Time to read: 12 min
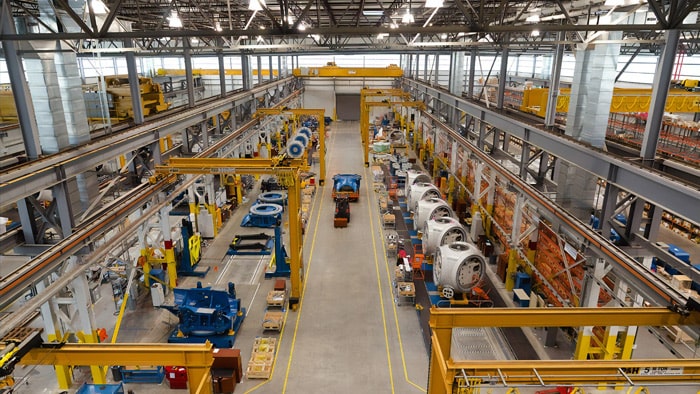
What’s a macro trend (also known as a macrotrend)? While a trend is a general shift toward a specific thing, a macro trend is a persistent and widespread shift on a global scale. Examples include urbanization, automation, and globalization. It’s much longer-lasting than a fad and tends to change national or global culture and practices.
2022 has brought challenges to the manufacturing industry that have given rise to certain macro trends, and companies are joining these macro trends to alleviate pain from these challenges:
- Skills gap
- The rise of automation
- Labor shortages
- Supply chain disruptions
With these challenges comes a refocusing period where manufacturers must understand the macro trends and their dynamics to adjust their processes and strategies. Manufacturing trends, including increased productivity in the face of rising costs and new production processes spurred on by material innovation, all stem from these global shifts. Companies can either stay ahead of the game or get left behind; so follow our macro trend guide for manufacturing to get ahead of the curve!
Why Macro Trends Matter
Macro trends matter because new manufacturing trends come with new risks and uncertainty. New trends generate:
- Demand volatility
- Capital cost uncertainty, currency fluctuations, and commodity price volatility
- Supply chain risks and location-specific risks
- Talent shortages
- Government policies that support and foster domestic manufacturing to impact manufacturing
Organizations have already faced the challenges presented by current macro trends with a reduced labor shortage and fluctuating demand post-pandemic. Companies are also designing more customized products to meet customer demand. Value-added services continue to grow, and locations with low cost of living are seeing a rise in wages.
Macro Trends in Manufacturing To Pay Attention to Today
Several macro trends are already exerting their influence over the manufacturing industry, and future macro trends are already in the wind. Here are 10 examples of macro trends that are gaining momentum and will affect the future of all manufacturing.
1. Digitizing Manufacturing Processes and Supply Chain: Industry 5.0, IoT, and Blockchain
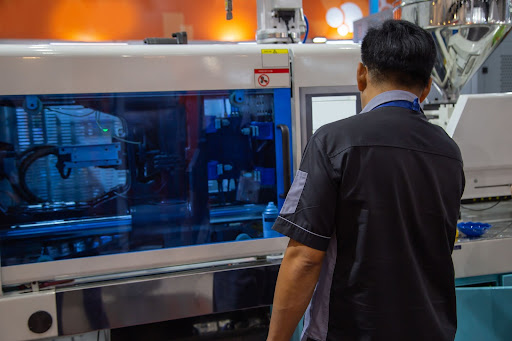
Robots are taking over the world! Just kidding… mostly. Unless you’ve been hiding under a rock, robotics, automation, and AI are everywhere; taken together, Industry 5.0, blockchain, and IoT are also bringing technology to the forefront of manufacturing. Some companies have fully incorporated these technologies and automation into their manufacturing processes, while others have hung behind to see where these macro trends will lead.
You know what they say: if you can’t beat them, join them. Now is the time to think about digital transformation of your manufacturing processes and supply chain.
Industry 5.0
The speed with which industry continues to change takes many by surprise. It wasn’t that long ago people were talking about Industry 4.0, or the fourth Industrial Revolution, which focused on automation. The Industry 4.0 movement was about the interconnectivity of systems and machines to optimize performance and increase efficiency. Industry 5.0, an emerging macro trend, seeks to put the human element back into manufacturing and forge a collaborative partnership between humans and robots.
