Time to read: 6 min
Your manufacturing partner and their location are critical factors to consider when it comes to part production. Many companies that outsource manufacturing or own factories overseas are nearshoring due to several advantages such as reduced lead times, improved communication and cost savings. Nearshore manufacturing is a trending topic in the U.S. due to these benefits and other geopolitical factors, including claims of the incoming U.S. administration.
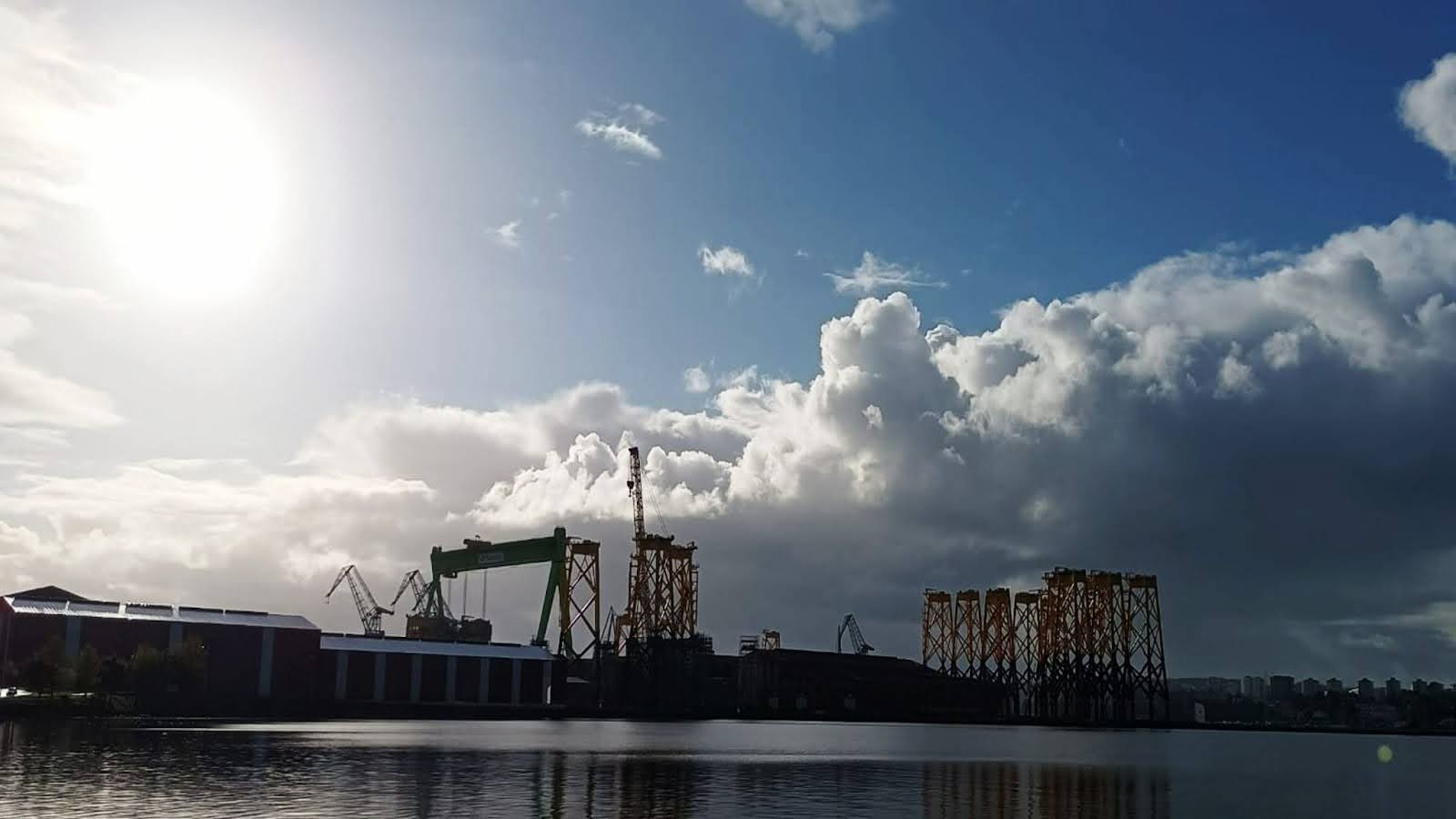
What Is Nearshore Manufacturing?
