Time to read: 10 min
Incorrect material selection can be detrimental to the success of a project and even result in financial loss or, more significantly, loss of life. Material selection is often one of the first and most important decisions you will make in new product development or component design. I have found few design engineers are well-versed in material science and material properties, and even fewer are experts in plastic material selection.
Keep reading to learn which 3D printing plastic material properties to consider,, how to select the best 3D printing materials, and which 3D printing materials are most suitable for common applications.
Pro-Tip: Check out our 3D Printing Material Selector Tool for a simple way to narrow down material selection for your next 3D printing part design.
3D Printing Materials – Important Properties to Consider
Here are the most important properties to consider when selecting the best material for 3D printing your design:
Durability
Durability is the superhero of material properties; it indicates whether a material can withstand static, quasi-static, or dynamic loading conditions without damage or degradation. Durability depends on relevant environmental conditions and is ideally calculated throughout a part’s service life.
Durability is often evaluated by calculating or measuring wear resistance. You may use this equation to compute the wear rate is:
Vi = ki * F * S
Where:
F = normal load
S = sliding distance
Vi = wear volume
ki = specific wear rate coefficient
Index i identifies the surface considered
Tensile Strength
The strength of a plastic is a measure of how much stress it can withstand before it deforms or fails. Strength is an intensive property often quantified as tensile strength for plastic filament and is commonly expressed in units of PSI or MPa. Tensile strength is the measure of a material’s ability to resist a force that results in tension, rather than compression, for the material.
The concentration of force a material can withstand depends on the material itself. Whereas the total amount of force a part can withstand is dependent on the geometry of the part, as well as manufacturing methods, etc. Therefore, the strength of a 3D-printed part is not just dependent on the material properties. It’s also impacted by infill density, part orientation (layer lines), wall thickness, and filament temperature during printing.
Pro-Tip: Check out our article 3 Tips for Stronger 3D Printed Parts to learn how to make your 3D prints more durable!
Heat Resistance
A commonly known fact about plastic materials is that they are often susceptible to melting when exposed to high temperatures. A general rule of thumb is that thermosets (i.e., polyurethane) are much more heat-resistant than thermoplastics (i.e., polypropylene).
Pro-Tip: For a comprehensive review of thermoplastics vs thermoset plastics, check out this article.
One of the most popular ways to quantify a plastic’s ability to resist deformation when exposed to heat (heat resistance) is by evaluating its heat deflection temperature (HDT). HDT is more than just heat resistance. It measures the plastic’s stiffness when exposed to a given temperature and loading conditions. This is an important property because it’s probable that your 3D printed parts will be exposed to loading conditions, with fluctuating temperatures or heat loads.
Flexibility or Rigidity
Flexibility may be critical in some applications, whereas a material must be rigid for others. What makes a material rigid or flexible? The modulus of elasticity (Young’s Modulus) is a measure of the rigidity or flexibility of a material. A low modulus of elasticity indicates materials that easily deform under loading conditions and are more flexible.
Other properties, such as strength, stiffness, malleability, toughness, and impact resistance, are also considered subsets of flexibility or rigidity. Rigid plastics have strong inter-molecular bonds, whereas flexible polymers have weak inter-molecular bonds and weak polymer chains, allowing the chains to slide over each other and be flexible.
Chemical and UV Resistance
Often, parts are designed to withstand either chemical attack or UV light exposure. Therefore, the ability of a material to remain strong after exposure to chemicals or UV radiation is critical. As a design engineer, I have been asked to troubleshoot many instances of improper material selection for the environment the parts were exposed to and should have been designed to withstand. While you cannot anticipate everything your parts will be exposed to, a good understanding of environmental conditions and thorough research are required.
Chemical attacks and UV radiation attacks affect plastic polymers differently. Some plastics degrade when exposed to UV light due to photo-oxidative degradation, where UV energy interacts with polymer molecules. This causes the excited photons to break the bonds of the polymer’s backbone chain, resulting in a reduction of its molecular weight. As a result, free radicals are created, which are unpaired and reactive electrons that can cause unpredictable and harmful reactions. Additionally, the color of compounds is determined by chromophores, and when exposed to UV light, the resulting free radicals can disrupt the molecular structure of the polymer, leading to further degradation.
