Time to read: 6 min
In today’s complex business climate, the capacity to bring new products to market quickly is central to staying ahead of the competition. New Product Introduction (NPI) is a critical process in an item’s lifecycle, and its efficiency directly impacts time-to-market and the product’s profitability. To achieve faster NPI, companies often turn to digital manufacturing, which leverages cutting-edge technologies to digitize and enhance various processes, including design, material selection, manufacturing, quality feedback, and shipping.
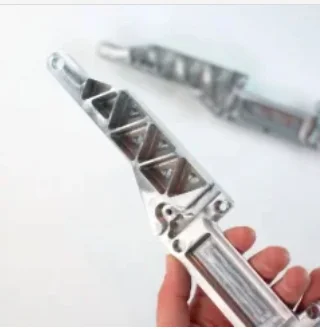
From planning and prototyping to mass production, digital manufacturing utilizes data-driven approaches to streamline the NPI process, enabling companies to be more flexible and responsive to customer demand. This article explores how digital manufacturing can accelerate NPI and help companies overcome traditional obstacles by leveraging advanced technologies and data-driven feedback systems.
Digital Design and Prototyping
One critical aspect of NPI is the design and prototyping phase. For several reasons, digital design and prototyping play a crucial role in accelerating NPI.
Utilizing Computer-Aided Design (CAD) Software
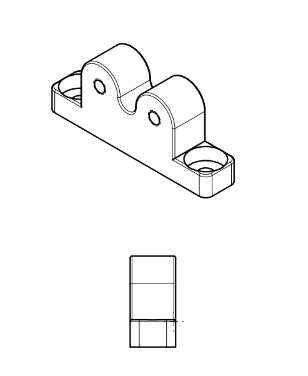
Digital manufacturing begins at the planning stage, with CAD (computer-aided design) modeling. CAD software lets draftsmen, engineers, and designers make point-by-point and complex part designs virtually. This virtual portrayal empowers fast cycles, change implementation, and design improvements much faster than the time customarily spent on hand drawings or physical modeling.
Importance of Simulation Tools and Virtual Prototyping
3D simulation software like Finite Element Analysis (FEA) and rendering programs for virtual prototyping further improve the prototyping process. Engineers can impart various boundary conditions and inputs, testing the part’s response and durability with FEA.
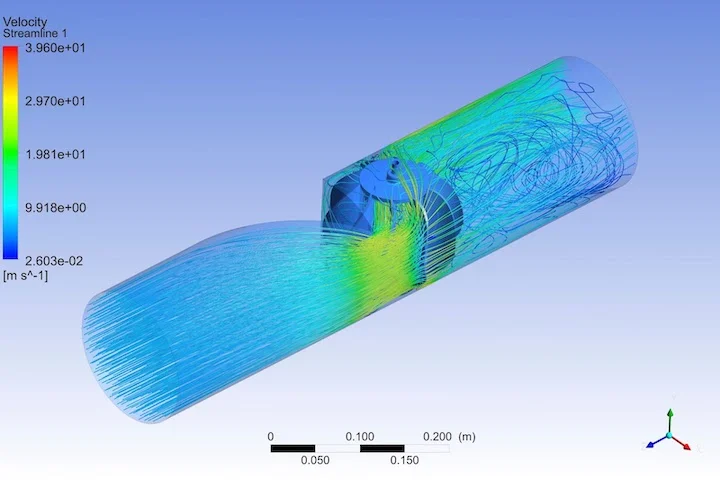
Depending on the industry, specifications, test requirements, and customer acceptance, test results from simulations may be accepted in place of physical part testing. This reduces NPI costs and can accelerate new product introduction because these simulations typically have a much lower lead time than physical testing. Virtual prototyping empowers groups to recognize potential issues and make changes before moving to the physical prototyping stage, saving significant time in the NPI cycle.
Reduction of Physical Prototypes and Accelerated Design Refinement
NPI processes frequently include many design iterations, each requiring revisions to or entirely new solid models. Digital manufacturing reduces the number of required prototypes. The capacity to repeat and refine plans carefully limits the requirement for broad testing and prototyping, adding to a smoother and faster NPI process.
Fundamentally, coordinating computerized plans and prototyping in the NPI cycle allows for a more efficient and fast item improvement venture. The advantages go beyond time savings, encompassing better design accuracy, reduced costs, and a more competitive market.
