Time to read: 8 min
Everyone wants manufacturing to be efficient and cost-effective—but those are outcomes, not strategies. A manufacturing strategy is a structured plan that connects production methods to broader business objectives.
Strategy is abstract by nature. Even the most action-oriented strategy is still a conceptual framework for how an organization intends to compete, grow, and evolve, shaped by an envisioned future. Production is concrete. It happens in real time, in real places, with real assets and constraints. Every strategic decision is ultimately expressed via specific choices: which facility, which country, which equipment, which people.
Without a well-developed strategy, production decisions become reactive and fragmented. With it, those same decisions become coordinated expressions of broader goals—ensuring that operations aren’t just efficient, but strategically aligned to deliver long-term advantage.
Different manufacturing strategies influence key factors such as efficiency, cost management, and scalability. Adopting the right production strategy can lower operational costs while increasing flexibility to meet fluctuating market demands. The wrong approach may lead to inefficiencies that hinder growth or disrupt supply chains.
In this article, we’ll discuss the following, and more:
- What a manufacturing strategy is
- Why manufacturing strategy matters
- Common types of manufacturing strategies
- How to choose the right manufacturing strategy
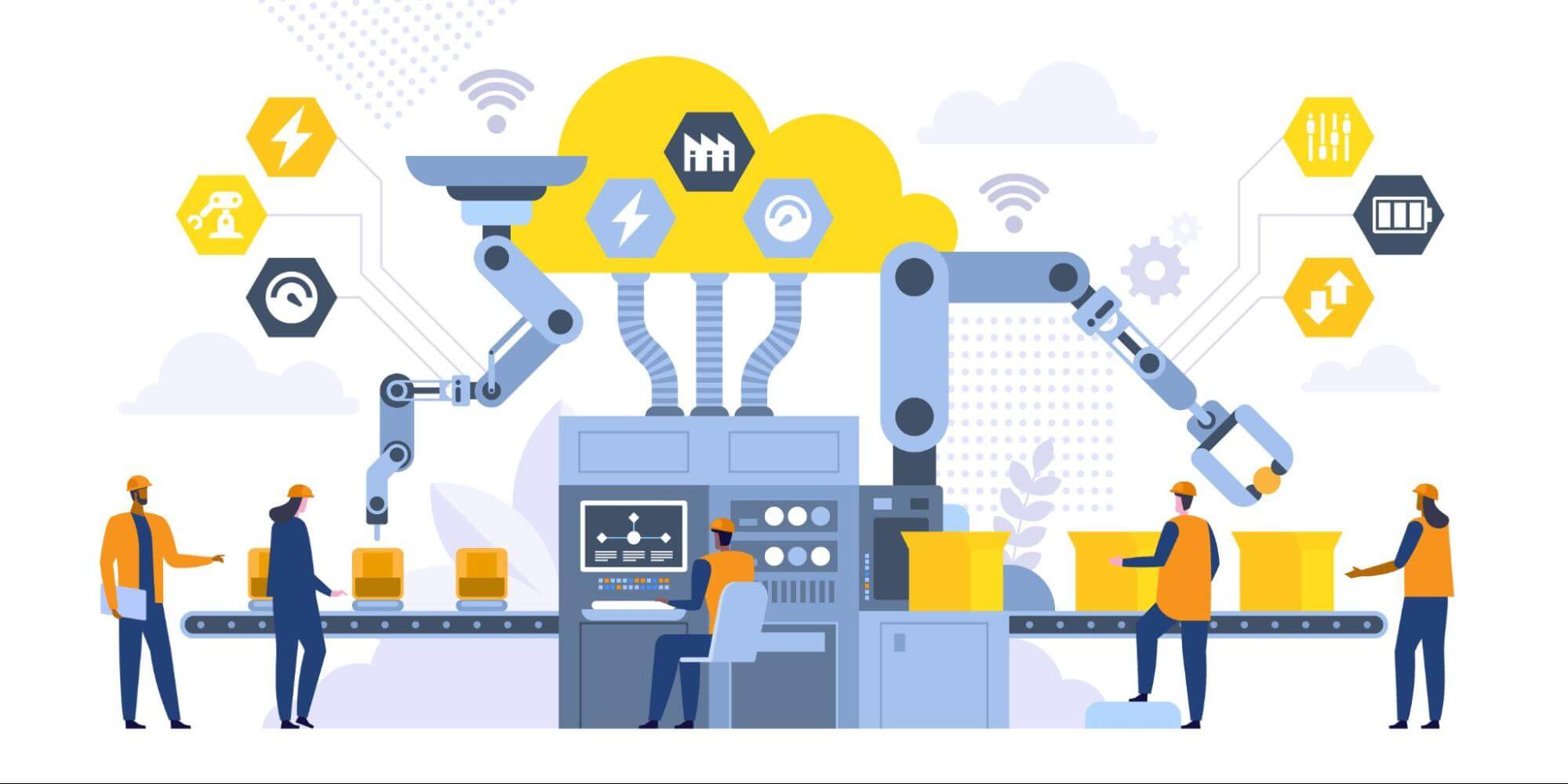
Understanding What Makes an Effective Manufacturing Strategy
A manufacturing strategy is a comprehensive framework that guides organizations in aligning their production processes with broader business objectives for long-term success. It encompasses the adoption of advanced methods, technologies, and resource optimization to enhance efficiency, reduce costs, and deliver high-quality products.