Chemicals can attack certain plastics due to a reaction that occurs on the molecular chain of the polymer. This reaction often results in the polymer chain breaking or “unzipping.” The reason certain plastics are more susceptible to chemical attack than others has to do with the composition of their molecular chains. When a plastic part experiences a chemical attack, the entanglement of the smaller segments of the molecular chain is reduced, leading to a breakdown of the plastic material. Therefore, it is important to be aware of the chemical properties of plastics in order to select the appropriate materials for specific applications.
Moisture Resistance
Designers often seek dimensionally stable plastics that don’t expand when exposed to water and/or heat. This means that the plastics will not change dimensions when exposed to water and heat.
Moisture resistance, more commonly measured by moisture absorption in plastic polymers, is the ability of a material to absorb moisture from the environment. Moisture absorption can cause changes in dimensions and material properties such as mechanical strength, electrical conductivity, and the dielectric loss factor. The electrical effects are because water within a plastic part reduces the surface resistivity and increases dielectric dissipative loss. Water absorption impacts a plastic’s strength because it degrades the polymer’s structure, causes dimensional changes, and involves extracting water-soluble components.
An example of a type of plastic with high moisture absorption (hygroscopic plastic) is polyamides (nylon, like Nylon 11, Nylon 12, or Nylon 6). Polyamides can absorb moisture readily, leading to dimensional changes, reduced strength, and changes in electrical insulating characteristics. Nylon polymers are advantageous for their high moisture absorption in some instances,
Examples of plastics with low moisture absorption (non-hygroscopic plastic) include ABS, polycarbonate (PC), PA 12, and polypropylene (PP).
Biocompatibility
The medical device industry is one of the highest utilizers of plastics, compared to other industries. . Biocompatibility is a hot topic in the medical and biomedical communities. A biocompatible plastic is one that is chemically inert (it will not cause an allergic or toxic reaction when living tissue is exposed to it). The degree of biocompatibility ranges from no response to a mild immune or inflammatory system response.. But biocompatible materials, regardless of the response they cause, should not cause harm; these responses are normal bodily reactions.
A non-biocompatible plastic may result in one or more indications like cytotoxic compound production, skin irritation, cellular disruption, formation of blood clots, and chronic inflammation. Plastics are intensively tested through several iterations and different test methods to determine biocompatibility. A biocompatible plastic must also be able to withstand one or several cycles of sterilization that would have the potential to degrade certain plastics. Some examples of biocompatible plastics include polycarbonate, ABS, polypropylene, polyurethane, and polyethermide.
Pro-Tip: To select and source the right materials for your projects,, check out How to Select & Source the Right Materials.
How to Select the Best Materials for Your Next 3D Printing Project
Now that we’ve reviewed the most important material properties to consider when selecting a 3D printing material, let’s review Fictiv’s new 3D Printing Material Selector Tool, which will simplify your material selection process.
Step 1: Select the most critical factor between properties and processes.
In our 3D Printing Material Selector Tool, the first choice is between the priority of material properties, visual appearance, and the 3D printing process. This helps narrow down the potential choices by selecting what quality or factor you would prioritize first.
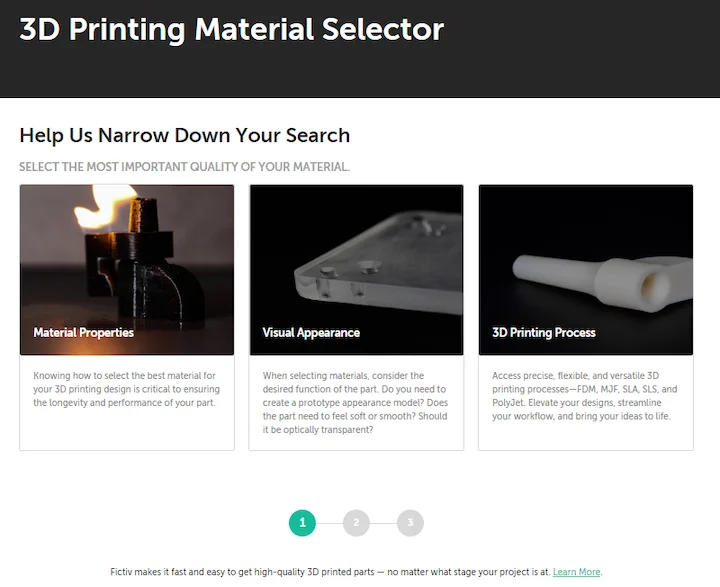
Step 2A: If You Selected Material Properties in the 1st Step
Let’s assume material properties are the most critical material selection criteria. Material properties can fall under one of several categories for 3D printing materials, such as physical, chemical, thermal, magnetic, optical, and mechanical properties.