Real-time Collaboration and Communication
Collaboration and communication are pivotal in the NPI cycle, especially when key process stakeholders or team members responsible for manufacturing new product prototypes are geographically dispersed. Digital manufacturing works with constant cooperation and correspondence, guaranteeing consistent data trade among cross-practical groups.
Overcoming Geographical Barriers through Digital Collaboration
Conventional NPI processes frequently need support when teams are distributed across regions. Digital manufacturing resolves this issue by providing seamless stages that enable real-time continuous correspondence and information sharing. Virtual gatherings, cloud-based record sharing, and collaborative programming instruments engage groups to collaborate and expedite NPI’s advancement consistently.
Tools for Real-time Communication Among Cross-functional Teams
As the NPI cycle evolves, it’s essential to have tools that help cross-functional teams communicate in real-time. Fortunately, digital manufacturing offers many options for ensuring efficient and effective remote communication. As I am sure everyone in the post-COVID-19 world now knows, we can use video conferencing, instant messaging, and project management platforms to collaborate and work together, regardless of our physical locations.
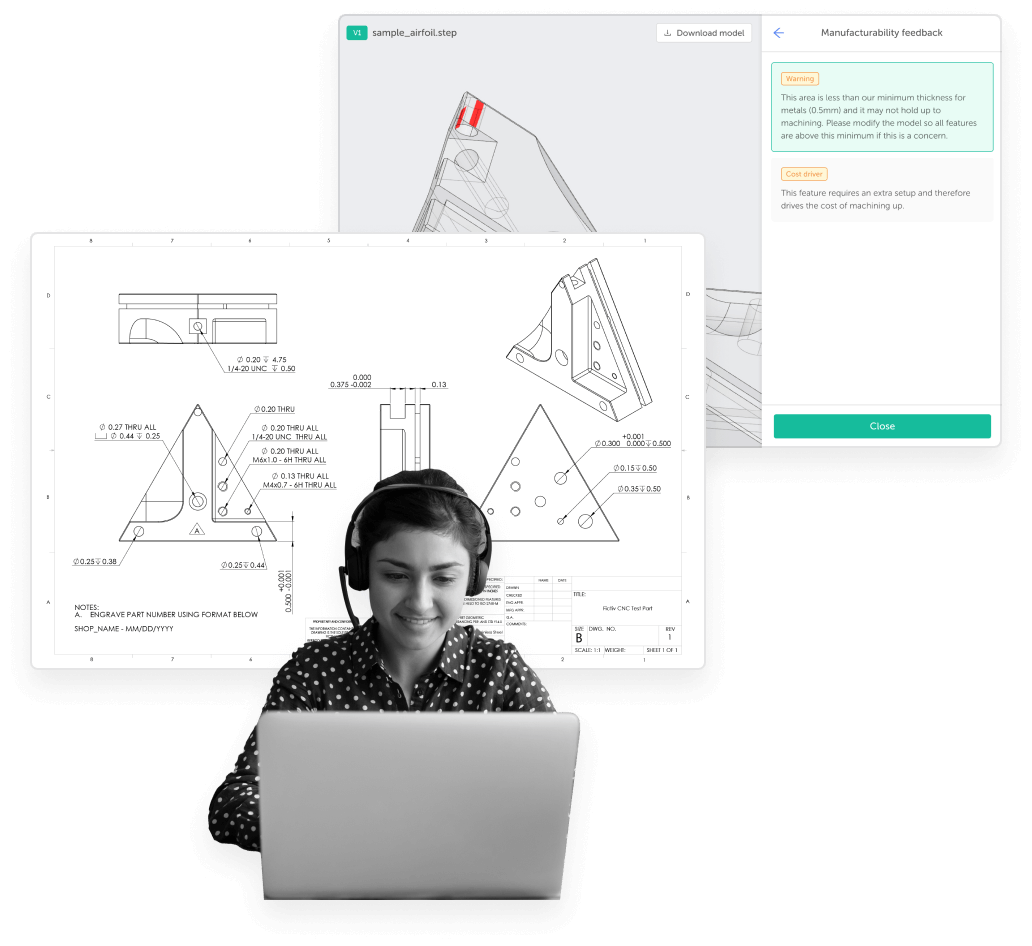
Digital manufacturing platforms like Fictiv’s further enable cross-functional collaboration with real-time visibility and tracking of manufacturing progress. Extending the cross-functional collaboration further, every part uploaded to the Fictiv platform receives expert design for manufacturability feedback—including instant, automated warnings and customized recommendations from our manufacturing engineers, as needed.