Industry 5.0 is all about robots and automation helping people work better and faster by leveraging advanced technology such as big data and IoT, but with a human touch and a more personal aesthetic to manufacturing. By merging cognitive computing capabilities with human intelligence and resourcefulness, you can achieve higher levels of collaboration and efficiency than ever before.
Industry 5.0 is not about superseding humans on the manufacturing floor. It’s about supporting humans and optimizing the balance between efficiency and productivity.
IoT in Manufacturing
With increased connectivity, manufacturing firms can gather more data and analyze it to glean insights that facilitate optimization and process improvements. The Internet of Things (IoT) in manufacturing — sometimes called the industrial internet of things or IIoT — enables companies to connect and monitor a multitude of operational components.
IIoT makes use of smart sensors and cloud computing to enable equipment and systems to communicate with one another over the internet. Using IIoT, manufacturers can improve safety, cut costs, increase efficiency, and accelerate new product development.
The IIoT market is expected to be worth US$110.6 billion by 2025, with manufacturing being a key driver of growth. Across the entire sectors, there has been more than twice as much IoT investment in the manufacturing industry as there has been in smart homes or production asset management.
Blockchain
A blockchain aggregates information in groups, also known as blocks. Blocks have certain storage capacities and, when filled, are connected to the previously filled block, forming a chain of data known as the “blockchain.”
When it comes to industrial manufacturing settings, a blockchain is utilized to record transactions and provide seamless tracking of a business’ assets. Blockchain technology also helps businesses leverage the full potential of other advanced technologies like IoT, 3D printing, and augmented reality
Blockchain provides immediate, easily accessible, and secure information — which can be used to increase supply chain transparency. The security of blockchain allows the tracking of the credentials and identities of key personnel and optimizes audits and regulatory compliance. It enhances track-and-trace and protects and monetizes critical intellectual property. Blockchain also simplifies and protects quality checks, advances machines as a service, and enables machine-controlled maintenance.
For manufacturers, blockchain increases visibility across every process, from supply and procurement to strategic sourcing and supplier quality. Shop floor operations, including machine-level monitoring and service, can benefit from blockchain’s distributed ledger structure and block-based approach to efficiently aggregating value-exchange transactions.
Industry 5.0 is arguably one of the most important current macro trends in manufacturing, and both IoT and blockchain technology support it.
2. Machine Learning and Artificial Intelligence
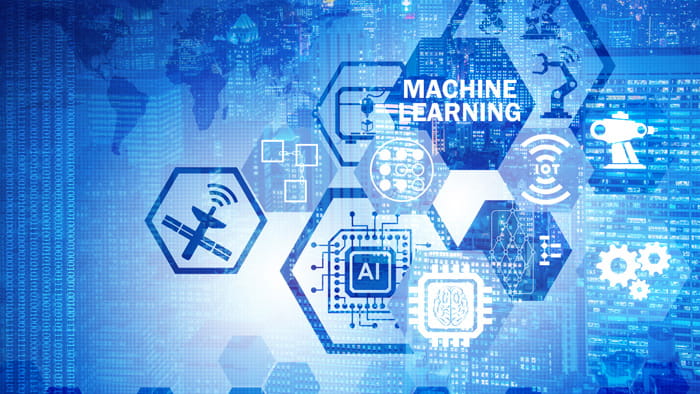
Remember the Steven Spielberg movie A.I. Artificial Intelligence? It was about a life-like child robot that was released in 2001. The movie scared me so much as a child that I still think of it when anyone mentions artificial intelligence (AI). Well, now we’re living in a future similar to the one the movie allowed us to fantasize about.
Machine learning and AI continue to be a consistent macro trend in manufacturing because they provide three fundamental values for manufacturing: scale, speed, and convenience. The fundamentals of speed and scale refer to a manufacturer’s ability to automate industrial functions without assigning a group of employees to designated tasks. With automation, a company achieves a reduction in time invested in a variety of jobs.