When using our 3D Printing Material Selector Tool, select the material properties that matter the most for your part’s design by checkingone or more of the boxes, as shown in the following image:
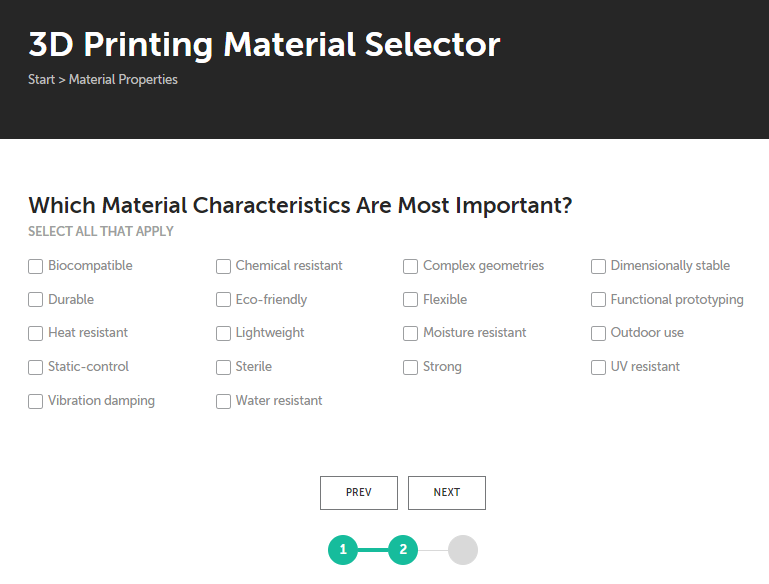
Once you select the most critical material properties, select the Next button, and the materials that fit the criteria will populate the next page. For example, when choosing a material that is durable, impact-resistant, and strong, the following options are filtered:
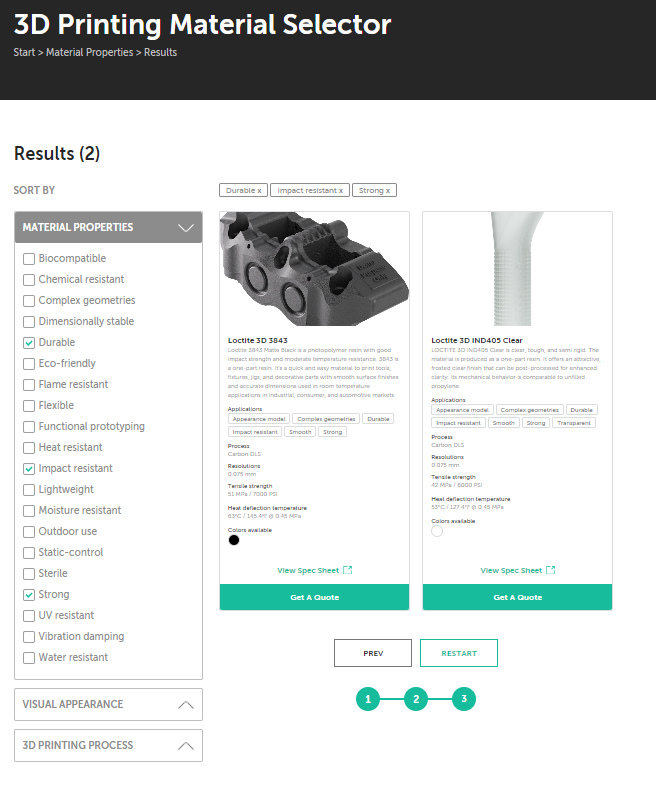
Step 2B: If You Selected Visual Appearance in the 1st Step
Sometimes, a part doesn’t need to be functional but must be aesthetically pleasing. Factors such as color, texture, and finish can significantly impact the overall part aesthetic so keep that in mind when selecting a 3D printing material. Our 3D Printing Material Selector Tool allows you to easily choose from the following visual appearance characteristics: smoothness, roughness (soft touch), transparency, color (9 available), and appearance modeling (for realistic prototypes). For example, if you select smooth and black filters with our 3D Printing Material Selector Tool, the filter narrows down to the innovative Carbon DLS material UMA 90:
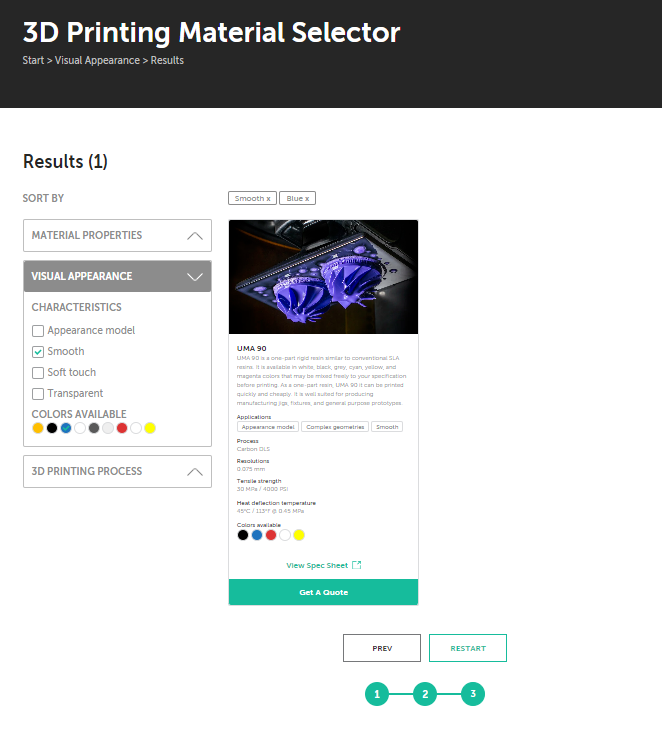
Step 2C: If You Selected 3D Printing Process in the 1st Step
Different 3D printing processes are compatible with different materials. Fused Deposition Modeling (FDM) is typically used with thermoplastics like ABS and PLA, while Selective Laser Sintering (SLS) is often used with nylon materials. You might choose one 3D printing method over another based on the cost or speed of printing. Whereas FDM is typically more affordable and faster than other methods, the surface finish produced is not as smooth. In addition, one process may be more favorable than another due to the resolution offered by each 3D printing process. For example, SLA provides a higher resolution than FDM.
Pro-Tip: Fictiv now offers Carbon DLS 3D printing, which offers injection molding level repeatability alongside the ability to manufacture complex geometries.
For example, choosing SLS as the 3D printing process, using our 3D Printing Material Selector Toolyields the following results:
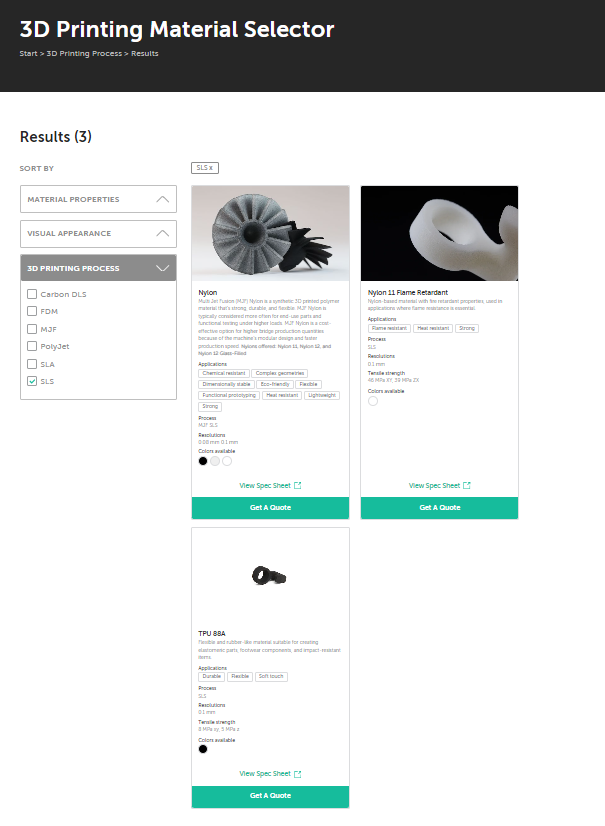
Step 3: Narrow Down Your Selection with the Second Step
After you make your first selection from material properties, visual appearance, or printing process, you can narrow your selection further by selecting the next important criteria. Say, for example, you chose material properties as the most important criteria, but you also wanted to select a material that meets your aesthetic requirements. Simply choose the aesthetic requirement from the drop-down list as well as shown here:
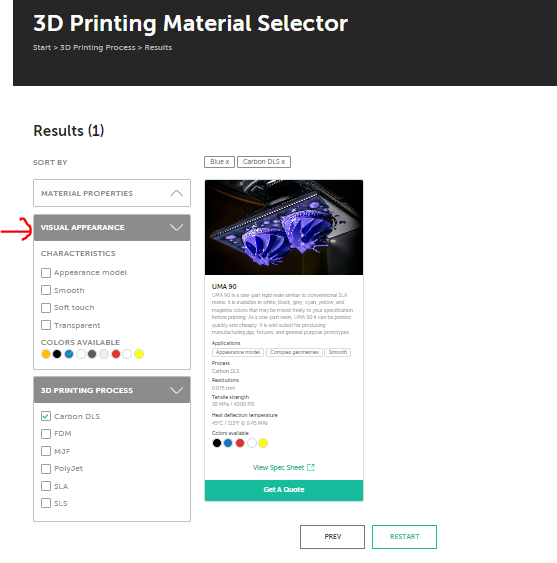
Selecting the Best Material for 3D Printing
Choosing the most suitable material for 3D printing is crucial to ensure that the end product meets the required specifications and performs as expected. In this section, we will explore some examples of applications where selecting the best material for 3D printing is critical and discuss the factors that must be considered when choosing a material.
Application One: Electronics Enclosure
An electronics enclosure is designed to protect electronics components from environmental factors like heat, moisture, impact, and vibrations. Plastic enclosures are often utilized because they are lightweight and easy to rapidly manufacture.
Material properties are a critical consideration for electronics enclosure design. The top properties are durability, flexibility, density, moisture resistance, impact resistance, strength, and heat resistance.
ABS, ABS ESD, PLA, nylon, and polycarbonate are good material choices for electronic enclosures.
Application Two: Appearance Model Prototypes
3D printing is often utilized to prototype and model parts and designs. One of the most important prototype models is an appearance model which is a type of 3D printed model that is created to showcase the appearance and design of a product. Appearance models are commonly used for marketing, advertising, design validation, and feedback.
Realistic representation and fine detail and accuracy, are characteristics of appearance models, which are often 3D printed. Appearance models are typically used to provide visual representations of products to investors, potential customers for examination and evaluation.
