Time to read: 5 min
Many experts consider the helical-thread screw to be one of the most important mechanical inventions in history — helical-thread screws are mechanical fasteners with a cylindrical shaft wrapped in helical threads or grooves cut into the cylinder’s surface. Screws are a critical mechanical assembly method because they convert rotational motion to a linear motion. This linear motion can even be transferred to a nut or other component if assembled at the same time as the screw.
In 2023, there is a seemingly infinite number of screws to choose from, and a walk down the fastener aisle at your favorite hardware store confirms this — it can be overwhelming. Designers usually want to reduce the number of fasteners in an assembly. But the ability to remove, replace, maintain or upgrade these assemblies is vital to many products, so fasteners aren’t going anywhere. — for example, there are over 2.5 MILLION fasteners in a Boeing 747.
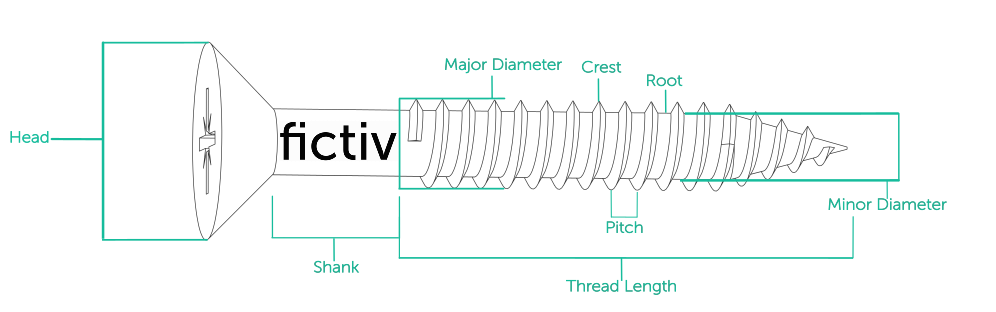
Knowledge of the purpose and working logic behind screw design is important, but it’s likely that your job duties entail designing threaded holes for screws, not the screws themselves. Threaded (or tapped) holes serve as a non-permanent joint and provide a location for fastener installation in mechanical assemblies. Threaded holes are created by tapping a helical groove, or thread, into the surface of an existing hole.
Knowing the ins and outs of threaded holes is crucial to ensuring your mechanical assembly is securely constructed, and this article discusses the various types of threaded holes, the methods used to create them, and important considerations to keep in mind when specifying threading holes in your next mechanical design project.
Pro-Tip: You can learn the difference between tapped and threaded hole terminology in this article.
Types of Threaded Holes
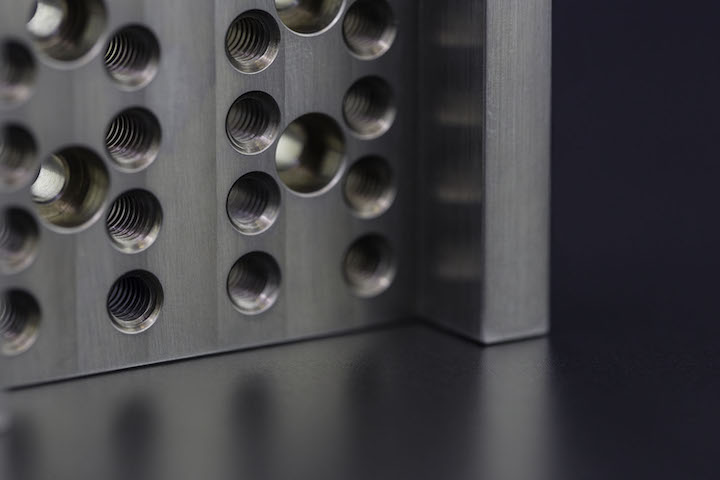
Understanding the different types of threaded holes is the first step in non-permanent joint design for mechanical assemblies. There are several types of threaded holes, each with its own unique characteristics. Here are some of the most common types:
- American National (Unified): These threads have a 60-degree thread angle and rounded or flat crest, making them well-suited for general-purpose applications. This type of thread is approved in the United States and Great Britain.
- UNC (Unified National Course): Coarser thread pitch for general, standard applications.
- UNF (Unified National Fine): Similar to UNC threads, but with a finer thread pitch — often used in precision applications.
- M (Metric): These threads are per the ISO 68 basic (non-rounded) profile, have a 60-degree symmetric thread angle, and are measured in millimeters. Metric threads are commonly used in international applications.
- MJ (Metric): MJ metric thread has a rounded fillet at the root of the external thread and a larger minor diameter for internal/external threads. These geometric features mean that these type of threads are optimal for high fatigue strength applications.
- Acme: These threads have a 29-degree angle, straight edged peaks and valleys (trapezoidal threads), and are designed for use in heavy-duty applications, where power is to be transmitted. They are typically used in power transmission applications, such as lead screws for machine tools. This type of thread is often modified by cutting the space between the teeth so they have a 10-15 degree included thread angle. This makes machining the threads easier but can limit the practical efficiency of the threads.
