Time to read: 6 min
The advent of 3D printable transparent materials has opened doors to new possibilities with rapid prototyping for optical applications. Now, we can consider how to use and manipulate light with 3D printed parts.
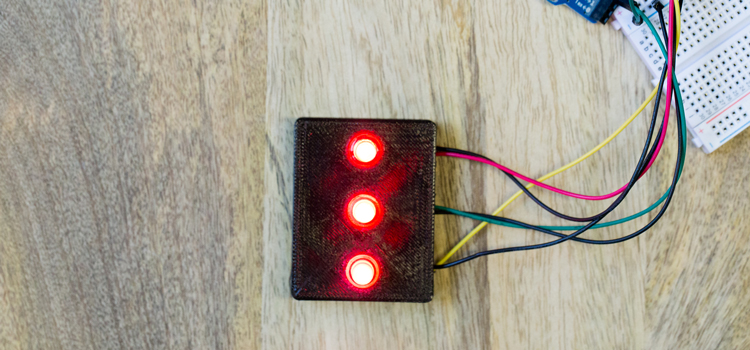
Light pipes, sometimes referred to as light guides or light tubes, are physical components used to purposefully redirect or transport light from a source to a desired location. More specifically, they’re clear pipes that propagate light from a source to the user, utilizing the concepts of optics and physics to do so. Applications of light tubes range from redirecting natural light into homes and physical structures without direct access to sunlight, to providing remote LED illumination in electronic assemblies.
In this article, we’ll consider a practical application of 3D printed optics: the LED light pipe. We’ll look at a common application of 3D printed light pipes/3D printed light guides in consumer products: a “mini” light pipe used to channel the light from a standard 5mm LED mounted on a printed circuit board to a user interface.
To investigate the best 3D printed light pipe material, we’re going to print light pipes using 3 different material samples:
- VeroClear material, unfinished.
- VeroClear material surface finished with a 2-part polyurethane clear coat
- Acura 60
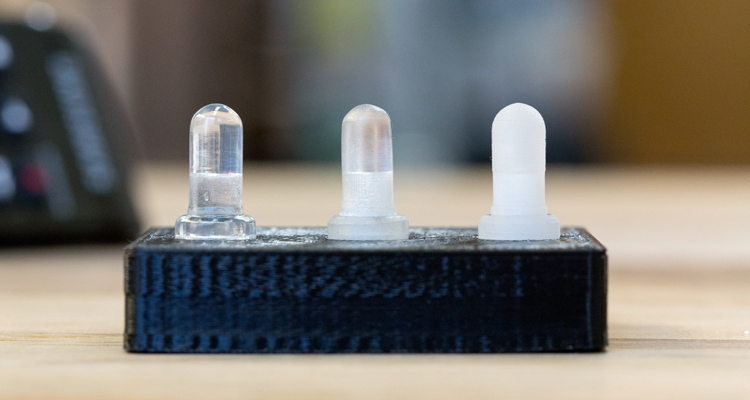
First, let’s go over some important considerations around optics and design.
Optics of Light Pipes
The key optical phenomenon at work in a light pipe application is total internal reflection, the amount of incident light between the boundary of two media that is reflected. As the name suggests, light pipes rely on carrying internally reflected rays of light from an entrance point to an exit point through an optically transparent medium.
For a simple understanding of what’s happening during total internal reflection, consider light traveling through two different substances — say, from glass to air. The critical angle is defined as the angle of incidence at which a ray of light yields a 90-degree angle of refraction at the boundary of the glass and the air. So, as it exits the glass, it refracts in a direction theoretically parallel to the boundary surface.
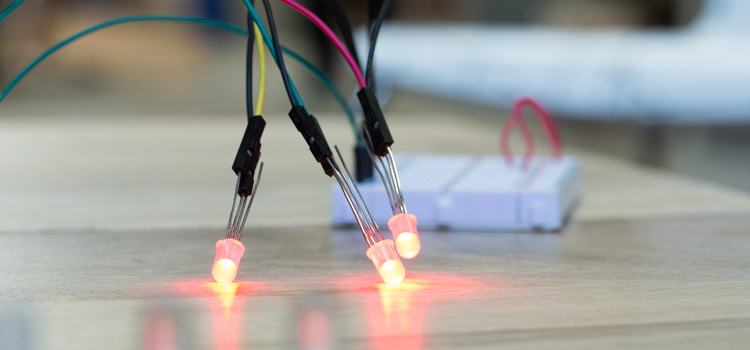
For an angle of incidence greater than the critical angle, total internal reflection occurs within the glass as the light would reflect against the internal surface of the medium. As total internal reflection occurs along the trajectory of light through a light pipe, light can be moved from the source of photons to the desired target, where it is finally refracted out and used in your application.
Note that total internal reflection occurs when the light travels from a medium with a higher optical density to a medium with a respectively lower optical density.
In our example, we’ll demonstrate 3D printed plastic light pipes in air. Since the plastic we’re using in our light pipes has a higher optical density than air, we can expect some total internal reflection to occur and for our light pipes to work!
