Usually, the point of a teardown is to figure out how something works—to take something complex and try to puzzle out how it works, and see what exciting new things the designers did to make this product special. This isn’t quite that type of teardown. Instead, this time, we’re going the opposite route and seeing what we can learn from something that’s designed to be simple. Something that’s made to be inexpensive and accessible. Something that we bought from an as-seen-on-TV commercial.
In this teardown, we’re taking apart the Robotwist hands-free jar opener. This little robot does exactly what the box says it will, opening almost any jar you place it on top of with the push of a button.
The areas of interest we’ll be looking in to for this $19.99, plus shipping and handling, product teardown will be:
1. Design for usability – How does the Robotwist’s design keep its target users top of mind?
2. Mechanical Design – What makes the Robotwist tick, and why was it made that way?
3. Design for Manufacture – How was the Robotwist built to be functional and affordable?
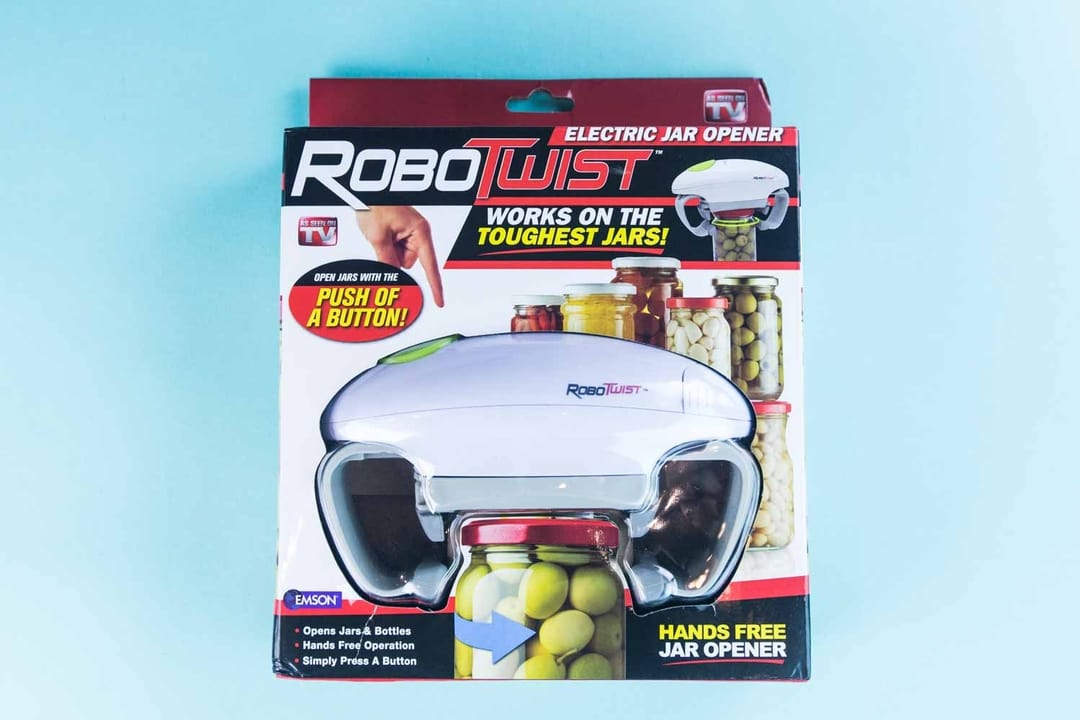
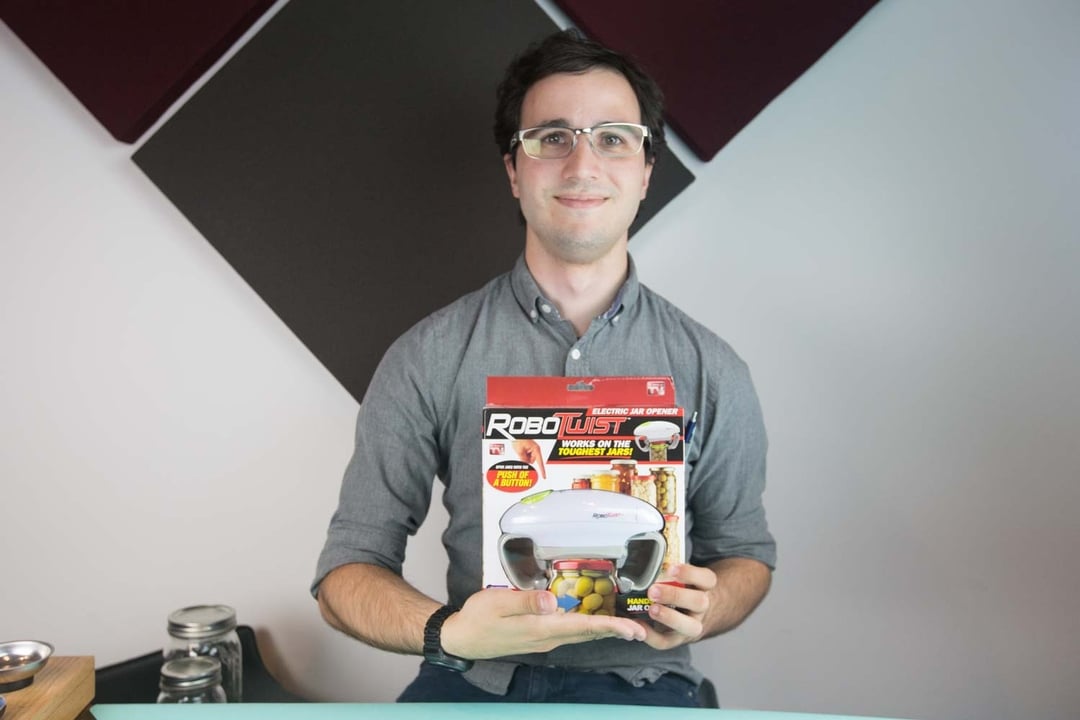
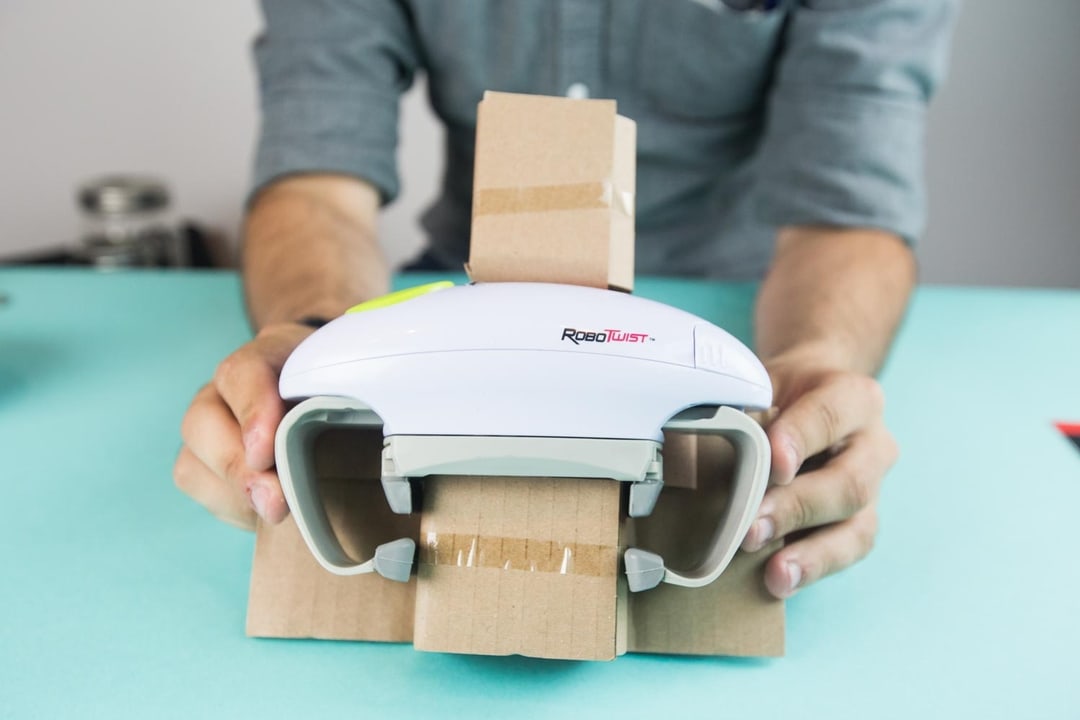
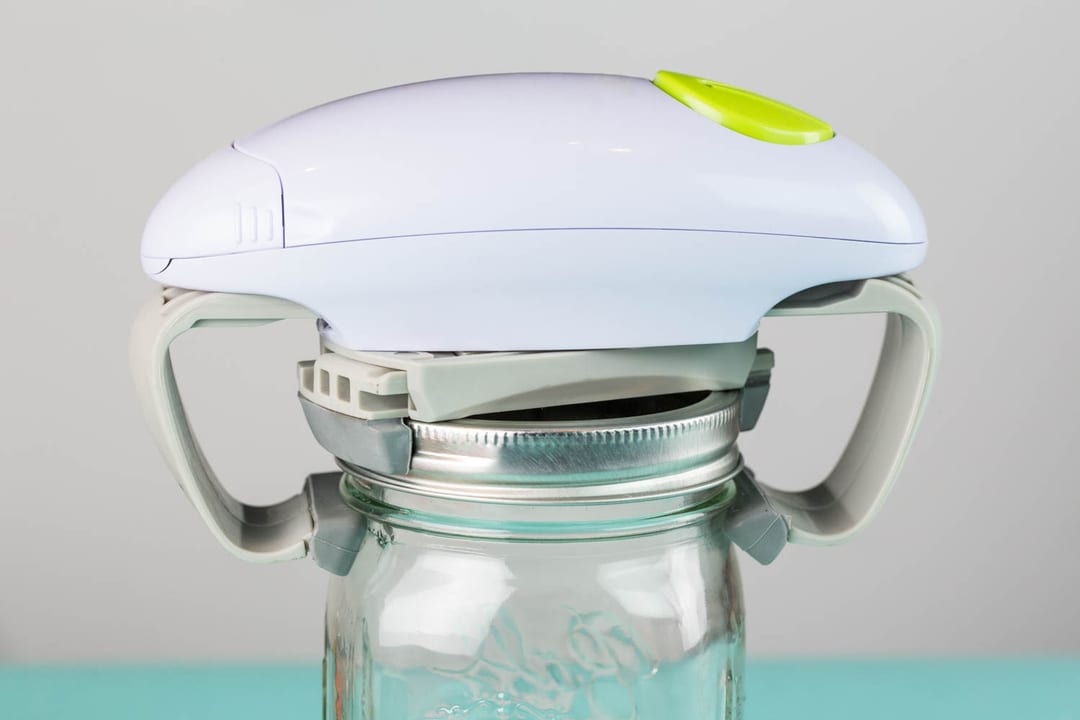
Design for Usability
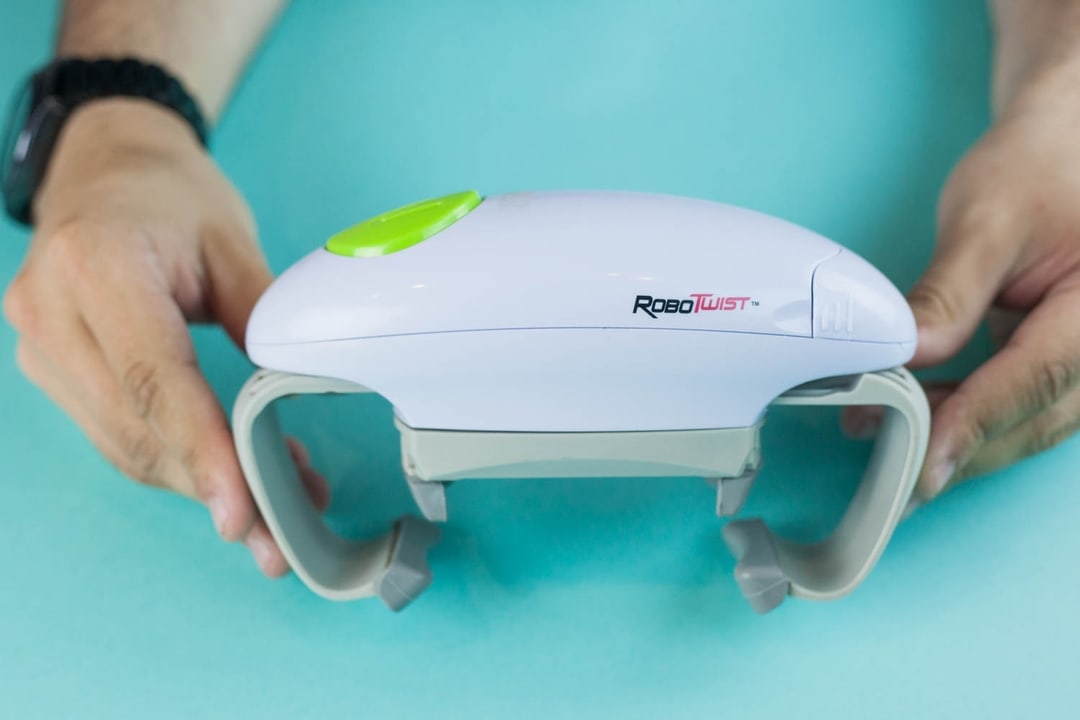
Before we take it apart, the Robotwist looks a little like a UFO that’s here to steal your jar lids. However, the weird look belies a human-centric design that does a good job of keeping its target users in mind. It makes sense that people who need help opening jars would not have much hand strength, and may appreciate easy-to-see visual cues to guide them through using the Robotwist.
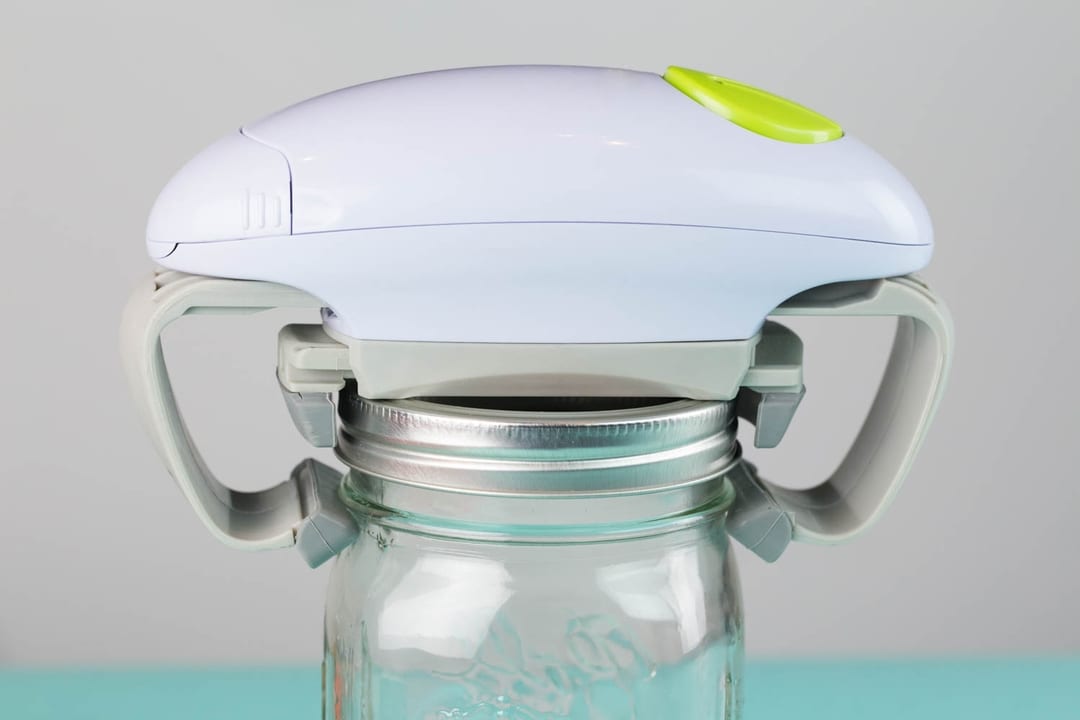
Once the Robotwist is out of the box, the user’s eye is immediately drawn to the large green button that takes up one end of the Robotwist’s body. Its loud color and visible button that sticks out from the rest of the body make it obvious that this is the part the user should interact with.
