Time to read: 8 min
3D printing and injection molding are each used to produce plastic parts. However, these processes are not mutually exclusive because some projects that begin with 3D printing end with injection molding.
3D printing is typically used for early-stage prototypes, evolving designs, and part geometries that can’t be produced with other methods. Because this form of additive manufacturing doesn’t require metal tooling, it’s economical for low-volume prototyping and production. 3D printing also offers shorter lead times. However, its cycle times are longer and fewer plastic materials are available. In addition, post-processing may be required, especially to improve surface finish, and 3D printed parts usually aren’t as strong as injection molded parts.
Injection molding is for later-stage prototypes, mature designs, and parts with tighter tolerances. Although it requires tooling, prototype injection molding is suitable for designs that require real-world testing. Low-volume injection molding is used for 100 to 10,000 pieces, and high-volume injection molding can produce tens of thousands of parts. Injection molding lead times can be longer, but its cycle times are shorter. Plus, more materials are available. Because parts can be molded with a specific surface finish, post-processing may not be necessary. Generally, injection molded parts are stronger than 3D printed parts.
This article compares 3D printing to injection molding in detail so that you can make the best choice for your next project. If you already know which process you need, create a free Fictiv account and upload your part design. Along with a quote, you’ll receive expert design for manufacturability (DFM) feedback.
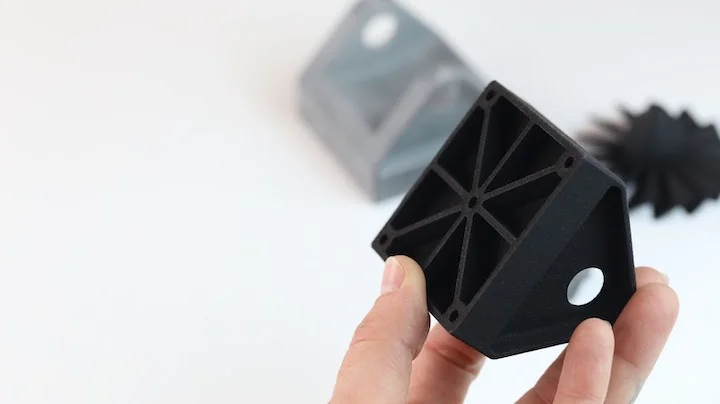
3D Printing: A Closer Look
3D printing uses computer-aided design (CAD) software and a printer to build three-dimensional (3D) plastic parts in layers. Different 3D printing techniques, such as stereolithography (SLA) and fused deposition modeling (FDM), are used.
The following sections describe core 3D printing concepts. You’ll also learn about the advantages and disadvantages of additive manufacturing.
STEP Files, STL Files, and G Code
Designers use CAD software to create a 3D part model, typically as either a STEP file or an STL file. STEP files contain precise measurements in an X, Y, Z coordinate system. STL files approximate a part’s surfaces with triangles and represent a mesh.
Designers can create either type of file, but it’s not the CAD file that directs the 3D printer. G-code, a type of computer numerical control (CNC), directs the machine instead.
Slicing and Printing
Slicing, the process of converting CAD files into G-code, uses specialized software. Typically, slicing also accounts for geometric dimensioning and tolerancing (GD&T). The 3D printer then builds the part by depositing plastic material layer by layer until the entire object is formed.
Each layer is a sliced cross-section of the part, but 3D printing techniques vary. For example, FDM forces a polymer-based filament through a heated nozzle that melts the material. SLA pours a liquid, photosensitive resin into a vat or tank where ultraviolet (UV) light cures the resin layer by layer until the final part is complete.
Post-Processing
When 3D printing is complete, post-processing may be required. Sometimes, this involves removing supports that held the part in place during production. Post-processing may also involve sanding or polishing a 3D printed part so that it has a specific surface finish. Curing, heat annealing, or the application of a laminating epoxy may be needed to strengthen the part.
Advantages of 3D Printing
The advantages of 3D printing begin with its low barrier to entry. Unlike injection molding, 3D printing does not require tooling that can cost thousands of dollars. Consequently, 3D printing supports on-demand prototyping and production. The lead times and setup times are shorter, and this form of additive manufacturing is cost-effective at lower part volumes.
Importantly, 3D printing’s support for rapid, iterative prototyping can reduce project costs and timelines. For example, when TransMed7 wanted to rapidly prototype a new suite of biopsy tools, Fictiv’s 3D printing services helped the medical device company save millions of dollars. TransMed 7 also reduced its new product introduction (NPI) timeline from 10 years to 2.
For designers, 3D printing’s greater freedom is especially attractive. From complex geometries to personalized products, designers can realize ideas that are technically impossible or financially unrealistic with other manufacturing methods. Examples include lattices, honeycomb structures, and personalized products such as shoes and clothing.