3D Printed Light Pipes Design Considerations
When designing a system that utilizes light pipes, your goal typically will be to use light provided by your source — in this case, an LED — as efficiently as possible. In other words, you want to minimize the light loss that will occur between your source and the viewer.
To do this, first, make sure you’re capturing as much of the source light as possible in your application. One method for accomplishing this task with minimal cost is to enclose your source in the light pipe structure so that as much of the light leaving the source as possible is ‘captured’ by the light pipe.
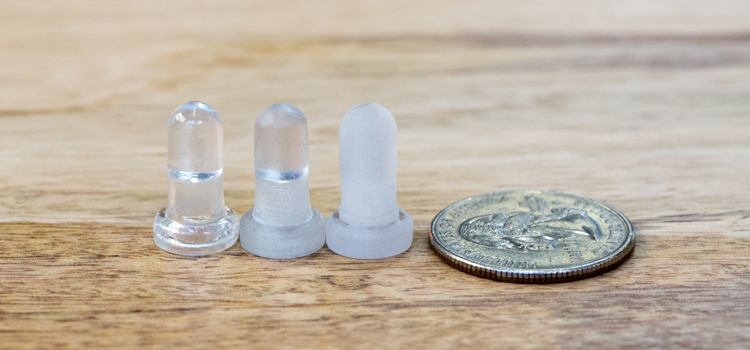
A stronger, less practical method is to focus the source-emitted light into the light pipe structure using a lens.
Next, you’ll want to make sure that the “pipe” section of your light pipe is as reflective as possible. This is because you want to maximize the total internal reflection of the light along its path, allowing as little light loss through the medium as possible along its trajectory. Naturally, you’ll want to deliver as much light as possible into the air at the end of the light pipe.
To do this, you want to minimize the amount of internally reflected light at the tip of the light pipe.This can be achieved by selectively smoothing the exit surface. This will create a multitude of randomly oriented critical angles relative to the internally reflected rays, increasing the amount of light that will “escape” diffusely from the light pipe. Think of the exit as a ‘selective leak’ of light, where you actually want to minimize internal reflection.
The geometry of the light pipe is an important variable to minimize internal reflection and you should follow these general guidelines:
- The exterior of the light pipe should be smoothed to a mirrored finish to avoid light loss
- The inside of the light tube should have all rounded edges to reduce the amount of light that escapes prior to exiting the surface (utilize a radius of at least 0.02”)
- The exit surface should be a diffused surface to allow for uniform illumination
- Utilize the same contour as the surface of the LED light inside of the light pipe to optimize light conductance
Materials for 3D Printing Light Pipes
Now let’s look at three material options for creating light pipes and the specific results we observed with each.
VeroClear – Unfinished
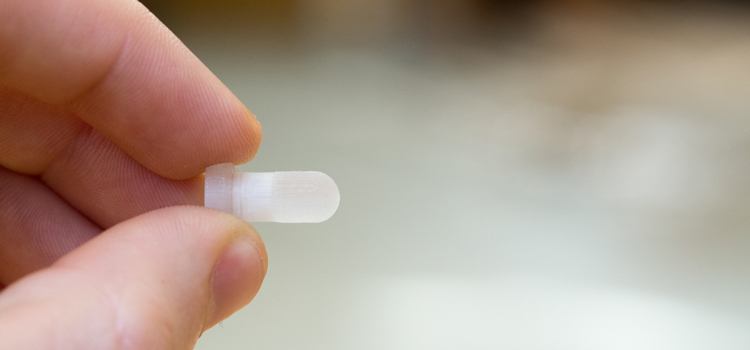
The first material sample we tested was the VeroClear unfinished material light pipe.
The VeroClear material printed a bit cloudy, causing less internal reflection than the other two samples. Though cloudier than the other two samples, this sample still provided a bright, even glow when lit with our red LED.
VeroClear – Finished
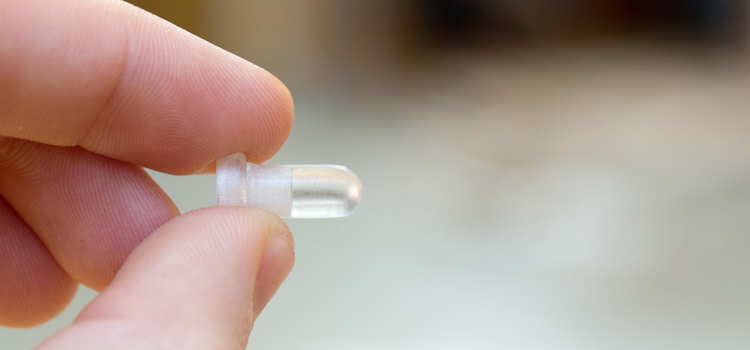
The second material sample tested consisted of the same VeroClear material but finished with a two-part polyurethane coating.
The coating caused a more even diffusion pattern, providing an even softer illumination effect than observed in the unfinished component. This is because the finish creates an optical boundary that causes light to diffuse more evenly across the coated surface as it exits the light pipe.
