface Roughness Ra (μm) |
A-1 | High Glossy / Optically Transparent | Grade #3, 6000 Grit Diamond Buff | 0.012 to 0.025 |
A-2 | High Glossy / Transparent | Grade #6, 3000 Grit Diamond Buff | 0.025 to 0.05 |
A-3 | High Glossy / Transparent | Grade #15, 1200 Grit Diamond Buff | 0.05 to 0.10 |
Semi-Glossy Finishes
SPI finishes B-1, B-2, and B-3 are the middle levels of polishing. They produce a semi-glossy finish using 600-grit, 400-grit, or 320-grit sandpaper, respectively. Surface finishing is achieved with various-sized filing tools and requires sanding back and forth across surfaces. Compared to the SPI A-level finishes, more lines are evident because of this sanding motion.
This surface finish chart below describes these SPI B-level standards, their finished methods, and surface roughness measurements.
SPI Standard | Description | Finishing Method | Surface Roughness Ra (μm) |
B-1 | Semi-Glossy – Fine | 600 Grit Paper | 0.05 to 0.10 |
B-2 | Semi-Glossy – Medium | 400 Grit Paper | 0.10 to 0.15 |
B-3 | Semi-Glossy – Coarse | 320 Grit Paper | 0.28 to 0.32 |
Some mold features, such as those that are designed to accommodate thin, deep ribs or small bosses, are more challenging to polish because they’re smaller than a file can reach. Typically, these features are on non-visual surfaces on the cavity side of the tool. There are ways to construct the tooling, such as by using sub-inserts, so that these features can be reached for polishing — for best results, you should discuss this during the DFM stage of mold construction.
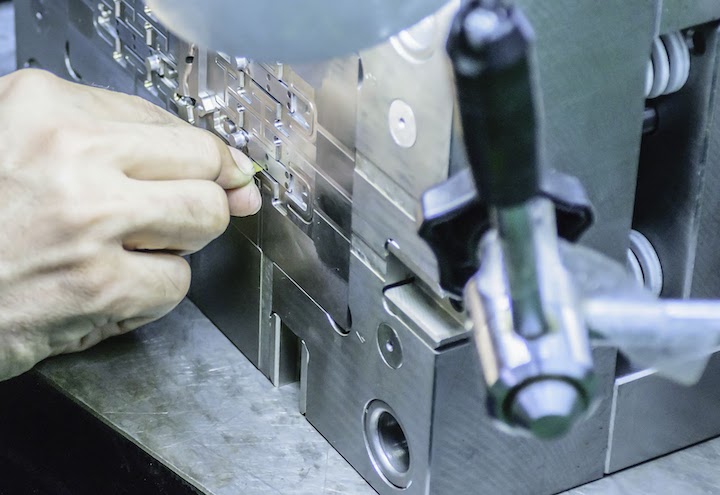
Matte Finishes
SPI standards C-1, C-2, and C-3 are rougher and are the fastest and least expensive finishing methods. Applications include cosmetic or interior (non-visual) surfaces. For each C-level SPI finish, a sanding stone tool with a specific grit is used.
SPI Standard | Description | Finishing Method | Surface Roughness Ra (μm) |
C-1 | Matte finish – Fine | 600 Grit Stone | 0.35 to 0.40 |
C-2 | Matte finish – Medium | 400 Grit Stone | 0.45 to 0.55 |
C-3 | Matte finish – Coarse | 320 Grit Stone | 0.63 to 0.70 |
Textured Finishes
Injection molded parts can also have a textured finish instead of a polished finish. There are hundreds of texture options, but three main texture systems:
- SPI and Mold Tech textures (United States)
- VDI textures (European)
- YS textures (Asian)
In addition to light, medium, and heavy textures, options include simulated wood or leather grain and checkerboards or diamond patterns. Fictiv typically uses blasting, chemical etching, or mirror EDM to produce mold textures; however, laser etching and standard sinker EDM are also used by the industry.
Bead Blasting
Bead blasting creates textured finishes by using a stream of highly-pressurized air to spray various media onto mold surfaces. SPI finishes D-1, D-2, and D-3 all use a dry blast method, but with different media. To save time and reduce the costs associated with outsourcing, factories that make prototype tools often have bead-blasting machines in-house.
This surface finish chart describes SPI standards for mold texture.