Machine learning uses computer systems capable of acquiring knowledge and adapting to circumstances without following explicit instructions. The technology uses algorithms and statistical models to analyze and draw inferences from patterns in data. AI allows computer systems to recognize trends and infer logical conclusions to perform data-driven decision-making.
With the enhanced logic capabilities of machine learning and AI, manufacturers can improve operations across an entire enterprise. The following processes are exceptionally compatible:
- Supply chain and logistics
- Inventory management
- Asset tracking
- Warehouse budgeting
- Transportation budgeting
- Forecasting
AI and machine learning are poised to provide much more value for manufacturers in the future. With them comes improved efficiency and increased profit margins.
3. Value Stream Transformation
Value stream transformation is a crucial tool for aligning manufacturing with post-COVID-19 expectations. Value stream transformation is a systematic approach aimed at achieving sustainable improvements throughout a company while developing a continuous improvement culture.
During the pandemic, companies raced to the cloud. According to the Flexera 2022 State of the Cloud Report:
- 53% of those surveyed said their annual spend on cloud technology is at least $1.2 million, up from only 38% in 2021
- 59% are focused on optimizing their existing use of cloud tech with cost savings
- 57% have a focus on migrating more workloads to the cloud within their business
COVID-19 increased interest in IoT technology for its remote monitoring and predictive maintenance capabilities. Manufacturing firms are now hoping to move into a post-COVID world using the lessons learned to transform their value stream.
There are three critical steps needed to move value stream transformation forward after the pandemic:
- Respond: Companies must take immediate actions to promote safety and essential business operations.
- Recover: Companies must restart activities such as opening, hiring, budgeting, and supplying as well as making a plan to restore a scalable state.
- Renew: Companies should take lessons and decipher emergent patterns from the first two steps to develop a new foundation.
Manufacturing firms need to strategically execute all of these processes to ensure a successful transformation. After the lessons learned from the COVID-19 pandemic, manufacturing companies are now looking to ways to make their businesses resilient to upcoming challenges that will inevitably occur in the future.
4. Manufacturing on Demand (MOD)
Manufacturing on demand, or MOD, is all about producing what customers need when they need it. With this technology, there’s no more manufacturing vast quantities of the same thing and storing it in inventory until someone buys it.
Using cloud technology and a digital self-service platform, customers obtain quotes for parts in real-time and stay connected to the order production process through to delivery. They order precisely the quantity needed for their requirements, leveraging JIT (just in time) manufacturing to its fullest extent.
Platforms like Fictiv’s operating system for custom manufacturing enable MOD with industry-first features for visibility, speed, traceability, and quality. Customers can use it to order custom mechanical parts for both prototyping and production. The platform fits in with work-from-home requirements and responds to compressed product introduction timelines.
MOD customers benefit from on-demand production status updates, centralized access to design files, historical DFM, and other features that streamline manufacturing while saving on materials and storage. All of the data for an order is in one place, and the customer can get expert guidance if needed.
The impact of MOD on enterprise customers ordering and tracking hundreds of parts at once is tremendous. 24/7 visibility, transparency, and access to a real-time schedule keep everything moving efficiently. With the use of CNC machining, customers can obtain complex, high-precision mechanical parts at 100 times the speed and one-tenth the cost compared to traditional manufacturing.
5. IoT-Enabled In-Plant Automation
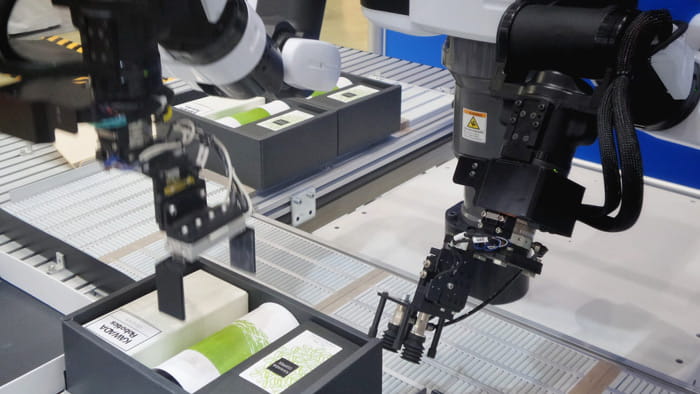
IoT-enabled in-plant automation is another way to interconnect devices within an existing infrastructure. Connectivity enables manufacturing to reduce costs, enhance efficiency, improve safety, and innovate.