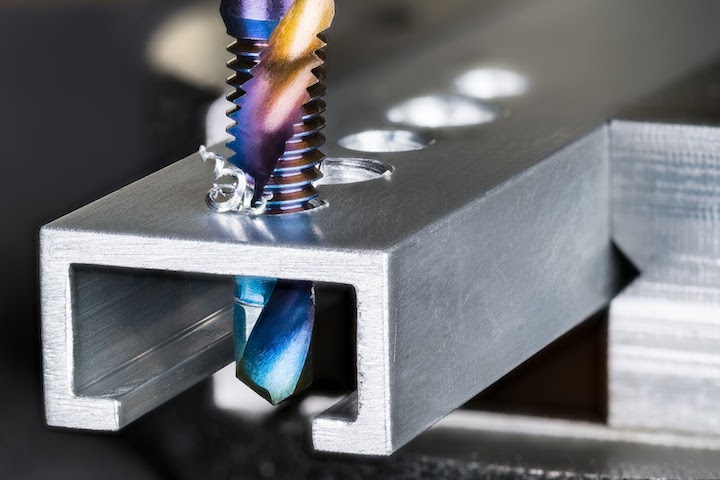
Methods for Manufacturing Threaded Holes
As with the production of many common geometric part features, there are a variety of methods used to create the internal threads in threaded holes, including cutting, rolling, and forming. Threaded holes are typically drilled then tapped with a thread tap. The optimal method depends upon:
- Your material
- Accessibility of the location where the threads are to be cut
- Budget
- Type of thread specified
Here’s what you need to know about the most common methods for internal thread formation in a hole:
Cutting
This method involves using a cutting tool, such as a tap or die, to cut threads into a hole. This method is most commonly used for creating threads in small or irregularly shaped holes. Generally, the drilled hole diameter should be equal to the minor diameter of the fastener you will install in the tapped hole. A cutting tool, or cutting tap, works by ejecting removed chips out of the hole along the tap’s flute as it cuts threads. Chip production in a blind hole may cause jamming during assembly.
Rolling
Rolling uses a rolling tool, such as a thread rolling die, to press threads into a hole. The roll forming method (aka forming method or form tapping) is often used for creating threads in large or regular holes and is considered to be more efficient and cost-effective than cutting. When forming, the drilled hole diameter should be bigger than the minor diameter of the fastener you will install in the tapped hole.
A rolling tool, or rollng tap, works without chip formation because it forms threads via deformation instead of material removal. Roll taps are typically stronger than cutting taps because of their rigid design, so they typically have a longer tool life as well. However, roll taps are not suitable for harder materials (like cast iron) or brittle materials (like plastics).
Tips for Threaded Hole Callouts
Here are a few important things to remember when specifying threads:
- Specify threads on a 2D drawing with a thread specification callout (aka thread hole callout)
- For metric sizes, specify size with the thread pitch (diameter X pitch in mm); i.e. M12 X 1.75 has a 12 mm major diameter and a 1.75 mm pitch
- For unified sizes, specify size with the number of threads per inch (nominal diameter, number of threads/inch, thread series; i.e. ⅝ in – 18 UNRF has a 0.625 in nominal diameter, 18 threads/inch and is a UNRF thread series type.)
- Always specify a thread standard when defining a thread type on a drawing or bill of materials for threaded holes and threaded fasteners.
- Consider material selection when specifying a fastener or hole material for a mechanical assembly. Remember that you want to avoid galvanic corrosion, so be mindful of dissimilar metals that make contact with each other in an assembly.
- Remember that smooth versus coarse threads have different benefits and should be selected depending on the application. Smooth threads are more beneficial for precision applications whereas coarse threads can be considered to be more general-purpose.
- Bolt holes should be deburred to break sharp edges. Sharp edges can increase the stress concentration on the fastener and lead to premature failure.
- If you are threading a blind hole, consider using a forming tap so that chips don’t get trapped in the bottom of the hole. But, there is a tradeoff because the drilled hole (prior to tapping) must be held to a tighter tolerance (<5% deviation from the pitch) for a forming tap to properly work.
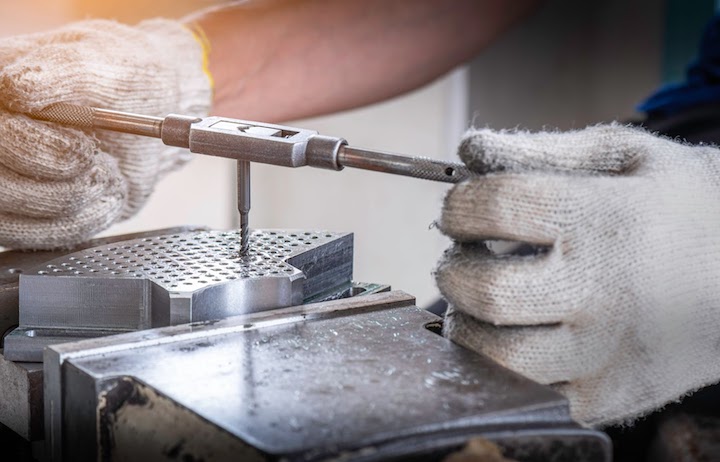
Pro-Tip: If you need additional guidance to determine the right tolerances for your mechanical design, check out our free Tolerance Stack Up Analysis Tool.
Custom Parts, Fast–Start Your Next Project With Fictiv
For all your CNC machining service and finishing needs, Fictiv has you covered. We’re experts at producing custom CNC machined tight tolerance parts, in a variety of materials, and we simplify custom part sourcing with intelligent, streamlined, automated workflows. Fictiv is your operating system for custom manufacturing that makes part procurement faster, easier, and more efficient.
Create an account and upload your part to see what our instant quote process, design for manufacturability feedback, and intelligent platform can do for you.