Disadvantages of 3D Printing
Despite its advantages, 3D printing has some key limitations. Compared to injection molding, fewer plastic materials are available. Therefore, a designer may not be able to 3D print a part using the intended production material. Even then, 3D printed and injection molded versions of the same polymer don’t have identical end-use properties. This includes strength since 3D printed parts may have weak points between layers.
In addition, 3D printed parts can’t match the tighter tolerances that are possible with injection molding. Injection molding is also capable of finer and glossier surface finishes. Plus, the post-processing operations that remove support structures, polish parts, and improve strength add costs and extend timelines.
Because of its longer cycle times, 3D printing is not recommended for high-volume production. 3D printers also come with limitations on build sizes. In other words, a specific 3D printer may not be able to produce parts that are large or as small as you need. Large-format and microscale 3D printers are available, but these machines tend to be specialized.
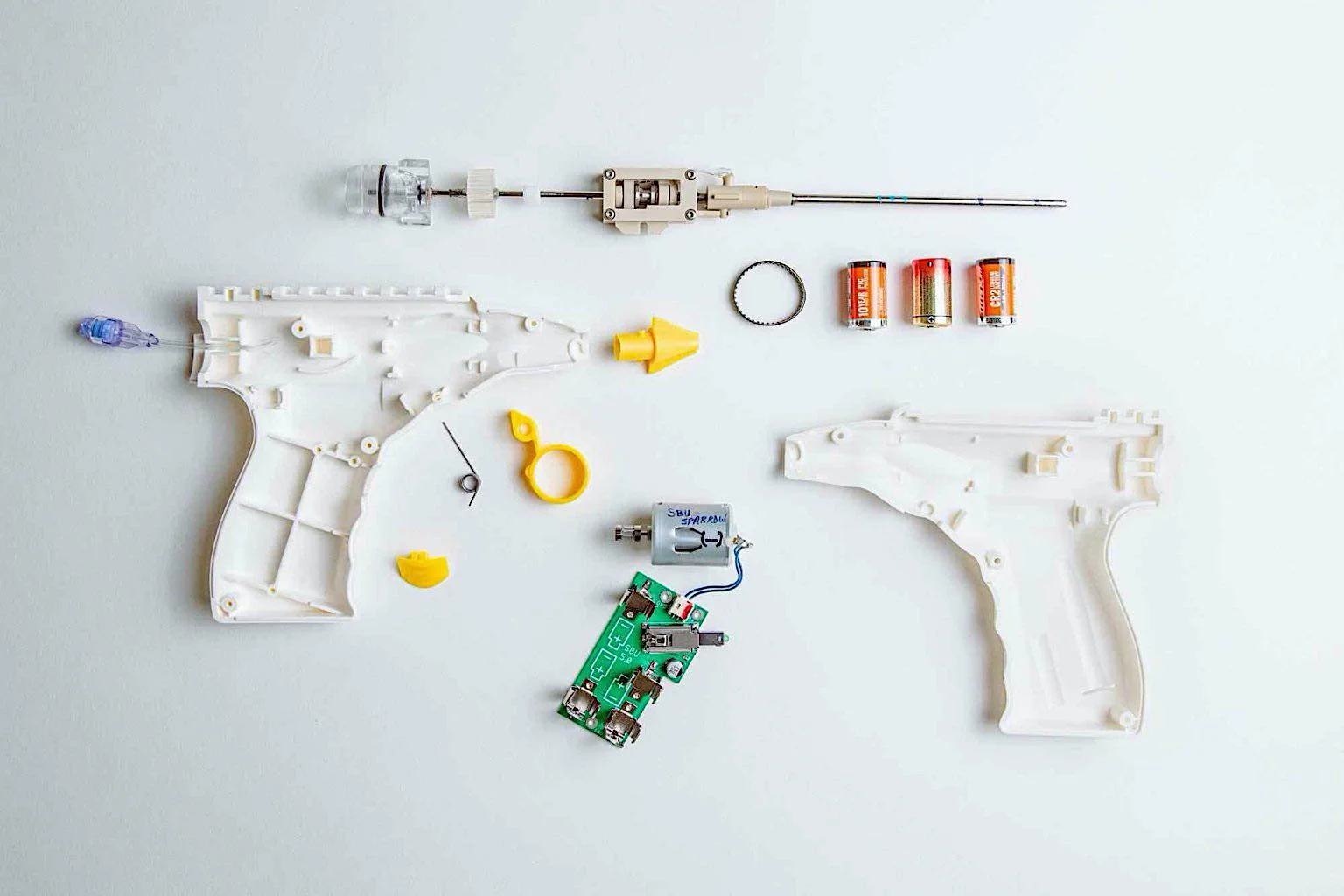
Injection Molding: A Closer Look
Injection molding uses plastic resins, a mold, and a machine called a press to produce parts in low or high volumes. Like 3D printing, this process has advantages and disadvantages.