Key priorities include
- Fostering flexibility to adapt to evolving market demands and technological innovations
- Ensuring reliable delivery to meet customer expectations
- Embracing sustainable practices to align with environmental goals
- Supply Chain Integration and Tariff mitigation for the lowest landed cost
By streamlining workflows and minimizing inefficiencies, businesses in competitive industries can enhance their responsiveness and resilience to disruptions and changes in market demand, regulatory environments, and technology. Manufacturing strategies also focus on agility, enabling companies to innovate, stay competitive, and meet the diverse needs of consumers.
This structured approach not only supports operational excellence but also drives strategic growth by striking a balance between stability and adaptability. Ultimately, a well-executed manufacturing strategy builds a solid foundation for a company’s desired manufacturing structure, infrastructure, and set of specific capabilities, integrating real-world supply chain resources with corporate goals like profitability, customer satisfaction, and securing a long-term competitive advantage in a global market.
Strategic Alignment With Business Goals
Manufacturing strategies are integral to achieving a company’s broader vision, ensuring that production efforts align seamlessly with organizational objectives.
For instance, a business striving to dominate its market segment through low-cost offerings would focus its manufacturing strategy on reducing expenses, utilizing lean principles, enhancing supply chain efficiency, or investing in automation technologies. Conversely, a company emphasizing innovation might prioritize cutting-edge research, advanced machinery, and specialized expertise to create groundbreaking products that meet evolving demands.
This alignment goes beyond operational tasks to connect production capabilities with strategic priorities. By tailoring manufacturing strategies to specific goals—such as innovation leadership, cost efficiency, speed to market, customization, etc.—organizations can foster greater cohesion, adaptability, and resilience, enabling sustainable growth while effectively meeting competitive pressures.
The Role of Digital Transformation
Digital transformation is fundamentally changing manufacturing strategies, embedding advanced technologies such as IoT, AI, and data analytics into every stage of production. These innovations empower manufacturers to make informed decisions, improving efficiency and minimizing risks.
IoT systems track equipment conditions in real-time, reducing unexpected downtimes through predictive actions. AI-driven analytics refine supply chain operations by forecasting demand fluctuations and optimizing inventory.