A growing number of production processes are leveraging smart devices and embedded intelligence. While not all firms have adopted these technologies, many manufacturers are planning to embed IoT into their products or processes. Along with predictive analytics, IoT technology offers new ways to connect businesses and improve processes.
Manufacturing accrues many benefits from IoT-enabled automation, including:
- Improved inventory management
- Upgraded supply chain visibility
- Enhanced product quality controls
- More real-time insights
- Increased cost savings
- Better asset security
Companies increase revenue and improve their supply chain with asset interconnectivity because they can anticipate the market, monitor assets, and mitigate unplanned shutdowns with predictive maintenance.
6. Picking Automation Using Cobots
A cobot is a collaborative robot designed to allow robots and humans to work together. Using cobots, organizations get more work done faster and safer while reducing repetitive tasks for employees. AMRs, (autonomous mobile robots) are cobots tailored for partnership with people. They are programmed to perform non-value-added tasks like moving heavy products, which frees humans to perform skilled labor tasks instead.
One of the most common cobot uses is picking in a logistics setting. In automated picking, a robot travels throughout a warehouse to pick the correct product. Employees then perform the rest of the fulfillment process. Cobots eliminate the walking time, which accounts for half of the time it takes a human to pick a product. Plus, the number of orders per hour a human can pick pales in comparison to a robot — humans pick between 60 and 80 orders per hour, while cobots pick up to 300 orders an hour. And often, automated picking introduces a higher level of accuracy into the process.
7. Integrated Planning Through ERP
Enterprise resource planning (ERP) includes demand planning, inventory planning, distribution planning, and RM and RG planning. ERP is a cloud-based solution that is easy to deploy and affordable for small businesses.
ERP tools help manufacturers automate multiple operations using a single system. Universal touchpoints provide exceptional insight over an entire operation. These tools help companies find and expedite improvements and make adjustments when needed.
More and more manufacturers are layering agile applications on top of their existing ERP solutions instead of using ERP tools for all of their tasks. Typically, data drives ERP upgrades, enabling manufacturers to move data forward and consolidate it around modern data platforms. Using ERP software as part of this process results in a faster time-to-value.
Manufacturers are also able to build tangent functions atop existing data models without requiring a total replacement of the ERP or making substantial updates to it.
8. Sustainability in Manufacturing
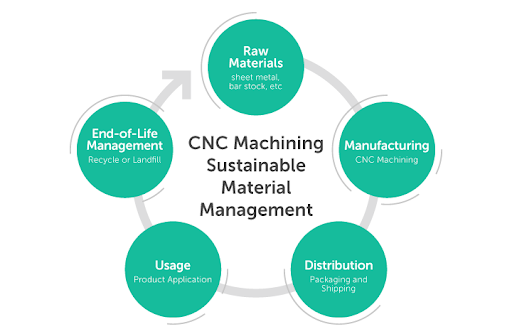
Sustainability is a supporting component of today’s overall environmental preservation trends. Working on process sustainability allows manufacturers to maintain a stable level of natural resources, rather than depleting them. So, sustainable paper manufacturing obtains wood from forests that are continually replanted. In other industries it means recycling and reusing oil, plastics, and glass.
The primary drivers of sustainability in manufacturing are:
- Improvements in energy efficiency
- Reductions in greenhouse gas emissions
Sustainability is a market driver because people increasingly desire environmentally sustainable products and practices. In our 2022 State of Manufacturing report, 63% of companies surveyed stated that product sustainability is increasingly important.
Improvements in sustainable practices are critical in the production of energy-intensive commodities like aluminum and cement, where energy costs can be 20% of total landed costs. The steel, chemical, and refined products industries face regulatory pressure to become more sustainable because they contribute up to 60% of the manufacturing sector’s CO2 emissions.
