Time to read: 6 min
In designing and machining, holes are central when constructing and utilizing different parts. Holes fill explicit needs, from enclosures to attaching sensors or pathways to liquids. Among the various sorts of holes, an important classification is blind holes. This article explains blind holes, investigating their definition, importance in designing and machining, and applications across various industries.
Definition and Purpose of Holes in Engineering
Holes, in design terms, are voids deliberately made in materials to satisfy explicit goals. They serve different capabilities, like reducing weight, assembling parts, or allowing the flow of liquids and gasses. Understanding the purpose of holes is fundamental for designing parts that meet primary, practical, and aesthetic requirements.
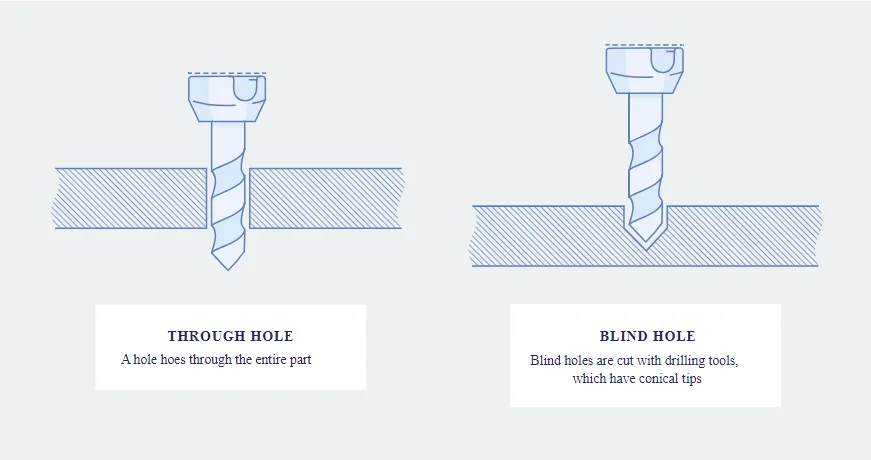
Overview of Different Hole Types
Different hole types exist, each with their own qualities and applications. Two essential classifications are blind holes and through holes. While through holes go completely through the part, blind holes are bored or machined to a particular depth, not completely exiting the material. Blind holes are decisively utilized in circumstances where a through hole is unrealistic or where a part requires inward highlights without undermining its outer appearance or construction.

Other standard hole designations we will not touch on in this article are ream, countersink, counterbore, and spotface holes.
Focus on Blind Holes and Their Relevance in Machining
Machining blind holes that have limited depth has advantages and disadvantages. This article explores the specifics of blind holes and their importance in enhancing primary reliability, reducing material waste, and providing designers and mechanics with versatile options in part creation. It is crucial to understand the significance of blind holes in machining processes to advance designs and ensure effective manufacturing practices.
Types of Holes in Machining:
To understand blind holes completely, it’s crucial to recognize different hole types and their roles in machining processes.
Blind Holes Versus Through Holes: Blind holes do not go through a part, whereas through holes do. Understanding the differences between blind and through-holes is critical for making informed choices in the design and machining stages.
Role of Hole Types in Component Functionality: Holes, regardless of their location, influence the usefulness of parts. Through holes might be preferred for specific applications, such as giving consistent pathways to bolts or upgrading ventilation. Then again, blind holes offer benefits like expanded strength and protection against environmental conditions. Analyzing how hole types add to general part usefulness helps engineers make optimal design choices.
Considerations for Machining Different Hole Configurations: Machining processes change given the sort of hole created. There are several considerations and difficulties related to machining blind holes. Factors like tooling choice, machining time, and accuracy prerequisites are critical.
Engineering Applications of Blind Holes
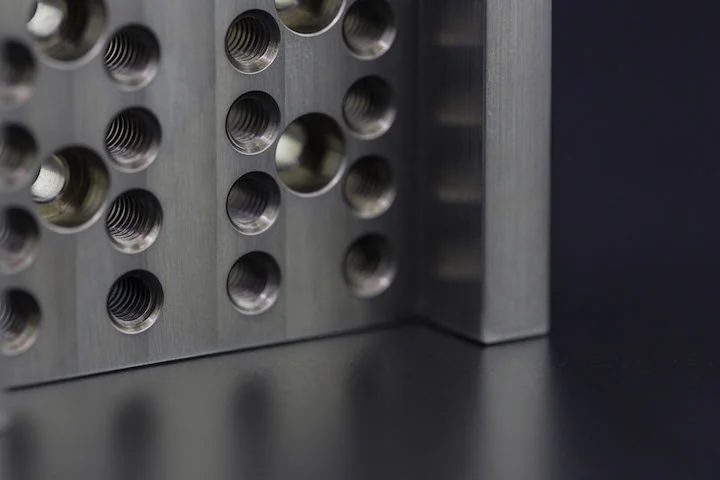
Purpose and Functionality
Blind holes are utilized for a broad range of applications across different industries because of their unique advantages. One primary role is to improve the robustness of parts. By decisively setting blind holes, engineers can provide the structure for improved strength without compromising on general weight. Furthermore, blind holes are useful for applications like container clasps and dowel pin press fits, or fixed chambers for delicate parts.