Additionally, digital solutions support smart manufacturing, which focuses on adaptability, personalized production, and environmental responsibility. This transformative approach not only elevates operational performance but also enables businesses to respond swiftly to evolving consumer needs and competitive market pressures.
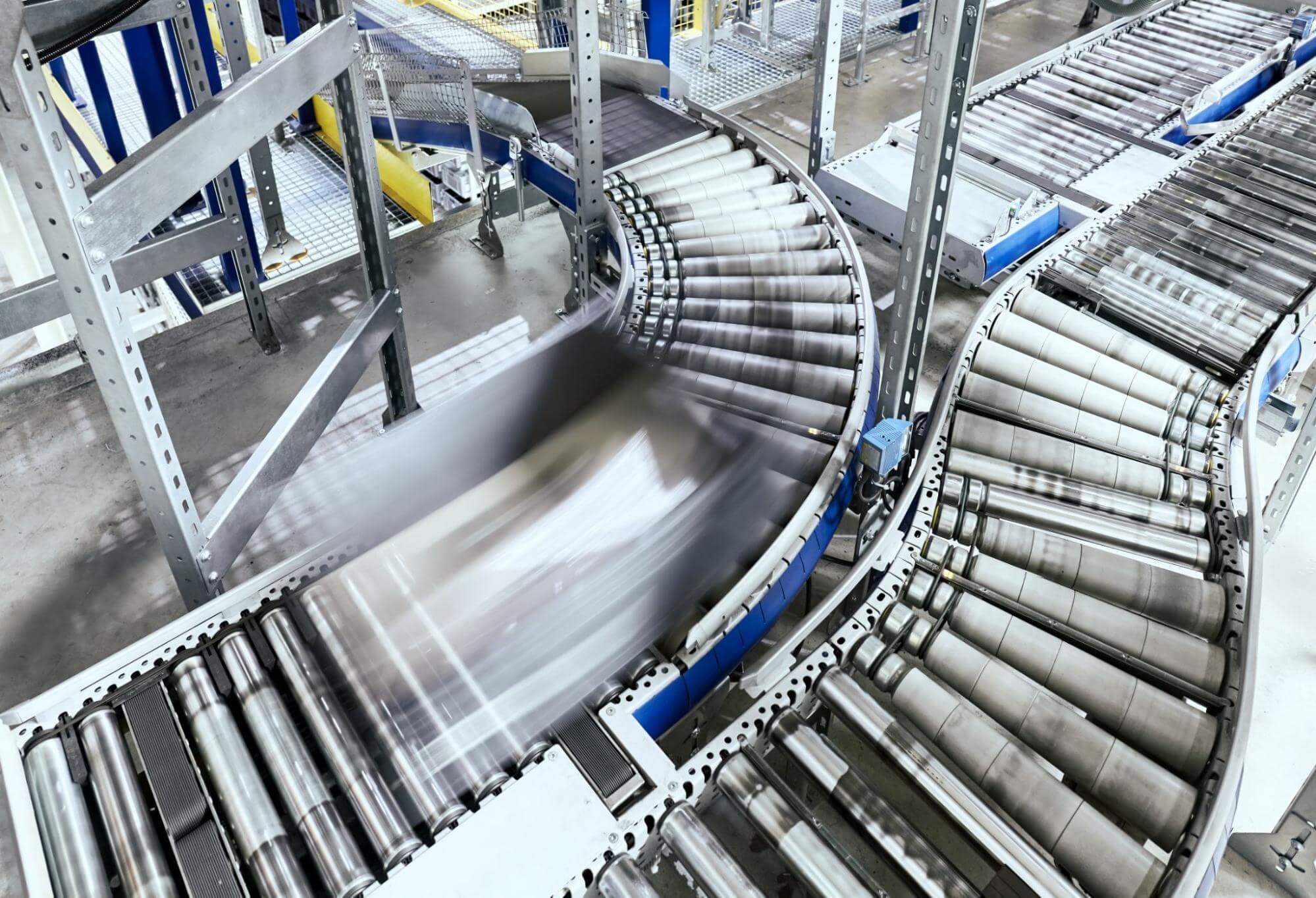
Common Types of Manufacturing Strategies
Manufacturing strategies are crafted to address specific production challenges and market requirements. Below are some widely adopted approaches that businesses employ to enhance efficiency and adaptability.
Make-to-Stock (MTS)
Make-to-Stock strategy focuses on producing goods based on forecasted demand. By anticipating market needs, manufacturers ensure product availability, which minimizes stockouts. However, inaccuracies in demand prediction can lead to overstocking or shortages.
Make-to-Order (MTO)
Make-to-Order strategy means products are manufactured only after customer orders are received. This approach is ideal for customized items, offering flexibility and reducing inventory costs. Despite its advantages, lead times may be longer, requiring careful coordination with customers.
Assemble-to-Order (ATO)
Assemble-to-Order strategy means components are pre-manufactured and then assembled based on specific customer demands. ATO provides a balance between customization and efficiency, allowing businesses to streamline inventory management while meeting unique customer needs promptly.
Level Production Strategy
Level production strategy involves maintaining consistent production levels throughout the year, regardless of fluctuations in demand. While it simplifies scheduling and utilization, it may result in excess inventory during periods of low demand and insufficient stock during peak periods.
Chase Strategy
Chase strategy means production adjusts dynamically to match real-time demand changes. Chase strategy reduces inventory carrying costs and ensures responsiveness, though it may strain workforce and resources during high-demand periods.
These strategies demonstrate how manufacturers can tailor their production methods to suit organizational goals and market dynamics, ensuring competitiveness across diverse industries.
Engineer-to-Order (ETO)
Engineer-to-Order (ETO) is used for highly customized products that require new designs for each order. The production process begins only after customer specifications are finalized, involving significant engineering input before manufacturing. This approach offers maximum customization and supports complex projects but extends lead times and requires close cross-functional coordination.
Batch Production (Job Shop)
Batch production focuses on creating small groups of products in non-continuous runs. This strategy is ideal for high-mix, low-volume manufacturing (HMLV) and supports frequent product changes and customization. It offers flexibility and efficient resource use, but can result in longer production times and higher handling costs than continuous processes.