Nearshoring refers to moving business operations, particularly manufacturing or supply chain operations, to a nearby country or region rather than relying on distant overseas locations. Various industries take advantage of nearshoring, including automotive manufacturing, pharmaceuticals, healthcare, and IT and software development. A common example is when a US-based company partners with a company in a neighboring country to take care of their manufacturing operations.
In some cases, nearshoring can also refer to a company moving its manufacturing operations to a nearby country without it being outsourced. This means that the manufacturing facility of the same company is just situated in a nearby country for the benefit of lower operation costs compared to where the company headquarters are located. They can then hire local talent in that area, often with lower labor costs.
Mexico is currently the leading nearshoring destination for companies based in the US, thanks to its strong industrial base and favorable trade agreements. These advantages can lead to lower landed costs, which refer to the overall expenses involved in getting products to their final destination. As a result, Mexico is an excellent alternative to offshore locations like Asia or India. Its proximity also enhances communication, collaboration, and quality control compared to more distant suppliers.
Learn more from this video clip about Fictiv’s nearshoring for injection molding, which offers the ability to ship precision tooling to Mexico, where parts can be produced.
Nearshoring vs. Offshoring, Onshoring, and Reshoring
There are various strategies related to domestic and international manufacturing. These terms may be commonly used in a similar context, but there are some key differences:
Offshoring
Offshoring is when a business moves operations to a third-party company in a distant country, usually to save on labor and operational costs. However, while it may have some cost advantages, it comes with challenges such as long shipping times, logistics, and communication across time zones, all of which can lead to increased costs.
Onshoring
Onshoring is when a company outsources some of its business functions to an independent contractor/company located within the borders of its home country. This is also referred to as domestic manufacturing. The benefits of onshoring are close proximity, easy cultural collaboration, matching time zones, etc. However, it does come with the cons of higher labor and logistics costs.
Reshoring