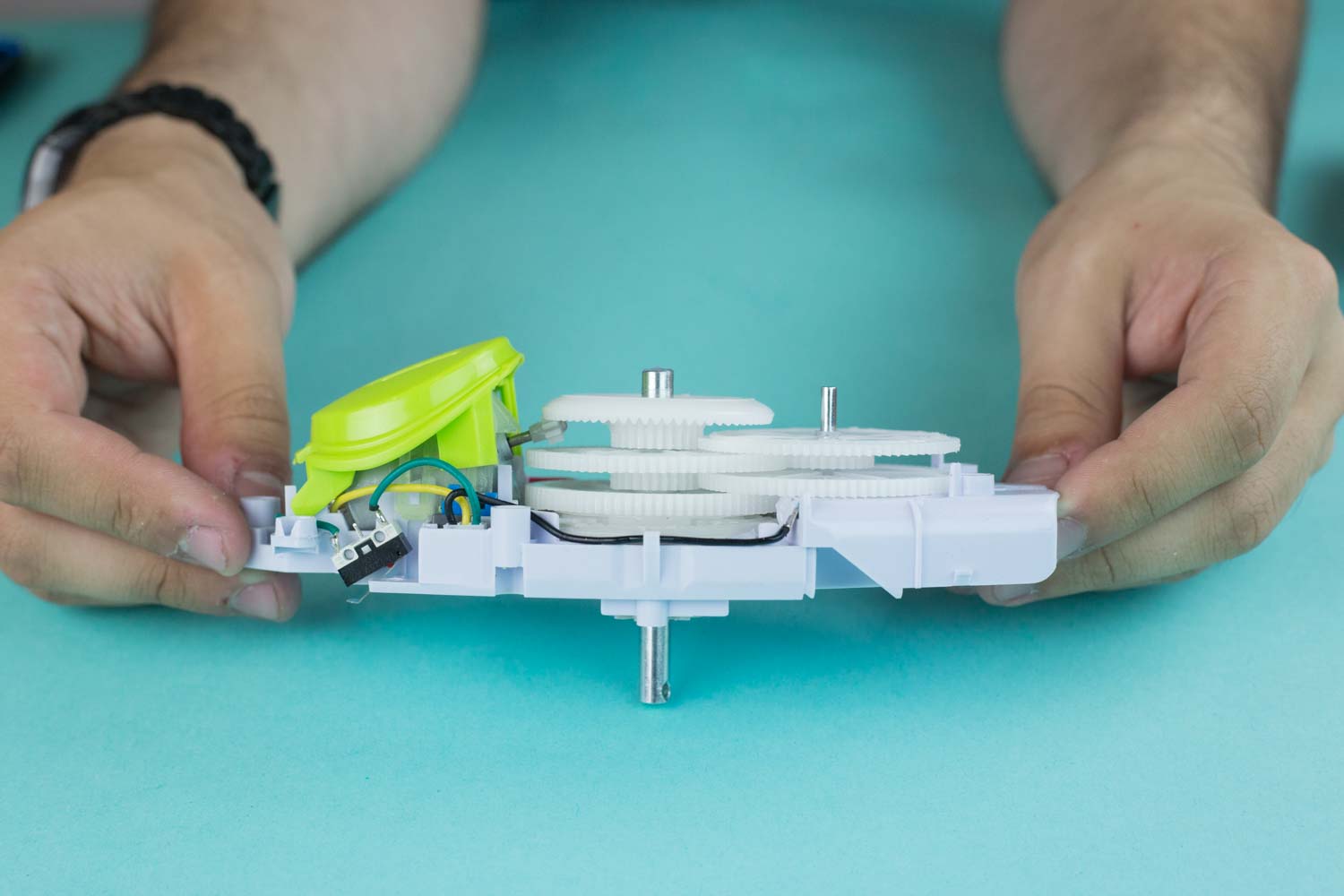
After we broke out the screwdrivers and got to the fun part of the teardown, we found that the button is hinged on one side, with the switches it actuates in the middle. This means the button acts as a class II lever, similar to a wheelbarrow or a nutcracker, and gives the user a mechanical advantage when clicking the button. Combined with its large size, this makes the button easy for anyone to use.
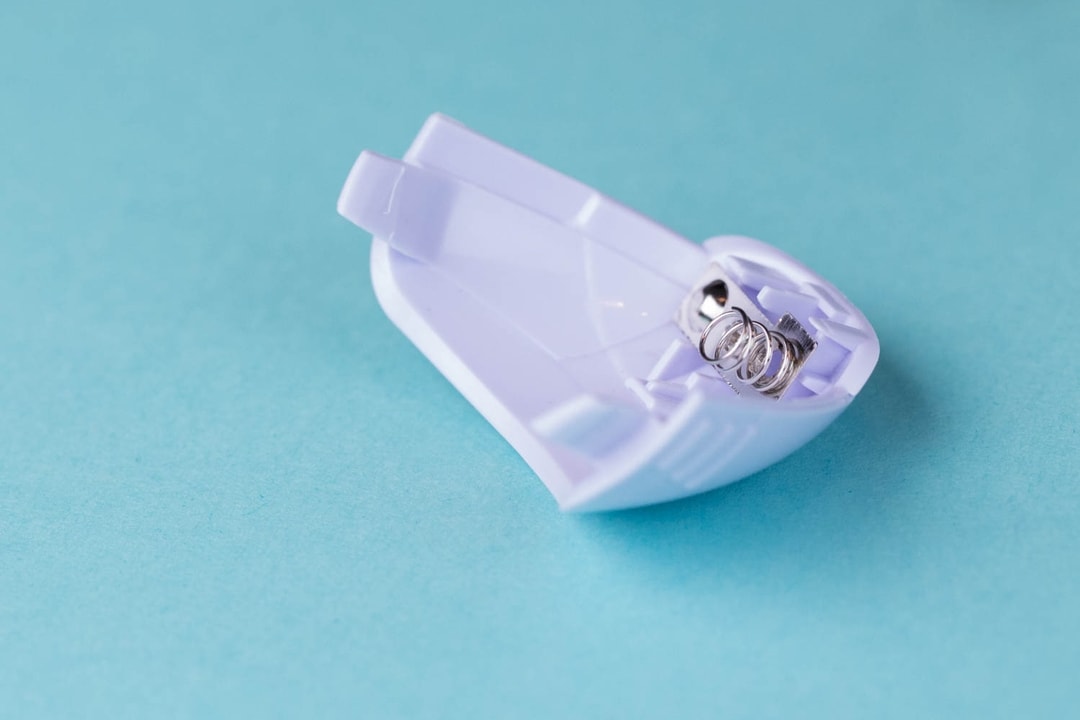
The main body of the Robotwist, made out of white ABS, has a curved shape, with a slightly bulbous top that tapers down into its arms. A housing would usually have this shape to make room for some large components (which is still true in this case), but here, this shape also serves double duty by making the Robotwist very easy to hold, particularly for users who have trouble holding onto a jar to begin with.
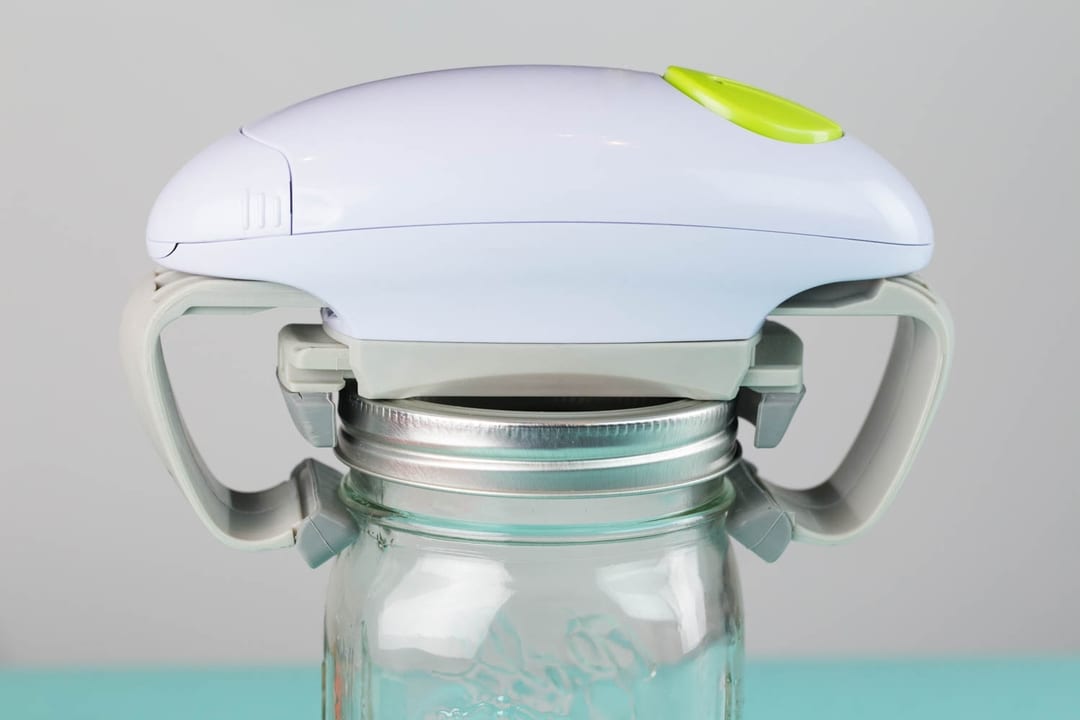
The battery door is built into the side of the housing, opposite the button. A simple snap fit holds it in place, but two large ridges in the door and ramps in the main body make it a breeze to open the battery compartment. Given that the the entire goal of this product is to help with opening jars, it’s good that opening the battery door won’t require a jar opener opener.