Continuous Flow Production
Continuous flow production maintains a steady, uninterrupted manufacturing process, making it ideal for standardized, high-volume goods like food, chemicals, or consumer products. It ensures high efficiency and low per-unit cost but lacks flexibility and requires significant upfront investment and predictable demand.
Hybrid Manufacturing Strategy
Hybrid strategies combine multiple approaches—such as Make-to-Stock for components and Assemble-to-Order for final products—to balance efficiency, responsiveness, and customization. Enabled by digital tools and planning systems, hybrid models are increasingly common in complex or global operations but demand careful coordination and real-time visibility.
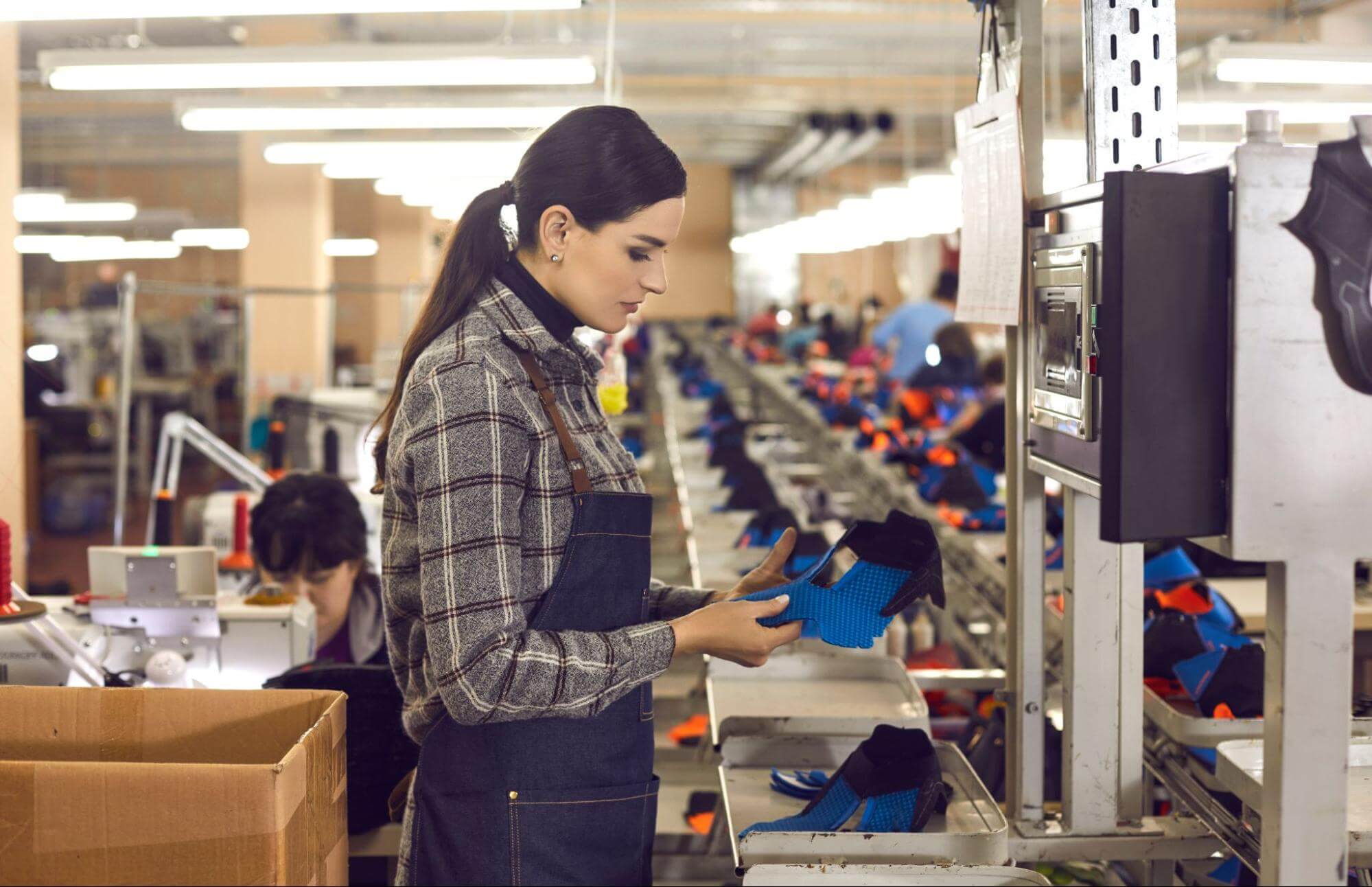
Choosing the Right Manufacturing Strategy
Selecting the right manufacturing strategy requires assessing key factors that impact efficiency and business success:
Market Demand
Customer demand patterns influence strategy choice. For stable demand, Make-to-Stock (MTS) ensures availability and fast delivery. In contrast, fluctuating demand may require Make-to-Order (MTO) or Agile approaches, allowing flexibility and reducing overproduction. Matching strategy to demand boosts responsiveness and competitiveness.