Smart Manufacturing Technologies
Brilliant innovations, including the Internet of Things (IoT) and modern mechanization, are essential in speeding up NPI by bringing knowledge and proficiency into different manufacturing system features.
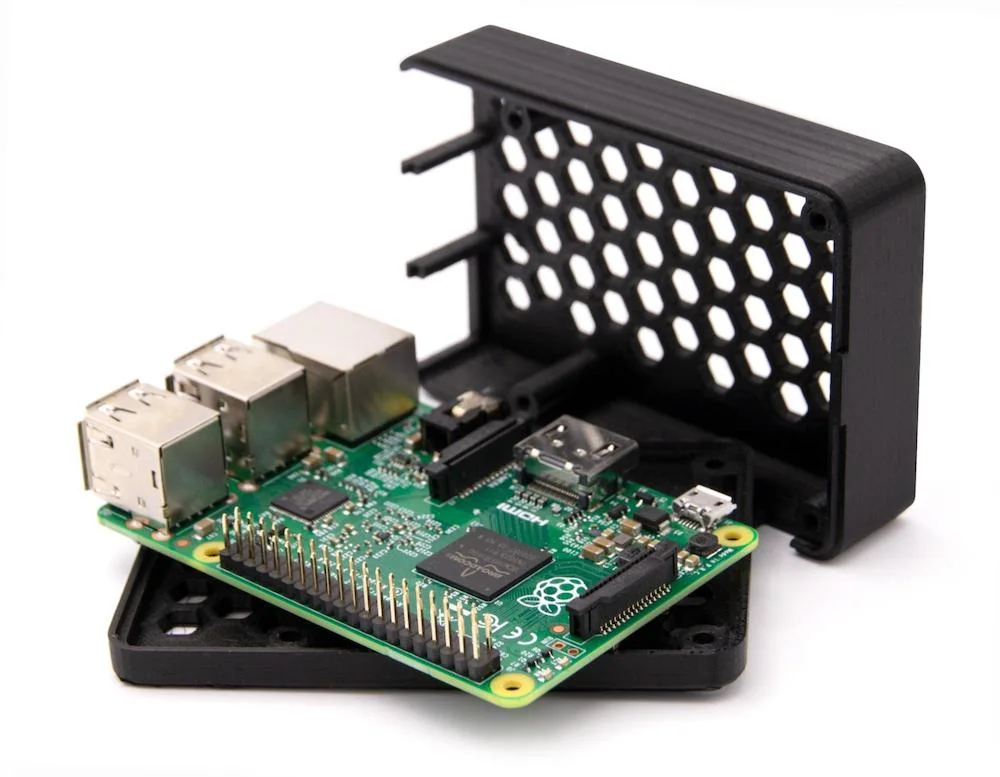
IoT in Manufacturing and Assembly Processes
IoT includes implanting sensors and other wireless technologies into machines and robots. Regarding NPI, IoT gives constant information on manufacturing processes, hardware execution, and item quality. Sensors on hardware gather data, which is analyzed to distinguish designs, anticipate possible issues, and improve creative effectiveness. This proactive approach guarantees that any deviations from expected results are quickly dealt with, limiting disturbances in the NPI timetable.
Role of Industrial Automation in Accelerating Production
Modern robotization is a foundation of assembling and utilizing mechanized frameworks and mechanical technology in the creation cycle. Computerization lessens manual intercession, smoothes tedious undertakings, and improves production speed.
Regarding NPI, robotization guarantees that complex work imperatives don’t bottleneck the assembling system. Robotization also speeds up the creation stage and improves an item’s production consistency and accuracy.
Proactive Issue Identification and Resolution Through Real-time Data
One of the vast benefits of manufacturing advancements is the capacity to recognize and resolve issues proactively. Continuous information from IoT sensors and mechanized frameworks gives insights into the health of the manufacturing system. Any deviations from predefined boundaries trigger cautions, permitting groups to mediate instantly and address possible issues.