The trend toward greater energy productivity is encouraging energy producers to change their mix of energy inputs from coal to cleaner fossil fuels or renewables. The transformation includes upgrading to newer technology, more efficient processes, and changing the materials mix to reduce emissions
9. Agile Manufacturing and Supply Chains
Supply chains are trending toward high-mix, low-volume (HMLV) manufacturing. In these cases, organizations need effective supply chain management to save costs while still being able to deliver products when and how the customer wants them.
Supply chain agility refers to the use of responsiveness, competency, flexibility, and quickness to manage daily supply chain operations using real-time data and updated information. Agility is all about keeping pace with the demand in supply chain and being resilient to disruptions in within supply chains. Agile supply chain technology impacts everything — procurement, inventory, assembly, logistics, transportation, and sales.
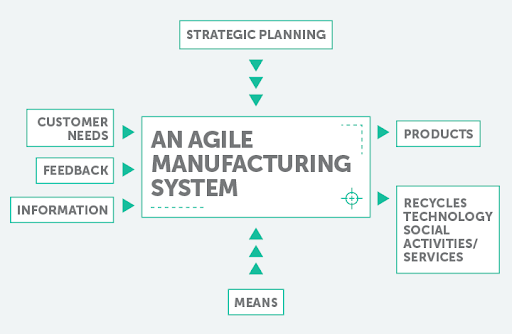
When you think of agile manufacturing, you may think of lean manufacturing, but they’re different concepts with different goals. The goal of lean manufacturing is to eliminate waste, whereas the goal of agile manufacturing is to utilize current resources intelligently. Agile manufacturing started with an agile approach to product development and has resulted in innovations in manufacturing, such as the ability to load a 3D model into a CNC machine to produce parts.
10. 3D Printing and Additive Manufacturing
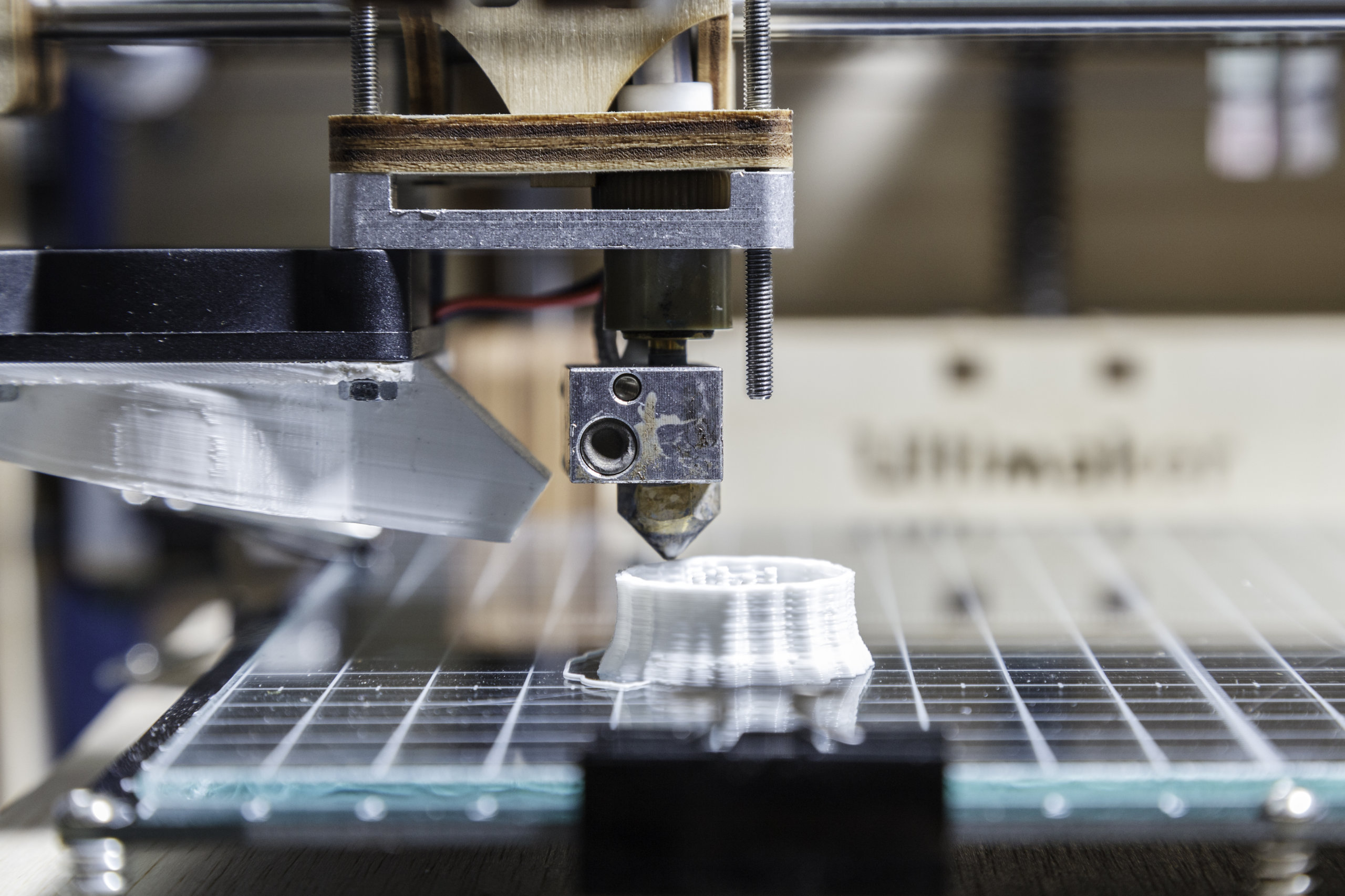
One of the most popular forms of additive manufacturing, 3D printing, uses CAD (computer-aided design) software to build custom parts and products a layer at a time. Additive manufacturing has increased its material capabilities dramatically over the past few years, moving from just plastics to concrete, metals, and even food 🤯! The applications for 3D printing are continuously expanding.
Additive manufacturing is particularly useful for modeling, prototyping, building molds, replacing investment casting, or manufacturing components for a final finished piece. 3D printing provides significant cost and time savings, and its use is growing at an accelerated rate — additive manufacturing is expected to grow to be a $23 billion industry by 2026.