SPI Standard | Description | Finishing Method | Surface Roughness Ra (μm) |
D-1 | Light Texture | Dry Blast Glass Bead #11 | 0.80 to 1.00 |
D-2 | Medium Texture | Dry Blast #240 Oxide | 1.00 to 2.80 |
D-3 | Heavy Texture | Dry Blast #24 Oxide | 3.20 to 18.0 |
Chemical Etching
Chemical etching creates a texture by applying a special film to the mold, which is then placed in an acid bath. The acid etches away the surfaces that are not protected by the film, creating the desired surface finish. These types of mold textures are relatively complex, so the work is usually outsourced to factories that specialize in finishing. Depending on the facility, this work can take between 2 and 5 days.
Fictiv recommends discussing chemical etching textures during your DFM design review — especially if your design is in the engineering validation testing (EVT) stage or the design validation testing (DVT) stage, or if engineering changes may occur. It may be best to apply texture to your tooling after initial sampling and engineering changes (ECs) when the design is locked.
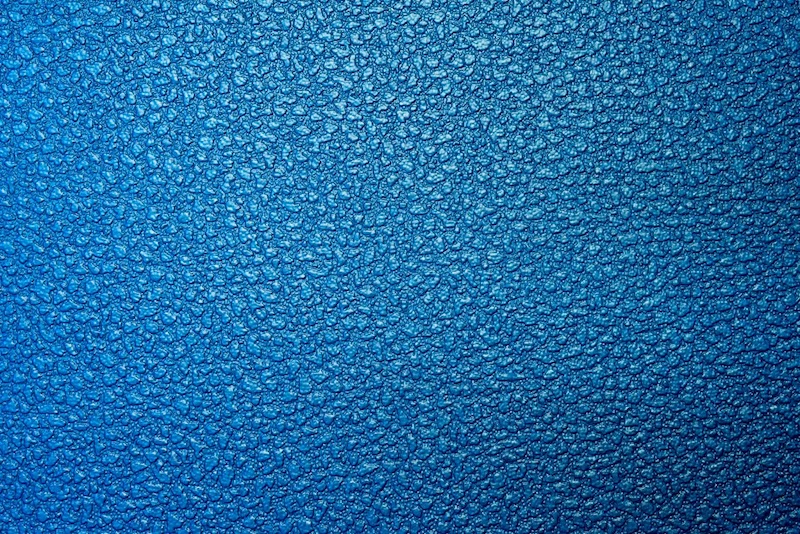
Mirror EDM
Sometimes, a product’s dimensional tolerances or design intent require avoiding any handwork on the tooling. For example, one of Fictiv’s customers developed a smartwatch where the design intent was for mating parts on the back cover and front bezel to appear seamless when assembled.
For these types of products, Fictiv recommends applying a light texture of Ra 0.2 (μm) via mirror electro-discharge machining (EDM). With this process, a copper electrode is machined and polished in the shape of the part surface and creates electrical sparks that burn away the surface of the mold. This creates the same shape and achieves the desired surface finish.
For mirror EDM, hardened steel is preferred because it can support a smoother surface finish. Mirror EDM is more time-consuming than CNC machining or hand polishing, however, and the machines are usually German, Japanese, or Swiss. Because this type of texture is the most costly, Fictiv can help you to decide if you need a mirror EDM texture.
Tips for the Texture of a Plastic Part
For textured surfaces on plastic parts, a heavier draft is applied so that the part can be released from the mold easily, and without drag marks. The surface finish chart below lists the required draft for the most common finishes.
SPI Standard | Draft | Mold Tech Texture | Draft |
A-1 | 2° | MT-11000 | 1° |
A-2 | 2° | MT-11010 | 1.5° |
A-3 | 2° | MT-11020 | 2.5° |
B-1 | 1° | MT-11030 | 3° |
B-2 | 1° | VDI Texture | |
B-3 | 1° | VDI-18 | 1° |
C-1 | 1° | VDI-24 | 1.5° |
C-2 | 0.5° | VDI-33 | 3.0° |
C-3 | 0.5° | YS Texture | |
D-1 | 1° | YS20001 | 1° |
D-2 | 2° | YS20005 | 3° |
D-3 | 3° | Mirror EDM | 3° |
Fictiv is able to support multiple surface finishes on the exterior surfaces of the part. Please provide a color-coded image and note the type of finish and the surface locations. Because the tool will be masked, we suggest creating a stepped feature of 0.010” (0.25 mm) to separate these surfaces.
Finally, it’s important to understand that choosing the best surface finish for your injection molded parts can be a complicated matter. Fictiv’s DFM experts can help guide you through the process, so create an account to get started.