Reshoring refers to bringing operations that were once taken outside national borders back into the country of origin. This differs from onshoring, where partnerships are formed within the home country from the start. The advantages and disadvantages here overlap with those of onshoring.
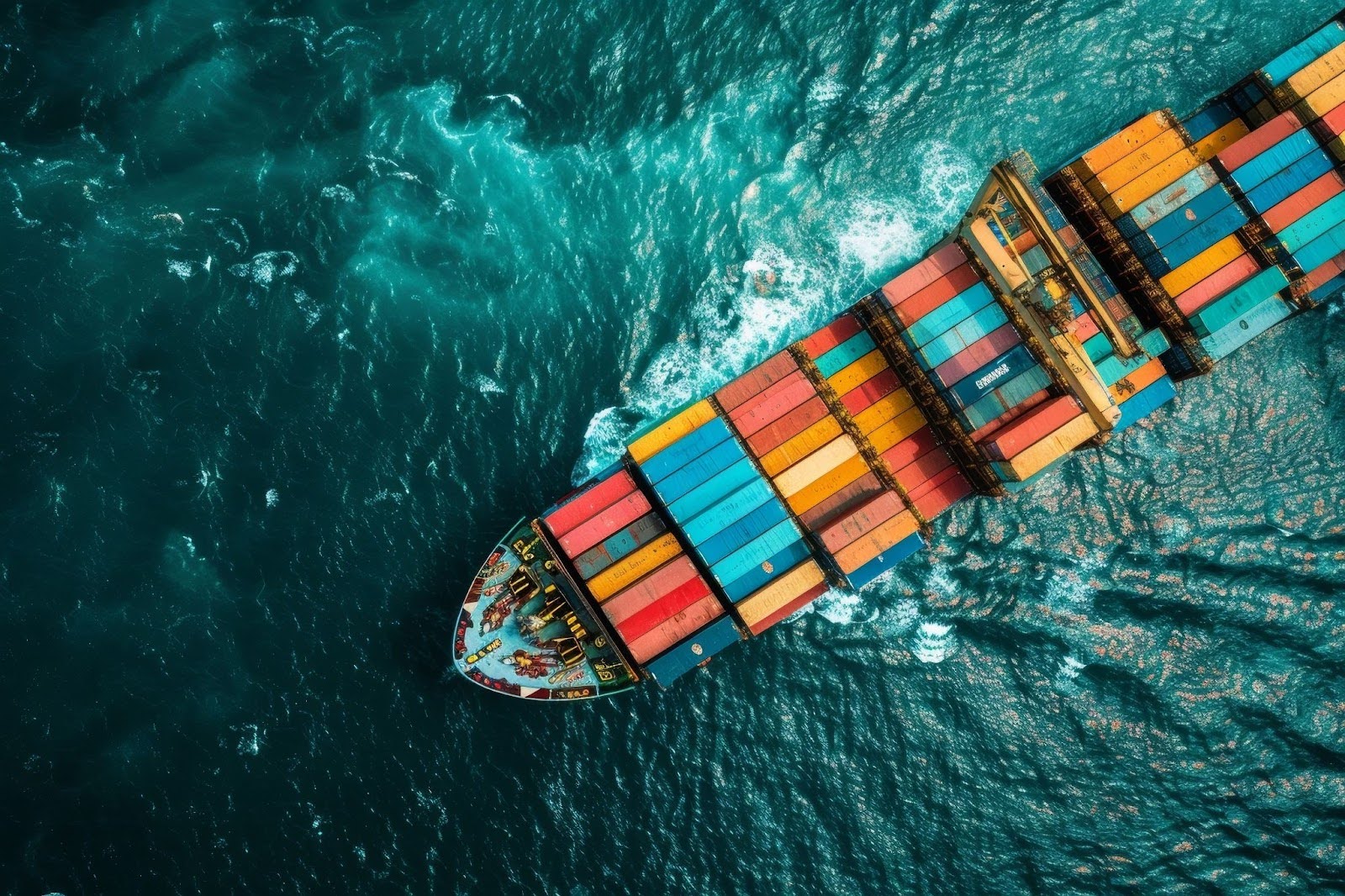
Advantages of Nearshoring Manufacturing
Nearshoring has a specific set of advantages that make it appealing to businesses around the globe, such as:
Cost Savings in Labor, Logistics, and Operations
One of the most significant advantages of nearshoring manufacturing for companies is cost savings. Companies save on investing in human capital with the experience needed to manufacture the products to the correct standards, desired functionality, and visual appeal. Moreover, businesses will save on capital investment in manufacturing facilities and machinery needed to produce the products.
Compared with other outsourcing options, such as offshoring, nearshoring also offers major savings on logistics costs. Instead of managing lengthy shipping routes and tariffs, which is often the case with offshoring, companies benefit from closer proximity to their supplier or factories. This can also reduce unpredictability, which can contribute to additional unexpected costs.
Is your business struggling with unpredictable logistics costs and material shortages? Watch our recorded webinar to explore smarter nearshoring strategies.
Improved Communication and Responsiveness
Neighboring countries often have fewer cultural and linguistic difficulties compared to offshoring locations. They usually have shared business practices and less of a language barrier, which leads to smoother relationships and fewer misunderstandings. Also, working within the same or even a similar time zone has the perk of simplified communication and collaboration.
Another advantage of shared or similar time zones is faster communication and quicker response time between you and your manufacturing partner. There is no delay in terms of time zones, and real-time collaboration is much easier. This adds up to quicker responses to design changes, adjustments in production, and even supply-chain disruptions, which often means quicker time to market compared to offshoring.
Reduced Lead Times and Supply-Chain Risks
Nearshoring helps offset complications like material supply disruptions, trade policy changes, or parts being held up at customs. Companies that go the nearshoring route can ensure faster delivery of parts or products, which allows them to respond quickly to market demands.