Acura 60
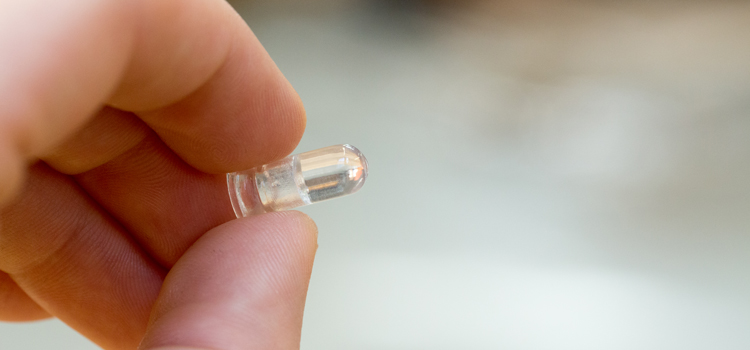
The final sample tested in the series was the Acura 60 material, which printed quite clearly.
As a result, when lit, the Acura 60 light pipe provided a more specular glow, creating a halo-like caustic pattern as the light from the light pipe reflected off of nearby surfaces. This unique effect was not observed in the two VeroClear samples.
Summary of Results
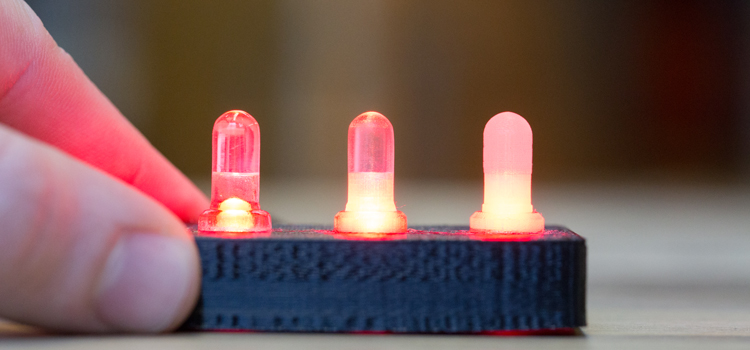
The greatest differentiation in results was observed between the unfinished VeroClear and the Acura 60 samples. The finished VeroClear sample provided final results somewhat in-between both of the Acura 60 and the unfinished VeroClear material.
Remember, total internal reflection is dependent upon the internal surfaces of a light pipe being smooth and non-diffusing, so that internal incident light from the LED is fully reflected. In fact, the diffusion of light is precisely what allows it to exit the light pipe, as incident rays refract at random angles less than the critical angle.
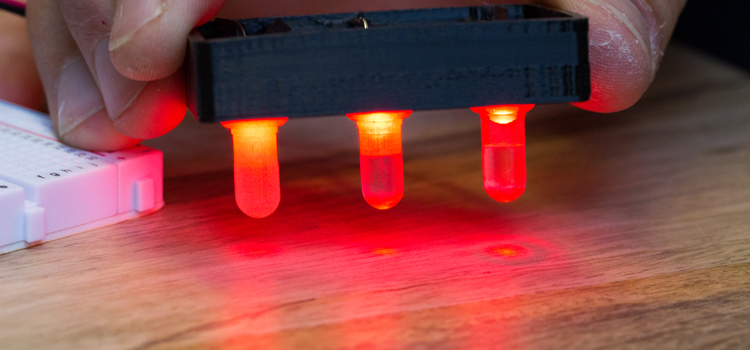
Since our 3D printed parts are created in layers, the internal surfaces of our light pipes are not quite as smooth and crystalline as they would be if manufactured by casting urethane, which can be used for final production parts.
Based on our results, we suggest using the VeroClear material with a polyurethane-finished surface for creating light pipes in your prototypes. Though the result wasn’t as spectacular as the Acura 60, it’s a more cost-effective way to prototype light pipes sinc Acura 60 material is quite expensive.
But if you really need a sharper, more specular appearance and are willing to spend the extra cash, Acura 60 may be the best choice.
FURTHER READING
- http://www.physicsclassroom.com/class/refrn/Lesson-3/Total-Internal-Reflection
- http://www.avagotech.com/docs/5988-7057EN
- http://electronicdesign.com/components/fundamentals-led-light-pipes
- https://vcclite.com/light-pipe-design-guide/
- http://www.lightway.cz/en/sunlight/what-are-light-pipes/
For all your custom 3D printed part manufacturing needs, Fictiv has you covered. We’re experts at machining 3D printed parts, in a variety of materials, and we simplify custom part sourcing with intelligent, streamlined, automated workflows. Fictiv is your operating system for custom manufacturing that makes part procurement faster, easier, and more efficient.
In other words, Fictiv lets engineers, like you, engineer.
Create an account and upload your part to see what our instant quote process, design for manufacturability feedback, and intelligent platform can do for you. Our 3D printing service can create your parts in as little as 24 hours!