Lead Times
Fast delivery is crucial for customer satisfaction. Assemble-to-Order (ATO) offers a middle ground—stocking components and assembling products when ordered—balancing speed and customization. MTO extends lead times but supports tailored solutions. Strategy selection depends on how time-sensitive the market is.
Cost Considerations
Each strategy affects cost differently. MTS can increase holding costs, while MTO reduces inventory but may require complex systems. Often paired with MTS, lean manufacturing cuts waste and lowers operational costs. The chosen strategy should align with business goals for profitability and scalability.
Technology and Automation
Automation enhances all strategies by improving speed, accuracy, and efficiency. Tools like Just-in-Time (JIT) and smart inventory systems support lean operations and responsive production.
Understanding frameworks like Lean, Agile, and Mass Customization helps clarify strategic choices:
- Lean: Focuses on reducing waste and maximizing value, often aligning with MTS.
- Agile: Emphasizes flexibility and fast response, suiting MTO.
- Mass Customization: Combines efficiency with personalization, as seen in ATO.
Examples:
- Toyota uses MTS with lean methods like JIT to meet predictable demand efficiently.
- John Deere applies MTO to build customized equipment after orders, cutting inventory costs.
- Dell follows ATO by stocking components and assembling on demand, ensuring fast, tailored delivery.
Each strategy reflects how businesses balance cost, speed, and adaptability to meet customer needs.
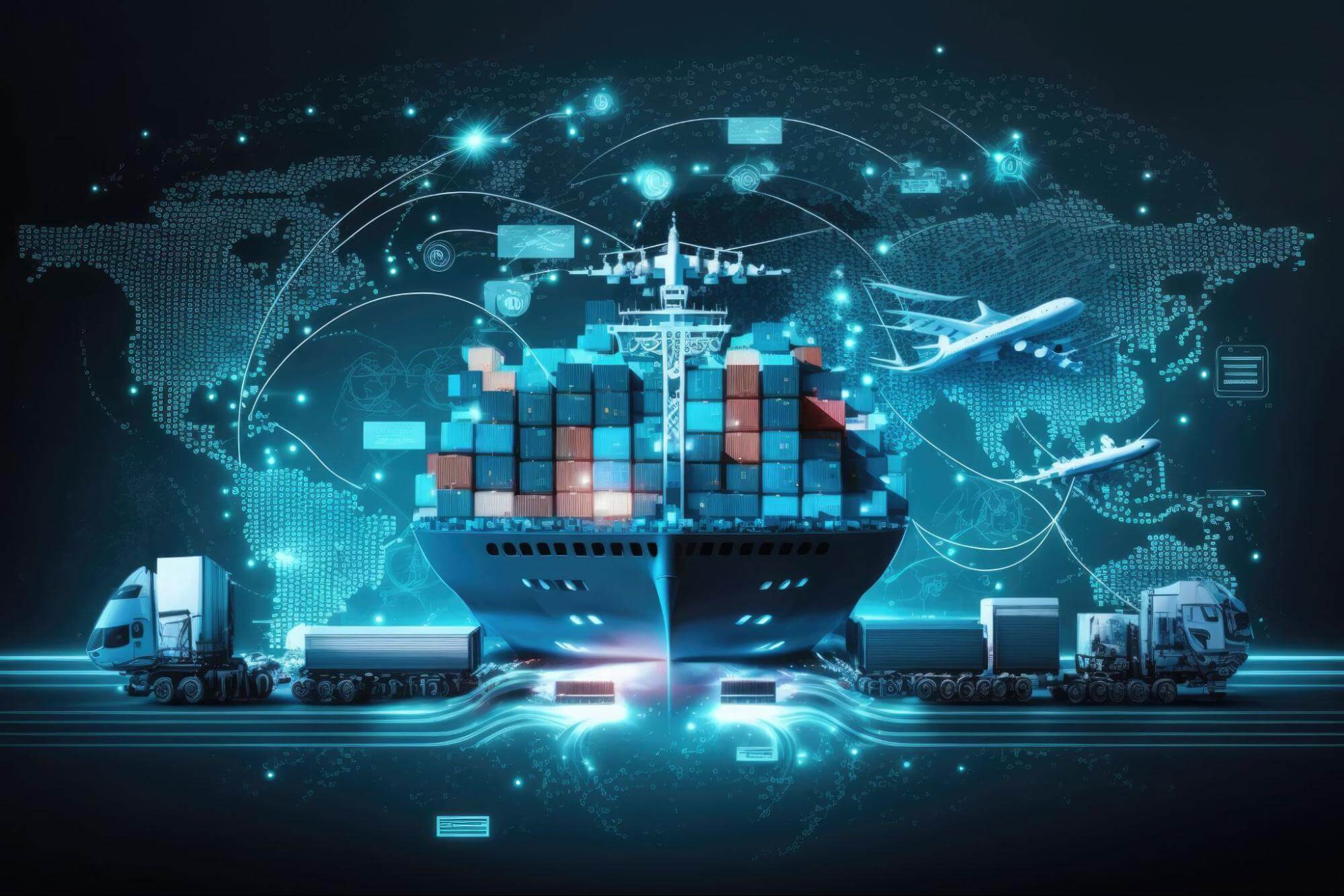
Tariff Mitigation and Global Sourcing Strategy
Modern manufacturing strategies increasingly incorporate tariff mitigation as a core objective. Geopolitical instability, trade disputes, and shifting regional costs have made sourcing decisions critical to financial performance.
