Time to read: 5 min
Whether you have a new and exciting part design, or you’ve been asked to optimize an existing part, choosing the optimal CNC cutting method can be difficult. CNC (Computer Numerical Control) machining is a large and growing industry, encapsulating a variety of manufacturing processes — all aimed at producing parts by removing material. In this article, you’ll find our best tips for choosing the optimal CNC cutting method to get quality, precision parts using the following methods:
- CNC Milling – 3, 4, and 5-axis machining capabilities for simple and complex geometries
- CNC Turning – Standard and live tooling capabilities for cylindrical parts such as pins, shafts, and spacers
- Electrical Discharge Machining (EDM) – Sinker and wire EDM capabilities for cutting deep pockets and complex features such as gears and keys with a keyway
- Gear Hobbing – Capabilities to cut gears with a wide range of stock hobbing tools
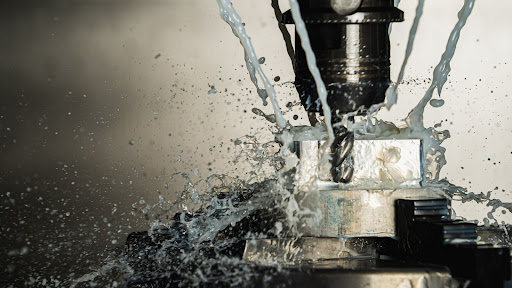
Choose CNC Cutting Method Based on Material Choice
One of the first and most important decisions made in new part designs is the material selection because the chosen material dictates which CNC cutting methods you can use to machine your desired part.
Pro-Tip: Check out our article where we rate common materials based on machinability, environmental resistance, and strength-to-density ratio (specific strength).
Best CNC Cutting Method for Hard Materials
Over the past few decades, there has been an increase in specialty metal alloy development. This is largely due to an increased understanding of materials science at an atomic level and new, innovative technologies. For example, there is a class of superhard materials with hardness values exceeding 40 GPa (Vickers hardness). They’re nearly incompressible solids with superior, high electron density and covalent bond strength. For comparison, diamond has a hardness of 70-150 GPa, whereas a 2021 project developed a new alloy capable of hardening up to 2500 GPa.
All types of CNC cutting can be used to cut hard materials, but EDM and CNC Milling are specially optimized for the task. The key to remember is that your cutting tools or wire must be harder than the material you’re cutting through. Tool durability can also be an issue, so consider carefully which one you choose — not all cutting tools are optimized for cutting through hard materials. Also, cutting through harder materials requires more energy dissipation because more heat is generated when cutting through harder materials.
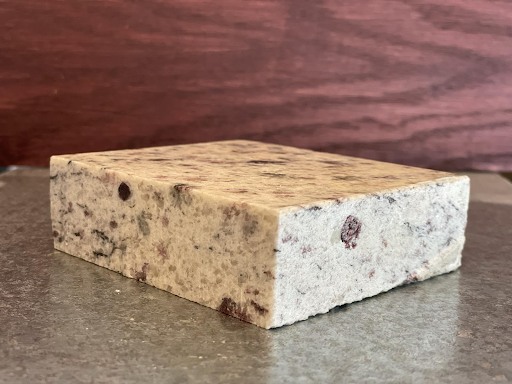
Tips for CNC Machining Hard Materials with EDM
- Choose the appropriate wire for wire EDM. Coating the wire (like zinc coatings) improves the wire stiffness, which in turn improves the cut speed and flushing at the cut surface. Pro-Tip: Use a larger diameter wire to make a rough cut then follow up with a smaller wire to create the finished edge.
- Take a look at the granite block pictured above, which was cut with wire EDM for my own home remodel. Granite is almost as hard as it gets for effective wire EDM cutting, and you can see that the shop didn’t follow up with a smaller wire diameter cut to smooth out the edge on the right.
- Utilize adaptive controls, where possible, to reduce the re-cast layer and heat-affected zone volumes.
- Change out dielectric fluid and tooling more often for sinker EDM applications, as the tooling tends to wear at a more rapid rate when harder materials are used.