Additive manufacturing enables cost-effective production of metal parts that, in the past, were impossible to produce with other methods. Selective sintering technology, an additive manufacturing technique that uses a laser to sinter powdered material, lets companies build metal products in-house, eliminate tooling costs, and significantly reduce development time. It has greater flexibility in shapes and materials while speeding up production and cutting costs.
Looking Ahead…Trends to Watch for in 2023
While a vast majority of these trends are likely to stick around for the next few years, there are some macro trends in the manufacturing industry to look out for in 2023:
- Smart factories
- Corporate commitment to social activism
- Fighting infodemics and misinformation
- Radical transparency for everything from diversity initiatives to sustainability pledges
Conclusion
In previous decades, manufacturing organizations lagged in technological adoption and innovation, but that has changed significantly. Macro trends are now driving current and future improvements in manufacturing in ways never before seen. For each macro trend, the industry has responded with new and improved processes that cut costs, provide efficiencies, and help to meet consumer and B2B demand. A majority of these macro trends have the goal of reducing costs, which is a particular focus in manufacturing because of rising material costs and labor shortages.
A successful organization understands the implications of each macro trend as it appears and makes the necessary changes to continue growth. Many of the changes are already occurring and are set to expand manufacturing capabilities if companies successfully adopt them.
To learn more about the current trends in manufacturing and how to leverage them to promote growth, read Fictiv’s 2022 State of Manufacturing Report which provides valuable manufacturing industry analysis and insights.
Sourcing Simplified
If you’re tasked with sourcing and supplying mechanical parts, Fictiv is your operating system for custom manufacturing that makes it faster, easier, and more efficient. In other words, Fictiv lets engineers like you, engineer. We offer a range of manufacturing capabilities to produce both simple and incredibly complex geometries — create a free account and upload your designs today!