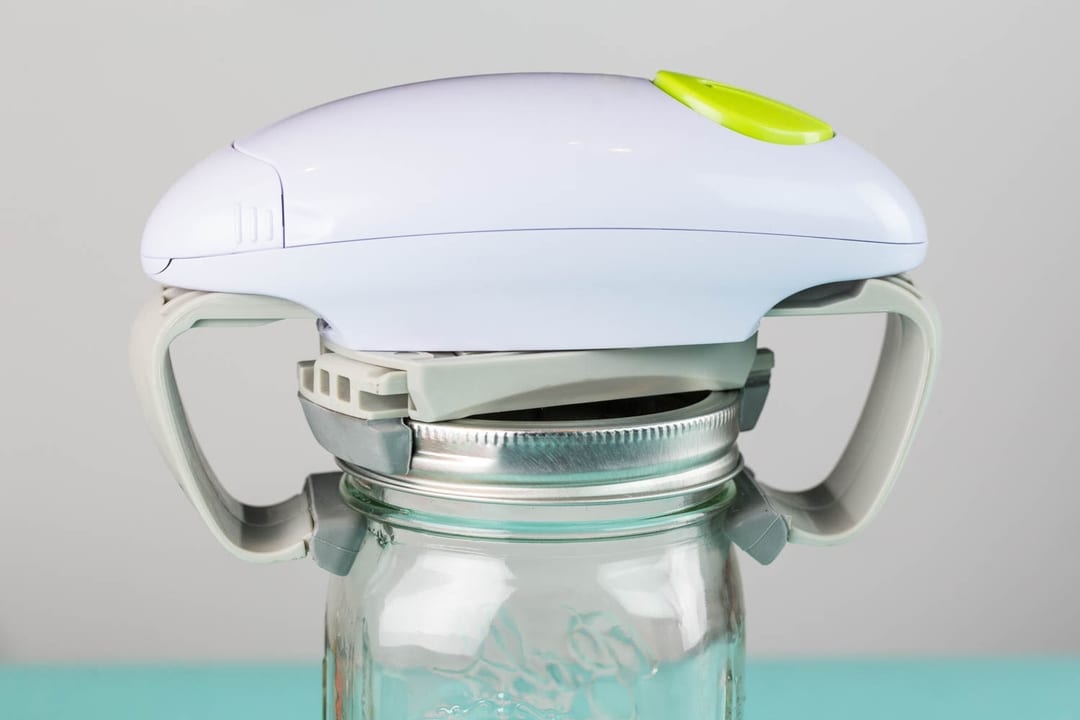
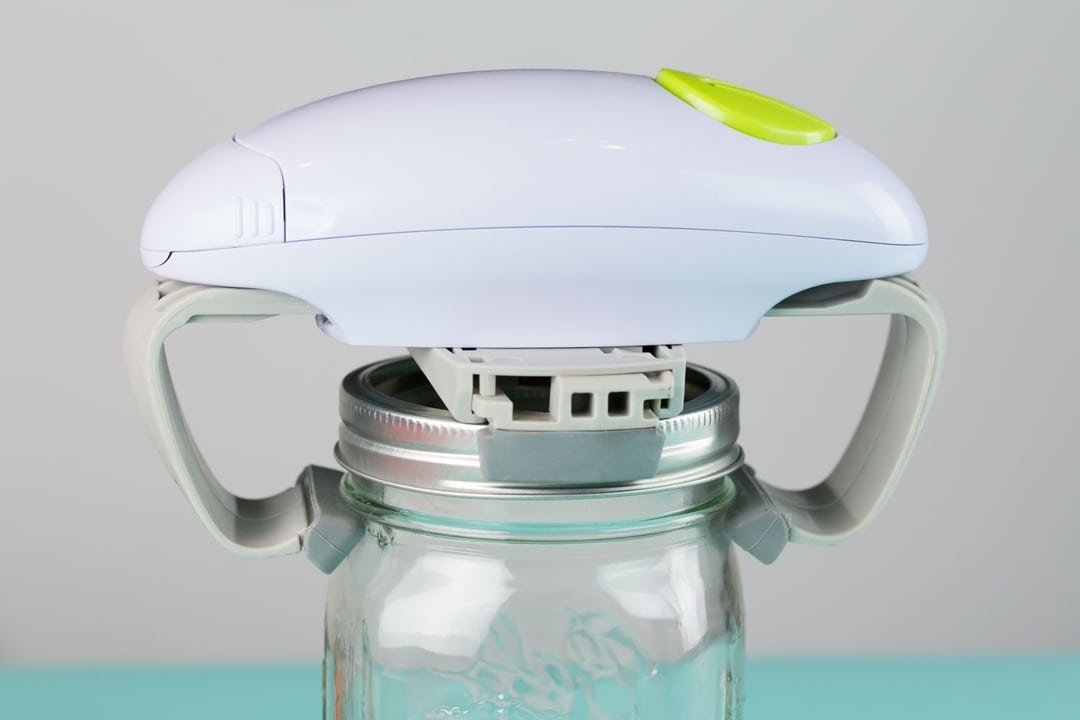
The final portion of the Robotwist’s exterior is the arms that actually grab the jar and twist the lid into cooperation. All of these parts are close to the lightish tan of undyed natural nylon, indicating that the color choice was less about making the product pretty and more about making it cheap. That said, the distinctness of the color does do a good job of visually indicating to the user which parts move, while its blandness dissuades the user from touching them.
Mechanical Design
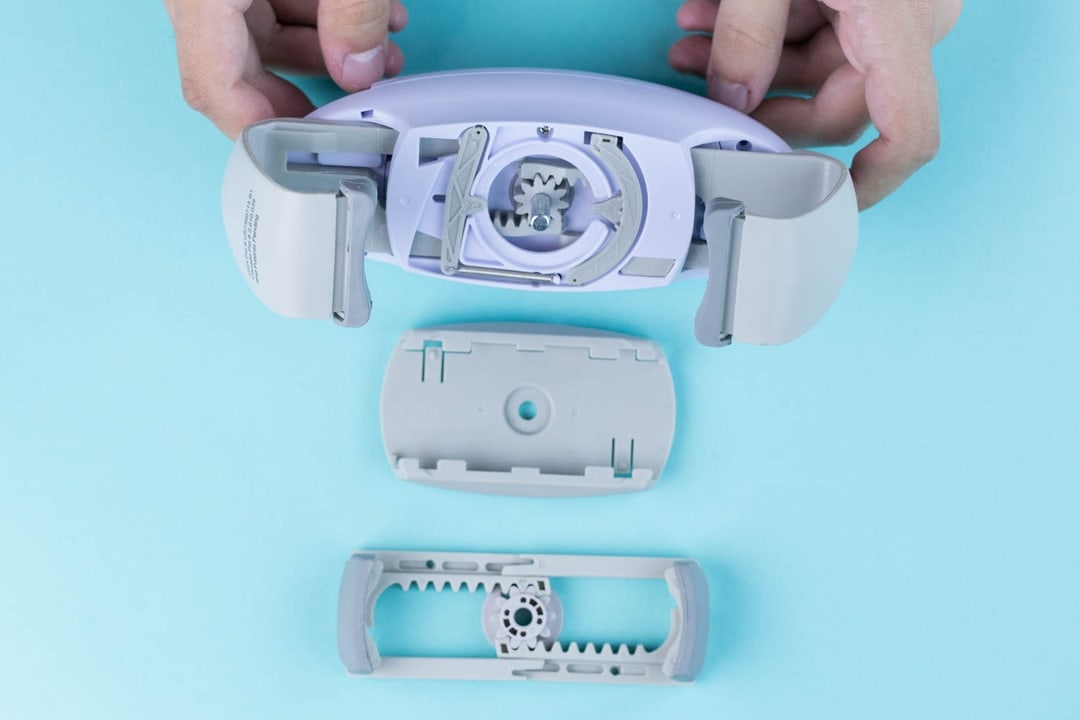
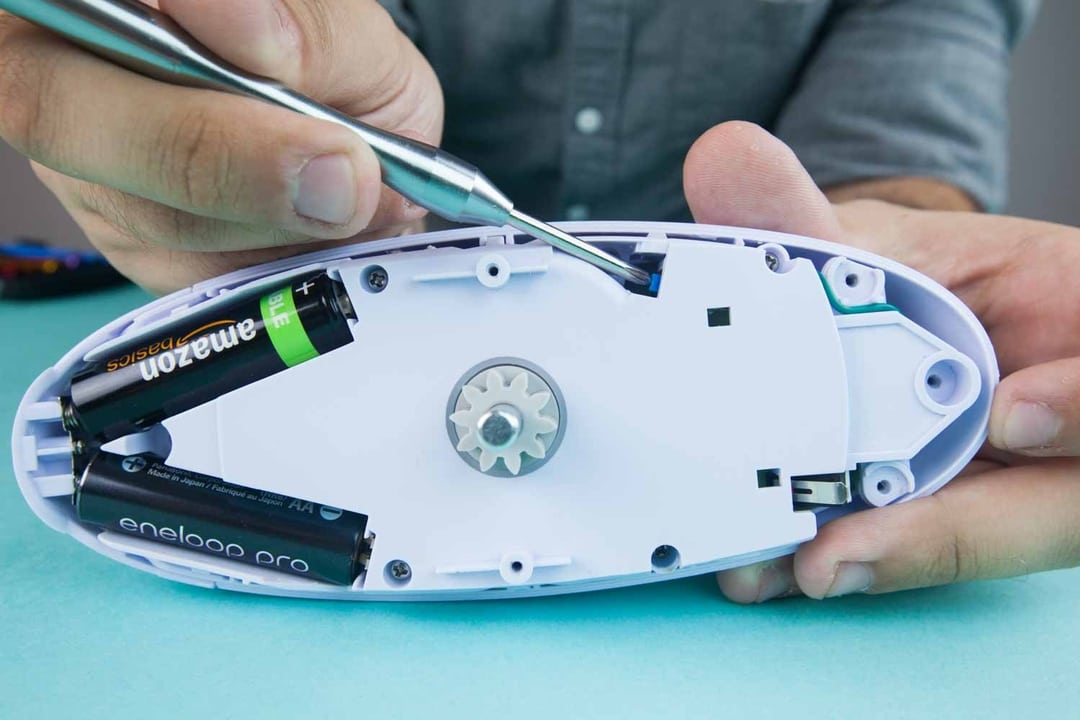
The final portion of the Robotwist’s exterior is the arms that actually grab the jar and twist the lid into cooperation. All of these parts are close to the lightish tan of undyed natural nylon, indicating that the color choice was less about making the product pretty and more about making it cheap. That said, the distinctness of the color does do a good job of visually indicating to the user which parts move, while its blandness dissuades the user from touching them.