Tips for CNC Milling Hard Materials
- Choose the right tool type for cutting through hard materials. Ball end mills are optimal because they help to dissipate heat from cutting while reducing the risk of deforming the workpiece.
- Choose the right tool material. Harder materials such as solid carbide and ceramics are good for CNC cutting parts from hard materials.
- Hold off until parts have been heat treated, if possible.
- Use the correct type and amount of coolant or lubricant to help to dissipate heat generated during the CNC cutting process. Spindle cooling systems offer excellent heat dissipation.
- Ensure radial step-over distance is ~10-20% of the tooling diameter.
- Reduce runout by using high-quality tool holders. These also reduce vibration, which provides higher precision cuts — dovetail holders are typically a good start.
Choose CNC Cutting Method Based on Desired Tolerance and Geometry
In general, EDM can hold tighter tolerances than CNC milling or CNC turning, or even gear hobbing. See our CNC tolerance sheet to learn more about the tight tolerances Fictiv is able to deliver. Our experienced manufacturing partners are able to achieve tight tolerances as low as a fraction of a mil (around 0.0004 inches) with CNC gear hobbing — the kind of precision companies like Hebi Robotics needs. Our CNC milling and turning processes can achieve even tighter tolerances than hobbing can, but when extremely high precision is required, EDM is the best choice.
Pro-Tip: for more information on what makes precision machining capable of achieving such remarkably tight tolerances, check out this article on the topic.
If your part has complex geometries, consider CNC milling or EDM.
EDM
Parts with complex geometries are best suited for EDM when they require precision machining of through holes or cutouts (wire EDM), or complex internal cavities (sinker EDM). EDM is also a good choice for parts with inside sharp corners, small features, and thin ribs. But EDM tends to cost more per part, so it’s often utilized for low-volume production.
CNC Milling
CNC milling is optimal for geometric features that don’t extend all the way through the thickness of the material, such as blind holes or recessed slots. CNC milling is also capable of creating geometric features on multiple part faces (or planes) simultaneously within one fixturing and machining setup — depending on the number of axes for the specific type of CNC machine used.
CNC milling also works well for parts with intricate contour geometries because the tool shapes that remove material are great at creating smooth radii, curves, counters, and similar features. CNC milling is also excellent at forming various edge profiles of different dimensions, including rounded or chamfered edges.
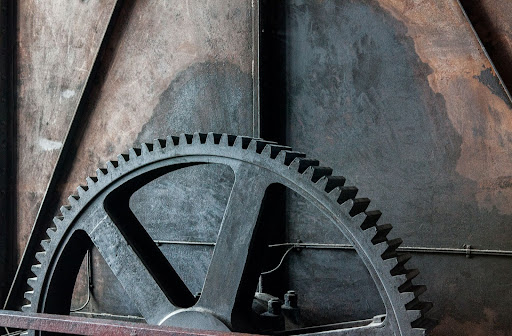
Gear Hobbing
We all remember from our early mechanics courses in school that gears, while relatively simple, are extremely valuable and versatile for transferring or changing the direction of movement. And gear hobbing is a specialty CNC machining process that is used to create — you guessed it — a wide variety of gear shapes on both metal and non-metal parts and is one of the most popular gear manufacturing methods for gear production.
With gear hobbing, the gear teeth (or splines) are progressively cut into a cylindrical piece of material by a cutting tool called a hob. Hobbing is excellent for achieving complex gear shapes and sizes such as spur gears, worm gears and bevel gears. Although gear hobbing can be used for prototyping small quantities, this process is best suited for higher volume production.
CNC Turning
Lastly, CNC turning is excellent for shapes that have cylindrical mirror symmetry as a part turns on its axis while the cutting tool is brought into contact with it. Complex geometries like threaded bodies are also optimal for CNC turning. Tapering and tunneling are also often performed with a CNC turning machine.
Choose a Strategic Partner
Regardless of the type of CNC services you need, Fictiv makes it faster, easier, and more efficient to source and supply quality mechanical parts. Head to Fictiv.com to learn more about our CNC Machining Service, then create an account and upload your designs to get an instant quote and free DFM feedback today!