Time to read: 4 min
Let’s say you’ve got a great idea for a new product. You’ve turned your back-of-the-napkin sketch into a CAD file, and you’re ready to engage a manufacturer. You know you’ll need a prototype, but you’re hoping you won’t need to repeatedly revise your design. It won’t be long, you think, until it’s time to submit an initial order and think about high-volume manufacturing — you can already imagine the orders rolling in.
Prototyping is usually an iterative process, however, and the goal isn’t to simply prove that your design is correct. You also need to determine which details drive the cost of your product, and consider quality, production timetables, and market acceptance. If the prototyping process doesn’t reduce the cost of your design, redesigning a part that you thought was manufacturing-ready will get expensive.
Fictiv can help you get high quality parts at ridiculous speeds in part by providing design for manufacturing (DFM) feedback along with our response to your request for a quote. That’s important because DFM is how you get quality parts that are easier to produce and cost less – even if those parts are complex. Create a Fictiv account and upload your CAD file to get started, and keep reading to learn more.
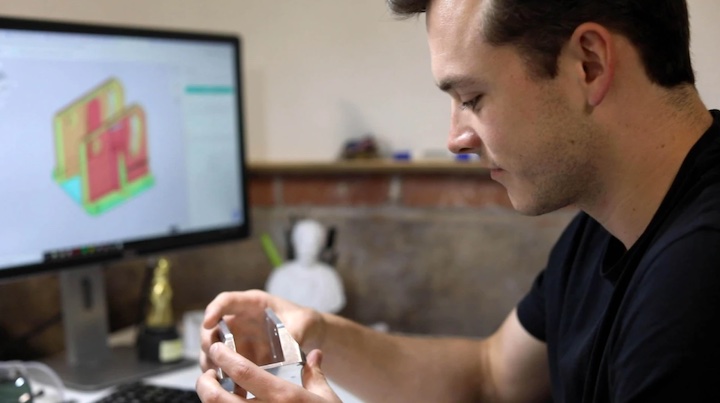
The Four Types of Prototypes
As much as you hope your initial design is perfect, you’ll probably have to make some changes along the way. You’ll also probably produce some different types of prototypes, often referenced as alpha, beta, working, and functional prototypes. Regardless of the nomenclature, prototyping provides an opportunity to refine your design so that it’s less expensive to manufacture.
Type | Purpose |
Proof-of-Concept | Evaluate scale and form.Demonstrate some level of functionality. |
Appearance (Looks-Like) | Visualize the product’s final appearance |
Functionality (Words-Like) | Validate the product’s form, fit, and function. |
Pre-Production (Looks-Like and Works-Like) | Validate the product’s final appearance and utility. |
Proof-of-concept prototypes have the lowest level of fidelity to the final product, while pre-production prototypes have the highest. So, how do you reach increasingly higher levels of fidelity as cost-effectively (and quickly) as possible? For that matter, how do you ensure that the design decisions you make won’t limit manufacturability when it’s time for high-volume production?
Working with Fictiv gives you access to expert DFM feedback along with a vetted network of manufacturing partners who can make your parts using 3D printing, CNC machining, injection molding, and urethane casting. Before choosing your method, it’s important to understand the costs associated with each of these processes because your product may need to use more than one process in going from prototyping through production.
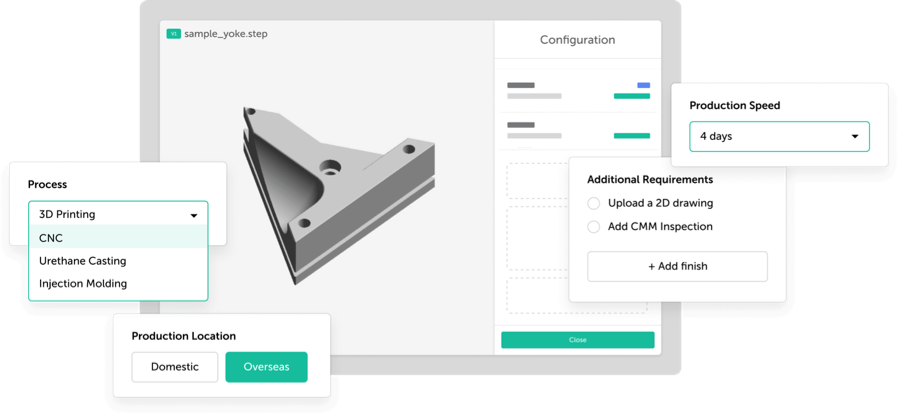
3D Printing
3D printing is synonymous with rapid prototyping, but this form of additive manufacturing can also be used to create bridge tooling or, depending on the application, production-quality parts. With bridge production, you can scale up from making a few prototypes to making a higher volume of production-quality parts.
3DP can reduce manufacturing costs by reducing assembly part counts, while supporting designs unachievable through other methods. However, 3DP materials have different end-use properties than the same materials used in other manufacturing processes. These other processes also have their own design rules, and you may need to make design changes before switching from 3DP.