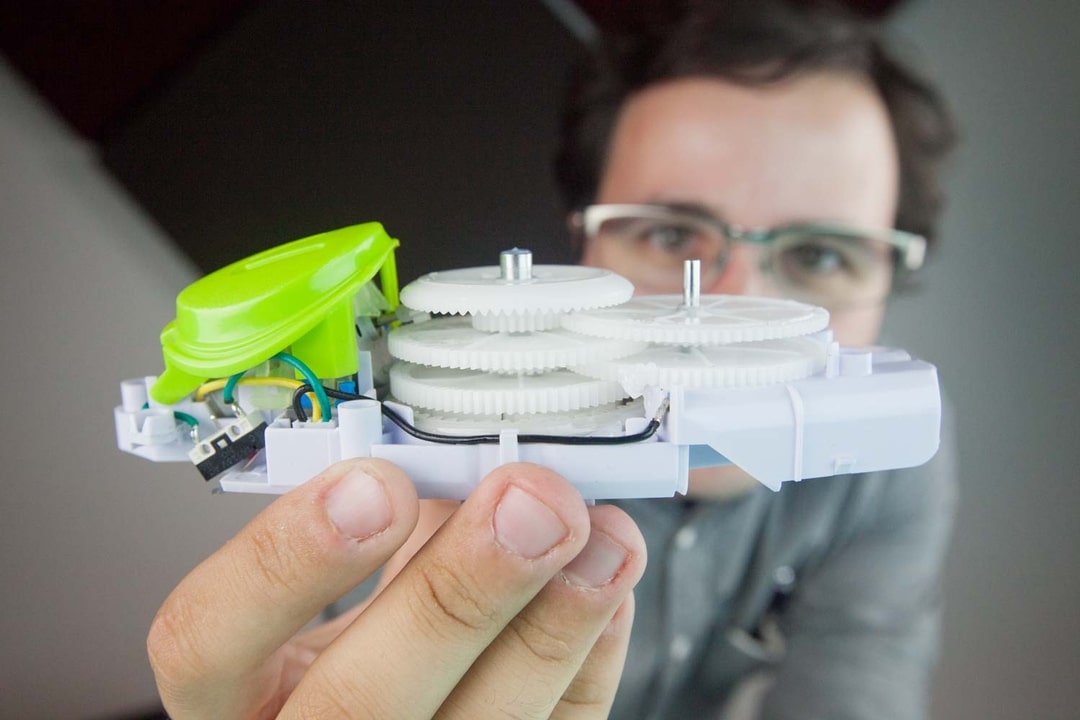
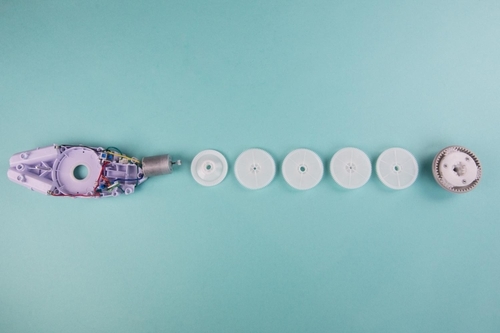
Inside is a sight familiar to anyone who took apart all their motorized toys as a child: a plastic gear train connected to a brushed DC motor. These brushed motors are cheap and widely available, due to their simplicity and ease of use, while the gear train allows for the high RPM, low-torque output of the motor to be transformed into a useable amount of torque, albeit with a reduced speed.
One special thing about the Robotwist’s gear train is that the very last step is a planetary gear, rather than another spur gear. Planetary gears have a much higher reduction, or torque increase, than spur gears, and since they have multiple points of contact to transfer this torque over, they are stronger, too. This gear is largely what helps give the Robotwist the strength to open the most stubborn of pickle jars.
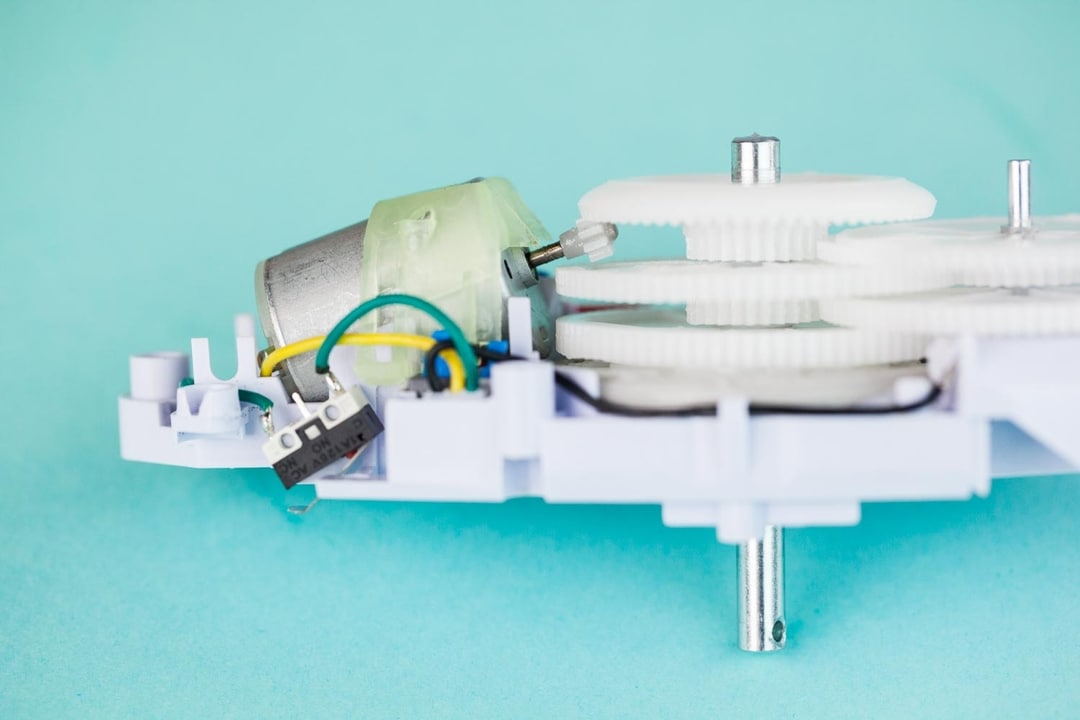
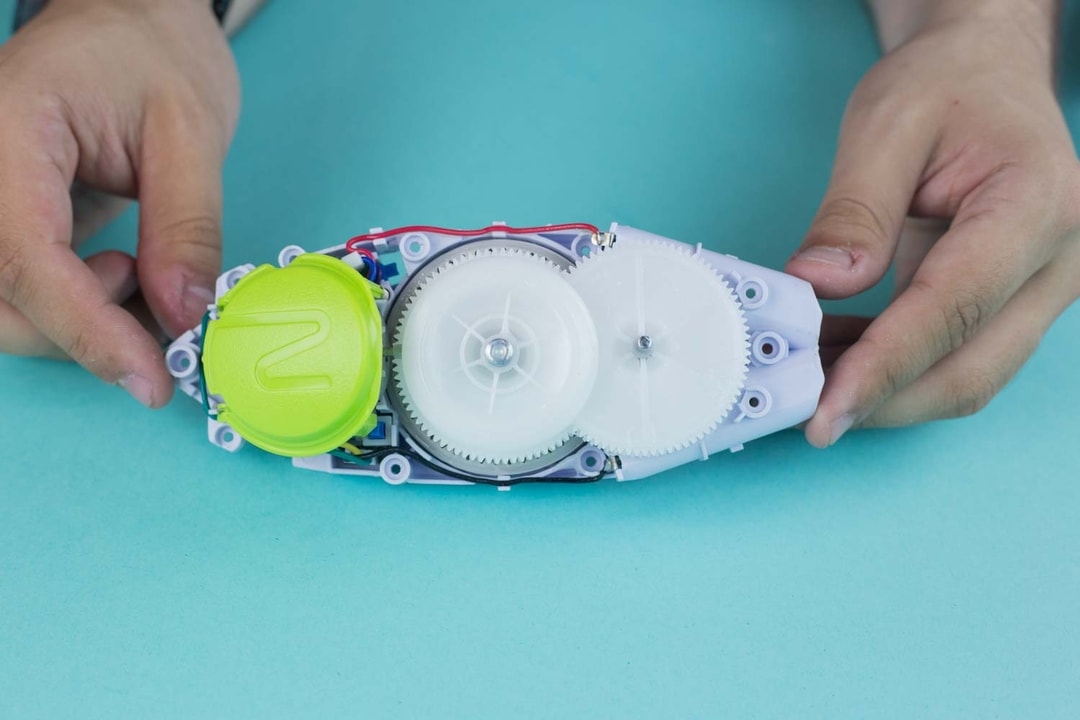
Looking inside the Robotwist explains its large, bulbous exterior. The gear train needs some large diameter gears to get enough of a reduction, and even the a decently sized motor needs to be fit into the case. Still, the Robotwist does a good job of compacting things as much as possible. The motor sits at an angle relative, which means the first gear in the train needs to be a more expensive bevel gear, but allows the main button to fit over the motor. The battery holder is also tucked in snugly, using the space left over under one of the gears in the gear train. Even the main shaft in the gear train, which drives the pinion that moves the arms, serves double duty as the axle for the half of the gears in the gearbox to spin around.