Common Industries and Use Cases
There are many use cases where blind holes are widely utilized, including:
- Aviation: Blind holes are utilized to lessen general weight without compromising the primary strength of airplane parts.
- Auto: Motor blocks and transmission parts frequently consolidate blind holes for integrated attachments and to decrease material use.
- Electronics: Circuit sheets might include blind holes to house connectors or mount parts safely.
- Clinical Gadgets: Blind holes help establish clean and fixed conditions for sensitive clinical instruments.
Understanding the applications of blind holes is crucial for specialists, creators, and mechanics engaged in various areas.
Machining Processes for Blind Holes
- Drilling and Boring Techniques: Making blind holes includes penetrating and drilling methods. Conventional penetrating might be appropriate for straightforward blind holes, while additional complicated calculations might require progressive strategies, for example, weapon boring or trepanning. Drilling processes, including line and back drilling, accomplish exact aspects and smooth completions in blind holes.
- Challenges and Considerations: Machining blind holes is complex. Chip clearing, device choice, and the potential for apparatus avoidance can affect the machining system. Tending to these difficulties includes a mix of mechanical headways, tooling developments, and machining systems.
Understanding the subtleties of machining processes for blind holes is fundamental for guaranteeing the creation of exact, accurate parts in assorted designing applications.
Design Considerations of Blind Holes
Planning parts with blind holes requires the following considerations:
- Depth and Diameter: Deciding the ideal hole geometry, given the expected capability and underlying prerequisites.
- Material Properties: Understanding how various materials should have different machining settings and how they impact the blind hole design.
- Placement and Orientation: Decisively situating blind holes to accomplish practical targets without compromising the general integrity of the part.
- Interaction with Other Features: How blind holes connect with design features, like neighboring holes or surfaces.
Here is an example of how to callout a blind hole for an engineering drawing:
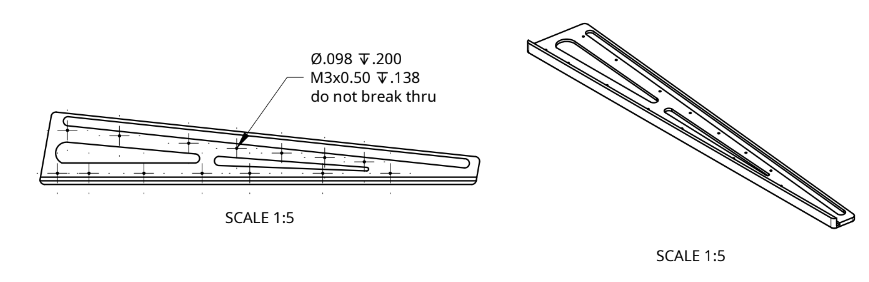
The callout ⌀.098 ↧.200 means a 0.098” diameter hole to a depth of 0.200”.
Importance of Hole Placement and Orientation
The placement and orientation of blind holes significantly impact the usefulness and manufacturability of parts. Engineers need to consider several factors, such as even distribution of stress, easy machining tool access, and the overall aesthetics of the final product.
Tolerances, Surface Finish, and Material Considerations
In addition, achieving precise tolerances and a suitable surface finish is crucial in blind hole design. Material properties, machinability, and the intended application influence decisions regarding tolerances. There is a distinct relationship between material properties, machining processes, and the optimal surface finish, guiding achieving the required accuracy in blind hole design.