It’s also important to recognize the benefits of minimizing the number of locations from which you source and ship to or from. For example, consider if you were to transport raw materials from one country to your manufacturer in another, and then ship the parts from the manufacturer to yet another location for assembly, finishing, testing, or packaging. The costs, lead times, and risks can accumulate due to an inefficient supply chain. Nearshoring is one effective strategy to mitigate supply chain risk. Reducing the number of stops and their distance has additional environmental benefits as well.
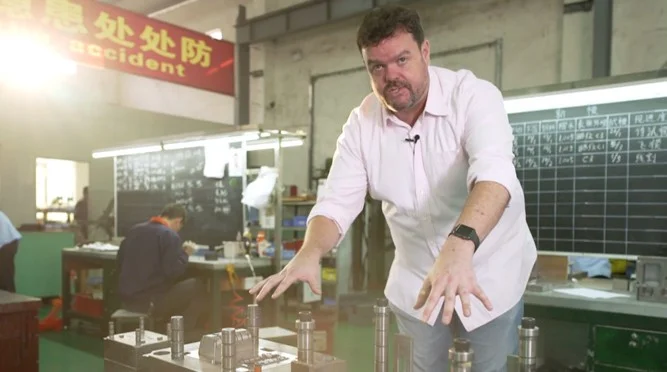
“I’ve seen plastic material made in the US, parts molded in China, and some sub-assembly done in Thailand, with final assembly, testing, and packaging done back in the US. Those costs add up. Also, that proves potentially risky, especially with volatile logistic costs.” – Cameron Moore, Fictiv General Manager, China
Trends Driving Nearshoring
There are many reasons for this emerging nearshoring trend, among which supply-chain disruptions and rising inflation are major contributors. Let’s take a closer look at what drives nearshoring trends:
Post-COVID-19 Supply-Chain Revisions
Many businesses felt the impact of the COVID-19 pandemic, which had significant effects on their supply chains. Due to this global disruption, companies have been searching for ways to shorten their supply chains to reduce future risks and respond quickly to market demands. Many companies are expected to reshore or nearshore their manufacturing operations in the next five years to promote supply-chain resilience.
Geopolitical Considerations
Geopolitics started to have more of an impact on global trade since 2018. Two factors that played a major part in this are trade relations between the US and China, and the Russia-Ukraine war. These tensions have led to a shift toward friend-shoring—prioritizing trade with geopolitically aligned nations—while decreasing trade between rival countries. Trade between geopolitically aligned countries has increased since 2018 compared to the previous five years.
Sustainability and Environmental Factors
Nearshoring is a relatively easy win in terms of improving a company’s sustainability. By reducing the distances that goods need to travel, companies lower their carbon footprint and energy consumption. Additionally, nearshoring often allows businesses to work with suppliers in countries with similar labor standards and environmental regulations, further enhancing their commitment to ethical practices.