Parametric Files and Plastic Resins
Designers use CAD software to create parametric part models in a non-mesh format. Typically, these CAD files contain a singular, solid body. Injection molding can support many different types of parametric files and even more types of plastic resins, including glass-filled or fiber-filled materials for added strength.
Tools and Tooling Costs
Injection molds consist of a core and cavity held together between metal plates. Other components, such as part ejection mechanisms, are also part of the injection mold. Typically, tooling is made of steel or aluminum. Steel molds are more expensive but can produce parts with greater precision. Steel molds also last longer for higher-volume production.
Molding Under Heat and Pressure
Injection molding machines work with heat and pressure. First, plastic pellets are poured into the hopper and melted inside a heated barrel. Next, a rotating screw pushes or injects molten material into the cavity of the mold, which remains clamped shut. Injection molding equipment varies, but the basic process is the same.
After injection, the molten plastic is held under pressure so that it flows and fills the mold completely. The plastic material cools and solidifies according to the shape and finish of the mold. The tool is opened, and the finished part is ejected.
Advantages of Injection Molding
The advantages of injection molding begin with its faster cycle times and greater precision. Compared to 3D printers, injection molding machines can produce more parts in less time. The tighter tolerances injection molding equipment can achieve, especially when steel molds are used, support greater part-to-part consistency.
Importantly, injection molding supports the use of a wider selection of materials, including silicone rubber and thermoplastic elastomers. Designers can use the same polymer for prototyping and production, which facilitates testing and approvals. Plus, the higher degree of automation in injection molding helps to contain labor costs. Injection molded parts are also denser and more uniform for greater strength.
In addition, most injection molded parts require minimal post-processing. Depending on the quality of the mold, parts exit the tool with the required surface finish and dimensions. Injection molding design guidelines are well-established, and a quality mold and skilled molder can help designers to achieve their goals at either lower or higher part volumes.
Disadvantages of Injection Molding
The disadvantages of injection molding begin with the cost of tooling. If you need less than 100 pieces, a mold made of soft or semi-hardened steel might not provide an adequate return on investment (ROI). Aluminum tools cost less, but they can’t match the tolerances of steel molds. Aluminum molds also wear more quickly, especially with parts made of abrasive materials.
Because injection molding always requires tooling, changes to your part design could require the cutting of a new mold. This makes injection molding a risky choice for early-stage prototypes where quantities are low, and designs are likely to change. Even if a tool can be modified instead of scrapped, part quantities need to be high enough to amortize the cost of the tool.