The reconciliation of continuously coordinated effort apparatuses and shrewd assembly advancements in the NPI cycle improves spryness, responsiveness, and productivity. These innovations enable groups to team up successfully and bring insight into assembling processes, adding to a quicker and smoother NPI venture.
Supply Chain Optimization
Inventory network improvement is essential to speeding up NPI with digital manufacturing. Supply chain optimization can streamline manufacturer selection, improve lead times, and reduce inventory issues using digital manufacturing insights and information-driven knowledge.
At Fictiv, we bring you a global manufacturing network that simplifies sourcing. Our network, spanning four global regions, gives you next-gen supply chain resiliency and agility. In each region is a Fictiv Operations Hub, led by a General Manager and staffed with Fictiv quality engineers, logistics managers, and manufacturing engineers to ensure quality at the source.
Streamlining the Supply Chain to Meet NPI Demands
One goal of NPI is to create an adaptable and robust inventory network. Digital manufacturing permits companies to quickly vet production partners, guaranteeing that the required parts are accessible when needed. Companies can remedy NPI difficulties by enhancing their inventory network, enabling them to meet tight timetables without settling on quality. Resolving issues with the inventory network likewise improves cash on hand and customer relationships.
Quality Control and Continuous Improvement
Quality control is vital in NPI, and digital manufacturing upholds powerful components for constant observation and consistent improvement throughout the creation lifecycle, transparency, and feedback mechanisms available in a digital world. Some examples of how digital manufacturing enables quality control and facilitates continuous improvement are:
- Real-time Monitoring of Production Processes
Digital manufacturing enables real-time monitoring of manufacturing processes through sensors and information investigation. This continuous monitoring allows manufacturers to track Key Process Indicators (KPIs) constantly and immediately recognize deviations from quality requirements. Manufacturers can guarantee that the new products function as intended by progressively observing temperature, strain, and measured dimensions.
- Immediate Identification of Deviations from Quality Standards
In traditional manufacturing, distinguishing quality issues includes post-manufacturing inspection, prompting possible deviations, potential escapes of non-conforming products, and ultimately inflating costs. Digital manufacturing often enables measuring and monitoring critical quality indicators during manufacturing, limiting the potential of numerous parts with quality issues getting through production or eliminating quality issues with proactive feedback mechanisms.
- Implementation of Continuous Improvement Initiatives Based on Data Insights
Information collected through digital manufacturing processes provides excellent feedback mechanisms that are useful in new product development. Manufacturers can use collected data to implement continuous improvement initiatives backed by accurate data instead of hunches.
By examining patterns and examples, manufacturers can distinguish regions for improvement, refine fabricating cycles, and upgrade effectiveness. This obligation to constant improvement guarantees that the NPI interaction advances and adjusts to evolving necessities, situating the association for long-haul achievement.
Inventory network streamlining and vigorous quality control systems are essential to speeding up NPI with Digital manufacturing.
Generally, the mix of Digital manufacturing in the NPI cycle means a change in perspective. It goes beyond improving individual stages; it changes the whole item improvement lifecycle. By embracing advanced approaches, associations position themselves to explore the intricacies of NPI with expanded proficiency, lessening time-to-advertise and improving generally speaking item quality.
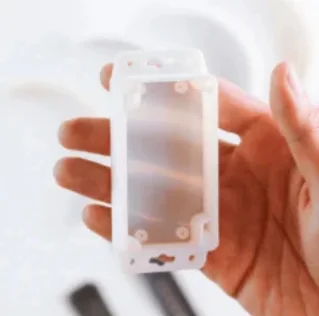
I have learned that as Digital manufacturing develops, companies that invest in these processes are better positioned for sustained success. It’s not only about speed and efficiency, there are other benefits such as improved collaboration, data-driven decision-making, and a guarantee of continuous improvement.
As we move forward, the integration of digital manufacturing and NPI will undoubtedly shape the future of product development. By leveraging technology, streamlining processes, and fostering a culture of innovation, companies can establish their position at the forefront of their industries, driving success through accelerated and efficient new product introductions.
Your digital manufacturing production partner is Fictiv. Fictiv’s digital quote-to-order platform puts you in the driver’s seat and keeps you connected at every step of the manufacturing process. Get a quote in seconds with parts delivered as fast as one day. Done right the first time. CNC machining, 3D printing, injection molding & urethane casting services in 1 partner. Upload a part for a free, instant quote today.