Advantages and Disadvantages of Blind Holes
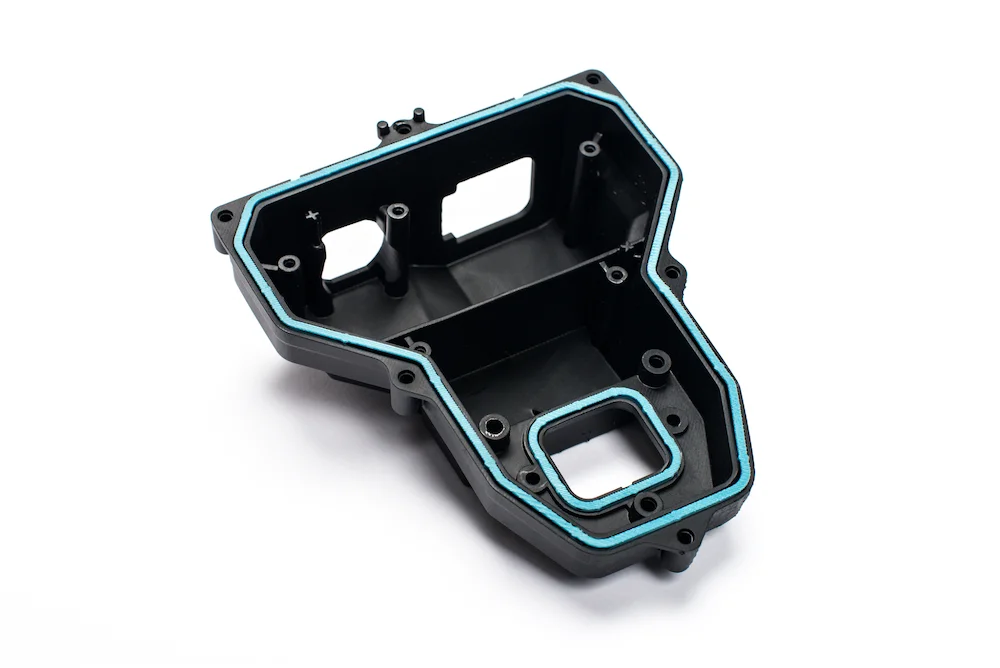
Benefits in Machining and Usage
- Enhanced Structural Integrity: Blind holes can improve the strength-to-weight ratio of parts.
- Reduced Material Usage: Precisely planned blind holes reduce material usage without compromising usefulness.
- Sealed Compartments: Blind holes make fixed compartments, shielding delicate parts from environmental degradation.
- Threaded Fastening: Blind holes give secure areas for attachments like threaded fasteners, adding to gathering effectiveness.
Limitations and Challenges in Machining and Usage
- Machining Complexity: Making blind holes, particularly in unpredictable plans, may present difficulties for device availability and chip departure.
- Potential for Stress Concentrations: Ineffectively planned blind holes might prompt pressure fixations, influencing the underlying part integrity.
- Assembly Considerations: Blind holes might complicate assembly processes, especially if tight tolerances are not held during machining.
Measurement and Inspection Techniques for Blind Holes
Quality Control Methods for Ensuring Blind Hole Accuracy
Accuracy in blind hole machining is critical for the assembly and fit-up of parts. So, accuracy and precision in measurement are critical and may be accomplished with methods such as:
- Coordinate Measuring Machines (CMM): Surveying hole aspects and resistances.
- Surface Profilers: Assessing surface completion and uprightness.
- Non-Destructive Testing (NDT): Recognizing interior imperfections or inconsistencies.
- Metrology Tools and Inspection Processes: Particular measures, bore checks, and endoscopes, among others.
Understanding how these apparatuses add to quality control in blind hole assembling is fundamental for keeping up with predictable and exact outcomes.
Environmental Considerations
Impact of Blind Hole Machining on Sustainability
There are many sustainable ramifications of blind-hole machining, particularly material waste. Blind holes, when correctly designed, can reduce material use, diminishing waste, and advancing supportability in assembly.
Machining processes, including those utilized for blind holes, frequently include energy-concentrated activities. Energy utilization of blind hole machining is reduced versus machining of other types of holes. Mechanical headways also add to more energy-proficient machining processes.
Potential Advancements in Blind Hole Engineering
Blind holes are a crucial element in engineering and machining, and their significance is only set to grow as technology advances.
One significant trend that could shape the future of blind hole machining is advancements in materials and tooling. As materials and tooling advance, they can improve the efficiency, accuracy, and flexibility of blind hole machining. Developments in apparatus coatings, materials science, and manufacturing methods can significantly impact the future of hole machining.
Another aspect that could shape the future of blind hole machining is compliance with industry regulations. Adherence to global standards and specifications can work towards smoother collaboration between manufacturers and advance global trade. It also ensures that products meet consistent quality standards, no matter their origin.
How to Ensure Correct Blind Hole Machining
Training programs for machinists and engineers can be vital in ensuring competence in blind hole machining. Formal education programs, on-the-job training, and continuous professional development programs can help individuals keep up with the latest advances and best practices.
Collaboration between engineers, designers, and machinists can significantly impact the success of blind hole machining projects. Interdisciplinary approaches to hole design and machining can lead to innovative and optimized blind hole designs. Case studies highlighting successful collaborative efforts can provide insights into the challenges faced, collaborative approaches used, and the impact on the outcome.
In conclusion, the importance of blind holes in engineering and machining cannot be overstated. Blind holes play a critical role in improving the robustness of parts, reducing material waste, and providing designers and mechanics with versatile options in part creation. As technology advances, it is essential to keep exploring and innovating in blind hole machining to ensure that it remains efficient, lightweight, and structurally sound.
For all your machining needs, check out Fictiv’s robust CNC machining capabilities, including precision blind hole machining. We offer a variety of materials and CNC part finishes that are sure to meet your needs! Upload a part for an instant quote today.