Since appearance models are likely to be visually examined, their visual appearance properties are the most important when selecting a 3D printing material. Surface finish, or the smoothness of the surface, is critical, along with resolution, to ensure all fine details are correctly displayed for the prototype acceptance. For functioning appearance model prototypes, transparency may also be important as it can allow mechanical components to be visualized.
Loctite 3D, ABS, PLA, Nylon, Vero, and Accura 25 are all excellent choices for appearance models.
Application Three: Automotive Parts
3D printing of automotive parts is widespread, with nearly all major auto manufacturers implementing 3D printing technology at their factories and design centers. From prototyping to low-volume production, 3D printing has proven to be a game-changer in the automotive world. 3D printing enables us to create highly customized and complex parts with ease.
The selection of 3D printing material for automotive components predominantly focuses on UV resistance, weather ability, heat resistance, durability, and toughness. This is due to the exposure of automotive components to UV light, environmental conditions, stress, repeated use, and impact.
ASA, Ultem 9085, Somos PerFORM, EPX 82, RPU 70, and Loctite 3D are all excellent choices for automotive 3D printed parts.
In conclusion, selecting the right material for your project is crucial to its success. When it comes to 3D printing services, understanding the important properties of plastic materials is essential for achieving the desired strength, durability, heat resistance, flexibility, and chemical/UV resistance. By considering these factors and using the right tools and resources, you can make informed decisions about material selection for your next 3D printing project. Remember to always do thorough research and understand the application of your parts entirely. With the right material and design considerations, you can create strong, durable, and long-lasting 3D printed parts.
Fictiv is the ultimate partner for professional and rapid 3D printed parts backed by high quality and expert guidance. Upload a design today for an instant quote.