Key considerations include:
Landed Cost Optimization
Landed cost includes not just raw materials and labor, but also duties, tariffs, shipping, and taxes. Strategic sourcing—from countries with favorable trade agreements or local incentives—can dramatically lower total costs.
Onshoring and Nearshoring
- Onshoring brings production within domestic borders, often reducing transportation costs and lead times.
- Nearshoring (e.g., U.S. companies shifting manufacturing from Asia to Mexico) balances cost with proximity and resilience. Both approaches also enhance agility and reduce supply chain risks.
Free Trade Zones and Duty Deferral
Utilizing free trade zones or bonded warehouses can help defer or avoid tariffs on imported goods that are re-exported, creating opportunities for savings in global logistics.
By integrating tariff mitigation into their strategy, manufacturers can improve cost competitiveness and build more robust supply chains.
Best Practices for Implementing an Effective Manufacturing Strategy
To create a robust manufacturing strategy, organizations must adopt practices that drive operational excellence while addressing industry-specific challenges.
Essential practices to consider:
Conducting a Manufacturing Process Audit
A detailed manufacturing process audit is instrumental in identifying inefficiencies, waste, and bottlenecks within production workflows. This involves assessing equipment usage, evaluating material flows, and pinpointing areas where delays or excess costs arise. Through this examination, organizations can uncover opportunities for enhancement, such as adopting advanced technologies or reconfiguring workflows to streamline production and reduce wastage.
Balancing Cost, Speed, and Customization
A successful manufacturing strategy requires carefully balancing cost-effectiveness, production speed, and customization. Priorities should be determined based on market demands and customer expectations. For instance, adopting strategies like Assemble-to-Order (ATO) enables rapid response to personalization needs while keeping inventories lean. Striking the right balance prevents over-commitment to one factor at the expense of others, allowing organizations to deliver value while maintaining profitability and flexibility.
Integrating Cross-Functional Collaboration Early
An often-overlooked best practice is ensuring early and consistent collaboration across engineering, design, operations, supply chain, and quality teams. Too often, manufacturing considerations are introduced late in product development, resulting in costly redesigns, inefficiencies, or missed timelines.
Embedding manufacturing input from the outset—such as during design for manufacturability (DFM) and DFX reviews—helps identify production constraints, standardize components, and optimize materials and processes. This cross-functional alignment leads to smoother new product introductions (NPIs), faster time to market, and more scalable production systems.