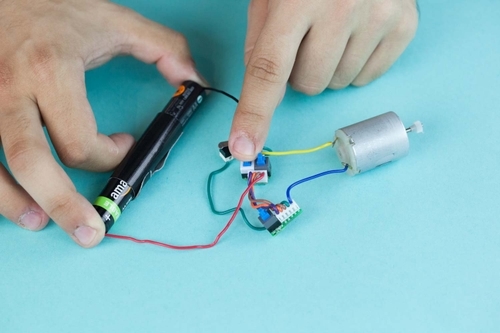
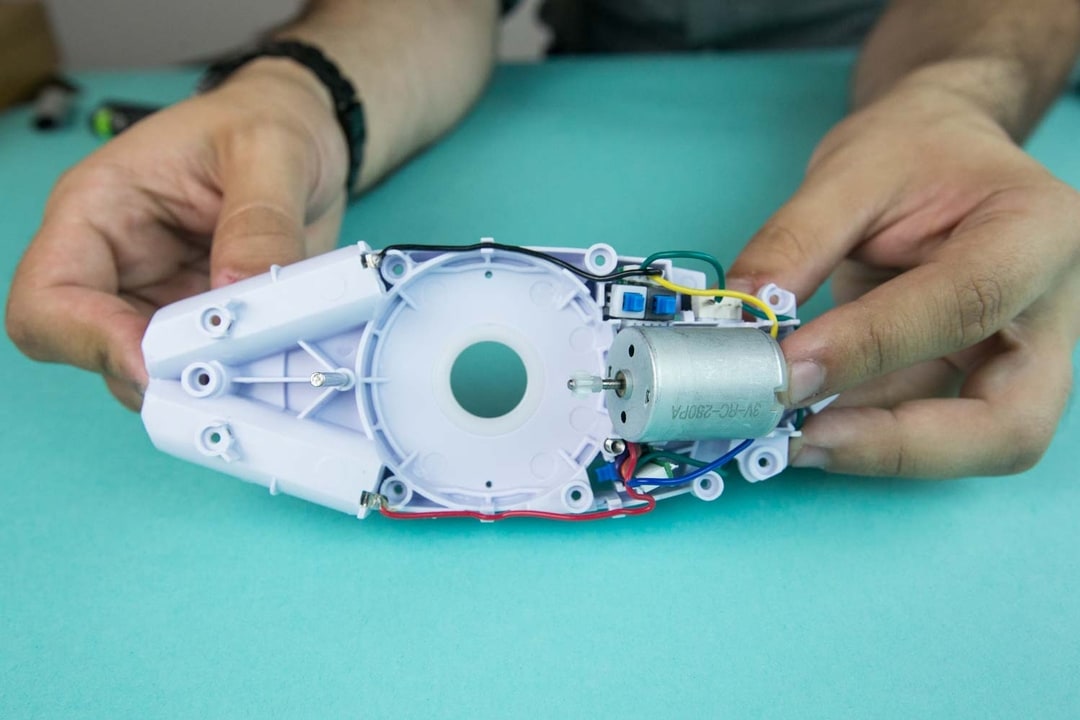
Speaking of the batteries, they and the rest of the electronics turned out the be the simplest part of the Robotwist. The entire circuit contains nothing but the motor, batteries, and a series of switches that either reverse the motor direction or turn it off. These switches were activated by various levers in the body of the Robotwist, meaning the motor will just run until the arms hit a certain point, and then it will reverse and run until another switch is hit, turning the motor off. This simplicity surely saved both design and manufacturing costs and also means that, unlike most products we’ve torn down, it can still run in its disassembled state. Doing this felt like working with a half-dead zombie Robotwist but allowed us to see exactly how its mechanisms work.
Design for Manufacturing
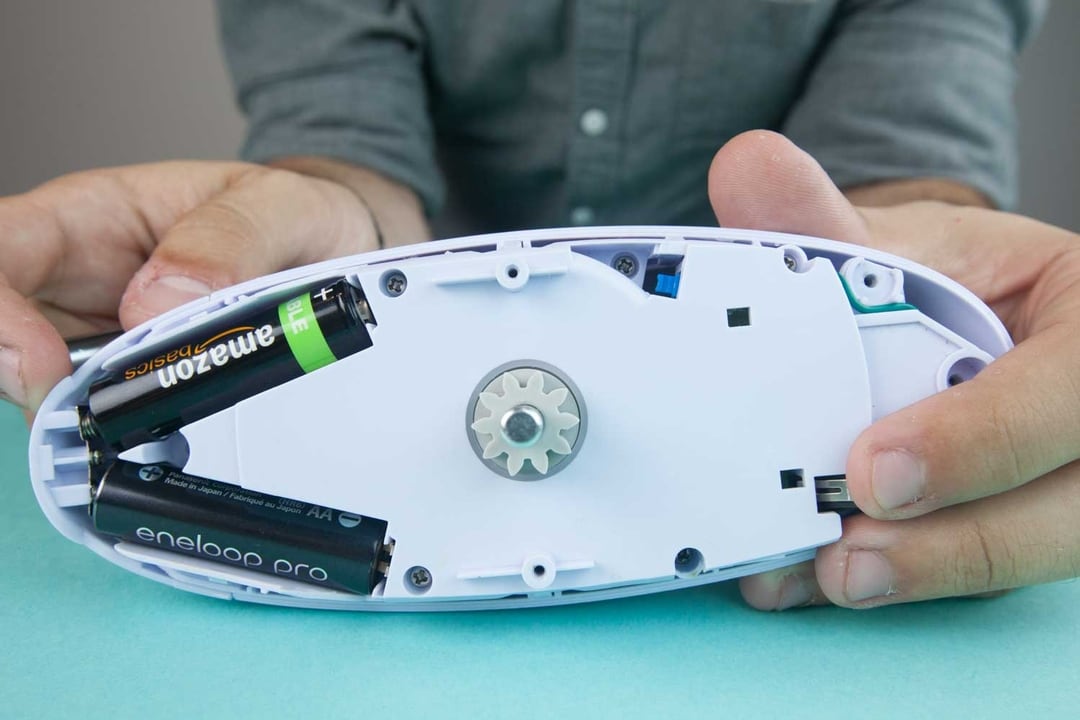
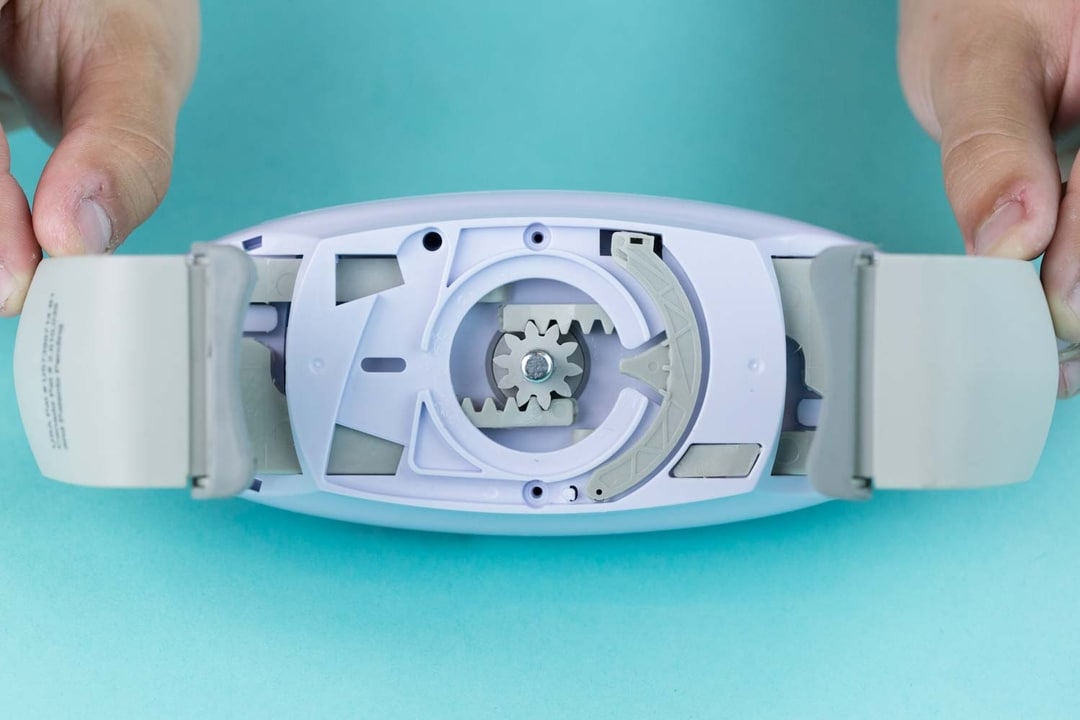
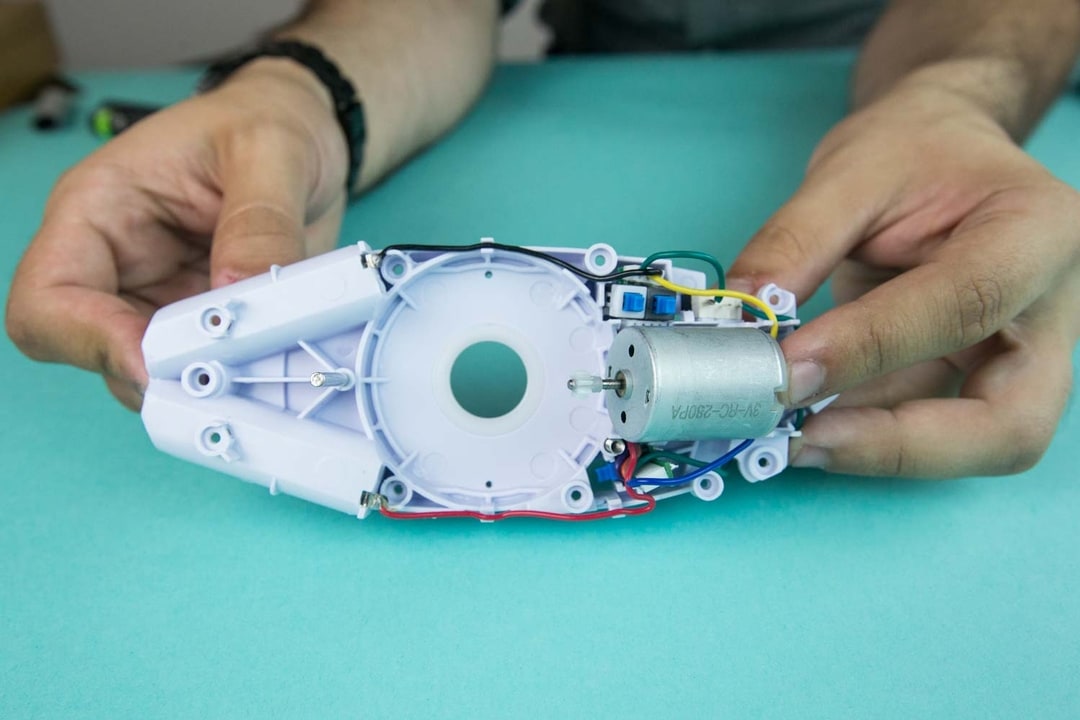
To hit as-seen-on-TV pricing for a product, it has to be cheap to make, which requires a balance of simplicity and good design for manufacturing principles. The Robotwist hits this mark by using smartly designed, injection molded components to simplify assembly and minimize part count.