CNC Machining
CNC machining creates parts with tight tolerances and complex geometries. Plus, you can use the same materials for both prototyping and production. That’s important if you need prototypes that provide the same strength, mechanical stability, tolerances, and other characteristics as you expect from production parts. Like 3D printing, CNC machining is also used to produce tooling for other manufacturing processes.
By creating prototypes that are as close as possible to the end product, CNC machining supports your transition toward bridge production and, eventually, full production. CNC machining can create significant material waste, however, and machinable materials are usually more expensive than their 3DP counterparts. There are also setups and fixtures to pay for.
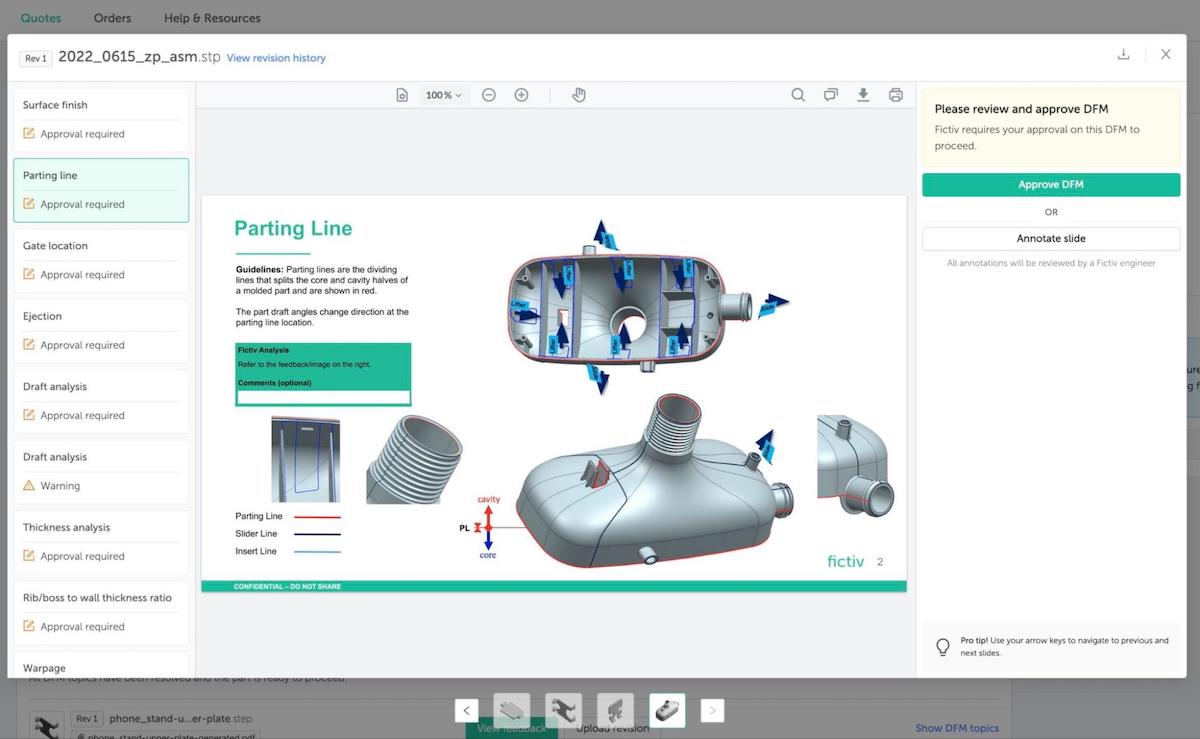
Injection Molding
Injection molding isn’t just for high part volumes, at least when you partner with Fictiv. For low-volume production, customers often start with a single-cavity tool made of soft or semi-hardened steel. These tools can be fabricated quickly, typically by CNC machining, and initial part samples can be produced in as little as 14 to 25 days. Plus, when you injection mold prototypes, you can use the same material (and design) from prototyping through production.
In our experience, customers who 3D-print their prototypes before ordering an injection mold can reduce their design changes and overall costs. If tooling changes are required, the soft or semi-hardened steel molds that we offer are easier to machine than hardened steel. Still, it’s important to finalize your part design before cutting a more expensive tool for high-volume production.
Urethane Casting
Urethane casting uses even less expensive tooling than injection molding, but there are still ways to reduce costs. Depending on the geometry of the original part, 3D printing the mold pattern can reduce lead times by up to 90% and cut costs by up to 70%. Whether the mold is 3D printed or CNC machined, urethane casting can provide you with the part volumes that you need for bridge production.
There are some disadvantages to urethane casting, however. For example, it’s not as fast as 3D printing and supports only a limited number of materials, namely silicone or urethane. Urethane casting won’t necessarily support the testing of material and performance properties either, but it’s faster than CNC machining and is a cost-effective option for lower volumes of parts.
Bring Products to Market Cost-Effectively
There’s a lot more to consider before deciding upon a manufacturing process, and the choices that you make can mean the difference between bringing a product to market cost-effectively or saddling your project with avoidable expenses. Fictiv can help you from prototype through production and has worked with companies like yours during new product development (NPD) and new product introduction (NPI).
Are you ready to get started? Create a Fictiv account and upload your part drawing today.