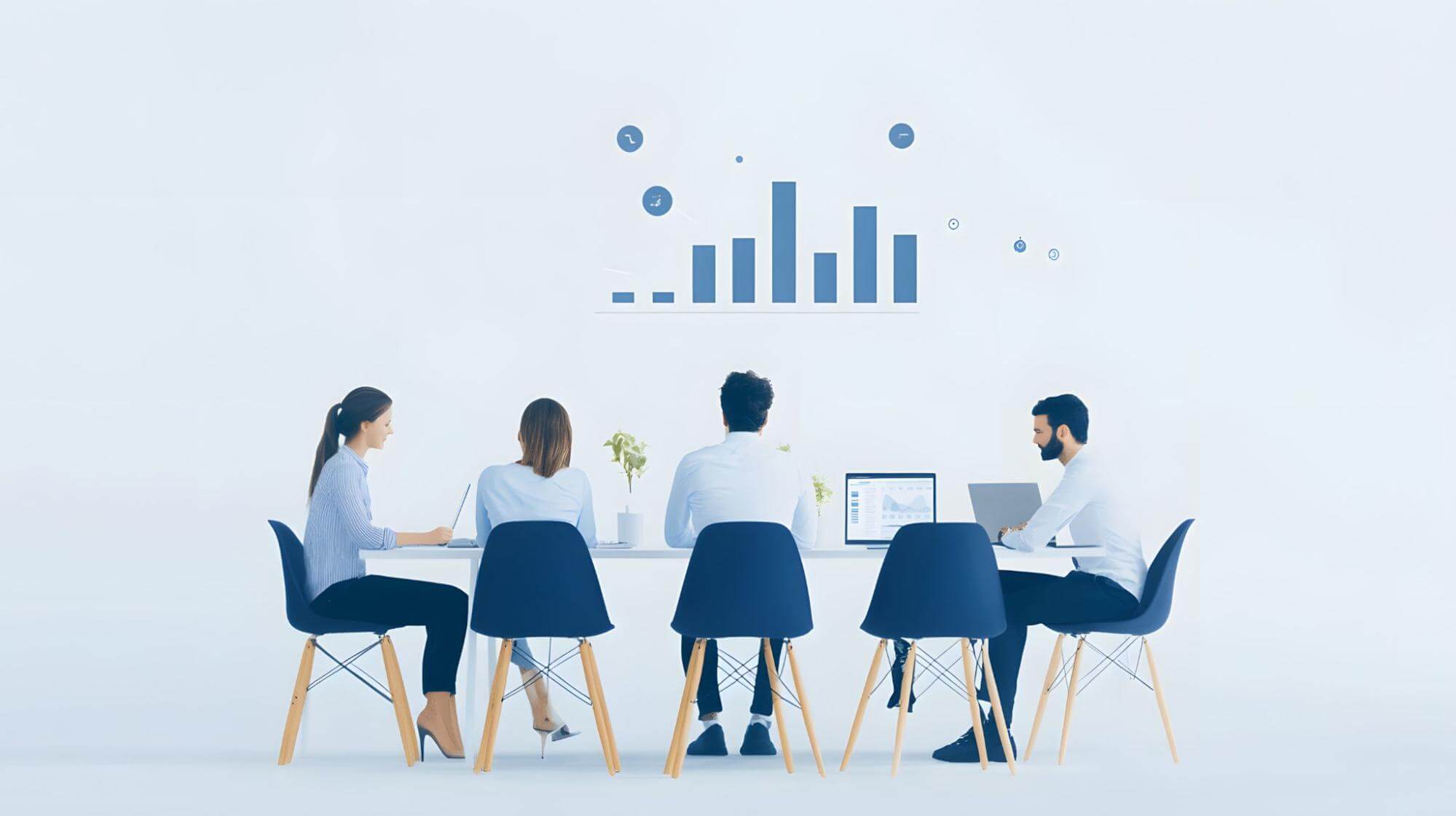
These best practices serve as a foundation for implementing effective manufacturing strategies. Conducting audits helps identify critical improvement areas, balancing key factors ensures strategic alignment, and leveraging lean-agile methodologies creates adaptability and continuous progress. Together, they position organizations to excel in production efficiency while responding proactively to evolving market challenges.
Digital and Emerging Manufacturing Strategies
Digital transformation and evolving global priorities are redefining manufacturing strategy. Technologies like artificial intelligence (AI), the Internet of Things (IoT), and cloud-based platforms are no longer optional—they’re foundational to modern, competitive production systems.
Digital manufacturing enhances agility and operational efficiency. AI analyzes vast datasets to optimize workflows, forecast demand, and enable predictive maintenance. IoT sensors provide real-time visibility into equipment performance and material usage, reducing downtime and waste. Cloud platforms centralize data sharing and collaboration across distributed teams, while digital twins allow simulation of production scenarios without disruption.
Future-ready strategies emphasize flexibility, speed, and sustainability. On-demand production reduces inventory and increases responsiveness to customer needs. Distributed manufacturing leverages regional facilities to cut lead times and mitigate risk. New trends such as high-mix, low-volume (HMLV) production, autonomous systems, and blockchain for supply chain transparency are gaining traction.
Sustainability is also central, with companies adopting circular manufacturing models and renewable energy solutions to meet environmental targets.
As the manufacturing landscape evolves, integrating digital tools and adaptive strategies will be key to achieving long-term resilience, innovation, and growth.