The main body of the Robotwist is made of three injection molded halves, which are the biggest pieces in the product. The upper and lower halves form the outer outer shell that the user is supposed to hold, with compound curved outer surfaces and bosses for screws on the inside.
The inner piece is more complex, as it holds the battery compartment, planetary gear, and mounting points for motor and wire harness, with ribs to keep the whole thing stiff. These parts only have features on their top or bottom, meaning they only need a simple two-sided mold to make them, without any side actions or sliders that would increase the price of the mold. The thin, constantly sized walls and ribs in the part prevent unsightly sink marks from forming, reduce material needed for each part, and also simplify the manufacture of the mold.
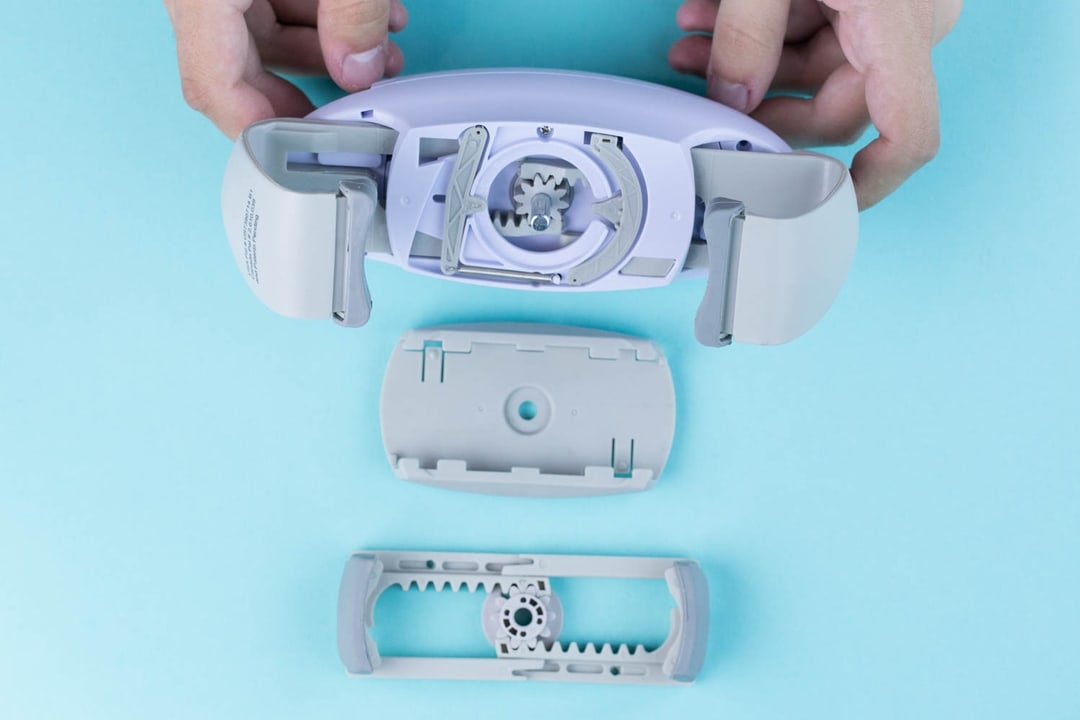
The arms, in comparison to the rest of the product, actually look complex and somewhat costly. Since they support all the load, they’re made of nylon, which is stiffer but more expensive than the ABS in the main body. Their walls are much thicker, which requires more material and more time to create a part. These parts also have undercuts and side features, which require much more complex and expensive molds. The outer arms are particularly complex, needing 5 separate pieces to come together to form the cavity in which the part is molded.
