Time to read: 5 min
When designing mechanical assemblies, it’s likely that they’ll require fasteners for assembly. Fasteners like screws and bolts are commonly used to secure mating components, and they usually require some type of hole for assembly. There are many types of holes to use to install fasteners such as countersunk, counterbore, tapped, tapered, spot faced, and screw clearance.
Now, let’s look at the definition of tapping vs threading, decode the proper use of the terms, and find out which is the correct terminology: threaded holes vs tapped holes.
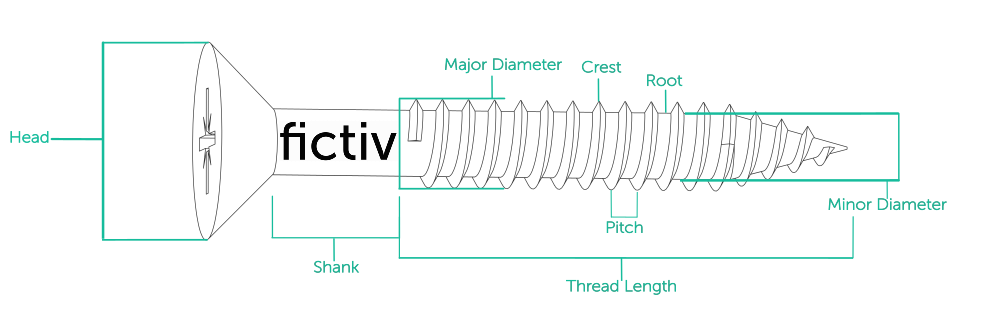
What is Tapping?
Tapping is the process of creating threads inside of a hole for the installation of a screw or bolt — so a tapped hole is just a hole that is internally threaded. The tapping process starts with drilling a hole that is typically slightly smaller in diameter than the major diameter of the threaded fastener you will use. Here’s the equation for determining the size of the tap to use for ANSI threads:
The next largest drill size beyond the calculated diameter should be chosen to tap the hole. So, if you calculate a drill diameter of 0.720”, you choose the next largest tap diameter of 0.750”.
After the hole is drilled, you form the threads on the inside diameter of the hole using a tap. Taps look similar to drill bits, and there are a few different types of taps: hand taps, power taps, tapered taps, extension taps, and exotic taps. All taps are marked with a standard designation that includes the following information:
Nominal Size (Threads/Inch) | Thread Form Designation |
Material Tap is Constructed From | Tolerance for Pitch Diameter |
The nominal size is the thread concentration, while the thread form designation identifies the thread family the threads belong to (i.e. ACME, UNC, UNF, UNJ, UNS). The material tap is constructed from is typically a tough material like carbide, and the pitch diameter tolerance gives an alpha-numerical code that designates the tolerance for the thread.
Here are some tips for defining a tapped hole and determining which type of tap to use:
- Hand taps do not typically offer the precision or ease that CNC taps do. Choose CNC tapping over hand tapping when possible.
- For blind holes, a bottoming tap is ideal, but you may want to start with a taper tap and then move to a bottoming tap to get better thread definition. (Side note: a bottoming taper is unique because it threads almost all the way down, which results in only 1-2 threads tapered at the bottom. This is useful for blind holes because you get better thread engagement.)
- Avoid using spiral point taps when CNC machining blind tapped holes, as the chips tend to get pushed down and remain in the blind hole. If the chips are not cleaned out well enough, they can cause issues with assembly. Opt for spiral flute taps or interrupted thread taps for blind holes.
- Thread forming taps, where chipless compression tapping occurs, provide greater thread strength and a longer thread lifespan due to decreased potential of thread breakage. Thread forming taps also require a larger tap drill diameter, so see Machinery’s Handbook for further details and calculations.
- You may have seen the term ‘clearance hole’ used as a common type of threaded or tapped hole. However, most clearance holes are not tapped — they are intended for installation of a nut on the free end to clamp the materials together. A clearance hole is too small for the head of the fastener to fit through, but large enough for the threaded portion of the fastener to fit and engage with the internal threads.
What is Threading?
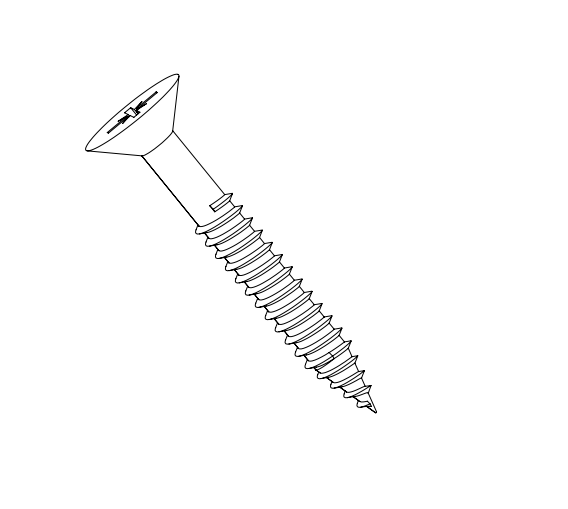
While tapping is the process of creating internal threads within a hole, threading is the process of creating external threads on the cylindrical body of a screw, bolt or other part to be assembled (like pipes). When referring to an installation location for a threaded fastener, you may use the term threaded hole or tapped hole but remember that a fastener is threaded, not tapped.
Threading on a screw or bolt begins at the point of engagement of the fastener and continues through the body to the shank, or unthreaded portion, of the fastener. See the image at the beginning of this article for a more detailed refresher on threaded fastener terminology.
Threaded fasteners have been around for decades and provide a novel method of force transformation to secure two or more components together in an assembly. Screws, in particular, have been the subject of many mathematical and geometric studies in the past because they act as simple machines that transfer rotational forces, or torque, into a simple linear force. One way to understand this is using the concept of the Archimedes screw — where a rising level of water turns a turbine connected to an electrical generator to generate power from a water source (the Archimedes screw acts as a power displacement pump).
Pro-Tip: If you’re tasked with designing a threaded fastener from scratch, advocate for an off-the-shelf solution instead. Otherwise, use threading calculations and fastener calculations to help with your design.
Takeaways
- A tapped hole is simply a threaded hole, and tapping is the process of creating internal threads within the internal sides of a hole.
- The difference between a threaded hole and a tapped hole: tapped holes are just another term for a threaded holes, and a tap is used to create threads in the hole.
- A drilled hole is just the result of removal of a cylindrical volume of material, with smooth internal walls. A tapped hole is a cylindrical hole with internal threads.
For all your custom CNC part manufacturing needs, Fictiv has you covered. We’re experts at machining any size of tapped holes in a variety of materials, and we simplify custom part sourcing with intelligent, streamlined, automated workflows. Fictiv is your operating system for custom manufacturing that makes part procurement faster, easier, and more efficient.
In other words, Fictiv lets engineers, like you, engineer.
Create an account and upload your part to see what our instant quote process, design for manufacturability feedback, and intelligent platform can do for you. Our CNC machining service can create your parts in as little as 2 days!