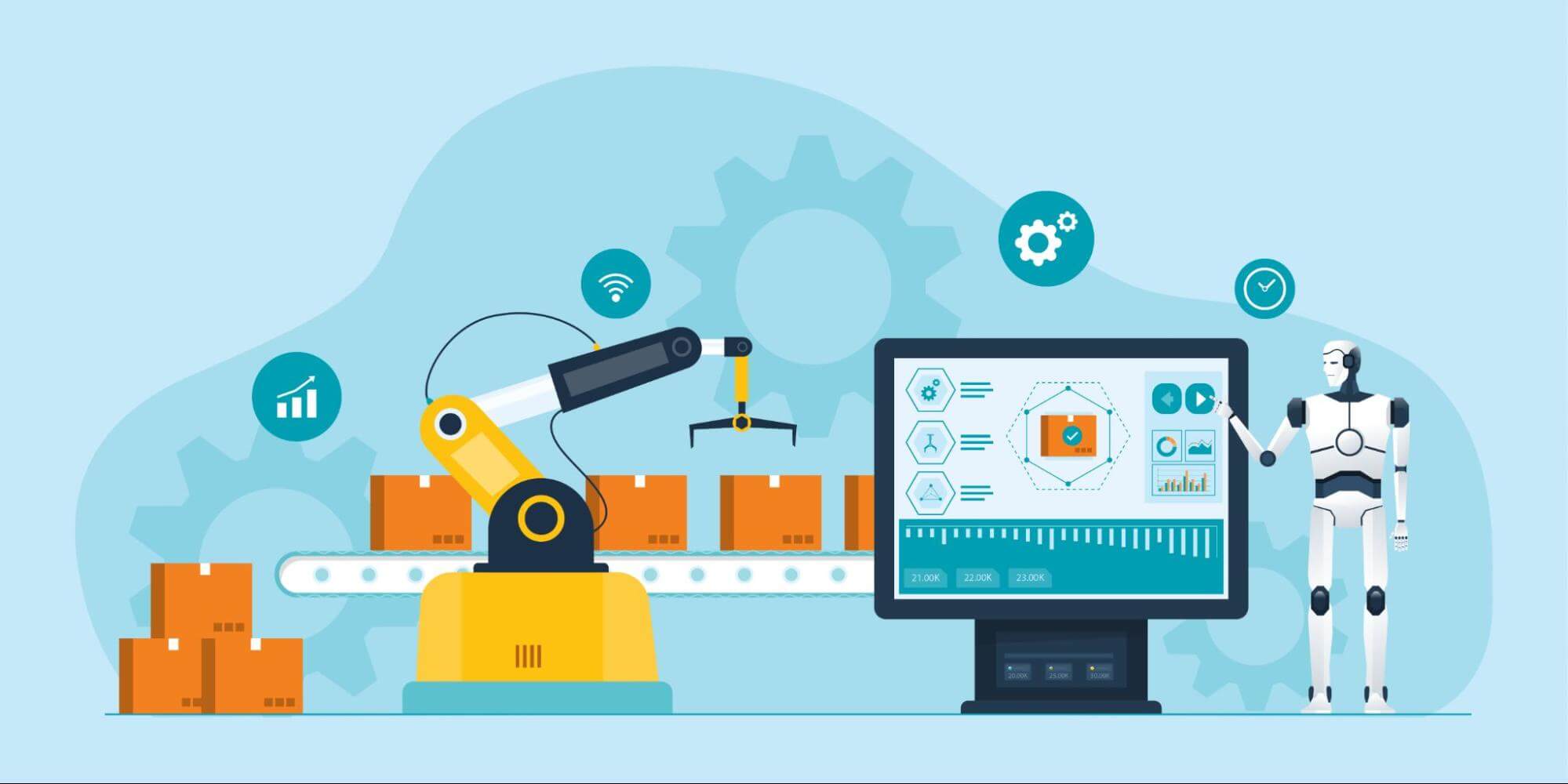
Optimizing Manufacturing Strategy in the Digital Age
Manufacturing strategies are vital for ensuring operational efficiency, competitiveness, and alignment with overall business goals. From cost reduction and quality enhancement to flexibility and sustainability, these strategies provide a framework for businesses to excel. Digital transformation has emerged as a game changer, revolutionizing production processes through technologies such as IoT, AI, and real-time data analytics.
To thrive in this environment, companies must continuously assess and optimize their manufacturing processes. Regular evaluation ensures that operations remain robust and resilient, allowing them to meet evolving demands and seize new opportunities.
Looking to Gain a Competitive Edge in Your Manufacturing Strategy?
Scale production, achieve the lowest landed cost, and minimize lead times with Fictiv’s digital manufacturing solutions and Fortune 500-class global supply chain.
Get started with an instant quote today.