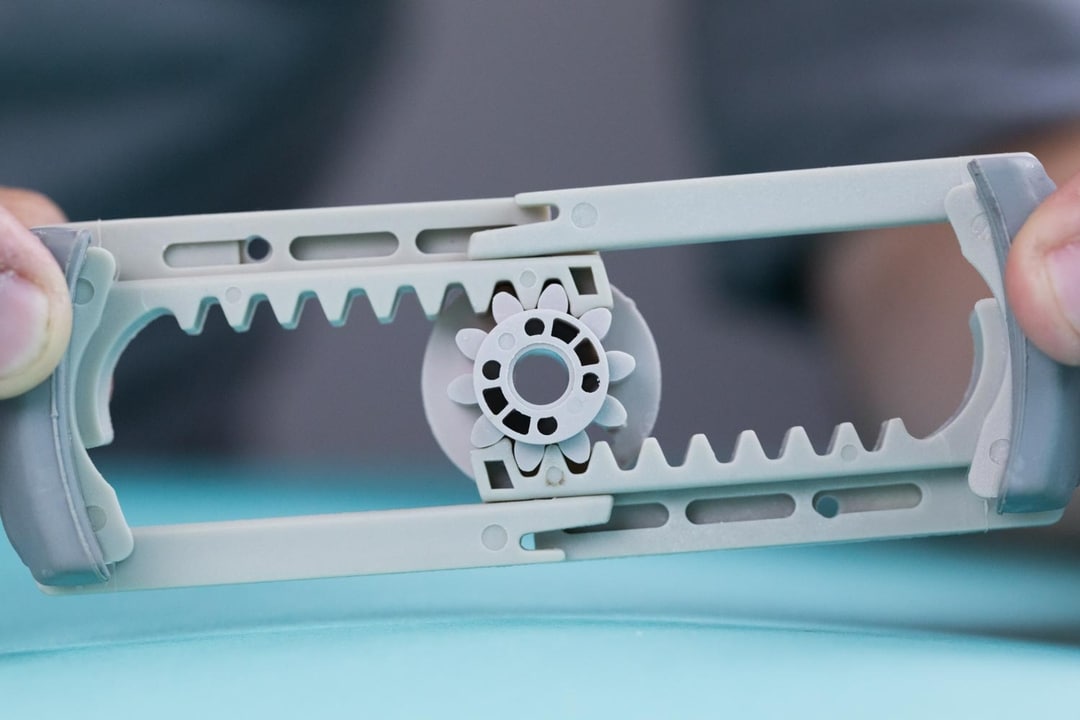
o somewhat offset these costs, both sets of arms, all four grippers, and two sets of gears in the gear train are all exact copies, so fewer unique tools need to be made to make a full product.
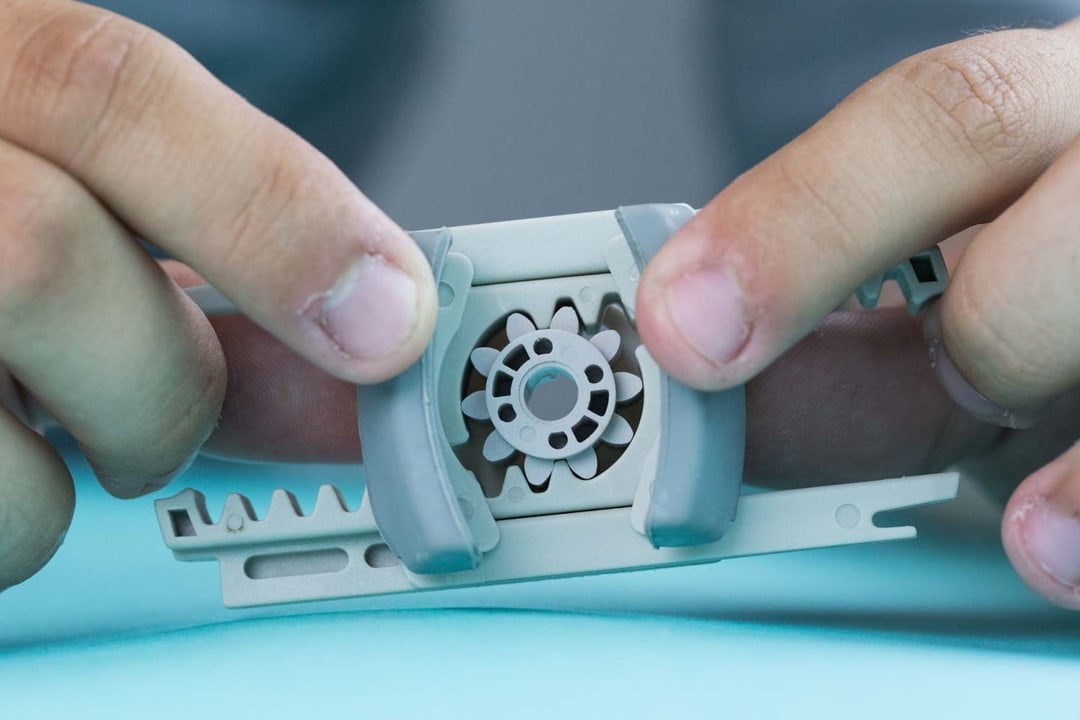
The final step of making the Robotwist, the assembly, is designed to be cheap and efficient. The entire product can be put together from just the top and bottom, meaning fewer fixtures need to be made for the assembly line. The main shaft that drives the pinion is connected with a easy-to-press-in pin, which is cheaper and doesn’t require the types of tolerances or complexity that would be needed for the shaft to be press fit or transfer molded into the pinion. Other parts of the assembly, like the motor mount and the rubber hands that grip the jar, use snap fits to hold them into place, which reduces the hardware needed for the assembly.
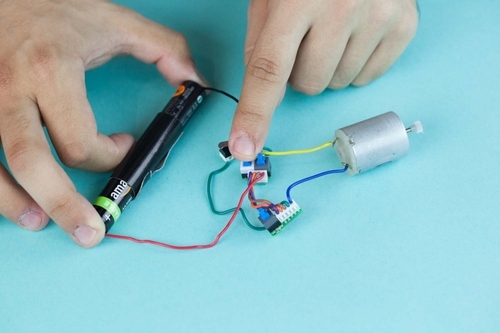
Even the electronics are made to be cheap to assemble, as all the joints are directly soldered together, instead of being attached with some kind of connector.
Main Takeaways
Simple products are often less exciting than complex, high-tech ones, but we can still learn from them. When the whole system is simple, it’s easy to look at every aspect of it in depth and figure out the reasoning behind each design choice.
Additionally, looking at a simple product that excels at a certain area of design shows that a successful design doesn’t have to be complex. For example, the Robotwist’s exterior does a good job of keeping its target users in mind, without making the design any more complex that it would be otherwise.
Since simple also often means inexpensive, simple products can be good examples of how to properly design a product with cost in mind. The Robotwist uses simplicity in manufacture and assembly to reduce part count and cost, rather than relying on a poor design or cheaper materials.
Perhaps more importantly, the Robotwist’s design doesn’t shy away from complexity where needed, using stronger materials and more involved molded parts in critical areas. The end result is a product that is cheap to buy but doesn’t feel like a piece of junk and is able to do its job well. All this goes to show that the complexity of a product’s design isn’t what makes it interesting, but the quality of the design really matters.
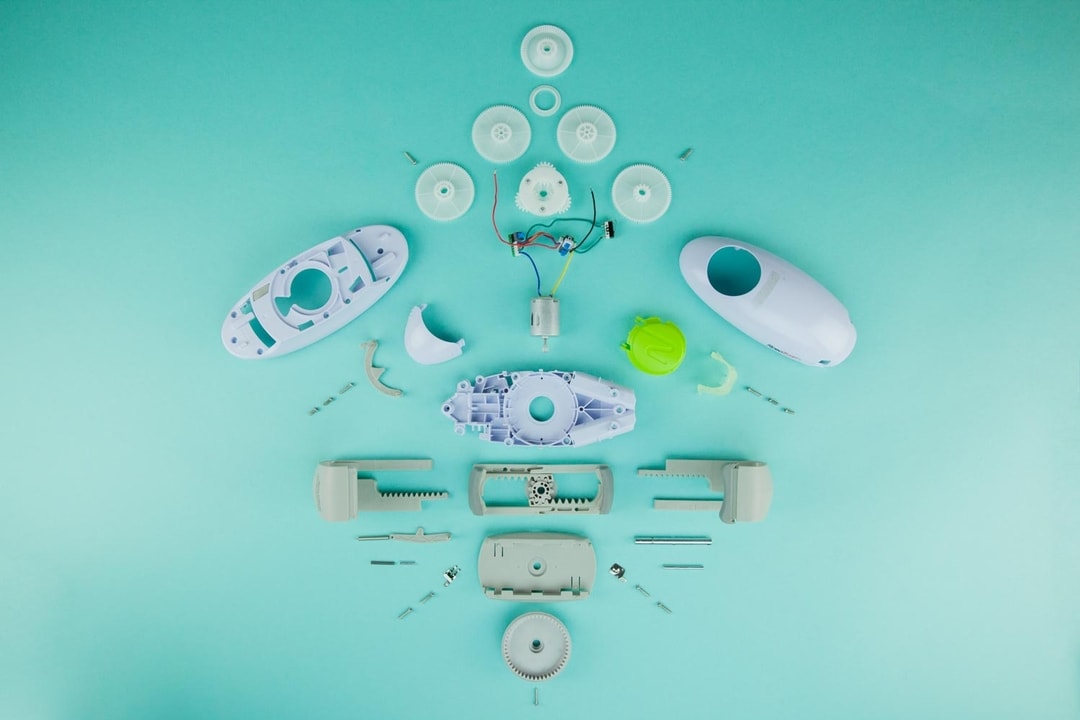