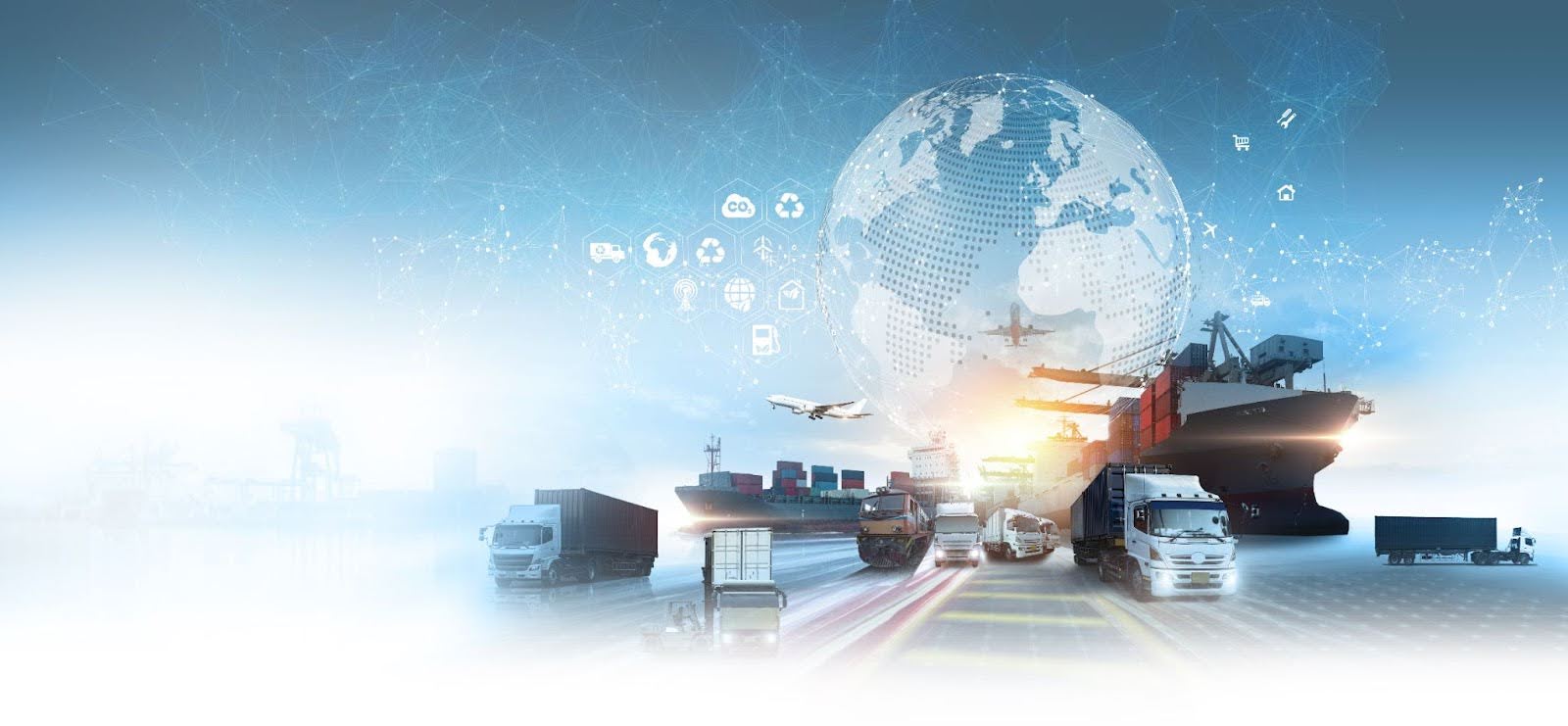
Best Practices for Effective Nearshoring
To make the most of nearshoring opportunities, it’s important to weigh the pros and cons, in careful consideration of the manufacturing source you are partnering with. Here are a few nearshoring best practices:
Conducting Thorough Research
Once you decide to nearshore, the next step is to find your ideal partner. Start with a comprehensive analysis of potential locations and partners. Consider factors like labor costs, infrastructure, trade agreements, and proximity to your target markets. You might also want to consider whether your potential partner’s workflow eases collaboration and whether they have cybersecurity protocols in place (depending on how damaging a data leak would be to your business).
Choosing the Right Nearshoring Partner
When selecting a nearshoring partner, it’s crucial to choose one with a proven track record and verify their reputation by contacting previous clients. Look for partners that align with your company’s values, quality standards, and capacity requirements, as a reliable partner can significantly impact consistent output and market demand fulfillment. Establishing a strong, long-term partnership will streamline processes and improve collaboration, increasing the likelihood of achieving consistent product quality.
Fictiv as Your Manufacturing Partner
Fictiv is a trusted digital supply chain partner for custom mechanical parts and assemblies that scales with you from prototype to production – whether it’s overseas or close to home. Our AI-driven platform delivers superior speed, quality and scale for customer’s manufacturing programs.
If you’re looking to nearshore your injection molding or another manufacturing process, Fictiv has teams on the ground across 4 global regions and offers agile supply chain solutions that are responsive to market disruptions, competitive challenges and economic change. Get in touch with our experts today.