Finally, injection molding has longer lead times because mold-making requires machining. There’s also less design freedom with injection molding, which can’t match some of the complex features (such as lattices) possible with 3D printing. Although most plastics are recyclable, failing to follow injection molding design guidelines can result in part defects.
For information about injection molding design guidelines, download this free resource.
Download the Injection Molding Design Guide
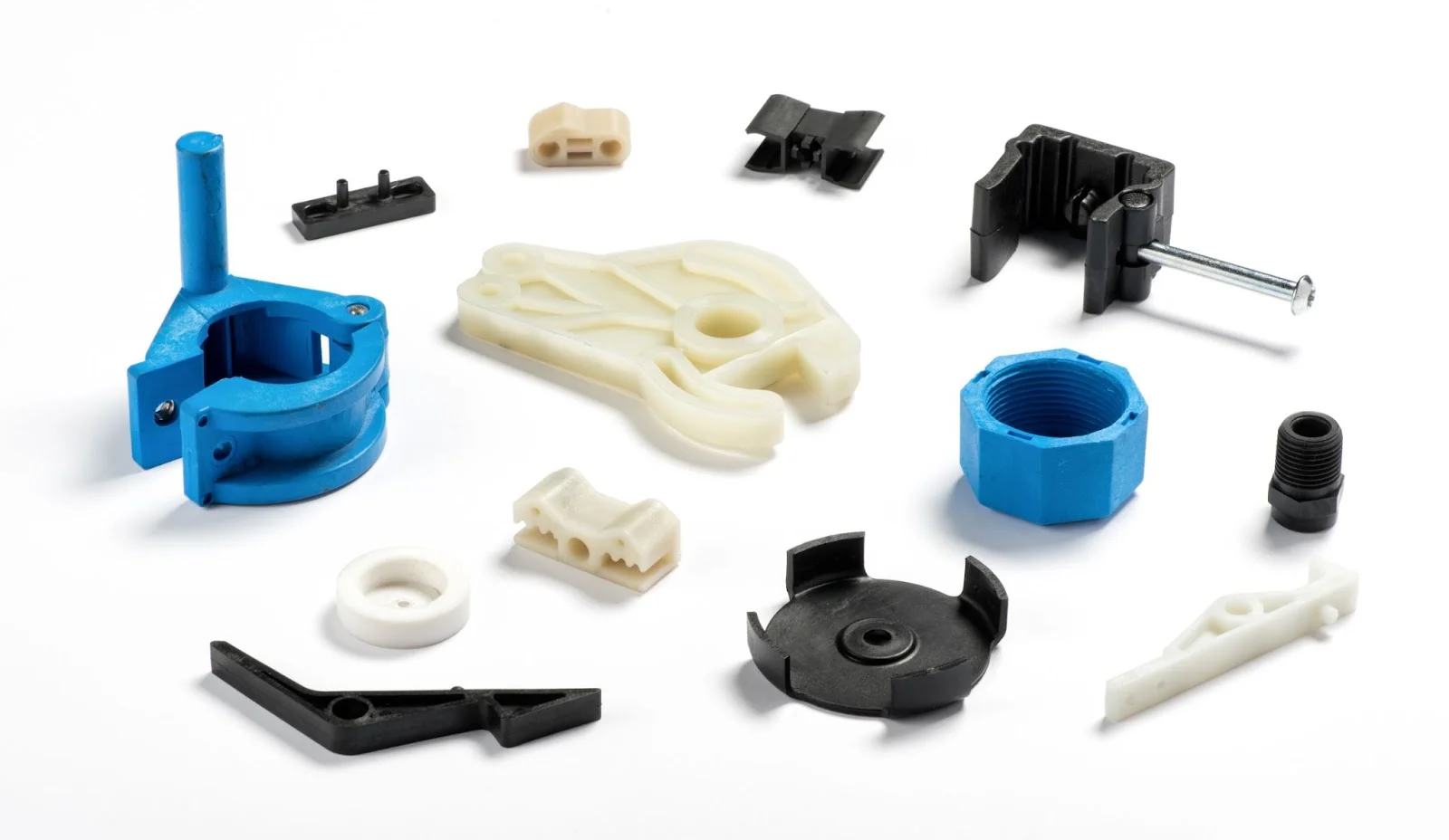
Injection Molding vs 3D Printing: Key Considerations
Now that you know more about the differences between injection molding and 3D printing, what’s the right choice for your project? Remember to consider all of these factors.
- Part Volumes
- Costs
- Lead Times
- Cycle Times
- Part Strength
- Design Complexity
The following sections explain.
Part Volumes
Injection molding can be used for either low or high part volumes. This mainly depends on the construction of the tool. Low volume injection molds made of soft or semi-hardened steels are used with part volumes ranging from 100 to 10,000. High volume injection molds made of hardened steel can produce tens of thousands of parts instead.
With 3D printing, part quantities are low. Part volumes aren’t the only reason to use 3D printing, but its cost-effective support for low-volume prototyping and production is a key consideration.
Costs
Injection molding has higher start-up costs because it requires metal tooling. When production volumes are low, the per-part cost of a tool is relatively high. When part quantities are high, however, the tool’s per-part cost is relatively low.
At sufficient volumes, injection molding has a lower per-piece cost than 3D printing can provide. It’s essential to determine this crossover volume, especially if you plan to use 3D printing for early-stage prototyping and injection molding for late-stage prototyping, low-volume production, and high volume production.
Lead Times
Because there isn’t any tooling to cut, 3D printing can produce part samples and initial order quantities more quickly. Typically, the lead time is one week. Injection molding has a longer lead time, but Fictiv can provide soft or hardened steel molds for low volumes in about two weeks.
Part Strength
Generally, injection molded parts are stronger than 3D printed parts. That’s because of how the parts are made. The layer-by-layer process of 3D printing can create weak points as layers are deposited. By contrast, injection molding uses high pressures and high temperatures to produce parts that are denser and more uniform.
Design Complexity
3D printing supports greater design complexity than injection molding. Although it can produce relatively complex parts in high volumes, injection molding can’t create the same intricate structures. For designers who plan to start their projects in 3D printing and then move to injection molding, it’s essential to understand that each process has different design guidelines.
Get the Plastic Parts You Need
Like all manufacturing processes, 3D printing and injection molding have pros and cons. Fictiv is staffed with engineering experts who can recommend the right process. We also work with a carefully vetted network of manufacturing partners and offer both molding services.
No matter what you decide, you’ll get design for manufacturability feedback along with your quote. Are you ready to get started? Create your free Fictiv account and upload your part drawing.